How to Be Quality Control Manager - Job Description, Skills, and Interview Questions
The lack of a quality control manager can have a significant impact on a business. Without someone overseeing the quality of products and services, there is a greater risk of customer dissatisfaction and increased costs due to rework, recalls, and repairs. customer loyalty and long-term relationships can be damaged due to poor quality and a lack of trust.
Furthermore, when there is no quality control manager, the organization may suffer from a lack of processes and standards, which can lead to inefficiencies, increased costs, and decreased productivity. the cost of not having a quality control manager can be high.
Steps How to Become
- Earn a Bachelor's Degree. Quality control managers typically need a bachelor's degree in a field related to business, engineering, or science. Examples of applicable degrees include industrial engineering, operations management, or management information systems.
- Gain Relevant Work Experience. Quality control managers typically need to have several years of experience in quality control or management. This experience can be obtained by working in areas like production, safety, or engineering.
- Consider Professional Certification. Although not required, certification may be beneficial for quality control managers who want to demonstrate their expertise and stay up to date with the latest industry standards. Certifications are available through organizations like the American Society for Quality (ASQ) and the Institute of Quality Assurance (IQA).
- Develop Leadership Skills. Quality control managers need to be good leaders who can motivate their employees and ensure that they are meeting quality standards. Effective communication and problem-solving skills are also essential.
- Stay Up to Date with Industry Developments. Quality control managers should stay up to date with the latest technology and industry trends in order to be more effective in their roles. They should also be familiar with relevant government regulations and safety standards.
You may want to check Quality Improvement Specialist, Quality Assurance Consultant, and Quality Control Lead for alternative.
Job Description
- Develop and implement quality control processes and procedures
- Establish standards of quality and ensure they are met
- Monitor and analyze quality performance data
- Identify areas of improvement and develop strategies to improve quality
- Ensure that all products meet customer requirements, legal regulations, and industry standards
- Develop and implement training programs for quality control personnel
- Conduct regular inspections and audits to evaluate product quality
- Investigate customer complaints and analyze root causes
- Coordinate corrective and preventive action plans
- Develop and maintain documentation related to quality control processes
- Oversee the implementation of new technologies and methods to increase efficiency and quality
- Liaise with internal and external stakeholders as necessary
Skills and Competencies to Have
- Knowledge of Quality Systems and Processes
- Knowledge of Quality Standards, Regulations and Guidelines
- Ability to Analyze Data and Identify Trends
- Ability to Develop and Implement Quality Control Plans
- Strong Organizational Skills
- Excellent Communication Skills (Written and Oral)
- Leadership and Management Skills
- Ability to Work Collaboratively with Team Members
- Attention to Detail and Accuracy
- Problem-Solving and Decision-Making Skills
- Ability to Train and Mentor Staff
- Proficiency in Computer Software Applications related to Quality Assurance
A Quality Control Manager must possess a wide range of skills to successfully oversee the quality of products and services. One of the most important skills a Quality Control Manager must have is the ability to think critically and logically. Being able to analyze data and identify potential flaws or issues in processes is essential to ensuring product quality.
Quality Control Managers must also possess strong interpersonal and communication skills to effectively work with teams and clients. A good knowledge of manufacturing and production processes, as well as of quality assurance standards, is also necessary for the job. Finally, the ability to stay organized and problem solve quickly is essential for a Quality Control Manager in order to ensure that products are compliant with standards and regulations.
By possessing these essential skills, a Quality Control Manager can help ensure the success of their organization by providing high-quality products and services.
Quality Performance Coordinator, Quality Support Manager, and Quality Improvement Engineer are related jobs you may like.
Frequent Interview Questions
- Tell us about your experience in the Quality Control field.
- How do you ensure that product quality standards are met?
- Describe your experience in managing a team of quality control staff.
- How do you stay up to date with emerging trends in quality control?
- What techniques do you use to ensure accurate and reliable data collection?
- How do you develop and maintain a quality assurance process?
- What challenges have you faced in quality control and how did you address them?
- How do you handle customer complaints related to product quality?
- What strategies do you use to motivate your team to produce high-quality results?
- Describe a time when you identified a problem in the quality control process and implemented a solution.
Common Tools in Industry
- Quality Management Software. Quality Management Software is a software solution that helps businesses assess and monitor the quality of their products and services. Example: Quality Management System (QMS) from ISO.
- Quality Control Checklists. Quality Control Checklists are used to document and assess the quality of products, processes and services. Example: Automotive Industry Action Group (AIAG) checklists.
- Statistical Process Control Software. Statistical Process Control Software is used to capture, analyze and report quality data in order to identify trends and anomalies. Example: InfinityQS ProFicient Software.
- Audit Tracking Software. Audit Tracking Software is used to track, schedule and report on internal and external audits. Example: AIMS Audit Management Software.
- Quality Assurance Testing Software. Quality Assurance Testing Software is used to test products and services for compliance with standards and customer requirements. Example: TestRail Test Management Software.
- Root Cause Analysis Software. Root Cause Analysis Software is used to identify and diagnose the underlying causes of quality problems. Example: Minitab Statistical Software.
Professional Organizations to Know
- American Society for Quality (ASQ)
- International Quality Federation (IQF)
- American Society of Quality Control (ASQC)
- International Organization for Standardization (ISO)
- International Accreditation Forum (IAF)
- International Association for Six Sigma Certification (IASSC)
- Project Management Institute (PMI)
- American Production and Inventory Control Society (APICS)
- European Organization for Quality (EOQ)
- American Society of Mechanical Engineers (ASME)
We also have Quality Management Analyst, Quality Improvement Manager, and Quality Performance Specialist jobs reports.
