How to Be Quality Improvement Manager - Job Description, Skills, and Interview Questions
Poor quality management can have a significant impact on an organization. Without effective quality management, organizations can experience a decrease in customer satisfaction, profits, and market share. This can be caused by a lack of clear process guidelines, inadequate training, or inadequate resources.
Quality Improvement Managers help to improve the quality of services and products by developing and implementing effective strategies. These strategies may include developing process standards, providing training and education to staff, and utilizing quality control tools to monitor performance. By creating measurable goals and objectives, and meeting those goals, Quality Improvement Managers help organizations achieve their desired outcomes while controlling costs.
Steps How to Become
- Obtain a Bachelor's Degree. A bachelor's degree in business, healthcare, quality management, or a related field is typically required to become a quality improvement manager. Coursework in accounting, mathematics, statistics, and business administration can be beneficial.
- Earn a Master's Degree. Some employers prefer quality improvement managers to have a master's degree in business administration, healthcare administration, or a related field.
- Gain Experience. Many employers prefer quality improvement managers to have several years of experience in the field. Working as a quality assurance analyst, quality control manager, or project manager can help aspiring quality improvement managers acquire useful knowledge and skills.
- Obtain Certifications. Quality improvement managers can pursue certifications such as Certified Quality Improvement Associate (CQIA), Certified Quality Auditor (CQA), and Certified Quality Manager (CQM).
- Become Licensed. Some states require quality improvement managers to obtain a license in order to practice. Requirements vary by state, but generally include passing an exam and completing a certain number of work hours.
The role of a Quality Improvement Manager is to ensure that products, services, and processes are meeting the highest standards. To be successful in this position, one must possess strong communication and problem-solving skills, as well as an understanding of quality assurance principles and practices. one must be able to identify areas of improvement and develop plans to meet organizational objectives.
If a Quality Improvement Manager is skilled and competent, they can create an efficient system to monitor and evaluate the quality of products and services. This, in turn, can lead to improved customer satisfaction and increased organizational growth. Furthermore, this improved system can also reduce costs associated with non-conformance and increase productivity.
a competent Quality Improvement Manager can have a significant positive impact on an organizations bottom line.
You may want to check Quality Assurance Auditor, Quality Improvement Inspector, and Quality Support Coordinator for alternative.
Job Description
- Develop and implement quality improvement strategies to ensure that products, services, and processes meet customer requirements.
- Monitor, analyze, and report on performance metrics to measure the effectiveness of quality improvement initiatives.
- Lead cross-functional teams in the design, implementation, and evaluation of quality improvement projects.
- Design and implement procedures and systems to ensure compliance with all applicable quality standards.
- Monitor supplier performance to ensure that products meet quality requirements.
- Identify, investigate, and resolve issues related to product defects and quality complaints.
- Develop best practices for quality assurance and control processes.
- Train and educate employees on quality improvement concepts and practices.
- Develop and maintain relationships with external stakeholders to ensure compliance with quality standards.
- Review customer feedback and use it to drive quality improvement initiatives.
Skills and Competencies to Have
- Strategic Thinking: Ability to think strategically, anticipate future needs and develop strategies to achieve desired outcomes.
- Change Management: Ability to lead change initiatives and manage the associated risks.
- Project Management: Ability to plan, organize, and execute projects to meet timelines and budget constraints.
- Process Improvement: Ability to analyze current processes and identify opportunities for improvement.
- Quality Assurance: Ability to develop and implement quality assurance plans and procedures to ensure consistent delivery of quality products and services.
- Data Analysis: Ability to collect, analyze, and interpret data to inform decision making.
- Communication Skills: Excellent communication skills, both written and verbal, to effectively convey information to various stakeholders.
- Problem Solving: Ability to identify problems, develop solutions, and take action to implement them.
- Interpersonal Skills: Ability to work effectively with a variety of people in different roles and at different levels of an organization.
- Leadership: Ability to lead teams and initiatives, motivate others, and provide direction and guidance.
The Quality Improvement Manager is a key role in any organization and requires a broad skill set to be successful. One of the most important skills a Quality Improvement Manager must possess is the ability to analyze data and identify trends. By examining data, they are able to determine relevant causes and effects that may be contributing to existing problems and develop strategies to improve processes.
