How to Be Quality Management Manager - Job Description, Skills, and Interview Questions
The success of any organization is largely dependent on the quality of its products and services. As such, Quality Management Managers are essential to ensure that the products and services meet the highest standards of excellence. Quality Management Managers are responsible for developing and implementing quality control systems, evaluating and tracking the performance of their teams, and ensuring that all processes meet regulatory standards.
By doing so, they help to guarantee customer satisfaction, reduce costs, and improve overall profitability. Quality Management Managers can also help to identify potential risks and develop appropriate strategies to mitigate them, thus further protecting the organization from potential losses.
Steps How to Become
- Earn a Bachelor's Degree. A bachelor's degree in quality management, business administration, engineering or a related field is the first step to becoming a quality management manager. Coursework should include studies in statistics, quality control methods, computer systems, project management and quality assurance.
- Gain Experience. Most employers prefer to hire quality management managers with at least two years of experience in a related field. This experience can be gained through internships, part-time jobs or volunteer positions.
- Obtain Certification. Obtaining certification in quality management is not required, but it can be beneficial in helping aspiring quality management managers stand out from other job candidates. Certifications are offered through organizations such as the American Society for Quality and the International Register of Certificated Auditors.
- Increase Your Knowledge. Quality management managers must constantly stay up to date on changes in technology, regulations and best practices. Participating in online forums, reading industry journals and attending professional conferences are all good ways to increase your knowledge of the field.
- Network. Developing strong relationships with other professionals in the field can be beneficial for quality management managers seeking job opportunities. Networking can also help you stay up to date on industry trends and changes.
Successful Quality Management Managers must stay ahead of the curve in order to remain qualified. This means proactively researching the latest developments and trends in quality management and staying up-to-date on best practices and industry standards. staying active in professional organizations related to the field, such as the American Society for Quality (ASQ), is essential for staying informed and connected with other professionals.
pursuing certifications or additional educational opportunities can help Quality Management Managers stay ahead of the competition and ensure they are providing the most up-to-date guidance to their organization. Finally, actively engaging in professional development activities, such as attending conferences, participating in webinars, or taking courses, can help Quality Management Managers stay ahead of the curve and remain qualified.
You may want to check Quality Assurance Coordinator, Quality Improvement Lead, and Quality Improvement Specialist for alternative.
Job Description
- Oversee and direct the Quality Management System (QMS) to ensure compliance with standards.
- Develop and implement quality assurance and control policies, procedures and objectives.
- Monitor and audit product and service quality, in accordance with established standards.
- Analyze customer feedback and complaints to identify areas of improvement.
- Establish and monitor supplier performance metrics.
- Train and supervise quality assurance and control staff.
- Design or implement quality-tracking systems for products or services.
- Coordinate corrective actions or process improvements with related departments.
- Generate reports on product quality assessment and customer satisfaction.
- Maintain documentation of product quality metrics, including test results and customer feedback.
Skills and Competencies to Have
- Strategic and organizational vision
- Leadership and team building
- Analytical and problem-solving skills
- Knowledge of quality management systems and standards
- Knowledge of data collection and analysis techniques
- Understanding of process improvement methods
- Knowledge of quality assurance methods
- Ability to develop and implement quality management policies and procedures
- Expertise in root cause analysis
- Excellent communication, interpersonal, and presentation skills
- Ability to work independently and as part of a team
- Attention to detail and accuracy
- Ability to manage multiple projects simultaneously
- Ability to develop, interpret, and implement statistical process control techniques
- Ability to use computerized systems for data analysis
- Ability to collaborate with different departments to ensure quality standards are met
In order to be an effective Quality Management Manager, one must possess a variety of skills that enable them to effectively manage the quality assurance process. One of the most important skills a Quality Management Manager needs is the ability to identify areas that need improvement and develop ways to address those issues. This requires the manager to have strong analytical and problem-solving skills in order to identify root causes, understand the potential impact of changes, and develop effective solutions.
the manager must have excellent communication and interpersonal skills in order to effectively collaborate with other departments and external stakeholders when making decisions. Finally, a Quality Management Manager must have a comprehensive understanding of quality assurance systems, processes, and regulations in order to ensure the organization meets all applicable standards and regulations. Without these essential skills, it would be difficult for a manager to effectively lead a quality management program.
