How to Be Life Cycle Cost Estimator - Job Description, Skills, and Interview Questions
Steps How to Become
- Obtain a Bachelor's Degree. To become a life cycle cost estimator, you should earn a bachelor's degree in a field such as engineering, finance, accounting, or mathematics. These degrees provide the foundation of knowledge necessary to become an effective cost estimator.
- Get Relevant Experience. To be hired as a life cycle cost estimator, you should gain experience in the field. Consider looking for internships or volunteer opportunities with relevant organizations. Or, you can enroll in a relevant certificate program.
- Earn Professional Certification. It is recommended that you obtain professional certification to demonstrate your knowledge and expertise in the field. The International Cost Estimating and Analysis Association (ICEAA) offers certification in cost estimating and analysis.
- Develop Your Skills. You should continually develop your skills as a life cycle cost estimator by attending conferences, taking courses, and networking with other professionals in the field.
- Join Professional Organizations. Joining a professional organization such as the ICEAA can help you stay up-to-date on the latest industry trends and technologies, as well as build relationships with other professionals in the field.
The lack of skilled and efficient labor can have a major impact on the life cycle cost estimator. Without the right personnel, the estimator may not be able to accurately predict the costs associated with a project and could lead to costly delays and overruns. The best way to ensure that the estimator has the necessary expertise is to invest in comprehensive training and education for its employees.
Furthermore, providing ongoing support and resources can help to ensure that the estimator remains up-to-date and is able to take into account changes in technology, market conditions, and other variables. By taking these steps, organizations can ensure that their life cycle cost estimator is reliable and effective, which can in turn help save time and money in the long run.
You may want to check Life Sciences Regulatory Specialist, Life Science Laboratory Technician, and Life Safety Code Consultant for alternative.
Job Description
- Project Manager: responsible for the overall planning, execution, and completion of the project.
- Design Engineer: responsible for creating and testing designs to meet customer requirements.
- Quality Assurance Engineer: responsible for developing and executing tests to ensure product quality.
- Manufacturing Engineer: responsible for developing and implementing production processes and equipment.
- Supply Chain Manager: responsible for managing all aspects of the supply chain, from procurement to delivery.
- Maintenance Technician: responsible for performing preventive maintenance and repairs on production equipment.
- Technical Writer: responsible for creating and maintaining technical documents for the product.
Skills and Competencies to Have
- Knowledge of financial analysis and budgeting
- Experience with project management and cost engineering
- Understanding of life cycle costing principles
- Proficiency in data modeling and quantitative analysis
- Ability to develop cost estimates for various scenarios
- Familiarity with life cycle cost estimating software and tools
- Familiarity with project scheduling and risk management
- Strong communication skills to present and discuss cost estimates with stakeholders
- Ability to identify, analyze, and solve cost-related issues
The ability to estimate the life cycle cost of a product or project is an essential skill in the modern business world. This skill helps project managers to evaluate the long-term costs of a project, including materials, labor, and maintenance, in order to make informed decisions. By understanding the true cost of a product or project throughout its entire life cycle, businesses can make better decisions about how to manage their resources and maximize their profits.
Furthermore, having this skill can help companies to better forecast their expenses and budget for future projects more accurately. having the ability to accurately estimate the life cycle cost of a product or project can help businesses to make smarter decisions, save money, and increase their profits.
Life Safety Inspector, Life Sciences Intellectual Property Attorney, and Life Skills Instructor are related jobs you may like.
Frequent Interview Questions
- How do you ensure accuracy in life cycle cost estimates?
- What methods do you use to assess the value of assets?
- How do you factor inflation into life cycle cost estimates?
- How do you evaluate the cost and benefit of different options?
- What techniques do you use to forecast future costs?
- How do you interact with other stakeholders to ensure cost estimates are accurate?
- How do you adapt to changing economic conditions when estimating life cycle costs?
- How do you prioritize costs when estimating life cycle costs?
- How do you use data to inform cost estimates?
- What strategies do you use to minimize life cycle costs?
Common Tools in Industry
- Project Management Software. This tool helps manage the cost of a project over its lifespan, including budgeting, scheduling, and resource allocation. (Eg: Microsoft Project)
- Life Cycle Cost Analysis Software. This tool allows users to analyze the total cost of ownership of an asset over its lifetime, taking into account factors such as inflation, fuel costs, maintenance costs, and more. (Eg: Deltek Costpoint)
- Cost Estimation Software. This tool allows users to estimate the cost of a project before committing to it, taking into account labor and material costs. (Eg: Sage Estimating)
- Risk Analysis Software. This tool helps identify potential risks associated with a project and assess their financial costs. (Eg: Monte Carlo Simulation)
- Cost Benefit Analysis Software. This tool helps determine the cost-benefit ratio of a project, allowing users to decide if the investment is worth it. (Eg: Analytica)
Professional Organizations to Know
- American Society of Civil Engineers (ASCE)
- American Institute of Architects (AIA)
- National Society of Professional Engineers (NSPE)
- American Council of Engineering Companies (ACEC)
- Project Management Institute (PMI)
- American Society for Quality (ASQ)
- Society of Cost Estimators and Analysts (SCEA)
- Association for the Advancement of Cost Engineering International (AACEI)
- International Council on Systems Engineering (INCOSE)
- National Institute of Building Sciences (NIBS)
We also have Life Span Developmental Psychologist, Life Sciences Research Associate, and Life and Health Insurance Agent jobs reports.