Quality Improvement Managers must also have strong communication skills to effectively communicate their findings, create action plans and coordinate implementation with other departments. they must have strong leadership skills to motivate and inspire others to work together to reach common goals. Finally, Quality Improvement Managers must have excellent problem-solving skills to quickly identify issues and develop innovative solutions.
With these skills, Quality Improvement Managers can ensure that processes are efficient, effective and compliant with industry standards.
Quality Assurance Coordinator, Quality Management Specialist, and Quality Engineer are related jobs you may like.
Frequent Interview Questions
- What experience do you have in managing Quality Improvement initiatives?
- How have your previous experiences prepared you to succeed in this role?
- What strategies have you employed to improve quality standards?
- What challenges have you faced in Quality Improvement initiatives, and how did you overcome them?
- How do you ensure customer satisfaction and continuous improvement?
- How do you ensure compliance with regulations and industry standards?
- How do you motivate teams to continuously improve quality?
- What metrics do you use to measure the success of Quality Improvement initiatives?
- How do you develop and manage quality improvement plans?
- What techniques do you use to foster collaboration and innovation within quality improvement projects?
Common Tools in Industry
- Root Cause Analysis. A method of problem-solving used to identify the source of a problem and its related causes. (Eg: A customer service representative uses Root Cause Analysis to identify why customers are having difficulty using a website. )
- Lean Six Sigma. A process improvement methodology which combines the principles of Lean and Six Sigma to identify and eliminate waste in a process. (Eg: A Quality Improvement Manager uses Lean Six Sigma to reduce the amount of errors in a manufacturing process. )
- Statistical Process Control (SPC). A method of monitoring and controlling processes by measuring the performance of a process against established standards. (Eg: A Quality Improvement Manager uses SPC to track the performance of an assembly line and measure it against established targets. )
- Failure Mode and Effects Analysis (FMEA). A risk assessment tool used to identify potential failure points in a process and their possible effects. (Eg: A Quality Improvement Manager uses FMEA to identify potential areas of failure in a new product development process and develop preventive measures. )
- Kaizen. A continuous improvement methodology which focuses on small, incremental changes to improve process efficiency. (Eg: A Quality Improvement Manager uses Kaizen to regularly assess and refine processes across the organization. )
Professional Organizations to Know
- American Society for Quality (ASQ)
- International Organization for Standardization (ISO)
- National Association for Healthcare Quality (NAHQ)
- National Association for Quality (NAQ)
- American College of Healthcare Executives (ACHE)
- Institute for Healthcare Improvement (IHI)
- The Joint Commission
- Healthcare Quality Association on Accreditation (HQAA)
- American Association of Medical Quality (AAMQ)
- International Society for Quality in Health Care (ISQua)
We also have Quality Assurance Inspector, Quality Improvement Technician, and Quality Systems Manager jobs reports.
Common Important Terms
- Process Improvement. The practice of identifying and implementing ways to improve processes and make them more efficient.
- Quality Control. The process of ensuring that products and services meet certain quality standards.
- Root Cause Analysis. A method of problem solving that involves identifying the source of an issue so that it can be addressed and prevented from occurring again.
- Six Sigma. An approach to process improvement that focuses on reducing variation, improving quality, and reducing costs.
- Total Quality Management (TQM). A management approach that emphasizes the importance of meeting customer needs and expectations by continuously striving for improvement.
- Lean Six Sigma. A combination of Lean and Six Sigma principles and tools that can be used to improve processes and deliver better results.
- Data Analysis. The process of collecting, organizing, analyzing, and interpreting data to draw meaningful conclusions.
- Quality Assurance. The practice of developing, testing, and monitoring systems to ensure that products and services meet certain quality standards.
Frequently Asked Questions
What is a Quality Improvement Manager?
A Quality Improvement Manager is a professional who is responsible for overseeing and managing quality assurance processes within an organization. They are tasked with developing and implementing strategies to ensure that products and services meet the highest levels of quality.
What qualifications are needed to become a Quality Improvement Manager?
