How to Be Quality Technician - Job Description, Skills, and Interview Questions
The quality of a product is essential to its success, and the role of the Quality Technician is vital in ensuring the product meets high standards. Quality Technicians assess products and materials to ensure they meet safety and performance requirements, and use their skills to identify defects or issues. Poor quality products can lead to customer dissatisfaction, costly recalls, and a weakened company reputation.
On the other hand, Quality Technicians who perform their duties diligently can help maintain a company's reputation, build customer trust, and create a reliable brand. In addition, they help reduce costs associated with re-work, scrap, and warranty claims. In short, Quality Technicians play an important role in maintaining high quality standards and protecting the reputation of their organization.
Steps How to Become
- Obtain a High School Diploma or GED. In order to become a quality technician, the first step is to obtain a high school diploma or equivalent.
- Pursue Post-Secondary Education. Most employers look for quality technicians who have a minimum of an associate degree in a related field such as engineering technology, industrial technology, or quality assurance.
- Get On-the-Job Training. While some employers may provide on-the-job training, others may require that you have prior experience or a certification before taking on the role.
- Obtain Certification. You may be able to obtain certifications that demonstrate your skills and knowledge in the field. Examples include American Society for Quality (ASQ) Certified Quality Technician (CQT) and Certified Quality Inspector (CQI).
- Stay Up to Date with Industry Trends. Quality technicians must stay up to date with changes in technology, regulations, and industry trends. This can be done by taking continuing education courses or attending conferences.
The quality of a product is determined by the quality of its components, and the skills and qualifications of the technician who assembles them. In order to ensure a high-quality product, the technician needs to have the appropriate skills and qualifications. For instance, they should have an understanding of the technical aspects involved in the assembly process, as well as being able to interpret diagrams and instructions.
They should also be familiar with the use of specialized tools and able to identify and rectify any defects that may occur during the assembly process. Furthermore, they should be able to accurately fill out documentation and keep accurate records of their work. Having a qualified and skilled technician can help ensure that the product is of the highest quality standards and will be able to meet the customer's expectations.
You may want to check Quality Management Coordinator, Quality Improvement Specialist, and Quality Assurance Coordinator for alternative.
Job Description
- Maintain quality control standards by verifying incoming materials and finished products.
- Audit raw material, work in process and finished goods inventory to ensure compliance with established quality standards.
- Monitor production line operations to ensure proper quality control procedures are followed.
- Inspect and test incoming materials and components to verify that they meet established standards.
- Perform visual inspections and mechanical tests on products to ensure conformance with specifications.
- Identify and document quality control issues and coordinate the implementation of corrective actions.
- Investigate customer complaints and product discrepancies to identify root causes and develop solutions.
- Compile and analyze quality control data to identify trends and recommend process improvements.
- Develop and maintain quality control documentation such as inspection plans, testing procedures, and calibration records.
- Train production personnel in quality control procedures and ensure compliance with applicable regulations.
Skills and Competencies to Have
- Knowledge of quality management systems and processes
- Familiarity with statistical methods and analysis
- Ability to interpret and analyze data
- Experience with quality assurance and control processes
- Excellent problem solving and troubleshooting skills
- Ability to communicate effectively and collaborate with other departments
- Attention to detail and strong organizational skills
- Ability to work independently and in teams
- Knowledge of applicable regulatory standards
- Proficiency in Microsoft Office applications
Attention to detail is a critical skill for any Quality Technician. This skill is essential for the successful completion of tasks and ensures accuracy in the final product. Quality Technicians need to inspect products for defects and make sure that the quality of the product meets industry standards.
In order to do this, Quality Technicians need to possess strong attention to detail, as well as good problem solving skills. This will allow them to identify any issues quickly and efficiently, and take the necessary steps to ensure that they are resolved. Quality Technicians must also have excellent communication skills to ensure that they can effectively communicate with other members of their team and stakeholders.
Good communication will ensure that any issues are identified and addressed quickly, thus reducing the risk of further problems arising down the line. Quality Technicians also need to be able to think critically and logically to determine the best course of action for a given situation. Having these skills will not only help Quality Technicians perform their job more effectively, but also help to ensure that the quality of products is always maintained.
Quality Control Lead, Quality Support Analyst, and Quality Management Manager are related jobs you may like.
Frequent Interview Questions
- What experience do you have working as a Quality Technician?
- Describe a situation where you had to identify a quality issue and resolve it.
- How do you ensure that quality standards are met?
- What do you consider to be the most important quality control measures?
- How do you keep up to date with the latest industry standards and regulations?
- How do you handle difficult customer complaints?
- What strategies would you use to motivate team members to meet quality goals?
- Describe a time you had to work with a difficult customer in order to maintain quality standards.
- What processes do you use to track quality trends and identify areas of improvement?
- How do you prioritize quality assurance tasks?
Common Tools in Industry
- Multi-meter. A device used to measure electrical current, voltage, and resistance. (eg: Fluke 77 Multimeter)
- Calipers. A precision instrument used to measure the distance between two points. (eg: Mitutoyo Digital Calipers)
- Gauges. A device used to measure the size or shape of a given object. (eg: Dial Bore Gauge)
- Test Stand. A mechanical device used to securely hold a product while it is being tested. (eg: LabJack U6 Test Stand)
- Microscope. An instrument used to magnify objects for further inspection. (eg: Olympus SZ61 Stereo Microscope)
- Force Gauge. A device used to measure force or weight. (eg: Chatillon DFS II Force Gauge)
- Tensile Tester. A device used to measure the tension of a material. (eg: Mark-10 Tensile Tester)
- Hardness Tester. A device used to measure the hardness of a material. (eg: Wilson Rockwell Hardness Tester)
- Oscilloscope. An electronic instrument used to measure voltage and time signals. (eg: Tektronix TBS1052 Digital Oscilloscope)
- Spectrometer. An instrument used to measure the intensity of light over a specific range of wavelengths. (eg: Shimadzu UV-VIS Spectrometer)
Professional Organizations to Know
- American Society for Quality (ASQ)
- International Organization for Standardization (ISO)
- Institute of Electrical and Electronics Engineers (IEEE)
- American National Standards Institute (ANSI)
- Society of Automotive Engineers (SAE)
- American Welding Society (AWS)
- National Institute of Standards and Technology (NIST)
- International Society of Automation (ISA)
- International Association for Six Sigma Certification (IASSC)
- International Council on Systems Engineering (INCOSE)
We also have Quality Management Specialist, Quality Improvement Analyst, and Quality Supervisor jobs reports.
