How to Be Quality Supervisor - Job Description, Skills, and Interview Questions
The lack of a quality supervisor can have a negative effect on the production process. Without someone to oversee the quality standards, the quality of the products may suffer, resulting in customer dissatisfaction and possible financial losses. This can also lead to decreased morale among employees, resulting in a decrease in productivity and increased stress levels.
To avoid these issues, it is important to have a qualified supervisor in place to ensure that quality standards are met and maintained. This will help ensure customer satisfaction and a healthy work environment for employees.
Steps How to Become
- Earn a college degree. Obtaining a college degree, such as a bachelor's degree in quality assurance, engineering, or business administration, is often a requirement for becoming a quality supervisor. Many employers prefer to hire individuals with a master's degree in a related field.
- Gain experience. Many employers prefer to hire quality supervisors with a minimum of two years' experience in quality assurance or another related field. Working as a quality inspector or quality control technician is a great way to gain experience in the quality assurance field.
- Acquire certifications. Professional certifications demonstrate knowledge and proficiency in the field of quality assurance and can help to secure a supervisory position. Examples of certifications include Certified Quality Engineer (CQE), Certified Quality Inspector (CQI), and Certified Quality Manager (CQM).
- Obtain specific skills. Quality supervisors must have strong interpersonal and problem-solving skills. Additionally, knowledge of statistical process control (SPC) and experience with root cause analysis techniques are beneficial for this position.
- Apply for the job. After gaining the necessary qualifications, begin applying for quality supervisor positions with local companies. Networking and attending job fairs are also great ways to find job opportunities.
The quality of any product is directly dependent on the skill and competency of the quality supervisor. A skilled and competent quality supervisor is able to detect any potential issues with the product before it is released, leading to a higher quality product. This in turn leads to higher customer satisfaction, as customers will be less likely to experience issues with the product and will be more likely to recommend it to others.
Furthermore, a skilled and competent quality supervisor can help to reduce the costs associated with producing a product, as they will be able to identify any areas where production is inefficient or costly. By ensuring that a product meets the highest standards of quality, a quality supervisor can help a business to increase its profitability and be successful in the long term.
You may want to check Quality Assurance Inspector, Quality Assurance Consultant, and Quality Management Analyst for alternative.
Job Description
- Develop and implement quality control systems to ensure product and service quality.
- Monitor production processes to identify opportunities for improvement.
- Develop and implement inspection processes and procedures to ensure product quality standards are met.
- Monitor the inspection process to ensure quality standards are consistently met.
- Analyze data from production processes to identify areas for improvement in product quality.
- Investigate customer complaints about product quality and make recommendations for corrective action.
- Train and supervise staff on inspection processes and procedures.
- Maintain records of inspection results and corrective actions taken.
- Establish and enforce quality standards for incoming materials and services.
- Develop and maintain relationships with suppliers to ensure highest quality of materials and services.
Skills and Competencies to Have
- Knowledge of quality assurance principles and techniques
- Ability to interpret technical drawings and specifications
- Strong communication and problem-solving skills
- Ability to work independently and in a team environment
- Experience with inspection techniques and methods
- Knowledge of ISO 9001 standards and other relevant quality assurance standards
- Knowledge of statistical process control (SPC) methods
- Ability to develop quality assurance plans, procedures, and documentation
- Proficient in the use of computer software such as Microsoft Office Suite
- Excellent organizational and time management skills
Good quality supervisors need to possess a wide range of skills to effectively manage the quality of a product or service. Chief among these is an understanding of quality assurance standards and procedures, and the ability to put them into practice. Quality supervisors must also have excellent problem-solving and decision-making skills, as well as be able to identify root causes of quality issues.
Communication and collaboration skills are also essential, as quality supervisors must coordinate with both internal and external stakeholders to ensure that quality assurance goals are met. Finally, quality supervisors must be adept in data analysis, in order to identify trends in the quality of a product or service, and be able to provide accurate reports to their teams. Collectively, these skills enable quality supervisors to ensure that their organization is producing the highest quality product or service possible.
