How to Be Quality Manager - Job Description, Skills, and Interview Questions
Poor quality management can lead to major losses for a company. Poor quality control can result in customer dissatisfaction, increased costs due to defective products, decreased efficiency, and a tarnished reputation. Quality control consists of activities such as inspecting incoming materials, conducting in-process checks on the production line, and testing finished products before they are shipped.
By implementing effective quality control measures, companies can increase customer satisfaction, reduce costs, improve efficiency, and enhance their reputation. Companies should also strive to meet industry standards and regulations while ensuring that their products are safe and reliable. Quality management is an essential part of any successful business, and companies should make sure they have the right resources and personnel to implement a successful quality management system.
Steps How to Become
- Obtain a Bachelor's Degree. Quality managers typically need a bachelor's degree in a related field like engineering, business, or science.
- Gain Expertise. Most employers prefer to hire quality managers with experience in the field. Aspiring quality managers can gain experience by working in quality assurance or a related role in an organization.
- Earn Quality Certifications. Many employers prefer to hire quality managers with certifications from organizations like the American Society for Quality (ASQ).
- Enhance Your Management Skills. Quality managers need to have excellent management skills. They should be able to lead and motivate their teams, as well as make tough decisions.
- Keep Up With Industry Trends. Quality managers should stay up to date with the latest developments in the quality management field. This will help them stay ahead of the competition and make sure their organization is meeting the latest standards.
- Pursue Professional Development Opportunities. Quality managers should take advantage of professional development opportunities like conferences and seminars to stay abreast of industry trends and best practices.
In order to stay ahead and competent as a Quality Manager, it is important to stay up-to-date on the latest industry trends, best practices, and regulations. This can be accomplished through attending conferences, obtaining certifications, and reading industry publications. By staying abreast of changes in the field, Quality Managers can gain the knowledge to make informed decisions, stay ahead of competition, and find innovative ways to improve their processes and procedures.
networking with other Quality Managers can provide invaluable insight and perspective on new ideas and strategies for success. By continuously learning and networking, Quality Managers can remain ahead of the curve and remain competent in their field.
You may want to check Quality Support Analyst, Quality Assurance Inspector, and Quality Support Specialist for alternative.
Job Description
- Develop and maintain quality assurance procedures and systems
- Establish standards and specifications for quality and reliability
- Monitor and review customer feedback and complaints
- Investigate customer issues and implement corrective action plans
- Develop and implement necessary changes in product design to improve quality
- Ensure products meet legal and safety requirements
- Monitor, review, and analyze data to identify trends and areas for improvement
- Conduct internal audits and inspections to ensure compliance with established policies and procedures
- Analyze customer feedback to identify areas of improvement
- Develop and implement training programs to enhance employeesÂ’ understanding of quality standards
- Monitor performance of suppliers and subcontractors to ensure quality standards are met
- Prepare periodic reports on quality assurance issues and activities
- Work with other departments to ensure quality issues are addressed in a timely manner
- Determine root cause of defects and implement preventive actions
Skills and Competencies to Have
- Knowledge of Quality Management System (QMS) principles and practices
- Knowledge of quality assurance, quality control, and related processes
- Ability to develop and implement quality plans and procedures
- Ability to monitor and evaluate process performance and products
- Expertise in statistical analysis and quality metrics
- Ability to identify and address potential quality issues
- Ability to inspect, test, and audit product quality
- Ability to develop corrective and preventive actions
- Excellent communication, problem-solving, and decision-making skills
- Knowledge of relevant industry regulations and standards
- Leadership qualities and team management skills
- Ability to plan and organize workloads
- Strong attention to detail and accuracy
- Ability to use industry-standard quality assurance software
Quality Managers are responsible for ensuring that products and services meet customer expectations and meet all applicable industry standards. As such, one of the most important skills for a Quality Manager is an in-depth understanding of quality management systems and processes. This includes having knowledge of the various tools and methods used to evaluate quality, such as statistical process control, failure mode and effects analysis, and root cause analysis.
