How to Be Quality Systems Coordinator - Job Description, Skills, and Interview Questions
Poor quality systems can lead to a decrease in customer satisfaction, resulting in a decrease in sales and profits. In order to maintain customer satisfaction and increase profits, it is essential for businesses to have a Quality Systems Coordinator. A Quality Systems Coordinator is responsible for developing, implementing, and monitoring the company's quality system.
They ensure that the company meets the standards set out by customers and regulatory bodies, as well as ensuring that quality processes are followed. A Quality Systems Coordinator is a key role in any organization as they will be able to identify and address any issues before they become major problems, thus providing customers with reliable products or services.
Steps How to Become
- Earn a Bachelors Degree. A bachelors degree in a field such as quality management, industrial engineering, or business management is necessary to become a quality systems coordinator.
- Get Relevant Work Experience. Quality systems coordinators must have extensive knowledge of quality control procedures and related systems. Gaining relevant work experience in quality management through internships or entry-level positions is beneficial.
- Obtain Certification. Earning a certification, such as the Certified Quality Engineer or the Certified Manager of Quality/Organizational Excellence, shows employers that an individual has attained a certain level of competency and knowledge in the field.
- Develop Technical Skills. Quality systems coordinators need to have a thorough understanding of various software programs used for quality control and assurance. Learning about programs such as Six Sigma, Total Quality Management, and Lean Manufacturing can help individuals become more competitive in the job market.
- Possess Strong Analytical Skills. Quality systems coordinators must be able to analyze data and evaluate processes to identify areas of improvement. Having strong analytical skills is essential for this position.
- Develop Communication Skills. Quality systems coordinators must be able to communicate effectively with all levels of personnel, from entry-level staff to top executives. Developing strong verbal and written communication skills will help individuals stand out in the job market.
The success of any organization depends on the quality of its systems, and the ability of its staff to use them effectively. To ensure that systems are up to date and used efficiently, a Quality Systems Coordinator is an essential role. This coordinator is responsible for maintaining the accuracy and integrity of the system, as well as for training staff to use it properly.
They also make sure that the system is compliant with any applicable laws and regulations. By having a Quality Systems Coordinator, organizations can be more confident that their systems are working correctly and that their staff are receiving the necessary education to use them properly. This helps to minimize errors and ensure that operations run smoothly.
You may want to check Quality Improvement Engineer, Quality Systems Analyst, and Quality Support Coordinator for alternative.
Job Description
- Develop and maintain quality systems to ensure the highest product quality.
- Monitor the implementation of quality requirements and ensure compliance with quality standards.
- Collaborate with cross-functional teams to identify areas for improvement and develop action plans.
- Manage the implementation of corrective actions to resolve quality issues.
- Perform process audits to evaluate compliance with established quality standards.
- Prepare and analyze statistical data to identify trends in quality issues.
- Develop and implement procedures to ensure the accuracy of data and product quality.
- Investigate customer complaints and determine root causes and corrective actions.
- Monitor supplier performance against quality criteria.
- Maintain quality system records and prepare reports as required.
Skills and Competencies to Have
- Knowledge of quality systems and standards
- Knowledge of FDA regulations
- Proficient in data analysis and interpretation
- Ability to work collaboratively with various stakeholders
- Excellent communication and problem-solving skills
- Ability to develop and implement quality systems
- Strong organizational and time management skills
- Ability to meet deadlines
- Experience with documentation and record keeping
- Proficient in software applications such as Microsoft Office Suite
Cause: Quality Systems Coordinators are responsible for ensuring that a businesss quality systems are in compliance with relevant regulations and standards. Effect: As such, the most important skill for a Quality Systems Coordinator to have is a strong understanding of quality systems and regulations. This means having a thorough knowledge of the standards, laws, and procedures that govern the specific industry they are working in.
they must have excellent organizational skills in order to keep track of all the documents that must be maintained for compliance. Furthermore, Quality Systems Coordinators must have excellent communication skills in order to effectively convey information to management and other stakeholders. Finally, they must be able to demonstrate strong problem solving skills in order to resolve any issues that may arise from either the system or its users.
Quality Performance Manager, Quality Improvement Technician, and Quality Assurance Supervisor are related jobs you may like.
Frequent Interview Questions
- What experience do you have in quality systems and management?
- How do you stay up-to-date with quality systems concepts, standards and best practices?
- What methods do you use to ensure compliance with quality standards?
- Describe a time when you implemented a new quality system or process?
- How do you ensure that quality requirements are met consistently?
- What experience do you have with auditing and corrective action processes?
- How do you ensure that customer complaints and feedback are handled properly?
- What strategies do you use to identify areas of improvement in the quality system?
- What challenges have you faced in quality systems and how did you overcome them?
- How do you motivate your team to achieve quality goals and objectives?
Common Tools in Industry
- Project Management Software. Used to manage large projects, typically with multiple stakeholders and teams. Examples: Microsoft Project, Trello.
- Quality Management Software. Used to monitor product and service quality standards and performance. Examples: Lean Six Sigma, ISO 9001.
- Document Control Software. Used to track and control the creation, maintenance, and storage of documents. Examples: Documentum, SharePoint.
- Training Management Software. Used to manage employee training and compliance. Examples: SkillSoft, Pluralsight.
- Risk Management Software. Used to identify, assess, and mitigate potential risks in a business environment. Examples: RiskLens, Enablon Risk Manager.
- Audit Management Software. Used to streamline the audit process and ensure compliance with regulations or other standards. Examples: AuditBoard, MetricStream.