Common Important Terms
- Life Cycle Cost (LCC). The total cost of owning and operating an asset over its entire life, taking into account purchase, maintenance, repair, and disposal costs.
- Initial Cost. The initial cost of an asset, including purchase and installation expenses.
- Operating Cost. The cost of operating an asset over its life cycle, including fuel and labor costs.
- Maintenance Cost. The cost of preventive maintenance, repairs, and replacements over the asset's life cycle.
- Disposal Cost. The cost of disposing of the asset at the end of its life cycle, including any applicable taxes or fees.
- Salvage Value. The amount of money received from selling the asset at the end of its life cycle.
- Cost-Benefit Analysis. A method of assessing the financial feasibility of a project by comparing the expected costs to the expected benefits.
Frequently Asked Questions
What is Life Cycle Cost Estimator?
A Life Cycle Cost Estimator is a tool that helps to analyze the costs associated with the ownership, operation and maintenance of a product or system over its entire life cycle.
What are the key components of a Life Cycle Cost Estimator?
The key components of a Life Cycle Cost Estimator include cost items such as purchase price, annual operating costs, maintenance costs, and end of life costs.
What are the benefits of using a Life Cycle Cost Estimator?
The benefits of using a Life Cycle Cost Estimator include the ability to make informed decisions about cost-effective product or system investments, identify cost-saving opportunities, and compare different options to determine the most cost-effective solution.
How long is the typical life cycle of a product or system?
The typical life cycle of a product or system can vary depending on the application and type, but generally ranges from 1 to 20 years.
What are some factors to consider when estimating life cycle costs?
Factors to consider when estimating life cycle costs include initial purchase price, operating and maintenance costs, energy costs, replacement parts costs, disposal costs, and any potential subsidies or incentives.
What are jobs related with Life Cycle Cost Estimator?
- Life Support Engineer
- Life Science Project Manager
- Life Care Manager
- Life Cycle Logistics Specialist
- Life Science Regulatory Affairs Specialist
- Life Scientist, Senior
- Life Sciences Regulatory Affairs Manager
- Life Cycle Logistician
- Life Insurance Claims Adjuster
- Life Sciences Business Development Manager
Web Resources
- Life Cycle Costing | Sustainability at Harvard green.harvard.edu
- Life Cycle Costing | Harvard Energy & Facilities www.energyandfacilities.harvard.edu
- Life Cycle Calculator | Sustainability at Harvard green.harvard.edu
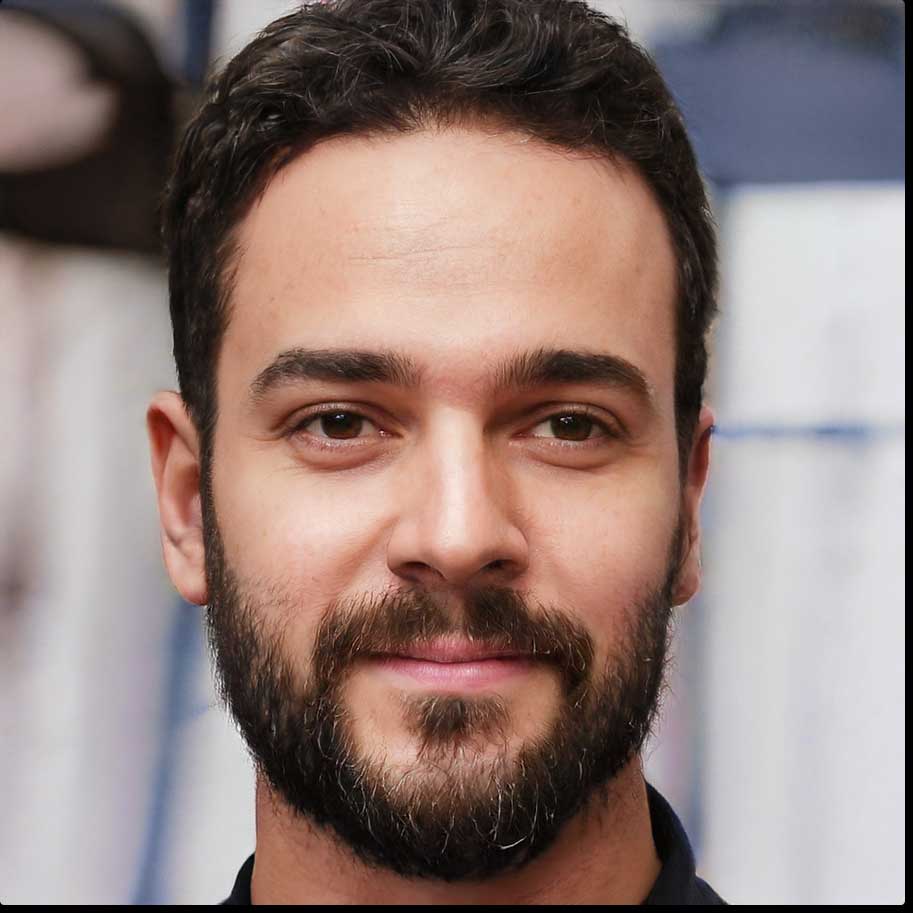