How to Be Quality Management Analyst - Job Description, Skills, and Interview Questions
Poor quality management can lead to significant financial losses for a company. This can include lost sales due to customer dissatisfaction, increased costs due to rework and scrap, and decreased efficiency of operations. A Quality Management Analyst is responsible for developing, implementing, and monitoring processes and procedures to ensure that products and services meet quality standards.
By evaluating existing processes and systems, the analyst can identify gaps and opportunities for improvement and recommend changes to enhance quality assurance. The analyst also assists with developing and executing strategies to reduce defects, improve customer satisfaction, and increase efficiency. a Quality Management Analyst can help a company save money by reducing losses due to poor quality and improving overall customer satisfaction.
Steps How to Become
- Earn a Bachelor's Degree. The first step to becoming a quality management analyst is to earn a bachelor's degree in a related field, such as business administration, engineering, or quality assurance.
- Gain Work Experience. Most employers prefer to hire quality management analysts who have prior work experience in the field. Consider gaining experience by completing an internship or working in a related field.
- Obtain Certification. Obtaining certification as a quality management analyst can help you stand out from other candidates. The American Society for Quality offers various certification options for quality management professionals.
- Show Your Expertise. Quality management analysts must be able to demonstrate their knowledge and abilities in the field. Consider joining a professional organization or taking classes to increase your knowledge of the industry.
- Apply for Jobs. After gaining the necessary experience and certifications, you can begin applying for jobs as a quality management analyst. You may find job postings on job boards, in newspapers, or through professional networks.
The Quality Management Analyst must stay updated and capable in order to effectively identify issues and recommend solutions that will improve an organization's overall quality. To do this, they must stay current on the latest industry trends, best practices, and technological advancements in their field. They should also attend seminars and training sessions so they can continue to build their skills and knowledge.
Quality Management Analysts should actively seek out opportunities to collaborate with peers and mentors to gain new perspectives and further develop their skills and expertise. Doing so will ensure that they are able to provide their organization with the most up-to-date, accurate, and effective solutions for improving their quality standards.
You may want to check Quality Performance Coordinator, Quality Performance Manager, and Quality Improvement Coordinator for alternative.
Job Description
- Lead Quality Management Analyst: Works with the organizations management and staff to ensure that the organization meets quality standards. Develops and implements quality assurance programs and reviews processes, procedures, and systems to ensure they meet established standards.
- Quality Assurance Analyst: Develops and executes test plans, scripts, and procedures to ensure the quality of products and services. Analyzes data to identify trends and potential issues, as well as recommends process improvements.
- Quality Control Analyst: Monitors products, services, and processes for compliance with quality standards. Conducts audits to verify documents and data accuracy.
- Quality Improvement Analyst: Assesses current processes, systems, and products to identify areas for improvement. Develops and implements new quality assurance processes to help the organization meet its goals.
- Quality Systems Analyst: Designs, develops, and maintains quality assurance systems. Analyzes system performance and resolves any issues that arise. Updates documents and records to ensure accuracy and compliance.
Skills and Competencies to Have
- Knowledge of quality assurance principles and techniques
- Experience with quality management systems and processes
- Strong analytical and problem-solving skills
- Excellent communication skills
- Ability to identify potential risks and develop solutions
- Ability to create detailed reports and presentations
- Proficiency in data analysis and statistical methods
- Knowledge of project management principles
- Good organizational, time management, and multitasking abilities
- Knowledge of relevant industry regulations and standards
Quality management analysts play a critical role in ensuring that products and services meet the highest standards of quality. They must possess a strong understanding of the entire product life cycle, from design to delivery. Analysts must also have excellent analytical skills, problem-solving abilities, and knowledge of quality control principles and processes.
As a result, they can identify potential issues early on and develop effective solutions to improve product quality. they must be able to communicate effectively with stakeholders, such as customers and executives, to ensure that their recommendations are understood and implemented. By doing so, they can ensure that products and services reliably meet customer needs and expectations, while also helping to ensure customer satisfaction.
Quality Assurance Lead, Quality Management Coordinator, and Quality Systems Analyst are related jobs you may like.
Frequent Interview Questions
- What experience do you have in quality management?
- How do you ensure that quality standards are met?
- What metrics do you use to measure quality?
- How have you improved the quality assurance process in past roles?
- What do you think are the most important aspects of a successful quality management system?
- How do you handle customer complaints regarding quality?
- What process do you use to identify and address quality issues?
- How do you ensure that employees are following quality standards?
- How have you successfully implemented new quality management systems?
- What experience do you have with developing and executing quality audits?
Common Tools in Industry
- Quality Assurance (QA) Software. Software that helps monitor and improve the quality of products or services. (Example: TestRail)
- Quality Management System (QMS). A comprehensive system for ensuring that a company's products and services meet the necessary quality standards and customer requirements. (Example: ISO 9001)
- Root Cause Analysis (RCA). A tool used to identify the underlying causes of problems and identify solutions to address them. (Example: Ishikawa Diagram)
- Statistical Process Control (SPC). A tool used to monitor and control processes to ensure quality. (Example: SPC Charts)
- Failure Mode and Effects Analysis (FMEA). A tool used to identify potential failures in a product or process and assess their impact. (Example: FMEA Worksheet)
- Quality Audit. An evaluation of an organizations quality practices and policies. (Example: Checklist Audit)
- Six Sigma. A set of practices used to improve processes and reduce defects. (Example: DMAIC Methodology)
- Kaizen. A system of continuous improvement in which employees are encouraged to identify opportunities for improvement. (Example: 5S System)
Professional Organizations to Know
- Association for Quality (AQ)
- American Society for Quality (ASQ)
- International Organization for Standardization (ISO)
- Project Management Institute (PMI)
- International Register of Certified Auditors (IRCA)
- International Federation of Inspection Agencies (IFIA)
- American College of Healthcare Executives (ACHE)
- National Association of Healthcare Quality (NAHQ)
- National Quality Forum (NQF)
- Institute of Quality Assurance (IQA)
We also have Quality Technician, Quality Management Specialist, and Quality Systems Specialist jobs reports.
