How to Be Quality Performance Coordinator - Job Description, Skills, and Interview Questions
The role of a Quality Performance Coordinator is essential to the success of any organization. By closely monitoring and analyzing the performance of the organization, the Quality Performance Coordinator is able to identify areas of improvement and develop strategies to ensure that the organization can meet its goals and objectives. As a result, the organization is able to improve its overall efficiency, productivity, and customer satisfaction levels.
by monitoring the performance of employees, the Quality Performance Coordinator can ensure that they remain motivated and their performance remains at a high level. Finally, by implementing quality management systems, the Quality Performance Coordinator can promote the continual improvement of organizational processes, ultimately leading to increased profits.
Steps How to Become
- Obtain a Bachelor's Degree. The minimum educational requirement to become a Quality Performance Coordinator is a Bachelor's degree in a related field, such as business management, healthcare administration, or quality assurance. Many employers also prefer applicants who have experience in the healthcare industry.
- Obtain Certification. Quality Performance Coordinators must be certified in quality improvement, performance improvement, or quality management. Certification programs are available through professional organizations such as the American Society for Quality (ASQ), and may require passing an exam.
- Develop Skills and Knowledge. Quality Performance Coordinators must be knowledgeable about the principles of quality improvement, performance improvement, and quality management. They should also have strong communication and interpersonal skills, as well as an understanding of healthcare systems and regulations.
- Gain Experience. Many employers prefer to hire Quality Performance Coordinators who have prior experience in the healthcare industry. It is important to gain experience in quality and performance improvement projects, as well as in data analysis and reporting.
- Join Professional Organizations. Joining professional organizations such as the ASQ can help Quality Performance Coordinators stay up-to-date on industry trends and best practices, network with peers, and take advantage of continuing education opportunities.
You may want to check Quality Support Analyst, Quality Assurance Coordinator, and Quality Systems Analyst for alternative.
Job Description
- Develop and maintain quality performance and compliance standards in accordance with applicable regulations and contractual requirements.
- Monitor performance against quality and compliance requirements; identify areas of non-compliance and work with business units to develop corrective action plans.
- Develop and implement quality performance metrics and reporting systems to ensure consistent performance.
- Monitor customer feedback to identify areas for process and product improvement.
- Facilitate internal and external customer audits, as required.
- Monitor production processes for compliance with established quality standards and safety requirements.
- Investigate customer complaints and recommend corrective actions, as needed.
- Analyze customer feedback and develop strategies to improve customer service and satisfaction.
- Provide guidance, training and mentoring to business units regarding quality performance and compliance requirements.
- Develop and implement quality systems, tools, policies and procedures to support quality initiatives.
- Monitor and report on quality performance data to management and key stakeholders.
- Maintain accurate records of all quality performance activities.
- Participate in continuous improvement initiatives to enhance quality performance.
Skills and Competencies to Have
- Knowledge of quality assurance processes and principles
- Analytical and problem-solving skills
- Excellent communication and interpersonal skills
- Attention to detail and accuracy
- Ability to work independently and as part of a team
- Ability to prioritize tasks and manage time effectively
- Ability to interpret and present data
- Knowledge of applicable regulatory standards
- Knowledge of relevant computer software programs
- Knowledge of Lean Six Sigma methodology
The Quality Performance Coordinator is a highly important role in any organization, and it requires a variety of skills to be successful. One of the most important skills for this position is the ability to communicate effectively with both internal and external stakeholders. Having excellent communication capabilities allows the Quality Performance Coordinator to clearly explain expectations and provide feedback in a timely manner.
Effective communication also enables the Quality Performance Coordinator to build trust and cooperation with other departments, which is critical for achieving organizational goals. having strong problem-solving skills allows the Quality Performance Coordinator to quickly identify and resolve issues in order to maintain a high quality of service. Finally, the Quality Performance Coordinator must possess strong organizational skills in order to remain organized and efficient when managing multiple projects simultaneously.
All of these skills are essential for the successful fulfillment of the Quality Performance Coordinator role.
Quality Technician, Quality Control Lead, and Quality Improvement Manager are related jobs you may like.
Frequent Interview Questions
- What experience do you have in a Quality Performance Coordinator role?
- How have you improved the performance of quality initiatives in your prior roles?
- What methods do you use to measure the success of quality initiatives?
- How do you ensure that quality standards are met across all departments?
- What strategies have you used to increase customer satisfaction with regards to product quality?
- Describe a time when you identified a quality issue and took corrective action.
- How do you stay up-to-date on industry trends and best practices related to quality assurance?
- How do you handle situations when direct reports dont meet quality expectations?
- What have been your biggest challenges when overseeing quality initiatives?
- How have you developed relationships with other departments in order to improve quality processes?
Common Tools in Industry
- Microsoft Excel. Spreadsheet software used to store large amounts of data and perform complex calculations. (Eg: tracking sales performance)
- Tableau. Data visualization software used to create interactive data visualizations. (Eg: creating dashboards to track metrics)
- PowerPoint. Presentation software used to create slideshows to communicate information. (Eg: presenting performance results)
- SharePoint. Collaboration software used to share information, documents, and tasks in a secure environment. (Eg: sharing reports with team members)
- Quality Control Software. Software used to monitor product quality and identify areas of improvement. (Eg: assessing product reliability)
- Six Sigma. A set of management techniques used for problem-solving and process improvement. (Eg: analyzing process efficiency)
- Root Cause Analysis. A method used to identify the underlying cause of an issue and develop solutions. (Eg: identifying sources of errors)
Professional Organizations to Know
- American Society for Quality (ASQ)
- International Quality Federation (IQF)
- Institute of Quality Assurance (IQA)
- National Association for Quality Assurance (NAQA)
- American Productivity and Quality Center (APQC)
- International Organization for Standardization (ISO)
- International Accreditation Forum (IAF)
- International Register of Certificated Auditors (IRCA)
- European Foundation for Quality Management (EFQM)
- National Institute of Standards and Technology (NIST)
We also have Quality Improvement Technician, Quality Management Specialist, and Quality Systems Manager jobs reports.
