How to Be Quality Improvement Specialist - Job Description, Skills, and Interview Questions
Steps How to Become
- Obtain a Bachelor's Degree. To become a Quality Improvement Specialist, most employers require a bachelor's degree in a related field such as health care administration, public health, or business administration.
- Receive On-the-Job Training. Many employers will provide on-the-job training for quality improvement specialists. This training often includes the use of specific software and quality improvement processes.
- Consider Earning a Graduate Degree. To stand out from other applicants, consider pursuing a master's degree in health care administration or public health. This advanced degree can give you a competitive edge when applying for jobs.
- Join Professional Organizations. Joining professional organizations such as the American Society for Quality or the Association for Healthcare Quality can help you stay up-to-date on the latest trends and industry developments.
- Obtain Certification. Obtaining certification as a Certified Professional in Healthcare Quality (CPHQ) is an excellent way to demonstrate your knowledge and commitment to quality improvement.
Keeping up to date and competent as a Quality Improvement Specialist requires ongoing education and practice. It is essential to stay abreast of current practices and trends in the field, as well as staying informed of changes in regulations or standards. To do this, Quality Improvement Specialists should regularly review industry publications, participate in continuing education courses, attend professional development seminars and conferences, and network with colleagues to stay informed of best practices.
Quality Improvement Specialists should engage in hands-on activities such as mock audits, quality improvement projects, and practice simulations to ensure that their skills remain sharp and up-to-date. By taking these steps, Quality Improvement Specialists can ensure that their knowledge and skills remain current and relevant.
You may want to check Quality Systems Specialist, Quality Control Manager, and Quality Support Manager for alternative.
Job Description
- Develop and implement performance improvement activities and initiatives to improve patient care and outcomes.
- Analyze data to identify areas for improvement and develop plans to address gaps in care.
- Provide educational material and resources to healthcare staff to improve quality of care.
- Evaluate processes and procedures to ensure compliance with regulations and standards.
- Lead interdisciplinary teams to create, implement, and evaluate evidence-based best practices.
- Monitor and report outcomes to executive leadership and other stakeholders.
- Collaborate with other departments to ensure successful implementation of quality improvement initiatives.
- Establish and maintain strong relationships with external organizations to promote quality improvement.
- Facilitate communication among stakeholders to ensure alignment of goals and objectives.
- Stay current on industry trends and developments in healthcare quality improvement.
Skills and Competencies to Have
- Knowledge of quality improvement principles and methods
- Understanding of Continuous Quality Improvement (CQI) and Total Quality Management (TQM)
- Ability to identify areas of improvement and develop strategies to address them
- Demonstrated problem-solving and analytical skills
- Ability to effectively communicate and interact with staff at all levels
- Proficiency in data analysis and interpretation
- Excellent project management skills
- Ability to work independently and within a team
- Proficiency in the use of computer software for data analysis and reporting
- Knowledge of relevant industry standards and regulations
The ability to identify areas for improvement and effectively implement changes is a key skill for a Quality Improvement Specialist. This involves the ability to analyze data, identify trends, and recognize patterns. With this knowledge, the Quality Improvement Specialist can then develop solutions that will lead to increased efficiency, cost savings, and improved customer satisfaction.
They must be able to effectively communicate their proposed solutions to key stakeholders and ensure they are implemented properly. they must have the ability to think creatively and develop innovative solutions, as well as have excellent problem-solving skills. Finally, they must be able to monitor the effects of their solutions and adjust them as needed in order to ensure optimal results.
Quality Improvement Specialists are invaluable in helping organizations reach their goals and provide the highest quality products and services.
Quality Systems Manager, Quality Support Coordinator, and Quality Improvement Analyst are related jobs you may like.
Frequent Interview Questions
- What experience do you have with quality improvement initiatives?
- What challenges have you faced working to improve quality in the past?
- How do you evaluate the success of a quality improvement program?
- Are you familiar with Lean Six Sigma and other quality improvement methodologies?
- What metrics do you use to measure the success of quality improvement initiatives?
- In what ways do you ensure that quality improvement efforts are maintained over time?
- How do you use data to drive quality improvements?
- How do you keep up with industry best practices related to quality improvement?
- Describe a successful quality improvement project that you have worked on in the past.
- What strategies do you employ to motivate stakeholders to support quality improvement initiatives?
Common Tools in Industry
- Root Cause Analysis Tool. A tool used to identify the underlying cause of a problem so that it can be addressed and resolved. (e. g. 5 Whys Analysis)
- Lean Six Sigma. A methodology that combines the Lean and Six Sigma philosophies to identify and eliminate waste from processes. (e. g. DMAIC process)
- Process Mapping Tool. A tool used to visualize a process, identify inefficiencies, and suggest improvement solutions. (e. g. Value Stream Mapping)
- Quality Control Chart. A tool used to track a process's performance over time, identify trends and outliers, and ensure it is meeting quality requirements. (e. g. Pareto Chart)
- Failure Mode and Effects Analysis (FMEA). A tool used to identify potential risks and identify the best strategies for mitigating them. (e. g. Risk Priority Number (RPN) analysis)
- Statistical Process Control (SPC). A tool used to monitor and control process performance by analyzing data from production processes. (e. g. Control Charts)
- Benchmarking. A tool used to compare current performance against industry standards in order to identify areas for improvement. (e. g. Balanced Scorecard)
Professional Organizations to Know
- American Organization for Quality
- International Quality Federation
- American Society for Quality
- Quality Management Institute
- Institute for Healthcare Improvement
- Malcolm Baldrige National Quality Award Program
- Project Management Institute
- International Institute for Learning
- Association for Performance Improvement
- Healthcare Quality Association on Accreditation
We also have Quality Improvement Manager, Quality Assurance Supervisor, and Quality Improvement Inspector jobs reports.
