How to Be Quality Assurance Inspector - Job Description, Skills, and Interview Questions
Steps How to Become
- Earn a Bachelor's Degree. A bachelor's degree in a technical field such as engineering, computer science, or quality assurance, is usually required to become a Quality Assurance Inspector. Coursework can include mathematics, statistics, manufacturing processes, and quality control methods.
- Gain Work Experience. Employers may prefer applicants with experience in a related field. Applicants can gain experience through internships, apprenticeships, or part-time work.
- Obtain Certification. The American Society for Quality offers the Certified Quality Inspector certification. This requires passing an exam and having two years of quality assurance experience.
- Obtain Licensing. Depending on the industry and state regulations, some states may require licensing to become a Quality Assurance Inspector. Requirements vary by state.
- Complete On-the-Job Training. Quality Assurance Inspectors typically receive on-the-job training to learn the specific processes and procedures of the employer. On-the-job training may last several weeks to several months.
Quality assurance inspectors have an important role to play in ensuring the reliability and efficiency of products and services. Their job is to inspect products, materials, and processes for defects, errors, or inconsistencies and ensure that they meet established standards. Quality assurance inspectors use a variety of tools, techniques, and equipment to identify potential risks and problems.
They also review data and documentation to ensure accuracy. To be reliable and efficient, quality assurance inspectors must be highly organized and must pay close attention to detail. They must be able to analyze data quickly and accurately, and they must be able to identify trends or patterns that could lead to problems or issues.
Quality assurance inspectors must also be able to communicate effectively with other members of the production team and make recommendations for improving the quality of the process or product. By ensuring that products are of high quality and meet the needs of consumers, quality assurance inspectors help ensure the success of companies.
You may want to check Quality Systems Specialist, Quality Support Coordinator, and Quality Management Specialist for alternative.
Job Description
- Quality Assurance Inspector: Inspects products to ensure that they meet quality standards and customer specifications. Conducts inspections throughout the production process to identify and resolve defects. Maintains records of inspection results, prepares reports, and performs other duties as assigned.
- Quality Control Engineer: Develops, implements, and monitors quality control systems to ensure product quality and reliability. Analyzes data to identify problems and determine corrective and preventive actions. Ensures that quality standards are adhered to in the production process.
- Quality Assurance Technician: Tests products and materials to ensure they meet company quality standards and customer specifications. Performs inspections and tests throughout the production process. Reports test results, prepares documentation, and performs other duties as assigned.
- Quality Assurance Manager: Oversees quality assurance processes and programs. Develops and implements quality control systems. Monitors performance of quality assurance personnel and inspects products to ensure compliance with established standards.
- Quality Assurance Analyst: Analyzes data collected from quality assurance processes and programs to identify problems, trends, and root causes of defects. Recommends corrective actions to improve product quality. Prepares reports and documentation related to quality assurance activities.
Skills and Competencies to Have
- Ability to read, understand, and interpret technical drawings and specifications.
- Knowledge of quality assurance principles and techniques.
- Ability to use and interpret a variety of measuring instruments, such as calipers and micrometers.
- Ability to identify and troubleshoot problems related to product quality.
- Knowledge of corrective and preventive actions for quality issues.
- Strong organizational and communication skills.
- Ability to maintain accurate records and documentation.
- Proficient in Microsoft Office applications (Word, Excel, Outlook).
- Ability to work independently and as part of a team.
- Detail-oriented with strong analytical skills.
Quality assurance inspectors play a vital role in ensuring the quality of products and services. Their ability to thoroughly inspect and evaluate the quality of products and services, identify potential defects and non-conformities, and recommend corrective action is essential for businesses to ensure customer satisfaction and maintain their competitive edge. In order to be effective, quality assurance inspectors must possess a variety of skills.
These include an eye for detail, problem-solving abilities, organizational skills, knowledge of quality standards, and experience with inspection tools and processes. Furthermore, they must have excellent communication skills in order to relay their findings to management and other stakeholders. Quality assurance inspectors must also be able to work both independently and collaboratively in order to maintain the highest level of quality assurance.
