How to Be Quality Improvement Analyst - Job Description, Skills, and Interview Questions
Poor quality improvement can cause significant financial and operational losses. Companies that overlook quality assurance measures often find themselves dealing with excess inventory, higher than expected returns, and dissatisfied customers. In order to prevent these costly consequences, Quality Improvement Analysts can provide valuable services to help manage the process.
Quality Improvement Analysts use proven methods, such as Six Sigma and Total Quality Management, to identify areas of improvement and create solutions that help to reduce costs, improve customer satisfaction, and increase efficiency. By utilizing these strategies, companies can be assured that their products and services are meeting the highest standards.
Steps How to Become
- Earn a Bachelor's Degree. Quality improvement analysts typically need to hold at least a bachelor's degree in business, healthcare administration, or a related field. Coursework should include classes in management, organizational behavior, and statistics.
- Gain Experience. Quality improvement analyst positions often require prior experience in a related field, such as healthcare administration or management. Internships and volunteer positions can be helpful in gaining this experience.
- Develop Industry Knowledge. Quality improvement analysts need to understand the industry they are working in. They should be familiar with the regulations and standards related to their industry, as well as the tools and techniques used to measure quality.
- Get Certified. Quality improvement analysts may choose to pursue professional certification in order to demonstrate their competency and stay up-to-date on best practices. Certifications are available through organizations such as the American Society for Quality and the American Association for Quality.
- Pursue Continuing Education. Quality improvement analysts should keep current on industry trends and advances in quality improvement techniques. Continuing education courses and seminars can help them stay ahead of the curve.
The ability to be a reliable and capable Quality Improvement Analyst requires three key elements. The first is an in-depth understanding of the Quality Improvement Process and how it is implemented. This includes having a comprehensive knowledge of the principles and techniques utilized to identify potential areas for improvement, as well as the tools and strategies needed to execute them.
Second, the analyst must have strong problem-solving skills to be able to effectively analyze data, identify trends, and devise solutions. Finally, the analyst must be able to effectively communicate their findings and recommendations to stakeholders in order to ensure that their solutions are implemented effectively. All together, these elements make up the core of what is needed to be a reliable and capable Quality Improvement Analyst.
You may want to check Quality Improvement Specialist, Quality Supervisor, and Quality Management Specialist for alternative.
Job Description
- Develop, implement and monitor quality improvement initiatives to ensure the delivery of safe, high-quality healthcare services.
- Monitor compliance with regulatory standards, accreditation standards, and quality assurance criteria.
- Design and conduct internal audits to ensure performance and quality standards are met.
- Analyze data, identify gaps and trends, and develop and recommend action plans to improve quality, safety and effectiveness of services.
- Collaborate with multidisciplinary teams to identify and address quality issues.
- Develop and maintain reports, databases and spreadsheets to track performance data and quality metrics.
- Facilitate change management and process improvement activities to enhance quality and safety.
- Monitor utilization of healthcare services and report any discrepancies or inefficiencies.
- Educate staff on quality improvement practices and initiatives.
- Provide technical assistance to staff regarding quality improvement processes.
Skills and Competencies to Have
- Data Analysis and Interpretation
- Quality Improvement Methodologies and Tools
- Database Management and Analytics
- Project Management
- Statistical Analysis
- Process Improvement
- Presentation and Communication Skills
- Knowledge of Quality Standards and Regulations
- Quality Assurance and Testing
- Problem Solving and Decision Making
- Team Leadership and Collaboration
- Change Management
- Continuous Improvement Techniques
- Risk Analysis and Mitigation Strategies
- Time Management
The role of a Quality Improvement Analyst requires a variety of skills, but the most important skill to have is an eye for detail. Quality Improvement Analysts need to be able to identify problems and suggest solutions to improve processes, products and services. They also need to be able to analyze data, develop action plans, and monitor progress and results.
