How to Be Quality Control Lead - Job Description, Skills, and Interview Questions
The lack of quality control in the workplace can lead to numerous issues; from customer dissatisfaction to an increase in production costs. When quality is not properly monitored and maintained, a company may experience decreased revenue due to customer complaints and costly repairs. it can lead to an increase in employee turnover due to a lack of trust in the companys products and services.
Finally, poor quality control can damage the reputation of the company, resulting in a decrease in brand loyalty. Companies should be aware of the need for quality control and take steps to ensure that they are able to maintain satisfactory levels of quality in order to avoid the costly effects of poor quality control.
Steps How to Become
- Obtain a Bachelors Degree in Quality Control, Engineering, or a related field. To become a Quality Control Lead, its essential to have a degree in Quality Control, Engineering, or a related field. This provides a solid foundation of knowledge and skills in quality assurance and control, as well as the principles of engineering and management.
- Gain Experience in Quality Control. Its important to gain experience as a Quality Control Technician or Engineer before becoming a Quality Control Lead. This experience will help you understand the fundamentals of quality assurance and control, as well as giving you the necessary skills to lead a team.
- Develop Your Leadership Skills. Quality Control Leads must possess strong leadership skills. They must be able to motivate and direct their team, as well as communicate effectively with other departments. Developing these skills is essential for success in this role.
- Pursue Professional Certifications. Having professional certifications can help you stand out from other candidates. Organizations like the American Society for Quality offer certifications such as Certified Quality Engineer (CQE) and Certified Quality Technician (CQT), which demonstrate your knowledge and expertise in quality control.
- Stay Up to Date on Quality Control Best Practices. Quality control best practices are constantly changing, so its important for Quality Control Leads to stay up to date on the latest trends and techniques. Reading industry publications and attending conferences are great ways to stay informed.
The quality control lead is responsible for ensuring that all products meet the necessary standards. To do this, they must have an ideal and efficient process in place. This includes identifying any potential issues that may arise, such as defects in the design or manufacturing process, and determining the best possible solutions to prevent them.
With proper planning and monitoring, they can ensure that products are of a high quality and meet all safety regulations. Furthermore, by properly communicating with their teams and stakeholders, they can ensure that all processes are running smoothly and any potential issues are quickly addressed. an ideal and efficient quality control lead is integral to the success of any business.
You may want to check Quality Assurance Technician, Quality Performance Analyst, and Quality Improvement Technician for alternative.
Job Description
- Ensure that all quality control processes are carried out effectively and efficiently to meet company standards.
- Maintain a clean and organized work area and provide regular feedback to staff on performance.
- Develop and implement quality control procedures to ensure compliance with applicable regulations, industry standards, and customer specifications.
- Monitor production processes to detect potential problems and take corrective action as necessary.
- Review and analyze data from quality control tests and make recommendations for improvement.
- Conduct quality audits to evaluate the effectiveness of existing quality control processes.
- Train new employees in quality control procedures and techniques.
- Develop and implement corrective and preventive actions in response to customer complaints or quality control issues.
- Work collaboratively with other departments to ensure product meets customer requirements.
- Prepare reports for management on quality assurance activities and results.
Skills and Competencies to Have
- Knowledge of quality assurance principles and techniques.
- Analytical skills for identifying trends in data and process improvements.
- Ability to develop and implement quality control plans.
- Ability to work effectively with cross-functional teams.
- Excellent communication skills for coordinating with stakeholders.
- Proficiency in using quality control software and statistical tools.
- Knowledge of current industry standards and best practices.
- Ability to identify potential areas of non-compliance and take corrective action.
- Strong problem solving and conflict resolution skills.
- Excellent organizational and time management skills.
The ability to effectively lead a quality control team is essential to any business. Quality control leads must be organized, detail-oriented, and able to prioritize tasks. They must also be able to effectively communicate with both their team members and the management team, as well as demonstrate strong problem-solving and critical thinking skills.
Quality control leads are responsible for ensuring that all processes are followed correctly and that products meet the standards of the company. Their efforts help to ensure customer satisfaction, reduce costs, and improve the overall efficiency of the organization. In order for quality control leads to be successful, they must be able to effectively manage their time, delegate tasks, and mentor their team members.
This combination of skills is essential for any successful quality control lead.
Quality Engineer, Quality Performance Manager, and Quality Control Inspector are related jobs you may like.
Frequent Interview Questions
- What experience do you have in quality control and assurance?
- How would you ensure that quality standards are met on each project?
- What methods do you use to track and measure the progress of quality control initiatives?
- What challenges have you faced while leading a quality control team?
- What strategies have you implemented to improve overall product quality?
- How do you stay up-to-date with the latest trends and technologies in quality control?
- How do you motivate and encourage team members to meet quality targets?
- Describe your approach to training team members on quality control processes and procedures.
- What steps do you take to deliver timely, accurate, and reliable results?
- How do you prioritize tasks and manage competing demands when leading a quality control team?
Common Tools in Industry
- Quality Assurance (QA) Software. This is a software solution that aids in the process of testing and validating software applications to ensure that they meet predetermined specifications and standards. (eg: Ranorex)
- Automated Testing Tools. These tools automate the process of testing, ensuring that all tests are completed in a timely manner. (eg: Selenium)
- Defect Tracking Software. This software helps track and manage any and all defects that appear during the development or testing process. (eg: Bugzilla)
- Performance Testing Tools. These tools help validate that an application meets performance requirements such as speed and scalability. (eg: Apache JMeter)
- Code Quality Tools. These tools help analyze code and flag any possible issues before they become problems. (eg: Code Climate)
Professional Organizations to Know
- Institute of Quality Assurance (IQA)
- American Society for Quality (ASQ)
- International Organization for Standardization (ISO)
- International Register of Certificated Auditors (IRCA)
- American Association for Laboratory Accreditation (A2LA)
- National Institute of Standards and Technology (NIST)
- International Accreditation Forum (IAF)
- International Society for Quality in Healthcare (ISQua)
- Association for the Advancement of Medical Instrumentation (AAMI)
- American Society for Healthcare Engineering (ASHE)
We also have Quality Systems Manager, Quality Assurance Auditor, and Quality Control Manager jobs reports.
