How to Be Quality Management Specialist - Job Description, Skills, and Interview Questions
Poor quality management can have a detrimental effect on a company's reputation and bottom line. Poorly managed processes can lead to wasted resources, late deliveries, customer dissatisfaction, and increased costs. Furthermore, the lack of adequate quality management can result in faulty products, missed compliance requirements, and safety hazards.
It is essential for companies to invest in quality management specialists to ensure that all processes are properly monitored and managed to avoid these costly issues. Quality management specialists play a critical role in tracking production data, conducting quality audits, and providing feedback to improve processes. By investing in these professionals, companies can protect their reputation and profitability by ensuring that their products and services meet customer expectations.
Steps How to Become
- Earn a Bachelor's Degree. Quality management specialists typically need a bachelor's degree in business administration, industrial engineering, or a related field. Coursework should include topics such as quality assurance and control, statistics, process improvement, and project management.
- Pursue Professional Certification. Quality management specialists can further their career by earning professional certification from an organization such as the American Society for Quality (ASQ). Certification requires passing an examination and having a certain number of years of experience in the field.
- Gain Experience. Quality management specialists can gain relevant experience by working as a quality assurance technician or in a related position in the manufacturing or service industries. They should be familiar with the concepts and techniques of quality assurance, such as Six Sigma and Lean Manufacturing.
- Use Quality Improvement Tools. Quality management specialists should be skilled in using quality improvement tools such as flowcharts, process mapping, and statistical process control. They should also be knowledgeable about quality systems, such as ISO 9000.
- Develop Communication Skills. Quality management specialists must be able to communicate effectively with all levels of employees, from management to production staff. Strong written and verbal communication skills are essential for this role.
- Stay Up-To-Date. Quality management specialists must stay abreast of changes in the industry, such as the implementation of new technologies and processes. They should also be familiar with current regulations and standards, such as ISO 9001.
You may want to check Quality Systems Analyst, Quality Improvement Analyst, and Quality Management Manager for alternative.
Job Description
- Develop and implement quality assurance processes, procedures and standards.
- Monitor and analyze customer feedback to identify areas of improvement.
- Carry out internal audits to assess the effectiveness of existing quality assurance processes.
- Devise and review specifications for products or services to ensure quality and reliability.
- Investigate causes of non-conformance using relevant quality tools and make recommendations for corrective action.
- Monitor supplier performance to ensure products meet required quality standards.
- Prepare and review quality control reports, process documentation and support customer complaints resolution processes.
- Liaise with customers, suppliers and other internal departments to ensure quality requirements are met.
- Implement and manage continuous improvement initiatives.
- Train staff in quality control activities and best practices.
Skills and Competencies to Have
- Knowledge of quality management principles and practices.
- Strong problem-solving and analytical skills.
- Knowledge of relevant industry regulations and standards.
- Excellent written and oral communication skills.
- Ability to work independently and as part of a team.
- Ability to manage multiple projects simultaneously.
- Experience developing and implementing quality control plans.
- Ability to analyze data and develop improvement strategies.
- Knowledge of auditing techniques and procedures.
- Ability to use computer software to analyze data and generate reports.
Quality management is a vital skill for any organization that wants to be successful. It involves identifying, understanding, and controlling processes that ensure the delivery of high-quality products and services. Quality management specialists are responsible for overseeing quality assurance processes, which involve the implementation of standards, inspection processes, and corrective action plans.
Quality management specialists must possess strong organizational and communication skills in order to effectively manage the quality assurance process. They must also have an understanding of various IT systems used in the industry, as well as an understanding of the implications of quality issues on customer satisfaction. they must be able to analyze data and develop strategies for improving product quality and customer service.
Quality management specialists must be able to identify areas of improvement in order to make sure that the company meets its goals and objectives. By utilizing quality measures, companies can ensure that their products and services remain competitive in the market and that customers are satisfied with their purchases.
Quality Improvement Coordinator, Quality Technician, and Quality Improvement Inspector are related jobs you may like.
Frequent Interview Questions
- What experience do you have in developing and implementing quality management systems?
- How do you ensure that company processes and procedures are up to date?
- What strategies do you use to identify areas of improvement within a quality management system?
- Describe a time when you faced an issue with a quality management system and how you overcame it.
- How do you stay current on industry trends related to quality management?
- What techniques do you use to ensure customer satisfaction with a product or service?
- How have you collaborated with other departments to improve quality management systems?
- How would you handle a situation in which the quality of a product or service did not meet expectations?
- Describe your experience managing teams responsible for quality control and assurance.
- What strategies have you used to help organizations achieve ISO certification or similar standards?
Common Tools in Industry
- Quality Management Software. This software helps to automate quality assurance processes and track performance metrics. (Example: SAP Quality Management)
- Process Mapping. This tool helps to document and analyze the sequence of activities used to complete a process. (Example: ARIS Process Mapping)
- Statistical Process Control. This tool is used to identify and analyze the cause of process variability to help reduce unwanted variation. (Example: Minitab Statistical Software)
- Six Sigma. This methodology uses data-driven tools and approaches to achieve process improvement and defect reduction. (Example: Lean Six Sigma)
- Root Cause Analysis. This tool helps identify the root cause of a problem or issue. (Example: 5 Whys Root Cause Analysis)
- Quality Control Checklists. This tool helps ensure that processes are being followed correctly and consistently. (Example: Quality Control Checklist Template)
Professional Organizations to Know
- American Society for Quality (ASQ)
- International Organization for Standardization (ISO)
- The Project Management Institute (PMI)
- National Institute of Standards and Technology (NIST)
- International Federation of Inspection Agencies (IFIA)
- American Association for Quality (AAQ)
- International Quality Federation (IQF)
- International Accreditation Forum (IAF)
- Institute of Quality Assurance (IQA)
- European Organization for Quality (EOQ)
We also have Quality Performance Manager, Quality Support Analyst, and Quality Assurance Consultant jobs reports.