Quality Managers must be able to effectively communicate with stakeholders, such as customers, vendors, and employees. They must also be able to develop and implement effective improvement plans to ensure that quality standards are met and improved upon. By having these skills, Quality Managers can help ensure that companies produce high-quality products and services that meet customer requirements, resulting in increased customer loyalty and satisfaction.
Quality Improvement Specialist, Quality Improvement Inspector, and Quality Performance Specialist are related jobs you may like.
Frequent Interview Questions
- How do you define quality?
- What experience do you have managing quality control processes?
- Describe your experience with developing and implementing quality assurance protocols.
- What strategies have you used to ensure customer satisfaction?
- How do you stay up-to-date on industry best practices in quality management?
- What challenges have you faced while managing quality processes?
- Describe your experience training and developing team members in quality processes.
- How do you handle customer complaints and feedback?
- How do you measure the success of quality assurance initiatives?
- How do you prioritize tasks to ensure quality standards are met?
Common Tools in Industry
- Quality Assurance Software. This is a software system designed to ensure products meet quality standards and are free from defects. Example: Jira, Zephyr.
- Root Cause Analysis Tools. These tools help identify the root causes of problems and give ideas for potential solutions. Examples: Fishbone Diagrams, 5 Whys Technique.
- Statistical Process Control (SPC). This is a quality management tool that uses statistical methods to identify and control processes so that they produce products of consistent quality. Example: SPC Charts, Control Charts.
- Quality Control Tools. These tools help ensure products meet quality standards and are free from defects. Examples: Flowcharts, Ishikawa Diagrams, Pareto Charts.
- Quality Auditing Tools. These tools are used to audit processes and operations to ensure quality standards are met. Examples: Checklists, Inspection Sheets, Surveys.
Professional Organizations to Know
- American Society for Quality (ASQ)
- International Organization for Standardization (ISO)
- International Register of Certified Auditors (IRCA)
- International Association for Six Sigma Certification (IASSC)
- Association for Manufacturing Excellence (AME)
- Project Management Institute (PMI)
- Institute of Quality Assurance (IQA)
- American National Standards Institute (ANSI)
- The Quality Management Forum (QMF)
- The Chartered Quality Institute (CQI)
We also have Quality Assurance Coordinator, Quality Improvement Analyst, and Quality Improvement Technician jobs reports.
Common Important Terms
- Quality Assurance. The practice of ensuring that the products and services a company provides meet certain standards of quality.
- Quality Control. The process of verifying that products and services meet specific requirements.
- ISO Standards. International standards that outline criteria for quality management systems.
- Root Cause Analysis. A process used to identify the underlying cause of a problem or issue.
- Statistical Process Control. The use of statistical methods to monitor and control a process.
- Six Sigma. A comprehensive approach to achieving process excellence by minimizing defects and maximizing efficiency.
- Lean Manufacturing. A system that focuses on eliminating waste and improving efficiency through streamlining processes.
- Kaizen. The Japanese term for continual improvement, usually applied to business processes.
Frequently Asked Questions
What is the primary role of a Quality Manager?
The primary role of a Quality Manager is to ensure that quality standards and processes are met in a production or service environment. They are responsible for developing, implementing, and maintaining quality assurance systems, ensuring compliance with regulatory and industry standards, and monitoring the performance of quality-related activities.
What qualifications are needed to become a Quality Manager?
Quality Managers typically need a Bachelor's degree in a relevant field such as engineering, business, or quality assurance. In some cases, employers may prefer a Master's degree. Additionally, they need to demonstrate strong organizational, problem-solving, and communication skills.
What metrics and KPIs do Quality Managers use to measure performance?
Quality Managers use various metrics and KPIs to measure performance, such as customer satisfaction surveys, defect rate, cycle time, and cost of quality. They also use process control charts and other statistical process control techniques to identify trends and root causes of quality issues.