Common Important Terms
- Quality Assurance (QA) - A process that ensures that products or services meet predetermined standards of quality.
- Quality Control (QC) - The process of ensuring that a product or service meets predetermined standards of quality.
- Process Improvement - The systematic approach to improving processes and procedures in order to increase efficiency and effectiveness.
- Root Cause Analysis (RCA) - A method of problem solving used to identify the root cause of an issue in order to prevent future occurrences.
- Six Sigma - A set of management techniques and tools used to reduce defects and improve quality.
- Lean Methodology - A method of process improvement aimed at reducing waste and increasing efficiency.
- Statistical Process Control (SPC) - A method used to track and analyze process performance in order to identify any potential problems or areas for improvement.
- Total Quality Management (TQM) - A management approach focused on continuous improvement and customer satisfaction.
Frequently Asked Questions
What is a Quality Management Analyst?
A Quality Management Analyst is a professional responsible for overseeing and monitoring the quality of services and products that a company provides. They are responsible for developing and implementing quality assurance processes and systems, and ensuring compliance with applicable regulations and standards.
What skills are necessary for a Quality Management Analyst?
Quality Management Analysts must possess a variety of skills, such as analytical and problem-solving skills, communication and interpersonal skills, and the ability to work collaboratively with a team. They must also have strong knowledge of quality management systems, such as ISO 9001 and Six Sigma, as well as experience in auditing and data analysis.
What qualifications do I need to become a Quality Management Analyst?
To become a Quality Management Analyst, you typically need a bachelor's degree in business administration, engineering, or a related field. Additionally, certifications in quality assurance or quality management systems can help you stand out from the competition.
What is the average salary of a Quality Management Analyst?
According to PayScale, the average salary of a Quality Management Analyst is $58,728 per year. Salaries can vary depending on experience, location, and employer.
What is the job outlook for a Quality Management Analyst?
The job outlook for Quality Management Analysts is expected to grow 5% from 2018 to 2028, according to the U.S. Bureau of Labor Statistics. This growth is slightly slower than the average for all occupations in the United States.
What are jobs related with Quality Management Analyst?
- Quality Management Manager
- Quality Support Analyst
- Quality Control Inspector
- Quality Performance Specialist
- Quality Improvement Technician
- Quality Assurance Inspector
- Quality Control Manager
- Quality Assurance Consultant
- Quality Assurance Technician
- Quality Performance Analyst
Web Resources
- Quality Management and Analytics | Department of Technology tec.illinoisstate.edu
- Quality Management/Analytics Graduate Certificate | Department tec.illinoisstate.edu
- How to Become a QA Analyst - Western Governors University www.wgu.edu
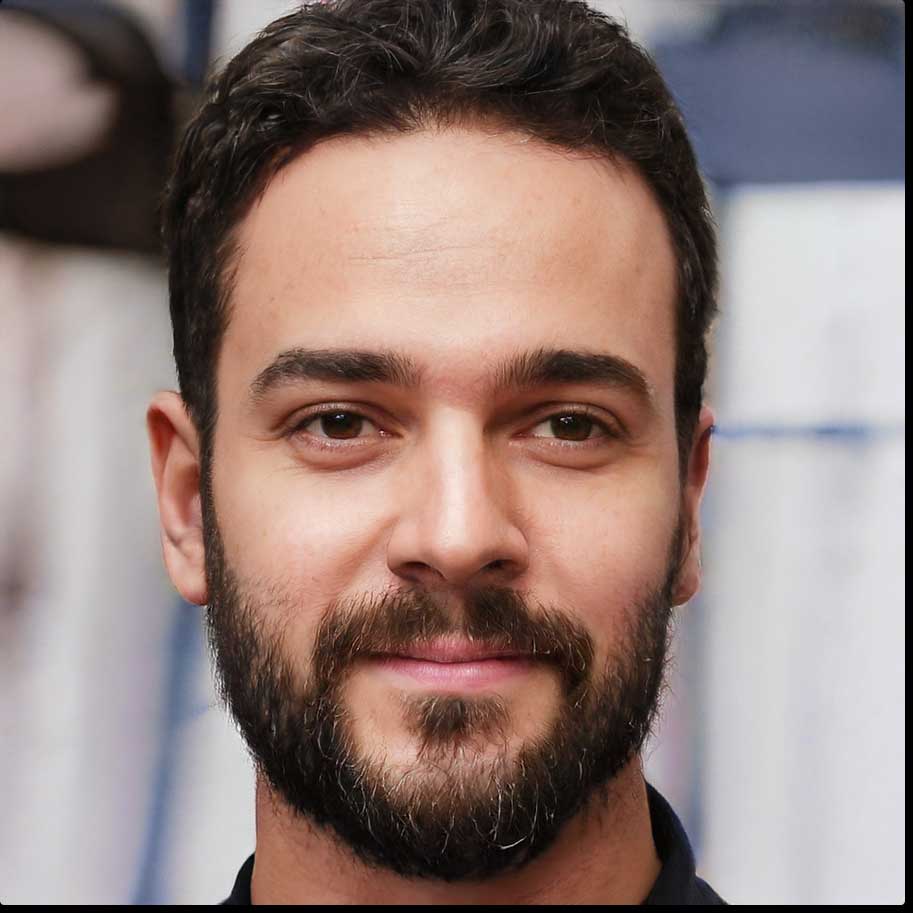