How to Be Quality Improvement Technician - Job Description, Skills, and Interview Questions
Steps How to Become
- Obtain a High School Diploma or GED. To become a Quality Improvement Technician, you must first have a high school diploma or GED.
- Complete an Associate Degree. To become a Quality Improvement Technician, you must have an Associate Degree in Quality Control/ Improvement from an accredited college or university.
- Obtain Certification. Most employers prefer that Quality Improvement Technicians have certification from a recognized organization such as the American Society for Quality (ASQ). Certification demonstrates your knowledge and commitment to quality improvement and can help you stand out from the competition when applying for jobs.
- Gain Experience. Quality Improvement Technicians must have experience in the field and in the quality improvement process. You can gain experience through internships, working on quality improvement projects, or by taking on additional responsibilities at your current job.
- Take Continuing Education Courses. Quality Improvement Technicians must stay up to date on the latest trends and technologies in the field. Taking continuing education courses is an excellent way to stay ahead in the field and to demonstrate your commitment to quality improvement.
The quality improvement technician must stay ahead and competent in order to ensure that they remain successful in their role. One way to accomplish this is to stay up to date with the latest trends and technology in the field. This can be done by attending seminars and webinars, reading industry publications, and networking with colleagues.
the technician should remain knowledgeable in the tools and processes used to measure and improve quality. Keeping up with certifications related to quality improvement can also help a technician stay ahead of the competition. By taking these steps, the quality improvement technician is better equipped to lead teams and provide valuable insights that can drive positive change.
You may want to check Quality Assurance Consultant, Quality Improvement Specialist, and Quality Assurance Technician for alternative.
Job Description
- Participate in quality improvement initiatives and projects to identify improvement opportunities.
- Monitor and analyze process performance to identify areas for improvement.
- Assist in developing, testing and implementing process improvement solutions.
- Develop, document and maintain quality improvement plans, processes and procedures.
- Monitor and measure the effectiveness of quality improvement initiatives and suggest corrective action when needed.
- Implement and maintain lean management principles to improve operational efficiency.
- Create reports to track progress of quality improvement initiatives.
- Provide training and support to staff on process improvement topics.
- Collaborate with teams across multiple departments to ensure quality standards are met.
- Monitor quality control systems and processes to ensure compliance with established standards.
- Identify root cause of process issues and develop strategies to prevent recurrence.
- Perform data analysis to identify trends, opportunities and risks.
- Address customer complaints in a timely manner and work to resolve issues quickly and effectively.
Skills and Competencies to Have
- Knowledge of quality assurance/control principles and techniques.
- Ability to read and interpret engineering drawings, schematics, and technical documents.
- Knowledge of statistical process control and data analysis techniques.
- Proficient in using specialized inspection and measurement equipment.
- Experience with root cause analysis and corrective action implementation.
- Ability to develop, implement, and maintain quality control systems.
- Ability to plan and organize work in order to meet deadlines.
- Excellent communication and interpersonal skills.
- Ability to interact effectively with management and other personnel.
- Knowledge of applicable federal and state regulations regarding quality assurance/control.
The Quality Improvement Technician plays an important role in ensuring the quality of products and services. They use various techniques and tools to analyze data and make improvements to processes, products and services. One of the most important skills for a Quality Improvement Technician is problem-solving.
They need to be able to identify problems, analyze data and develop solutions to improve quality. the Quality Improvement Technician needs to have excellent communication skills. They must be able to communicate effectively with clients, colleagues and stakeholders in order to ensure that everyone is on the same page in terms of the desired outcome.
They must also be able to work well in teams and collaborate with others to ensure the quality improvement process is successful. Lastly, having strong organizational skills is essential for the Quality Improvement Technician to stay on top of deadlines and tasks. these skills are essential for the Quality Improvement Technician to be successful in their role.
Quality Performance Specialist, Quality Control Inspector, and Quality Technician are related jobs you may like.
Frequent Interview Questions
- What experience do you have in Quality Improvement?
- What processes have you implemented to improve quality?
- How do you ensure accuracy and compliance with industry standards?
- What strategies do you use to identify opportunities for improvement?
- How do you ensure that corrective actions are taken to address quality issues?
- What methods do you employ to ensure customer satisfaction?
- What challenges have you faced in the past while working on Quality Improvement projects?
- How do you stay up-to-date on the latest Quality Improvement trends and technologies?
- Describe a time when you successfully identified and corrected a quality issue.
- How do you collaborate with other departments to ensure quality across all areas of the business?
Common Tools in Industry
- Quality Control Tools. These tools help to measure, analyze, and improve the quality of products and services. Examples: Statistical Process Control (SPC), Failure Mode and Effects Analysis (FMEA).
- Root Cause Analysis. This tool helps to identify and analyze the root causes of problems or issues. Example: Ishikawa Diagram.
- Process Mapping. This tool is used to document the steps, inputs, and outputs involved in a process. Example: Value Stream Mapping.
- Continuous Improvement. This tool helps to identify and implement areas for improvement in a process. Examples: Kaizen, Six Sigma.
- Lean Manufacturing. This tool helps to reduce wasted time and resources in manufacturing processes. Example: Kanban.
Professional Organizations to Know
- American Society for Quality (ASQ)
- Institute for Healthcare Improvement (IHI)
- Lean Enterprise Institute
- American College of Healthcare Executives (ACHE)
- Association for Professionals in Infection Control and Epidemiology (APIC)
- American Health Information Management Association (AHIMA)
- Association for Quality and Participation (AQP)
- National Association for Healthcare Quality (NAHQ)
- National Association of Long Term Care Administrator Boards (NAB)
- International Society for Quality in Healthcare (ISQua)
We also have Quality Assurance Supervisor, Quality Control Manager, and Quality Assurance Inspector jobs reports.
