How to Be Quality Systems Manager - Job Description, Skills, and Interview Questions
Steps How to Become
- Obtain a Bachelor's Degree. You'll need a bachelor's degree in a relevant field such as engineering, chemistry, or biology to become a quality systems manager.
- Gain Relevant Work Experience. Quality systems managers are expected to have experience in quality assurance and quality control. You can gain experience working as a quality assurance specialist or quality control technician in an industry related to the organization you hope to manage.
- Earn a Quality Systems Management Certification. Quality systems managers should become certified in their field. There are several certifications available, such as the Certified Quality Manager (CQM) from the American Society for Quality (ASQ). The CQM requires you to have significant experience in quality management and pass an exam.
- Develop Your Leadership Skills. Quality systems managers are responsible for leading a team of quality assurance and quality control specialists. You should develop your leadership skills by taking classes or workshops on team management and communication.
- Apply for Quality Systems Manager Positions. Once you have the education, experience, certification, and leadership skills needed to become a quality systems manager, you're ready to apply for jobs. Check job boards and industry websites for open positions. You can also contact organizations directly to inquire about job openings.
Staying ahead and efficient in a Quality Systems Manager role requires a combination of proactive planning, continual improvement, and effective communication. To plan ahead, Quality Systems Managers should set clear objectives, establish measurable goals, and develop strategies to achieve them. They should also stay up-to-date on industry trends and best practices, and review relevant legislation and regulations.
To ensure continual improvement, Quality Systems Managers should stay organized and use data to inform decision making. They should also create systems to monitor and measure progress, and identify areas for improvement. Finally, effective communication with stakeholders is key to successful Quality Systems Management.
Quality Systems Managers should ensure they communicate clearly, accurately, and in a timely manner to maintain relationships and ensure everyone is on the same page.
You may want to check Quality Performance Analyst, Quality Improvement Engineer, and Quality Systems Coordinator for alternative.
Job Description
- Develop and implement quality assurance protocols and procedures.
- Monitor and evaluate the effectiveness of quality assurance programs.
- Monitor customer complaints, collect and analyze customer feedback, and initiate corrective action plans.
- Develop and maintain quality systems to ensure product and service quality meets customer requirements.
- Manage and coordinate customer complaints, audits and other quality-related activities.
- Develop, implement and review the effectiveness of corrective action plans.
- Maintain a safe working environment in compliance with all applicable regulations.
- Monitor the performance of suppliers and subcontractors to ensure quality requirements are met.
- Prepare and review quality documentation, such as inspection plans, inspection reports and test plans.
- Train and mentor staff on quality assurance processes and tools.
Skills and Competencies to Have
- Understanding of Quality Management System (QMS) standards and principles.
- Knowledge of Quality Assurance processes and procedures.
- Experience in developing and leading quality initiatives.
- Ability to analyze and interpret data to identify trends and improvement opportunities.
- Strong problem-solving, decision-making, and analytical skills.
- Excellent communication, interpersonal, and leadership skills.
- Proficient in data management and analysis software.
- Knowledge of quality control techniques and tools, including Six Sigma and Lean Manufacturing.
- Ability to develop and implement corrective action plans to address quality issues.
- Ability to develop, review, and maintain quality documentation.
- Proven experience in auditing and inspecting processes for compliance with quality requirements.
- Excellent organizational, time management, and multitasking skills.
Having excellent organizational and communication skills are essential for a Quality Systems Manager. One of the most important skills for this role is the ability to effectively manage and monitor quality assurance systems. These systems must be designed to ensure products and services meet quality standards.
Quality Systems Managers must have a firm understanding of relevant regulations, standards, and industry best practices in order to ensure compliance with these regulations. They must also be able to work with management and other stakeholders to identify potential areas of improvement and to ensure that corrective action is taken as needed. This requires strong leadership and negotiation skills, as well as the ability to coordinate multiple complex tasks.
Quality Systems Managers must be able to identify when processes need to be updated or modified, as well as being able to effectively communicate changes to all stakeholders. By having these skills, a Quality Systems Manager can help ensure that products and services meet quality standards, leading to higher customer satisfaction and increased profitability.