All these skills are necessary in order to effectively identify and address problems and ensure that customer expectations are met.
Quality Engineer, Quality Performance Coordinator, and Quality Improvement Inspector are related jobs you may like.
Frequent Interview Questions
- What experience do you have in quality assurance inspection?
- How do you stay up to date with the latest quality assurance technologies and methods?
- Describe a successful quality assurance inspection project that you have worked on.
- What strategies do you use to ensure accuracy and compliance during quality assurance inspections?
- What challenges have you faced when conducting quality assurance inspections and how did you overcome them?
- How do you ensure product safety and performance standards are met during quality assurance inspections?
- How do you handle disagreements between stakeholders on inspection results?
- What techniques do you use to identify potential problems during quality assurance inspections?
- How do you ensure data is collected and reported accurately during quality assurance inspections?
- What processes do you use to ensure quality control during quality assurance inspections?
Common Tools in Industry
- Quality Control Checklist. A list of criteria that must be met before a product is approved for production. (e. g. all welds must be free of cracks and other defects)
- Calipers. A measuring tool used to measure the size of an object. (e. g. measuring the inside diameter of a pipe)
- Gauges. A device used to measure physical characteristics such as pressure, temperature, and thickness. (e. g. measuring the thickness of sheet metal)
- Computerized Data Analysis Software. Software that can be used to generate reports and analyze trends in product quality data. (e. g. tracking changes in product dimensions over time)
- Visual Inspection. A method of inspecting a product or component using sight or a magnifying glass. (e. g. looking for scratches or other surface defects on a finished part)
- X-Ray Inspection. A method of inspecting internal components of a product using x-ray imaging technology. (e. g. looking for cracks or other internal defects in a cast part)
- Ultrasonic Testing. A method of testing the integrity of a product using high-frequency sound waves. (e. g. detecting flaws in welds and other components)
- Test Fixtures. A tool used to test the performance of a product or component under simulated conditions. (e. g. testing the strength of a weld joint under simulated stress)
Professional Organizations to Know
- International Software Testing Qualifications Board (ISTQB)
- American Society for Quality (ASQ)
- International Institute of Business Analysis (IIBA)
- International Quality Federation (IQF)
- International Organization for Standardization (ISO)
- National Institute of Standards and Technology (NIST)
- American Association for Quality (AAQ)
- American Society of Quality Control (ASQC)
- Institute of Quality Assurance (IQA)
- Quality Assurance Institute (QAI)
We also have Quality Improvement Manager, Quality Assurance Technician, and Quality Improvement Engineer jobs reports.
Common Important Terms
- Quality Control. The process of inspecting, testing, and verifying products or services to ensure they meet predetermined standards of quality.
- Quality Assurance. The process of preventing defects and ensuring quality through the continuous improvement of processes, products, and services.
- Nonconformance. A failure to meet the requirements of a product or service specification.
- Defects. An imperfection or flaw that causes a product or service to not meet its intended purpose.
- Test Protocols. A set of instructions or criteria for conducting tests in order to determine the quality of a product or service.
- Root Cause Analysis. An investigation into the cause of a defect or problem in order to correct it and prevent it from occurring again.
- Validation. The process of verifying that a product or service meets its stated requirements.
- Inspection. The process of examining a product or service to verify that it meets predetermined standards and requirements.
Frequently Asked Questions
What is the main purpose of a Quality Assurance Inspector?
The main purpose of a Quality Assurance Inspector is to ensure that products meet quality standards set by the manufacturer and applicable regulations.
What qualifications are necessary for a Quality Assurance Inspector?
Qualifications for a Quality Assurance Inspector typically include a high school diploma, prior experience in quality assurance, and knowledge of relevant quality standards and regulations.
How often do Quality Assurance Inspectors inspect products?