Common Important Terms
- Quality Control. The process of evaluating and maintaining the quality of a product or service to ensure it meets specific standards.
- Quality Assurance. A system of procedures and techniques used to ensure that a product or service adheres to specified standards.
- Process Improvement. A systematic approach to improving the efficiency, effectiveness, and cost-effectiveness of a process.
- Root Cause Analysis. A problem-solving technique used to identify the underlying cause of a problem in order to solve it.
- Statistical Process Control. A tool used to measure, analyze, and control processes by monitoring key performance indicators.
- Lean Manufacturing. A philosophy of production that eliminates waste and maximizes efficiency.
- Six Sigma. A data-driven methodology used to improve performance by reducing variation and eliminating defects.
- Kaizen. A continuous improvement philosophy focused on small, incremental improvements to processes and products.
Frequently Asked Questions
What is a Quality Improvement Technician?
A Quality Improvement Technician is a professional who works to improve the quality of products and services. They use a variety of techniques such as process improvement, root cause analysis, and statistical methods to identify areas for improvement and develop strategies to implement them.
What qualifications are needed to become a Quality Improvement Technician?
To become a Quality Improvement Technician, you typically need a bachelor's degree in a related field such as engineering, mathematics, or statistics. Additionally, many employers may require certification in quality management systems such as ISO 9001 or Six Sigma.
What skills do Quality Improvement Technicians need?
Quality Improvement Technicians need strong communication, problem-solving, and analytical skills. They should also have an understanding of process improvement methods such as Lean Six Sigma, Kaizen, and Total Quality Management. Additionally, they should have knowledge of data analysis concepts and tools such as process mapping and control charts.
What is the job outlook for Quality Improvement Technicians?
The job outlook for Quality Improvement Technicians is positive. According to the Bureau of Labor Statistics, the job outlook for quality control inspectors is projected to grow 6% from 2019-2029, which is faster than the average for all occupations.
What is the average salary of a Quality Improvement Technician?
The average salary of a Quality Improvement Technician varies depending on experience level and location. According to PayScale, the median salary for a Quality Improvement Technician is $56,622 per year.
What are jobs related with Quality Improvement Technician?
- Quality Assurance Coordinator
- Quality Management Coordinator
- Quality Support Specialist
- Quality Management Manager
- Quality Support Manager
- Quality Improvement Inspector
- Quality Manager
- Quality Support Analyst
- Quality Systems Manager
- Quality Improvement Analyst
Web Resources
- Quality Technician - Anoka Tech anokatech.edu
- Quality Technician Certificate | Northcentral Technical College www.ntc.edu
- Skills for Success - Quality Technician - Purdue mep.purdue.edu
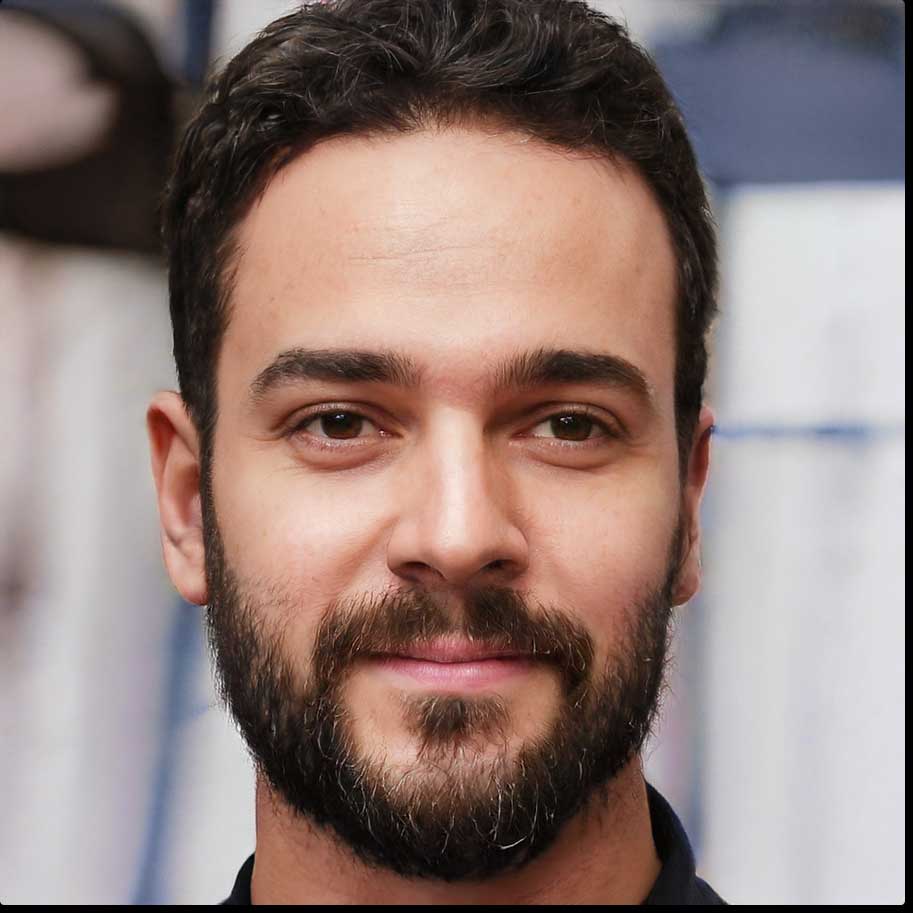