Common Important Terms
- Quality Assurance (QA). The process of verifying that products, services, and processes meet required standards of quality.
- Quality Control (QC). The monitoring and regulation of products and processes to ensure they meet a predetermined level of quality.
- Six Sigma. A set of techniques and tools used to improve the quality of products and services, reduce costs, and increase customer satisfaction.
- Lean Six Sigma. A combination of Lean and Six Sigma methods used to improve the quality of products and services while reducing costs.
- Kaizen. A Japanese term meaning “continuous improvement” that is used to refer to a system of activities designed to improve the efficiency and effectiveness of business processes.
- Root Cause Analysis (RCA). A method used to identify and address the root causes of problems or issues.
- Process Improvement. The systematic use of data, analysis, and feedback loops to identify and eliminate problems or obstacles that impede the delivery of a product or service.
- Data Analysis. The process of collecting, organizing, analyzing, and interpreting data in order to draw conclusions and make decisions.
- Quality Management System (QMS). A system designed to ensure that products, services, and processes meet specified quality criteria.
- Continuous Improvement. An ongoing process of incremental improvement to products, services, and processes in pursuit of high quality and customer satisfaction.
Frequently Asked Questions
What is a Quality Improvement Specialist?
A Quality Improvement Specialist is a healthcare professional who works to identify areas of improvement within an organization and develop strategies to increase quality and efficiency.
What qualifications are required for a Quality Improvement Specialist?
Quality Improvement Specialists typically require a Bachelor's degree in healthcare administration, healthcare management, or a related field. Additionally, many employers require certification in Quality Improvement or Six Sigma.
What duties does a Quality Improvement Specialist perform?
Quality Improvement Specialists are responsible for evaluating existing systems and processes, identifying areas of improvement, and developing strategies to increase quality and efficiency. They may also be responsible for developing quality metrics, conducting training sessions, and providing oversight of quality initiatives.
What skills are needed to be a successful Quality Improvement Specialist?
Successful Quality Improvement Specialists must possess strong problem-solving and analytical skills, as well as the ability to think strategically and develop innovative solutions. They must also have excellent communication and interpersonal skills, as well as the ability to lead teams and collaborate with stakeholders.
How much does a Quality Improvement Specialist typically earn?
According to PayScale, the average salary for Quality Improvement Specialists in the United States is $58,000 per year. However, salaries can vary significantly depending on experience, location, and employer.
What are jobs related with Quality Improvement Specialist?
- Quality Assurance Auditor
- Quality Control Inspector
- Quality Improvement Coordinator
- Quality Support Analyst
- Quality Performance Analyst
- Quality Assurance Lead
- Quality Improvement Lead
- Quality Systems Analyst
- Quality Control Lead
- Quality Management Analyst
Web Resources
- Clinical Quality Improvement Specialist | Quality Improvement jobs.northwell.edu
- What is Quality Improvement in Healthcare? | SNHU www.snhu.edu
- Quality Improvement | Pediatrics | U of U School of Medicine medicine.utah.edu
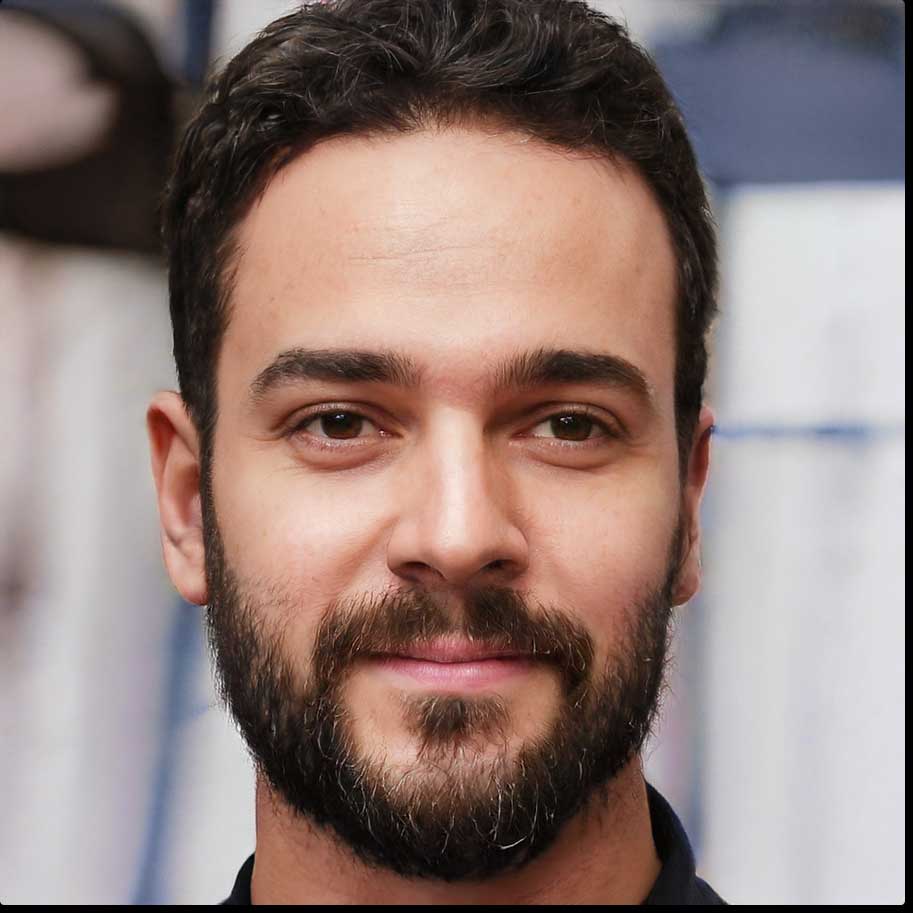