Quality Improvement Analysts also need to have excellent communication and collaboration skills, as they need to be able to collaborate with other teams, departments, and stakeholders to identify and implement successful solutions. they need to be able to effectively present their findings in order to create buy-in from the necessary stakeholders. Finally, they need to be able to think critically and be creative when coming up with solutions.
These skills will help them develop and implement successful quality improvement initiatives that will benefit the organization.
Quality Assurance Supervisor, Quality Management Coordinator, and Quality Improvement Inspector are related jobs you may like.
Frequent Interview Questions
- How would you define quality improvement?
- Describe a successful quality improvement project you have led in the past.
- What methods do you use to identify areas of quality improvement?
- What strategies do you employ to develop and implement quality improvement initiatives?
- How do you ensure that all stakeholders are involved in the quality improvement process?
- Describe a time when you had to handle resistance to a quality improvement initiative.
- What techniques do you use to measure the success of a quality improvement project?
- How have your past experiences prepared you for a role as a Quality Improvement Analyst?
- What challenges have you faced in previous quality improvement roles and how did you overcome them?
- What suggestions do you have for improving our current quality improvement initiatives?
Common Tools in Industry
- Process Mapping. A tool used to map out a process in order to identify inefficiencies and areas for improvement. (Example: creating a flowchart to identify steps and opportunities for streamlining a customer service process).
- Root Cause Analysis. A tool used to identify the underlying cause of an issue. (Example: conducting interviews and surveys to identify why customers are not returning to a website).
- Data Visualization. A tool used to display data in a visual format that is easy to understand and interpret. (Example: creating a bar chart to show customer satisfaction ratings over time).
- Cost Benefit Analysis. A tool used to determine the financial impact of an improvement project. (Example: calculating the cost of a new customer service system versus the potential benefits of improved customer service).
- Lean Six Sigma. A framework used to improve quality and reduce waste. (Example: using Lean Six Sigma to reduce defects in a manufacturing process).
Professional Organizations to Know
- American Society for Quality (ASQ)
- American Statistical Association (ASA)
- Healthcare Information and Management Systems Society (HIMSS)
- Institute for Healthcare Improvement (IHI)
- Lean Enterprise Institute (LEI)
- National Committee for Quality Assurance (NCQA)
- Project Management Institute (PMI)
- Six Sigma Forum
- The International Society for Quality in Health Care (ISQua)
- Total Quality Management Association (TQMA)
We also have Quality Performance Analyst, Quality Manager, and Quality Systems Coordinator jobs reports.
Common Important Terms
- Quality Assurance. The process of ensuring that products and services meet or exceed customer expectations.
- Quality Control. The process of measuring, inspecting and testing products and services to ensure they meet quality standards.
- Quality Management System. A system of processes and procedures that ensures a product or service meets the quality requirements of its customers.
- Six Sigma. A business management strategy that focuses on improving the quality of products and services by reducing variation and eliminating defects.
- Root Cause Analysis. A method of problem solving that attempts to identify the underlying cause of a problem, as opposed to treating only its symptoms.
- Lean Six Sigma. A combination of Lean and Six Sigma philosophies focused on reducing waste and eliminating defects.
- Risk Management. The process of identifying, analyzing and mitigating potential risks to an organization's operations.
- Process Improvement. The process of finding ways to improve existing processes in order to increase efficiency and reduce costs.
- Quality Auditing. The process of examining a product or service to determine whether it meets established quality standards.
Frequently Asked Questions
What is a Quality Improvement Analyst?
A Quality Improvement Analyst is a professional who works to identify areas of improvement in processes, products and services to ensure quality and efficiency in an organization.
What skills are needed for a Quality Improvement Analyst?
Quality Improvement Analysts need strong analytical and problem-solving skills, as well as excellent communication and interpersonal skills. They should have knowledge of quality management processes, standards and procedures, as well as data analysis techniques.
What are the responsibilities of a Quality Improvement Analyst?