Common Important Terms
- Process Quality Control. The process of monitoring and verifying the quality of a product or service throughout the production or delivery cycle.
- Quality Assurance. The process of ensuring that a product or service meets certain standards of quality.
- Quality Metrics. Measures used to assess the quality of a product or service.
- Root Cause Analysis. A process used to identify the underlying cause of an issue or problem.
- Six Sigma. A set of methods and tools to reduce defects and increase efficiency in a process.
- Continuous Improvement. A method of continually identifying and implementing improvements in a process.
- Statistical Process Control. A method of analyzing data to evaluate and improve processes.
- Fault-Tree Analysis. A method of analyzing potential causes of a failure in a system or process.
Frequently Asked Questions
Q1: What is the primary role of a Quality Control Lead? A1: The primary role of a Quality Control Lead is to ensure that all products meet quality standards and comply with applicable regulations and industry standards. They are responsible for developing and implementing quality control systems and procedures, monitoring production performance, and conducting audits to ensure compliance. Q2: What qualities should a Quality Control Lead possess? A2: A Quality Control Lead should possess excellent communication and problem-solving skills, an understanding of product specifications and quality assurance processes, and the ability to analyze data and identify trends. They should also have strong organizational and leadership skills, as well as the ability to work in a team environment. Q3: What are the responsibilities of a Quality Control Lead? A3: The responsibilities of a Quality Control Lead include developing quality control systems and procedures, monitoring production performance, conducting audits to ensure compliance, analyzing data to identify issues and trends, and providing feedback and guidance to production teams. They are also responsible for training personnel on quality control processes and procedures. Q4: How many people does a Quality Control Lead typically manage? A4: A Quality Control Lead typically manages a team of up to 10 people, depending on the size and complexity of the organization. Q5: What qualifications are required to become a Quality Control Lead? A5: To become a Quality Control Lead, the minimum qualifications typically include a degree in engineering or a related field, such as quality assurance or manufacturing. Experience in quality control is also desirable.What are jobs related with Quality Control Lead?
- Quality Improvement Lead
- Quality Support Specialist
- Quality Performance Coordinator
- Quality Support Manager
- Quality Systems Analyst
- Quality Support Coordinator
- Quality Systems Coordinator
- Quality Performance Specialist
- Quality Support Analyst
- Quality Systems Specialist
Web Resources
- What is a Manufacturing Quality Controller? | Goodwin University www.goodwin.edu
- Quality Control Course | Engineering Courses | Purdue Online Learning engineering.purdue.edu
- Quality control Harvard Gazette news.harvard.edu
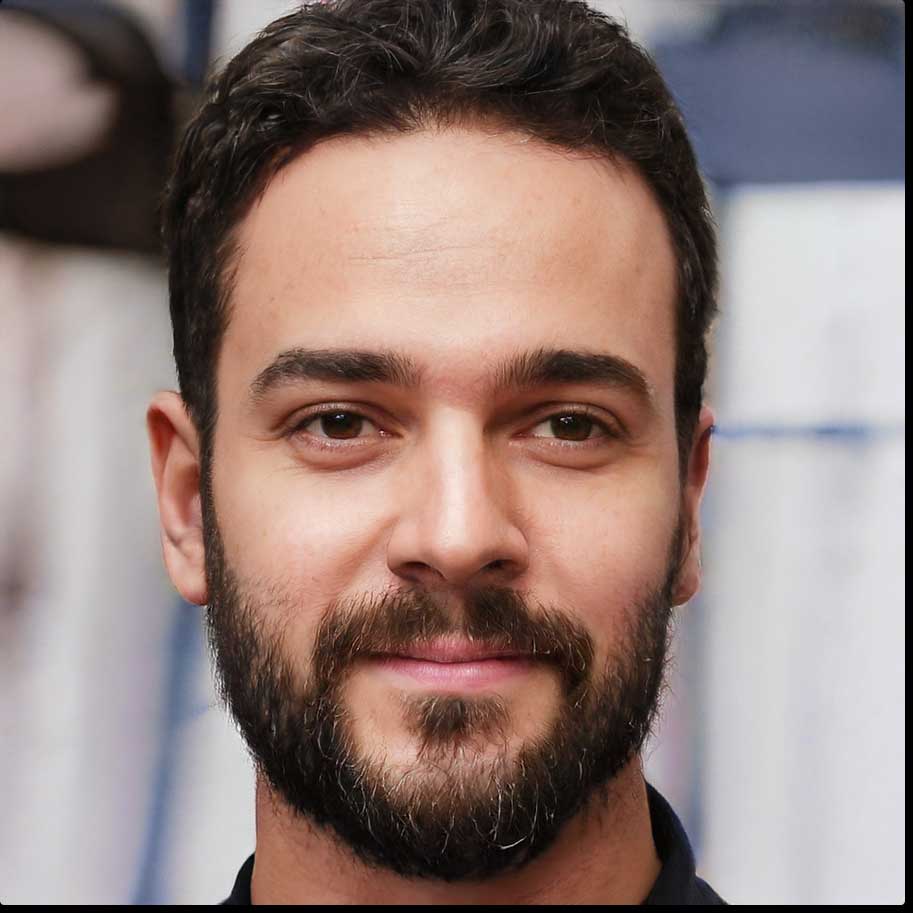