Professional Organizations to Know
- International Society for Quality in Health Care (ISQua)
- American Society for Quality (ASQ)
- Institute of Quality Assurance (IQA)
- Healthcare Quality Association on Accreditation (HQAA)
- Association for the Advancement of Medical Instrumentation (AAMI)
- American College of Healthcare Executives (ACHE)
- International Association for Healthcare Quality (IAHQ)
- National Association for Healthcare Quality (NAHQ)
- The American Board of Quality Assurance and Utilization Review Physicians (ABQAURP)
- The Joint Commission (TJC)
We also have Quality Performance Analyst, Quality Assurance Coordinator, and Quality Improvement Analyst jobs reports.
Common Important Terms
- Quality Assurance (QA). A set of activities intended to ensure that a product or service meets certain standards of quality.
- Quality Control (QC). A process for verifying that a product or service meets certain standards of quality.
- Quality Management (QM). The overall process of planning, designing, and executing activities to ensure that a product or service meets the required standards of quality.
- Quality Metrics. A set of metrics used to measure the quality of a product or service.
- Quality Plans. A set of documented instructions for ensuring that a product or service meets the required standards of quality.
- Quality Standards. A set of guidelines and rules for ensuring that a product or service meets the required standards of quality.
- Risk Management. A process for identifying, analyzing, and mitigating risks associated with a product or service.
- Regulatory Compliance. A process for ensuring that a product or service complies with applicable regulations.
Frequently Asked Questions
What is the primary job responsibility of a Quality Systems Coordinator?
The primary job responsibility of a Quality Systems Coordinator is to plan, implement, manage and maintain quality systems and processes in order to ensure compliance with regulatory and industry standards.
What qualifications are required to become a Quality Systems Coordinator?
Generally, a Quality Systems Coordinator should have a bachelor's degree in a related field such as engineering, quality management, or business administration, as well as experience in quality assurance, auditing, and/or project management.
How do Quality Systems Coordinators ensure regulatory compliance?
Quality Systems Coordinators ensure regulatory compliance by developing and implementing quality systems that meet or exceed applicable regulatory requirements. They also monitor and audit processes to ensure compliance and take corrective action when necessary.
What types of industries typically employ Quality Systems Coordinators?
Quality Systems Coordinators are typically employed in highly regulated industries such as healthcare, pharmaceuticals, automotive, aerospace, and food production.
What is the average salary for a Quality Systems Coordinator?
According to PayScale, the average salary for a Quality Systems Coordinator is approximately $61,000 per year.
What are jobs related with Quality Systems Coordinator?
- Quality Assurance Consultant
- Quality Manager
- Quality Management Manager
- Quality Improvement Coordinator
- Quality Assurance Lead
- Quality Systems Specialist
- Quality Assurance Technician
- Quality Control Lead
- Quality Management Analyst
- Quality Performance Specialist
Web Resources
- Quality Systems - Bowling Green State University www.bgsu.edu
- Quality Systems Management Degree | Northwestern SPS: sps.northwestern.edu
- Quality Management Program - Online Bachelor's Degree global.cambridgecollege.edu
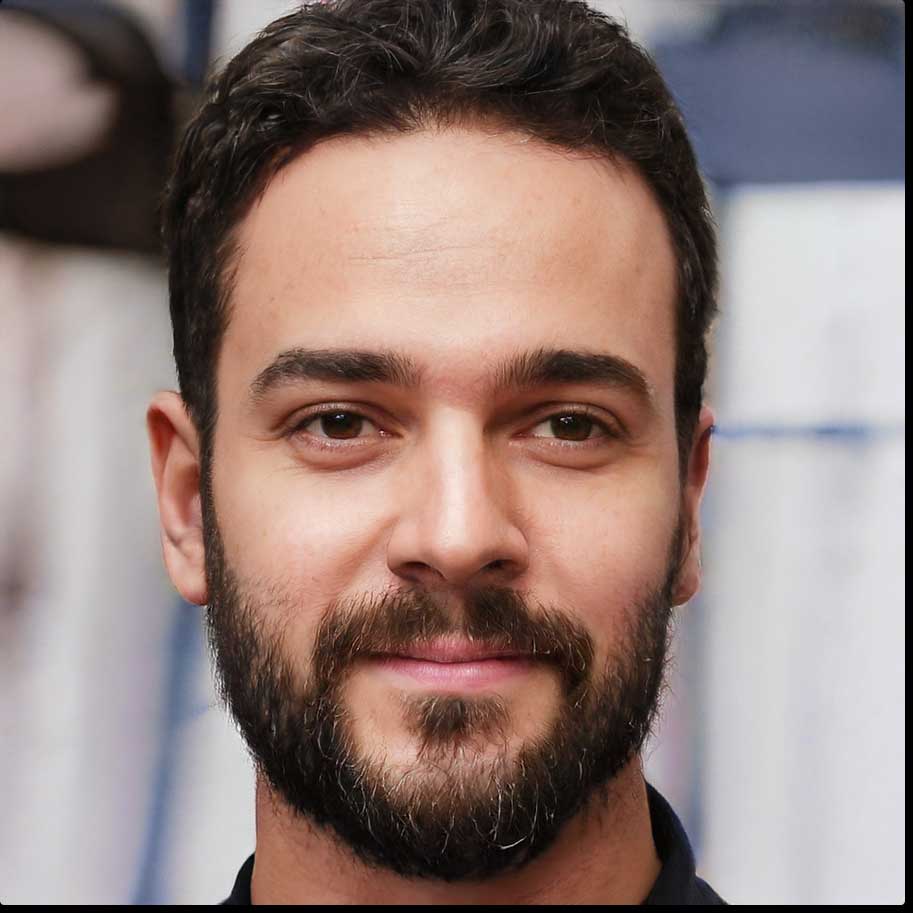