Quality Assurance Inspectors typically inspect products on an ongoing basis, inspecting each product or batch of products as they are produced.
What tools do Quality Assurance Inspectors use to inspect products?
Quality Assurance Inspectors use a variety of tools to inspect products including measuring instruments such as calipers and micrometers, as well as visual inspection tools such as magnifying glasses and borescopes.
What type of reports do Quality Assurance Inspectors generate?
Quality Assurance Inspectors typically generate reports that list any defects found during inspection and make recommendations for corrective action. They may also generate statistical process control (SPC) charts and other process performance metrics.
What are jobs related with Quality Assurance Inspector?
- Quality Assurance Consultant
- Quality Manager
- Quality Improvement Technician
- Quality Systems Analyst
- Quality Support Specialist
- Quality Improvement Specialist
- Quality Improvement Coordinator
- Quality Control Inspector
- Quality Support Manager
- Quality Supervisor
Web Resources
- Online Quality Inspector from Arkansas State University ed2go.degree.astate.edu
- What is a Welding Quality Assurance/Quality Control ¦ www.tws.edu
- Working in Quality Assurance: The Skills That You Need www.northeastern.edu
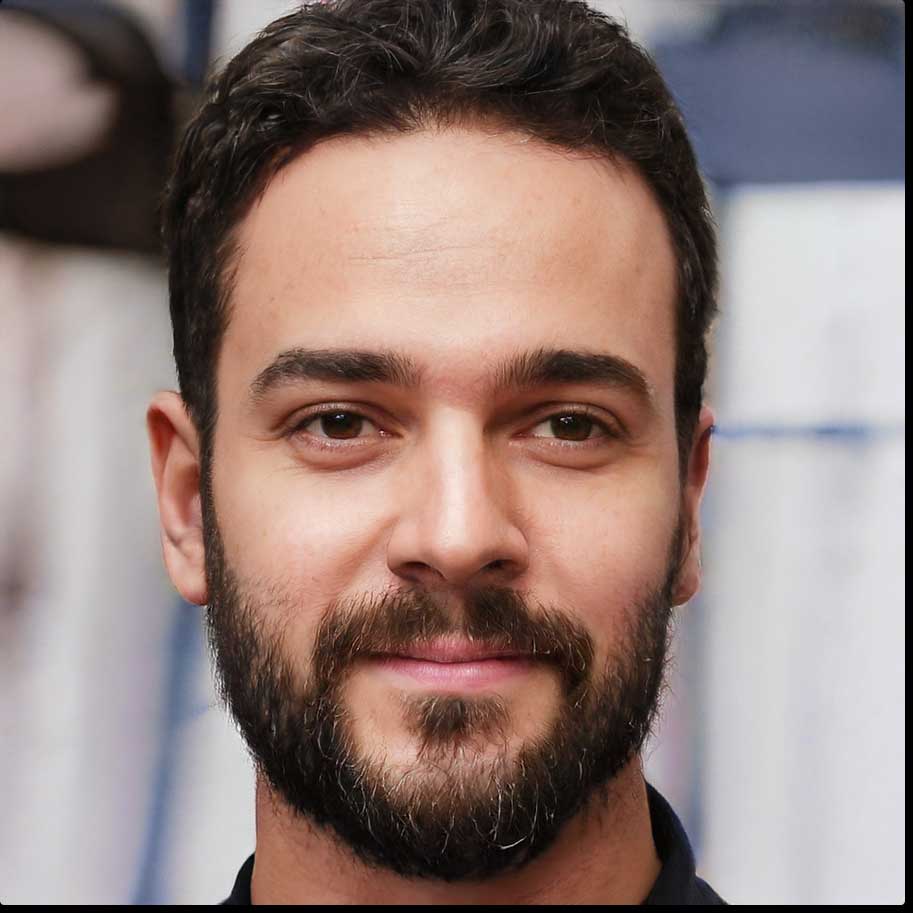