Common Important Terms
- Quality Assurance (QA). The process of ensuring that the product or service meets the required quality standards.
- Quality Control (QC). The process of ensuring the quality of the product or service by inspecting and testing it to meet the set standards.
- Quality Management System (QMS). A set of processes, policies, and procedures used to ensure that a product or service meets the required quality standards.
- Quality Improvement (QI). The process of continually evaluating and improving the quality of a product or service.
- Nonconformity. A deviation from the specified requirements for a product or service.
- Root Cause Analysis (RCA). An investigative process used to identify the underlying cause of an issue or problem.
- Quality System Audit. An assessment of a company's quality management processes and systems.
- Six Sigma. A process improvement methodology designed to reduce defects and increase efficiency.
Frequently Asked Questions
What is the primary role of a Quality Management Specialist?
The primary role of a Quality Management Specialist is to ensure that products and services meet the required standards of quality and safety. They are responsible for developing and implementing quality control systems, managing audits and inspections, and monitoring product performance.
What qualifications are needed to become a Quality Management Specialist?
To become a Quality Management Specialist, an individual typically needs at least a bachelor's degree in business or engineering, as well as relevant experience in quality assurance and management. In some cases, certification in a specific quality management system such as ISO 9001 may be required.
What type of environment does a Quality Management Specialist work in?
Quality Management Specialists typically work in an office or laboratory setting, where they have access to the necessary documents and instruments to conduct their work. They may also be required to travel to different sites to inspect products or facilities.
How many years of experience is typically necessary for a Quality Management Specialist?
The amount of experience necessary to become a Quality Management Specialist varies depending on the industry and position, but most positions require at least two to five years of relevant experience.
What are the most important skills for a Quality Management Specialist?
The most important skills for a Quality Management Specialist include strong problem solving and analytical skills, attention to detail, excellent organizational skills, and the ability to communicate effectively with both customers and colleagues.
What are jobs related with Quality Management Specialist?
- Quality Performance Analyst
- Quality Assurance Lead
- Quality Performance Coordinator
- Quality Assurance Supervisor
- Quality Assurance Auditor
- Quality Manager
- Quality Support Specialist
- Quality Support Coordinator
- Quality Improvement Technician
- Quality Improvement Lead
Web Resources
- Quality Management Online | University of Minnesota crk.umn.edu
- Quality Management [M.S.] - Engineering - Eastern Michigan www.emich.edu
- Quality Management | University Research Administration | The ... ura.uchicago.edu
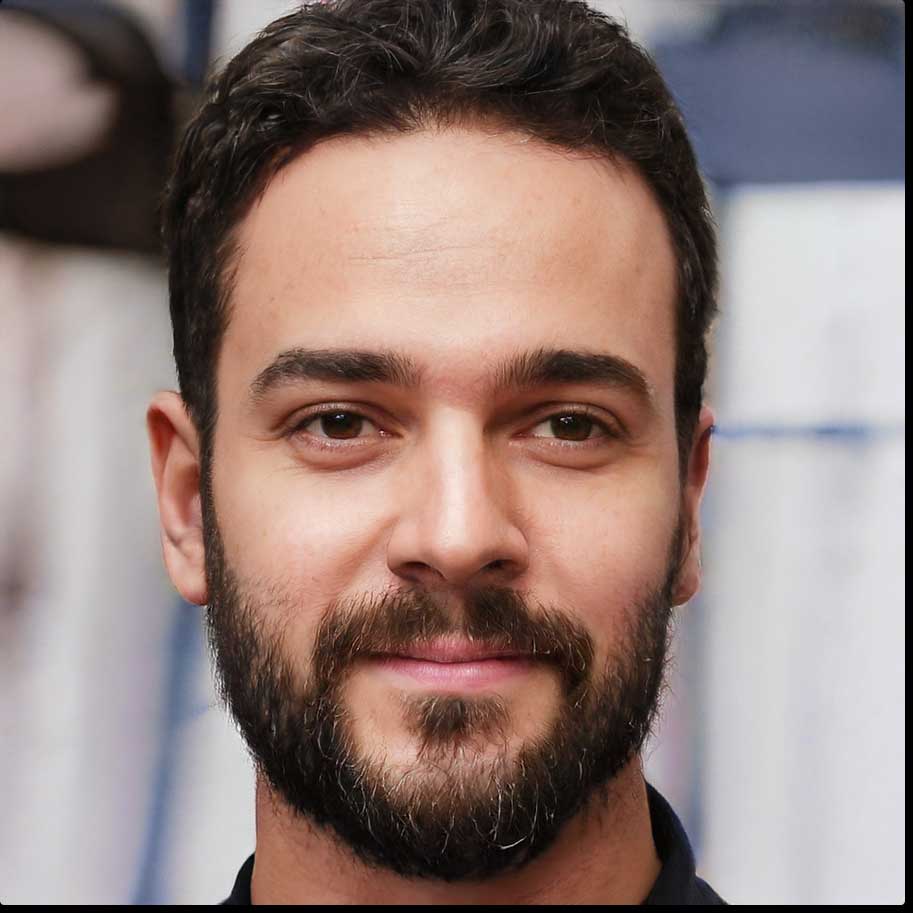