How to Be Quality Improvement Inspector - Job Description, Skills, and Interview Questions
The role of a Quality Improvement Inspector is to ensure that products and services are meeting the desired standards set forth by the company. As a result, customers receive products and services of the highest quality. To do this, Quality Improvement Inspectors use a variety of techniques, such as conducting in-depth inspections, analyzing data, and executing corrective actions.
These efforts lead to improved customer satisfaction, increased profits, and reduced waste. Quality Improvement Inspectors strive to create a culture of quality within the organization, which ultimately creates a better working environment and enhances employee morale.
Steps How to Become
- Earn a Bachelor's Degree. Quality improvement inspectors typically need to earn a bachelor's degree in a field such as engineering, industrial technology, business administration or quality management.
- Obtain Certification. Quality improvement inspectors can pursue certification through the American Society for Quality (ASQ). To qualify for certification, applicants must meet education and work experience requirements and pass an exam.
- Gain Work Experience. Many employers prefer to hire quality improvement inspectors who have prior work experience. Work experience can be acquired through internships, part-time or full-time jobs in quality assurance or related fields.
- Participate in Continuing Education. Quality improvement inspectors should take advantage of continuing education courses to stay abreast of industry trends and changes in regulations and standards.
- Become Proficient in Quality Assurance Software. Quality improvement inspectors should become proficient in a variety of quality assurance software programs such as Minitab, SAS, JMP and SPC. This software is used to monitor and analyze quality data in order to identify areas for improvement.
You may want to check Quality Improvement Specialist, Quality Support Analyst, and Quality Assurance Auditor for alternative.
Job Description
- Quality Improvement Inspector: Responsible for conducting inspections to ensure that products meet quality standards and customer requirements. Inspects raw materials, components, and finished products; evaluates quality of items; and identifies and reports any non-conformances.
- Quality Assurance Manager: Responsible for developing and implementing a quality assurance system to ensure that products meet quality standards and customer requirements. Monitors performance, evaluates data, and initiates corrective action when necessary.
- Quality Control Technician: Responsible for performing tests on manufactured products to ensure that they meet quality standards and customer requirements. Performs a wide variety of tests; preparing test reports; and taking corrective action when necessary.
- Quality Engineer: Responsible for developing, implementing, and maintaining quality assurance systems to ensure that products meet quality standards and customer requirements. Investigates customer complaints; identifies root causes; and implements corrective action when necessary.
- Quality Auditor: Responsible for performing audits of quality systems to ensure that they meet quality standards and customer requirements. Evaluates products; assesses compliance with applicable specifications; and recommends corrective action when necessary.
Skills and Competencies to Have
- Attention to detail
- Understanding of quality control processes
- Ability to read blueprints and technical drawings
- Knowledge of measurement tools and gauges
- Analytical and problem-solving skills
- Knowledge of manufacturing and production processes
- Strong communication and interpersonal skills
- Ability to work independently and in teams
- Ability to meet deadlines and stay organized
- Computer skills, such as Microsoft Office or other software programs
Having good problem-solving skills is an essential skill for Quality Improvement Inspectors. By being able to identify and analyze the causes of issues, they can effectively determine the best solutions to improve the quality of a product. This is especially important in order to prevent future quality issues from arising.
Quality Improvement Inspectors must also be able to communicate effectively with their colleagues and customers to ensure that everyone is on the same page and understands the objectives of the quality improvement efforts. they must be organized and have excellent attention to detail so that they are able to identify even the smallest problems and take corrective action. All these skills are essential in order for Quality Improvement Inspectors to be successful in their jobs.
Quality Management Manager, Quality Assurance Consultant, and Quality Performance Manager are related jobs you may like.
Frequent Interview Questions
- What experience do you have with quality improvement initiatives?
- How do you ensure the accuracy of your work?
- What techniques do you use to identify areas of improvement and how do you prioritize them?
- What steps do you take to ensure customer satisfaction?
- How do you handle difficult situations with customers or colleagues?
- Describe a difficult problem that you have successfully solved in a quality improvement setting.
- How do you stay up-to-date on current quality improvement trends and standards?
- What processes have you implemented to improve quality within an organization?
- How do you handle conflicting opinions when it comes to making decisions about quality improvement?
- What do you think sets you apart from other Quality Improvement Inspectors?
Common Tools in Industry
- Statistical Process Control (SPC). A set of methods used to monitor and control quality by tracking production data and identifying trends and outliers. (e. g. using data to detect defects in a manufacturing process)
- Failure Mode and Effects Analysis (FMEA). A method used to identify potential failures in a process and their associated effects. (e. g. identifying conditions that may cause a production line to malfunction)
- Root Cause Analysis (RCA). A method used to identify the underlying cause of an issue or problem. (e. g. determining why a product is not meeting its desired quality standards)
- Design of Experiments (DOE). A statistical method used to determine the relationship between input factors and output response. (e. g. testing different combinations of materials and techniques to determine the optimal process for a particular product)
- Lean Six Sigma. A set of methods used to improve the efficiency and effectiveness of processes and reduce waste. (e. g. improving cycle time and eliminating non-value added activities in a manufacturing process)
Professional Organizations to Know
- American Society for Quality (ASQ)
- Institute for Healthcare Improvement (IHI)
- International Society for Quality in Healthcare (ISQua)
- National Association for Quality Assurance (NAQA)
- International Organization for Standardization (ISO)
- National Institute for Standards and Technology (NIST)
- American Association for Accreditation of Ambulatory Surgery Facilities (AAAASF)
- The Joint Commission (TJC)
- Healthcare Quality Association on Accreditation (HQAA)
- American College of Healthcare Executives (ACHE)
We also have Quality Control Inspector, Quality Management Coordinator, and Quality Engineer jobs reports.