Quality Assurance Technician, Quality Assurance Lead, and Quality Management Specialist are related jobs you may like.
Frequent Interview Questions
- How have you managed complex Quality Management projects in the past?
- What experience do you have with developing and implementing Quality Management systems?
- How do you ensure ongoing compliance with Quality Management standards?
- Describe a time you identified and solved a problem related to Quality Management?
- How do you keep up with the latest developments in Quality Management?
- What tools and techniques do you use to evaluate the effectiveness of Quality Management processes?
- What strategies do you use to motivate your team to achieve quality objectives?
- How do you ensure customer satisfaction with Quality Management deliverables?
- How have you used data and analytics to improve Quality Management systems?
- What steps do you take to ensure that all employees are familiar with Quality Management procedures?
Common Tools in Industry
- Quality Assurance Software. This software allows a company to track, monitor, and manage the quality assurance process. Example: Pro QC.
- Root Cause Analysis Tools. These tools help to identify and analyze the underlying causes of problems or issues. Examples: Fishbone Diagrams, Five Whys, Ishikawa Diagrams.
- Statistical Process Control Software. This software helps identify process variability and manage process performance. Examples: Minitab, Statgraphics.
- Quality Auditing Software. This software enables organizations to perform quality audits and report on the results. Examples: AQS Audit Manager, QADEX.
- Nonconformance Management Software. This software helps to identify and manage product defects, identify corrective actions, and track their implementation. Examples: QIMA Nonconformance Manager, IQS Nonconformance Manager.
Professional Organizations to Know
- American Society for Quality (ASQ)
- International Quality Federation (IQF)
- International Organization for Standardization (ISO)
- Institute of Quality Management (IQM)
- American Society for Quality Control (ASQC)
- European Organization for Quality (EOQ)
- International Association for Six Sigma Certification (IASSC)
- National Institute of Standards and Technology (NIST)
- Project Management Institute (PMI)
- Association for Quality and Participation (AQP)
We also have Quality Improvement Engineer, Quality Improvement Manager, and Quality Support Specialist jobs reports.
Common Important Terms
- Quality Control. The process of monitoring and verifying the quality of products, services, or processes to ensure they meet specified requirements.
- Quality Assurance. The process of establishing and maintaining a desired level of quality in products, services, or processes.
- Nonconformity. A product, service, or process that does not meet specified requirements.
- Root Cause Analysis. A method of problem-solving used to identify the root cause of a problem or issue.
- Statistical Process Control (SPC). A method of monitoring and controlling the quality of production processes by using statistical techniques.
- Total Quality Management (TQM). An approach to management that seeks to continuously improve the quality of products, services, or processes through the use of quality assurance techniques.
- Kaizen. A Japanese term meaning improvement or change for the better that is used in total quality management to describe ongoing efforts to improve quality and efficiency.
Frequently Asked Questions
What qualifications are required for a Quality Management Manager?
Quality Management Managers typically need at least a bachelor's degree in quality assurance, business administration, engineering, or a related field. Many also have professional certifications such as Certified Quality Manager (CQM), Certified Quality Auditor (CQA), and/or Six Sigma certifications.
What are the primary responsibilities of a Quality Management Manager?
Quality Management Managers are responsible for developing, implementing, and maintaining quality control systems and procedures in order to ensure that products meet customer expectations and industry standards. This includes identifying areas of improvement, developing and implementing corrective action plans, tracking results, and providing feedback to management.
What type of environment will a Quality Management Manager typically work in?