Common Important Terms
- Quality Assurance. The process of ensuring that products or services meet certain quality and performance standards.
- Quality Control. The process of monitoring and evaluating the quality and performance of products or services to ensure that they meet the desired standards.
- Quality Improvement. The process of systematically improving the quality and performance of products and services to ensure that they meet the desired standards.
- Quality Management System. A systematic approach to managing the quality and performance of products or services to ensure that they meet the desired standards.
- Quality Standards. The criteria for evaluating the quality and performance of products or services.
- Quality Audit. A process of evaluating the quality and performance of products or services to ensure that they meet established standards.
- Quality Metrics. A set of measurements used to track the quality and performance of products or services.
- Quality Assurance Plan. A document that outlines the methods and processes used to ensure the quality and performance of products or services.
- Quality Management Software. Software designed to track, monitor, and manage the quality and performance of products or services.
Frequently Asked Questions
What are the primary duties of a Quality Performance Coordinator?
The primary duties of a Quality Performance Coordinator include monitoring performance to ensure quality standards are met, analyzing data and identifying areas for improvement, developing and implementing quality control processes, and providing feedback to stakeholders.
What qualifications are required for this role?
Qualifications for a Quality Performance Coordinator typically require a degree in a relevant field, such as Quality Management or Business Administration, along with several years of experience in quality control and performance management.
What skills are needed to be successful in this role?
To be successful as a Quality Performance Coordinator, one must possess strong analytical, communication and organizational skills, as well as the ability to work independently. They should also have knowledge of quality systems and methods for measuring performance.
What is the average salary for this position?
According to PayScale, the average salary for a Quality Performance Coordinator is $57,000 per year.
What type of environment does this position typically operate in?
Quality Performance Coordinators typically work in office settings, though they may also provide remote support. They work closely with other departments and stakeholders to ensure that quality standards are being met.
What are jobs related with Quality Performance Coordinator?
- Quality Assurance Lead
- Quality Improvement Inspector
- Quality Performance Analyst
- Quality Control Inspector
- Quality Assurance Technician
- Quality Control Manager
- Quality Support Manager
- Quality Improvement Specialist
- Quality Management Coordinator
- Quality Supervisor
Web Resources
- Job Standard for Quality Assurance Coordinator www.boisestate.edu
- Section 1. Achieving and Maintaining Quality Performance ctb.ku.edu
- Quality and Performance Excellence, Post-Baccalaureate Certificate www.slu.edu
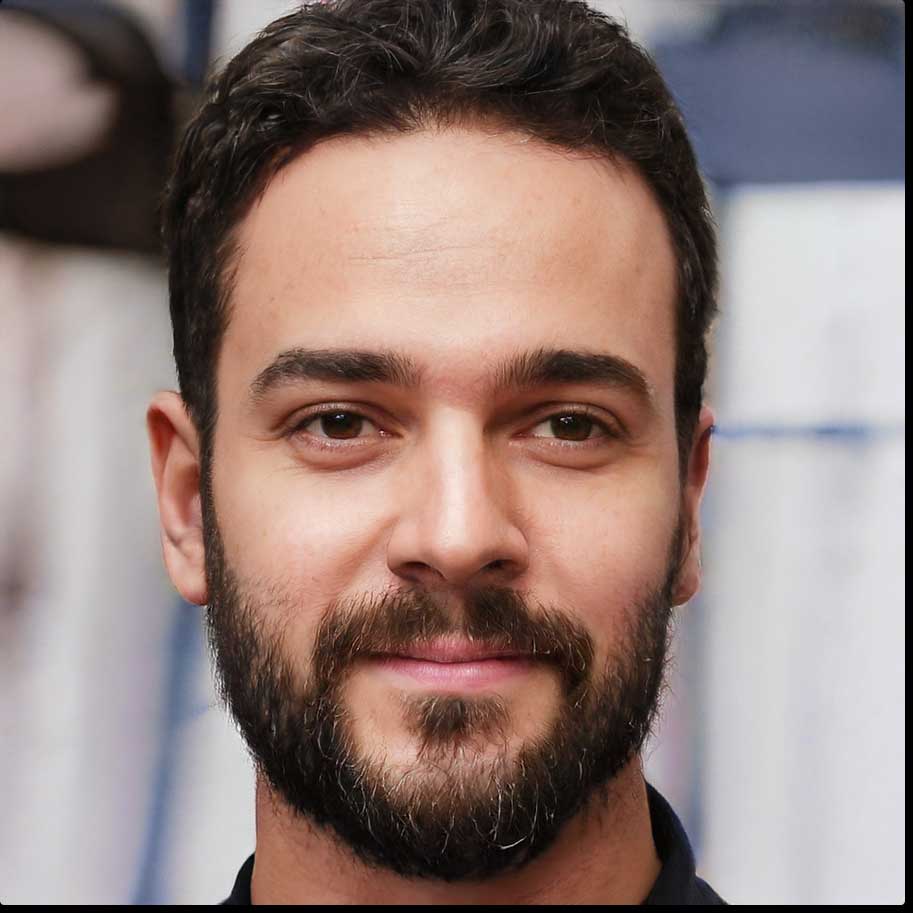