Quality Management Specialist, Quality Systems Coordinator, and Quality Assurance Technician are related jobs you may like.
Frequent Interview Questions
- What experience do you have in quality assurance and control?
- What methods do you use to monitor and review quality standards?
- How do you ensure that production processes meet customer requirements?
- How do you evaluate the effectiveness of quality management systems?
- How do you identify and address potential weaknesses in product quality?
- Describe a time when you have had to address a customer complaint about product quality.
- How do you ensure that the products produced are up to standard?
- What techniques do you use to audit and analyze quality data?
- How do you establish and maintain quality objectives?
- Describe a time when you had to make a difficult decision regarding product quality.
Common Tools in Industry
- Quality Inspection Checklist. A list of items to inspect for quality assurance purposes (e. g. item dimensions, surface finishes, etc. ).
- Defect Tracking System. A system used to track and manage defects found during inspections (e. g. documenting the type, severity, and resolution of reported issues).
- Quality Reporting Software. Software used to generate detailed reports on quality assurance findings (e. g. analyzing defects by product type and severity).
- Non-Conformance Database. A database used to track and store non-conformance information (e. g. tracking and managing customer complaints).
- Statistical Process Control (SPC) Tools. Software used to monitor and control product quality through statistical analysis (e. g. measuring process capability).
- Root Cause Analysis Tools. Software used to identify root causes of quality issues (e. g. determining the source of a defect).
- Quality Auditing Software. Software used to audit and assess product and process quality (e. g. conducting internal audits for ISO 9001 certification).
Professional Organizations to Know
- American Society for Quality (ASQ)
- International Organization for Standardization (ISO)
- Institute of Quality Assurance (IQA)
- American Quality Institute (AQI)
- International Register of Certified Auditors (IRCA)
- Association for Quality and Participation (AQP)
- Association for Quality Management Professionals (AQMP)
- Institute of Quality Management (IQM)
- National Institute of Quality Management (NIQM)
- International Federation for Quality Management (IFQM)
We also have Quality Performance Specialist, Quality Management Coordinator, and Quality Engineer jobs reports.
Common Important Terms
- Quality Assurance (QA). Quality Assurance is a process of ensuring products or services meet a certain level of quality before they are released to customers. It involves activities such as inspections, tests, and evaluations.
- Quality Control (QC). Quality Control is the process of ensuring that products meet the established standards of quality. It involves inspecting, testing, and verifying that the finished product is up to the desired quality level.
- Root Cause Analysis (RCA). Root Cause Analysis is a process used to identify the underlying cause of an issue or problem. It is done by gathering data, analyzing it, and using the results to develop corrective actions to prevent the issue from recurring.
- Total Quality Management (TQM). Total Quality Management is a management strategy that focuses on meeting customer needs and expectations through continuous improvement and innovation. It involves a set of tools and processes to ensure quality in every part of the business.
- Six Sigma. Six Sigma is a set of tools and processes for improving quality and reducing variation in products and services. It is based on the principles of data-driven decision making, continuous improvement, and defect prevention.
Frequently Asked Questions
What are the primary responsibilities of a Quality Supervisor?
Quality Supervisors are responsible for ensuring that products meet quality standards and customer requirements. They oversee production processes to ensure that products are manufactured correctly, investigate customer complaints and product defects, and develop and implement quality control procedures.
What qualifications are needed to become a Quality Supervisor?
Qualifications for a Quality Supervisor typically include a Bachelor's degree in a relevant field such as engineering, chemistry, or quality management, as well as several years of experience in quality assurance and/or production. Certification from the American Society for Quality (ASQ) may also be required.
How many people does a Quality Supervisor typically oversee?
The exact number of people overseen by a Quality Supervisor will depend on the size of the organization, but typically they manage a team of between 5 and 25 people.