Quality Management Managers usually work in manufacturing and production facilities, but they may also work in research and development, engineering, or other related fields. They may work in office settings, laboratories, or factories.
What type of skills are necessary for Quality Management Managers?
Quality Management Managers must have excellent analytical, communication, problem-solving, and organizational skills. They must also have an understanding of manufacturing processes and quality control systems, as well as the ability to use data analysis software.
What is the typical salary range for a Quality Management Manager?
The average annual salary for Quality Management Managers is between $80,000 and $110,000 per year, depending on experience and location.
What are jobs related with Quality Management Manager?
- Quality Manager
- Quality Support Analyst
- Quality Support Coordinator
- Quality Performance Coordinator
- Quality Assurance Supervisor
- Quality Systems Coordinator
- Quality Support Manager
- Quality Control Lead
- Quality Assurance Auditor
- Quality Control Manager
Web Resources
- Quality Management [M.S.] - Engineering - Eastern Michigan www.emich.edu
- Quality Management | University Research Administration | The ... ura.uchicago.edu
- Quality Control Manager | NC State Online and Distance Education online-distance.ncsu.edu
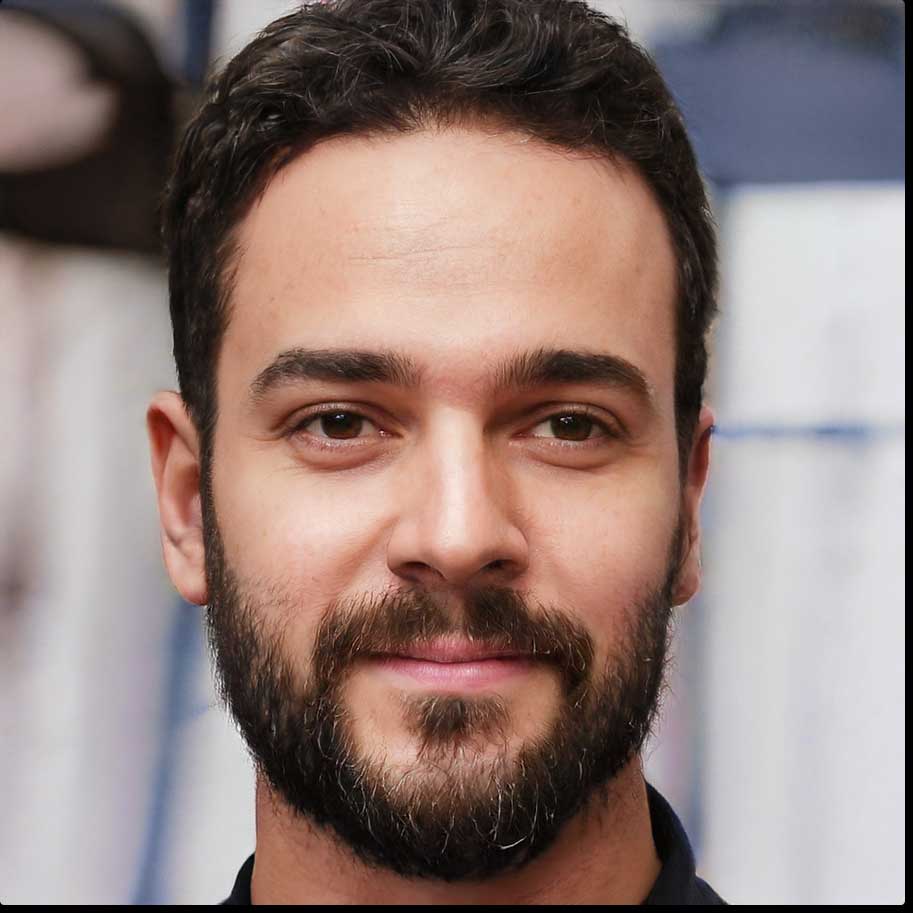