How to Be Quality Performance Specialist - Job Description, Skills, and Interview Questions
Steps How to Become
- Earn a Bachelor's Degree. The first step to becoming a Quality Performance Specialist is to earn a bachelor's degree. A degree in a relevant field such as industrial engineering, business management, or quality assurance is recommended.
- Attain Work Experience. While most employers prefer to hire individuals with experience in the field, entry-level positions are available. Working as a quality analyst, quality control specialist, or project manager is a great way to gain the skills and knowledge necessary to become a Quality Performance Specialist.
- Gain Certification. Certifications such as the Certified Quality Technician (CQT), Certified Quality Manager (CQM), and Certified Quality Auditor (CQA) are often preferred by employers and demonstrate a high level of knowledge and expertise.
- Take a Quality Performance Course. Taking a quality performance course is another great way to gain the skills and knowledge necessary to become a Quality Performance Specialist. Courses such as Six Sigma, Lean Manufacturing, and Statistical Process Control will help prepare individuals for the role of Quality Performance Specialist.
- Obtain a Quality Performance Position. After gaining the necessary qualifications and experience, individuals can apply for positions as a Quality Performance Specialist. Many companies have specific job postings for this role, while other companies may allow candidates to apply with their general application.
Maintaining a high level of competence and staying up-to-date in the field of Quality Performance Specialists is essential to success. To achieve this, it is important to stay informed on the latest developments and trends in the industry and to continually expand one's knowledge and skills. This can be done by taking advantage of opportunities such as attending conferences, seminars, webinars, or other forms of professional development.
staying active in professional organizations and engaging in networking activities can provide insights into best practices and help keep Quality Performance Specialists current with the latest industry trends. by committing to furthering their education, staying connected to their peers, and staying abreast of new technologies and methodologies, Quality Performance Specialists can ensure they remain knowledgeable and effective in their field.
You may want to check Quality Management Analyst, Quality Systems Analyst, and Quality Improvement Lead for alternative.
Job Description
- Develop and implement quality assurance processes and procedures to ensure product and service standards are met.
- Analyze customer feedback to understand customer satisfaction levels and identify areas of improvement.
- Monitor and audit quality control procedures and processes to ensure compliance with established standards.
- Develop and implement corrective action plans to address quality issues.
- Create and present reports on quality performance to management.
- Collaborate with other departments to identify potential improvement opportunities.
- Train and mentor staff on quality control processes and procedures.
- Utilize tools such as Six Sigma and Lean Manufacturing to identify process inefficiencies and devise strategies for improvement.
- Research industry best practices and track trends in quality performance.
- Monitor production lines and inspect finished products to ensure quality standards are met.
Skills and Competencies to Have
- Knowledge of performance improvement methods and techniques
- Ability to analyze problems and develop creative solutions
- Ability to effectively communicate ideas, concepts and solutions
- Ability to work with cross-functional teams
- Knowledge of process improvement methodologies such as Lean Six Sigma
- Ability to manage multiple projects and tasks
- Ability to identify and measure performance metrics
- Knowledge of organizational change management
- Understanding of data analysis techniques and tools
- Ability to identify and prioritize customer needs
- Strong organizational and problem-solving skills
- Excellent interpersonal and communication skills
Being a Quality Performance Specialist requires a combination of technical and interpersonal skills. A successful Quality Performance Specialist must have excellent problem-solving capabilities, be detail-oriented and have a knack for improving processes and systems. They must also have strong organizational skills, be able to multitask, and have strong interpersonal skills in order to effectively communicate their findings to other departments and stakeholders.
Having an understanding of quality assurance principles, as well as familiarity with industry standards and regulations, is also essential for success in this role. Quality Performance Specialists should also have knowledge of data analysis techniques, software development best practices, and techniques for collecting and assessing customer feedback. All these skills come together to help Quality Performance Specialists identify areas of improvement and recommend strategies that will increase the quality of products and services.
Quality Improvement Specialist, Quality Support Manager, and Quality Technician are related jobs you may like.
Frequent Interview Questions
- Tell us about your experience in developing and implementing quality systems in a performance setting.
- How do you handle challenging customer service situations?
- How do you ensure quality performance in the workplace?
- Describe how you have implemented successful strategies to improve customer satisfaction.
- Are you familiar with current performance standards and ISO regulations?
- Describe a time when you had to make a difficult decision that affected the quality of a product or service.
- How do you ensure that all quality control measures are being followed?
- What techniques do you use to stay organized when managing multiple quality performance tasks?
- How do you prioritize tasks to ensure that the highest priority tasks are always completed first?
- How have you used data to make decisions and improve performance?
Common Tools in Industry
- Quality Control Tools. These tools help monitor and measure the quality of a product or service. Examples include process control plans, Six Sigma tools, statistical process control (SPC), and fault tree analysis.
- Performance Metrics Tools. These tools measure performance indicators such as customer satisfaction, on-time delivery, cost reduction, and defect prevention. Examples include Balanced Scorecards and Key Performance Indicators (KPIs).
- Process Improvement Tools. These tools help to analyze and optimize processes. Examples include Lean Six Sigma, Kaizen, and the Theory of Constraints.
- Problem Solving Tools. These tools are used to identify, analyze, and solve problems. Examples include root cause analysis (RCA), 5 Whys, and Ishikawa diagrams.
- Quality Systems Tools. These tools help to establish, maintain, and improve quality systems. Examples include ISO 9001 and Total Quality Management (TQM).