Common Important Terms
- Calibration. The process of adjusting and testing a device to be sure it meets a standard or specification.
- Statistical Process Control (SPC). A set of methods used to measure and control quality during the manufacturing process.
- Quality Assurance. A system of processes and procedures that ensure products meet a certain level of quality before being released.
- Non-Conformance. A product or service that does not meet the required standards.
- Root Cause Analysis. A process used to identify the underlying cause of a problem.
- Corrective Action. Actions taken to address identified problems or non-conformances.
- Six Sigma. A methodology used to improve processes and achieve quality goals.
- ISO 9000. A set of international standards defining quality systems and management processes.
Frequently Asked Questions
Q1: What does a Quality Technician do? A1: Quality Technicians are responsible for inspecting, testing, and monitoring products and processes to ensure they meet quality standards. They may also be involved in troubleshooting and corrective action. Q2: What qualifications are required for a Quality Technician position? A2: Quality Technicians typically hold a high school diploma or equivalent, as well as specialized training in quality assurance and control. They may also have experience in a manufacturing environment. Q3: What type of environment does a Quality Technician work in? A3: Quality Technicians usually work in a manufacturing or production environment, where they are responsible for inspecting and testing raw materials, products, and processes. Q4: What types of tools do Quality Technicians use? A4: Quality Technicians typically use a variety of tools and instruments to inspect, test, and monitor products and processes, such as calipers, micrometers, gauges, and thermometers. Q5: How much does a Quality Technician earn? A5: The median annual salary for Quality Technicians is approximately $41,000. Salaries can vary depending on experience and location.What are jobs related with Quality Technician?
- Quality Improvement Inspector
- Quality Support Coordinator
- Quality Improvement Engineer
- Quality Performance Coordinator
- Quality Support Manager
- Quality Improvement Technician
- Quality Improvement Manager
- Quality Systems Manager
- Quality Performance Analyst
- Quality Manager
Web Resources
- Quality Technician - Anoka Tech anokatech.edu
- Quality Technician - Anoka Tech www.anokatech.edu
- What is a Manufacturing Quality Technician | Goodwin University www.goodwin.edu
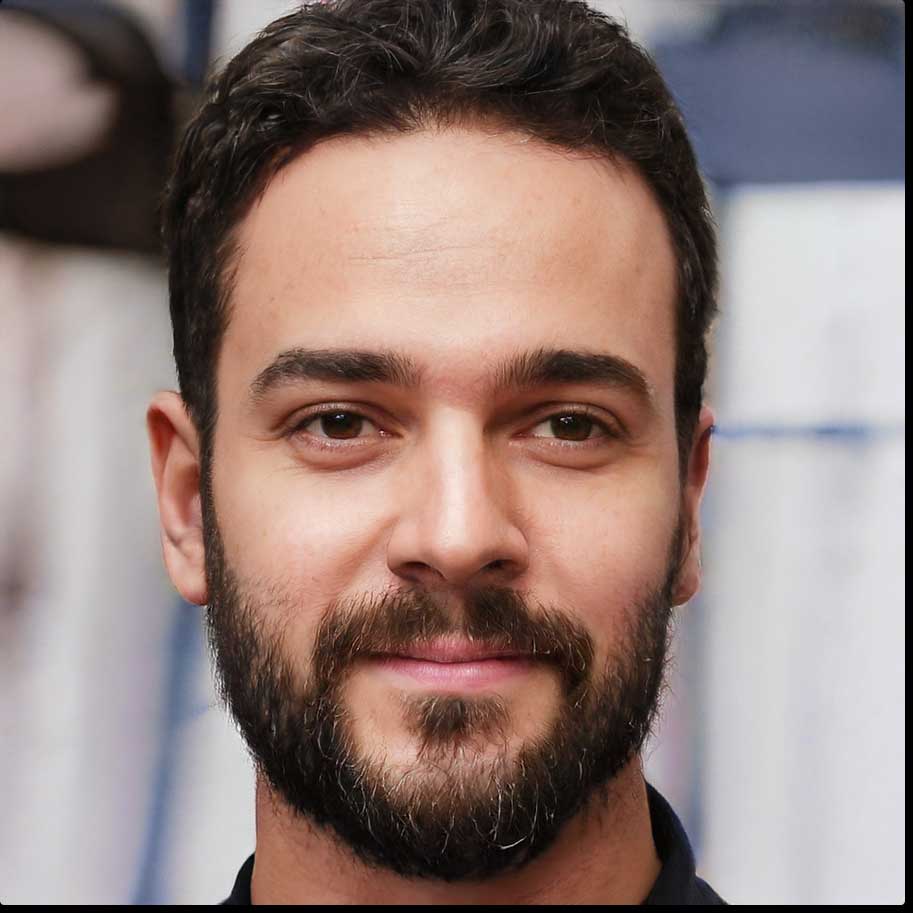