What are some common tools used by Quality Managers?
Quality Managers often use a variety of tools to ensure quality standards are met including flowcharts, process maps, checklists, and risk management tools. They also use software programs such as statistical analysis software and enterprise resource planning (ERP) systems to track quality data and analyze trends.
What is the salary range for Quality Managers?
According to PayScale, the average salary for Quality Managers is $77,798 per year in the United States. Salaries typically range from $60,000 to $94,000 per year depending on experience, location, and employer.
What are jobs related with Quality Manager?
- Quality Assurance Technician
- Quality Technician
- Quality Assurance Auditor
- Quality Support Manager
- Quality Improvement Lead
- Quality Assurance Supervisor
- Quality Improvement Manager
- Quality Support Coordinator
- Quality Assurance Lead
- Quality Control Lead
Web Resources
- Quality Control Manager | NC State Online and Distance Education online-distance.ncsu.edu
- Quality Management, M.S. | Florida Tech - www.fit.edu www.fit.edu
- Quality Management - Quality Management - Dashboard confluence.cornell.edu
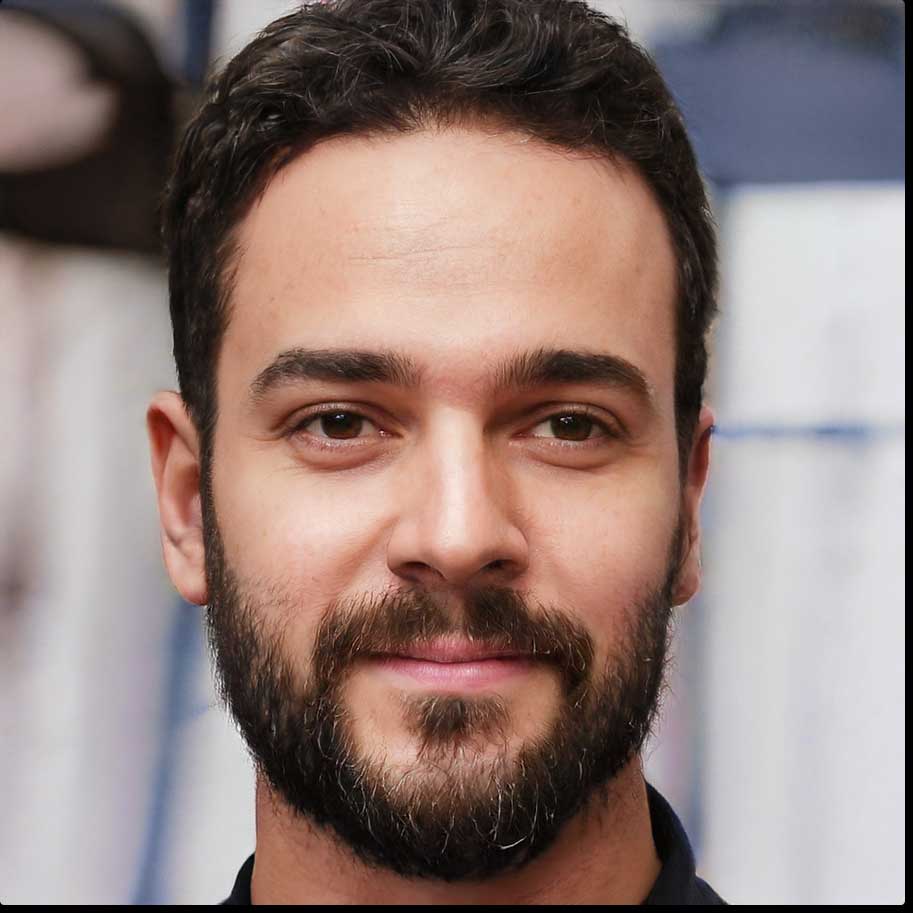