What tools do Quality Supervisors use?
Quality Supervisors use a variety of tools, such as statistical process control (SPC) charts, process capability studies, and defect tracking systems, to ensure that products meet quality standards and customer requirements. They may also use various software programs to monitor production processes and analyze data.
What type of environment does a Quality Supervisor typically work in?
Quality Supervisors typically work in a manufacturing environment, where they oversee the production process and ensure that products meet quality standards. They may also work in an office setting, where they analyze data and develop quality control procedures.
What are jobs related with Quality Supervisor?
- Quality Systems Analyst
- Quality Improvement Analyst
- Quality Control Inspector
- Quality Support Analyst
- Quality Performance Coordinator
- Quality Support Coordinator
- Quality Technician
- Quality Management Manager
- Quality Assurance Coordinator
- Quality Assurance Auditor
Web Resources
- What is a Manufacturing Quality Supervisor? | Goodwin University www.goodwin.edu
- Quality Assurance Supervisor | NC State Online and Distance ¦ online-distance.ncsu.edu
- What is a Quality Assurance Supervisor? | Goodwin University www.goodwin.edu
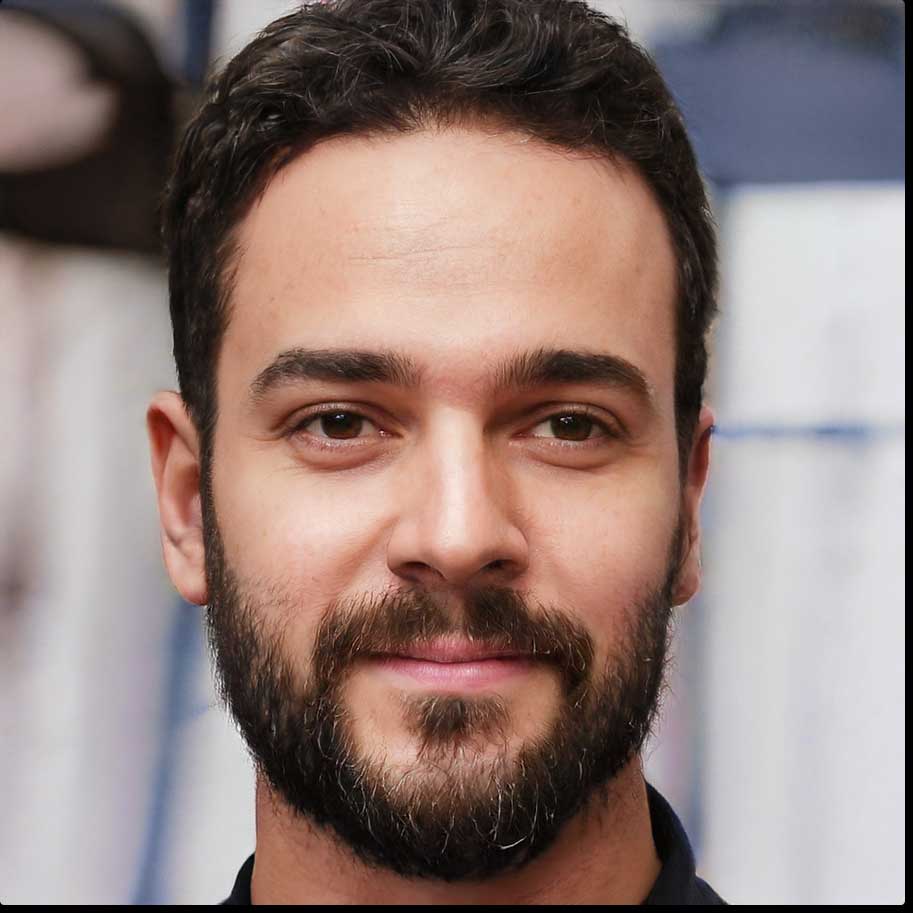