Common Important Terms
- Quality Assurance (QA) A systematic process of ensuring that all products and services meet the required standards of quality.
- Quality Management System (QMS) A system of processes and procedures used to ensure that products and services meet the established quality standards.
- Quality Control (QC) The process of monitoring, auditing, and inspecting products and services to ensure they meet the established quality standards.
- Root Cause Analysis (RCA) A systematic process used to identify the underlying causes of a problem and develop strategies to prevent it from occurring in the future.
- Statistical Process Control (SPC) A method of monitoring and controlling process performance using statistical tools and techniques.
- Quality Audit A systematic review of the processes, products, and services to ensure they comply with established quality standards.
- Total Quality Management (TQM) A comprehensive approach to quality management that focuses on continuously improving processes, products, and services.
Frequently Asked Questions
What is the role of a Quality Control Manager?
A Quality Control Manager is responsible for ensuring that products and services meet established quality standards. This includes managing quality assurance processes and personnel, overseeing product testing, inspecting products, and creating reports to identify areas for improvement.
What qualifications are needed to become a Quality Control Manager?
To become a Quality Control Manager, you will typically need at least a bachelor's degree in a field such as engineering, quality assurance, business, or management. Other qualifications may include experience in quality assurance, knowledge of ISO 9001 standards, and certification in quality management systems.
What is the average salary for a Quality Control Manager?
According to Glassdoor, the average salary for a Quality Control Manager is $71,858 per year in the United States. Salaries can vary depending on experience, location, and company size.
What skills are required for a Quality Control Manager?
The skills required for a Quality Control Manager include attention to detail, problem-solving, strong communication skills, knowledge of quality assurance processes, organizational skills, and the ability to work with cross-functional teams.
What tasks does a Quality Control Manager typically handle?
The tasks of a Quality Control Manager typically include developing and implementing quality control systems and processes, performing product inspections, monitoring performance standards, creating and analyzing reports, investigating customer complaints, and training employees on quality assurance processes.
What are jobs related with Quality Control Manager?
- Quality Manager
- Quality Management Specialist
- Quality Technician
- Quality Control Inspector
- Quality Systems Analyst
- Quality Systems Manager
- Quality Assurance Lead
- Quality Engineer
- Quality Systems Coordinator
- Quality Performance Manager
Web Resources
- Quality Control Manager | NC State Online and Distance Education online-distance.ncsu.edu
- Quality Control Manager Career Development Center | Rutgers ... careers.newark.rutgers.edu
- What Does a Quality Assurance Manager Do? www.goodwin.edu
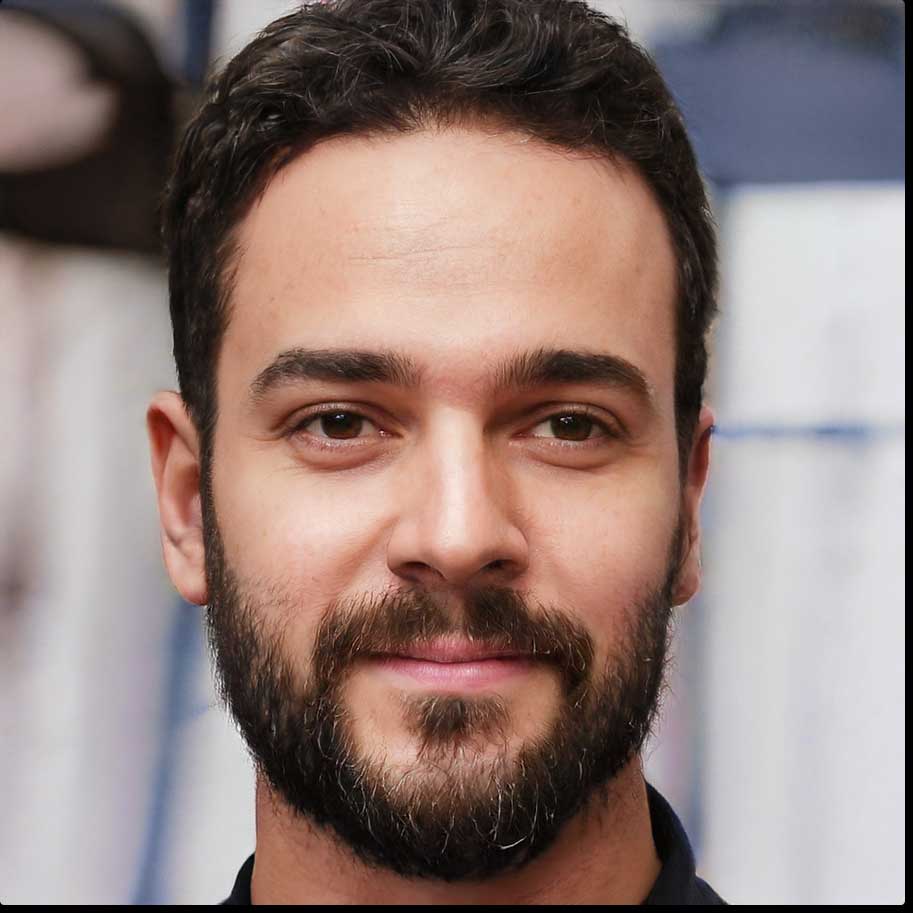