To become a Quality Improvement Manager, it is typically required to have a bachelor's degree in a field such as management, engineering, or business. Additionally, prior experience in quality assurance, process improvement, and/or project management is highly desirable.
What responsibilities does a Quality Improvement Manager have?
The primary responsibilities of a Quality Improvement Manager include developing and implementing quality policies, procedures, and systems; evaluating existing processes and making necessary changes; identifying potential areas for improvement; and monitoring performance against quality standards.
What tools are used by Quality Improvement Managers?
Quality Improvement Managers may use a variety of tools such as process mapping, root cause analysis, statistical process control, benchmarking, and Six Sigma to identify potential areas for improvement and to monitor performance against quality standards.
What is the average salary for a Quality Improvement Manager?
The average salary for a Quality Improvement Manager is approximately $71,000 per year in the United States. This figure may vary depending on experience, qualifications, and the size of the organization.
What are jobs related with Quality Improvement Manager?
- Quality Improvement Engineer
- Quality Performance Manager
- Quality Improvement Analyst
- Quality Support Analyst
- Quality Improvement Lead
- Quality Control Inspector
- Quality Support Specialist
- Quality Management Coordinator
- Quality Systems Coordinator
- Quality Performance Coordinator
Web Resources
- Quality Improvement Manager - Stanford University Careers careersearch.stanford.edu
- Quality Improvement - ICAP at Columbia University icap.columbia.edu
- PROGRAM MANAGER (Quality Improvement and Accreditation) opportunities.ucsf.edu
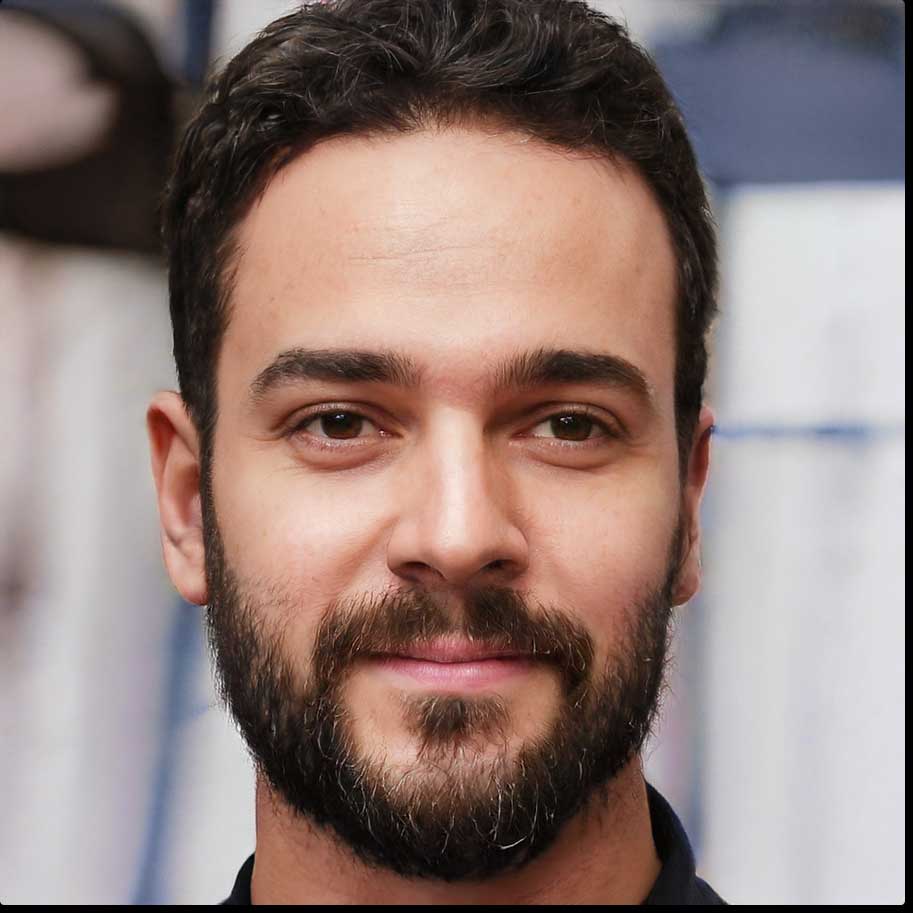