Common Important Terms
- Quality Assurance (QA). A systematic approach to ensuring that products, services, and processes meet the requirements and expectations of customers and other stakeholders.
- Quality Control (QC). The process of monitoring and inspecting products, services, and processes to ensure they meet predetermined quality standards.
- Root Cause Analysis (RCA). A problem-solving method used to identify the root cause of a defect or failure in order to prevent the same issue from occurring in the future.
- Nonconformance Report. A written document that describes an incident in which a product does not conform to its specifications or requirements.
- Statistical Process Control (SPC). A data-driven method used to analyze a process or product and identify areas for improvement.
- Six Sigma. A business strategy designed to reduce defects and improve quality by focusing on process improvement and data-driven decision-making.
- Process Mapping. A visual representation of a process, showing each step, task, and decision that must be made in order to complete it.
Frequently Asked Questions
What is a Quality Improvement Inspector?
A Quality Improvement Inspector is a professional who assesses the quality of products and services, provides feedback to staff, and suggests improvements to help ensure quality standards are met.
What qualifications are required to be a Quality Improvement Inspector?
To become a Quality Improvement Inspector, one must typically have a degree in a relevant field such as engineering, quality assurance, or manufacturing and at least 5 years of experience in the quality assurance field.
What does a Quality Improvement Inspector do?
Quality Improvement Inspectors are responsible for inspecting products and services for conformance to quality standards, verifying accuracy of documentation, identifying and resolving issues, and making recommendations for improvement.
What tools do Quality Improvement Inspectors use?
Quality Improvement Inspectors typically use a variety of tools to inspect and monitor quality, including statistical process control charts, calibration equipment, and other specialized testing equipment.
What is the average salary for a Quality Improvement Inspector?
The average salary for a Quality Improvement Inspector is approximately $50,000 per year, depending on experience and location.
What are jobs related with Quality Improvement Inspector?
- Quality Improvement Engineer
- Quality Systems Analyst
- Quality Improvement Lead
- Quality Assurance Supervisor
- Quality Support Specialist
- Quality Systems Coordinator
- Quality Management Specialist
- Quality Control Manager
- Quality Support Coordinator
- Quality Systems Specialist
Web Resources
- Quality Improvement - ICAP at Columbia University icap.columbia.edu
- What Does a Quality Control Inspector Do? | Goodwin University www.goodwin.edu
- Quality Inspector | Professional Development & Training training.unh.edu
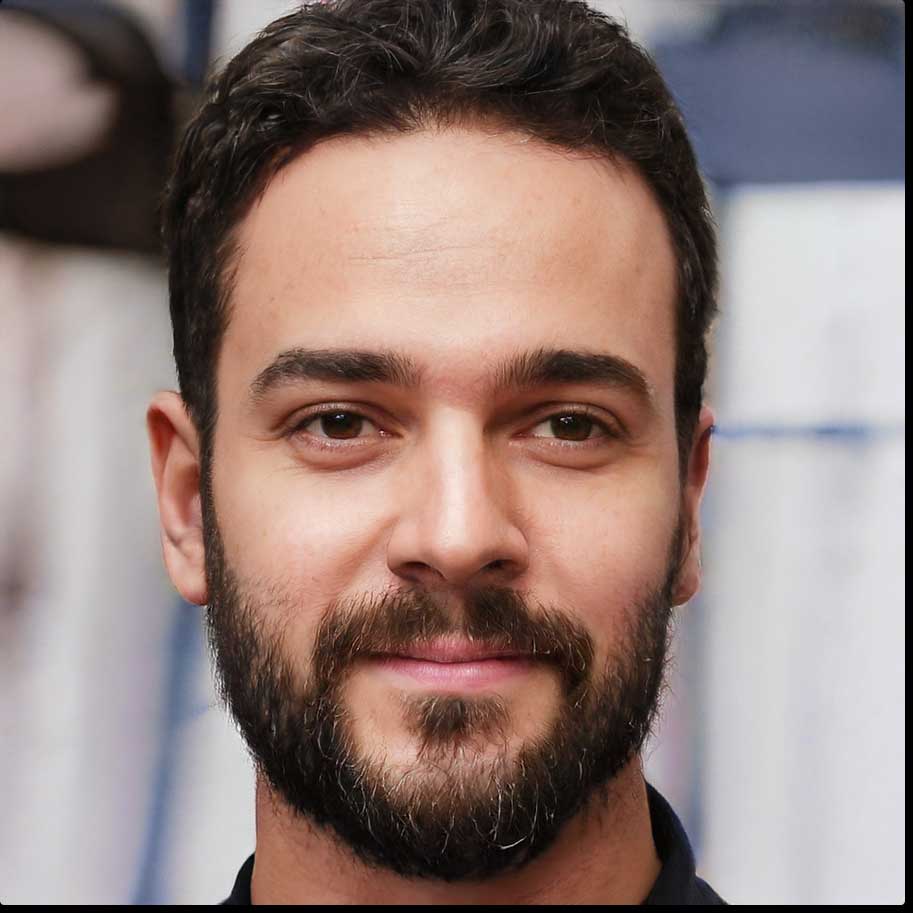