The responsibilities of a Quality Improvement Analyst include analyzing data to identify areas of improvement, developing quality assessment plans, monitoring process performance, and recommending solutions to improve efficiency and quality.
What qualifications are required for a Quality Improvement Analyst?
Quality Improvement Analysts typically need at least a bachelor's degree in a related field such as engineering, business or statistics. They should also have experience with quality improvement techniques and processes.
What is the salary range for a Quality Improvement Analyst?
The salary range for a Quality Improvement Analyst can vary depending on experience and location, but the median salary for this position is around $64,000 per year.
What are jobs related with Quality Improvement Analyst?
- Quality Assurance Inspector
- Quality Performance Manager
- Quality Improvement Technician
- Quality Control Manager
- Quality Systems Manager
- Quality Management Analyst
- Quality Improvement Coordinator
- Quality Support Specialist
- Quality Performance Specialist
- Quality Assurance Coordinator
Web Resources
- Quality Improvement - ICAP at Columbia University icap.columbia.edu
- Quality/Process Improvement Analyst - alumnijobs.cofc.edu alumnijobs.cofc.edu
- MIH Data Analyst, Division of Quality Improvement www.umass.edu
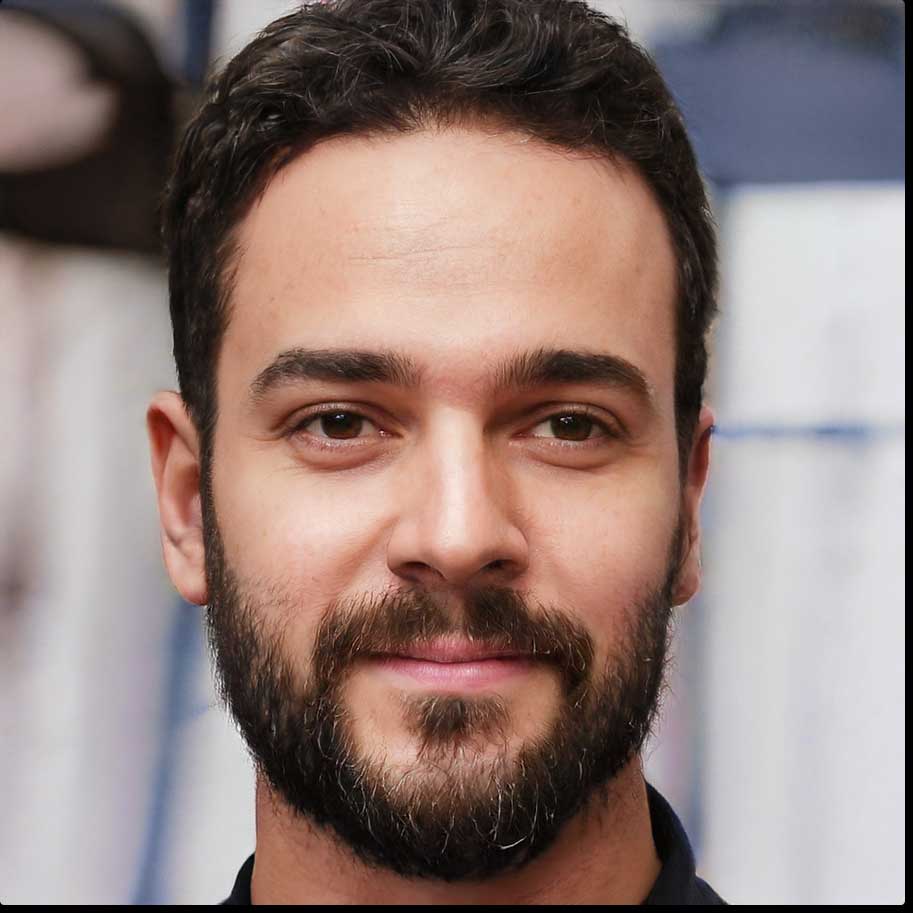