Professional Organizations to Know
- American Society for Quality (ASQ)
- International Quality Federation (IQF)
- Institute of Industrial and Systems Engineers (IISE)
- International Organization for Standardization (ISO)
- The Malcolm Baldrige National Quality Award (MBNQA)
- Project Management Institute (PMI)
- American Statistical Association (ASA)
- Lean Certification Alliance (LCA)
- Association for Quality and Participation (AQP)
- Society for Quality Assurance (SQA)
We also have Quality Support Analyst, Quality Performance Analyst, and Quality Engineer jobs reports.
Common Important Terms
- Quality Assurance (QA). A process of ensuring that products meet certain standards or criteria.
- Quality Control (QC). A process of verifying the quality of a product.
- Quality Improvement (QI). A process of making changes to products or services in order to make them better.
- Root Cause Analysis (RCA). A process of determining the underlying cause of a problem or issue.
- Process Mapping. A graphical representation of the steps involved in a process.
- Six Sigma. A methodology used to identify and eliminate defects in a process.
- Lean Six Sigma. An approach combining the principles of Lean Manufacturing and Six Sigma to improve quality and reduce waste.
- Statistical Process Control (SPC). A method of monitoring and controlling a process using statistical measurements.
- Kaizen. A Japanese term for continuous improvement, or the ongoing effort to improve processes.
- Risk Management. A process of identifying, assessing, and mitigating potential risks to the success of a project or organization.
Frequently Asked Questions
Q1: What is a Quality Performance Specialist? A1: A Quality Performance Specialist is a professional who is responsible for improving organizational performance by assessing and evaluating the quality of services and products. Q2: What skills are required to be a Quality Performance Specialist? A2: To be a successful Quality Performance Specialist, one must have excellent problem-solving skills, communication and interpersonal abilities, knowledge of industry standards and regulations, and experience with data collection and analysis. Q3: What is the typical job outlook for Quality Performance Specialists? A3: According to the US Bureau of Labor Statistics, the job outlook for Quality Performance Specialists is expected to grow by 7% through 2026. Q4: What are the typical duties of a Quality Performance Specialist? A4: Typical duties of a Quality Performance Specialist include analyzing customer feedback, conducting quality audits, identifying areas of improvement, developing and monitoring performance metrics, and recommending changes to improve performance. Q5: What is the average salary for a Quality Performance Specialist? A5: According to PayScale, the average salary for a Quality Performance Specialist is $59,452 per year.What are jobs related with Quality Performance Specialist?
- Quality Improvement Engineer
- Quality Management Coordinator
- Quality Improvement Coordinator
- Quality Improvement Technician
- Quality Assurance Technician
- Quality Control Manager
- Quality Systems Specialist
- Quality Assurance Coordinator
- Quality Improvement Analyst
- Quality Performance Manager
Web Resources
- Quality Assurance Specialist | NC State Online and Distance online-distance.ncsu.edu
- Section 1. Achieving and Maintaining Quality Performance ctb.ku.edu
- What is Quality Improvement in Healthcare? | SNHU www.snhu.edu
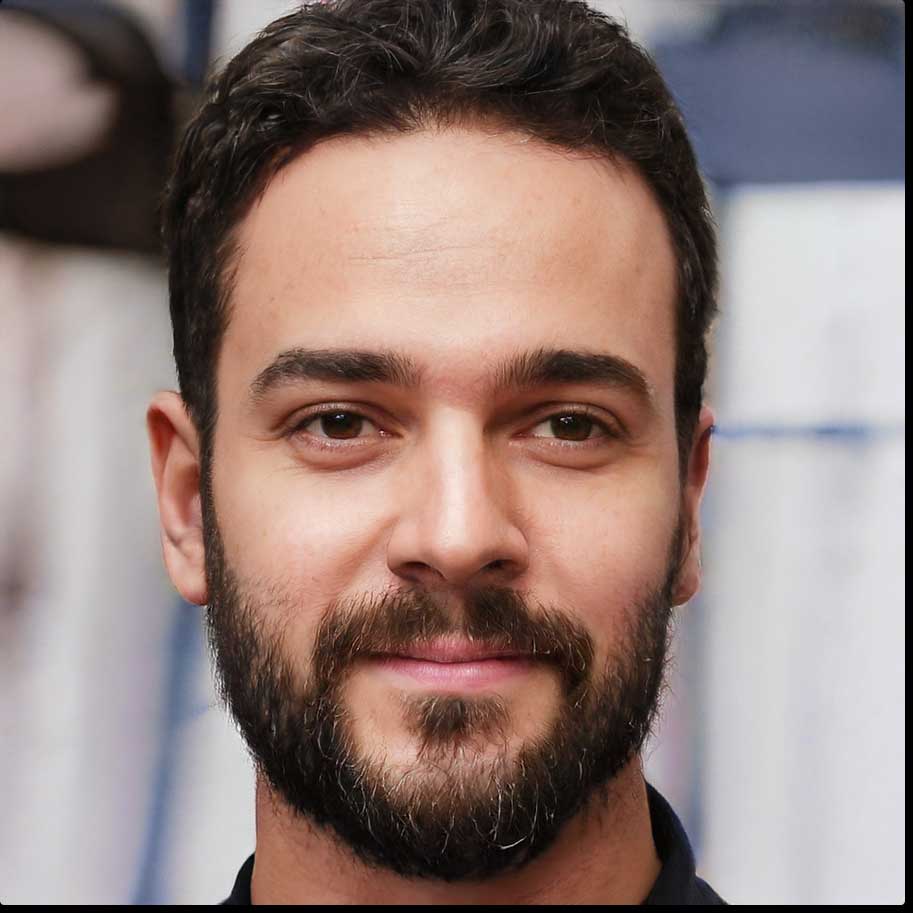