Quality Engineer, Quality Control Inspector, and Quality Systems Analyst are related jobs you may like.
Frequent Interview Questions
- What experience do you have in developing and managing Quality Systems?
- How do you ensure your Quality Systems are effective and compliant with industry standards?
- What strategies do you use to resolve conflicts between different Quality Systems?
- Describe a recent project where you implemented a Quality System.
- What challenges have you faced in managing Quality Systems?
- How do you ensure that all stakeholders are informed about the Quality System?
- What techniques do you use to train personnel on Quality Systems?
- How do you measure the success of Quality Systems?
- How do you manage changes to Quality Systems?
- How do you stay up-to-date with the latest Quality Systems trends?
Common Tools in Industry
- Quality Assurance Software. A software tool used to measure and control the quality of products and services. (Example: Zoho Quality Assurance)
- Quality Control Software. A software tool used to ensure that processes and products meet specific standards. (Example: ISO Quality Control Software)
- Quality Management Systems (QMS). A system for managing the quality of a product or service throughout its life cycle. (Example: ASI QMS)
- Quality Analysis Software. A software tool used to analyze data from a variety of sources to detect patterns and trends, identify potential problems, and generate insights. (Example: Minitab Quality Analysis Software)
- Quality Improvement Software. A software tool used to identify opportunities for process and product improvement, develop solutions, and track progress towards goals. (Example: Six Sigma Quality Improvement Software)
- Risk Management Software. A software tool used to identify, assess, and monitor risks in order to minimize their impact on the organization. (Example: Risk Manager Software)
- Document Management Software. A software tool used to organize, store, and manage documents and other data in an organized manner. (Example: DocuWare Document Management Software)
- Auditing Software. A software tool used to evaluate compliance with standards, policies, and procedures, as well as identify areas of improvement. (Example: ProcessAudit Auditing Software)
Professional Organizations to Know
- International Society for Quality in Healthcare (ISQua)
- American Society for Quality (ASQ)
- Healthcare Quality Association on Accreditation (HQAA)
- The Joint Commission
- Institute for Healthcare Improvement (IHI)
- International Accreditation Forum (IAF)
- European Foundation for Quality Management (EFQM)
- Regulatory Affairs Professionals Society (RAPS)
- The Association for the Advancement of Medical Instrumentation (AAMI)
- American College of Healthcare Executives (ACHE)
We also have Quality Technician, Quality Improvement Analyst, and Quality Support Analyst jobs reports.
Common Important Terms
- ISO 9001. An internationally recognized standard for Quality Management Systems (QMS) that defines the requirements for organizations to achieve customer satisfaction and continual improvement.
- Quality Management Plan (QMP). A document that outlines the organization's strategy for achieving quality objectives, policies, and processes.
- Quality Assurance (QA). An activity or set of activities that ensure a product or service meets specified requirements.
- Quality Control (QC). The process of verifying that a product or service meets its quality requirements.
- Risk Management. The process of identifying, analyzing, and responding to potential risks in order to minimize their impact.
- Total Quality Management (TQM). An approach to managing organizations that focuses on continuously improving all aspects of their operations.
- Process Improvement. The practice of improving business processes in order to increase efficiency, reduce costs, and improve customer satisfaction.
- Root Cause Analysis (RCA). A method used to identify the underlying causes of a problem in order to prevent it from happening again.
Frequently Asked Questions
What is the job of a Quality Systems Manager?
A Quality Systems Manager is responsible for designing, implementing, and maintaining quality management systems to ensure that products and services meet required standards.
What qualifications are needed for a Quality Systems Manager?
A Quality Systems Manager typically requires a bachelor's degree in engineering, quality assurance, or a related field, as well as several years of experience in a related field.
What are the duties of a Quality Systems Manager?
The primary duties of a Quality Systems Manager include developing and implementing quality control procedures, conducting audits and reviews, ensuring compliance with safety standards, and overseeing the development of corrective action plans.
What tools are used by a Quality Systems Manager?
Quality Systems Managers typically use a variety of tools including quality management software, statistical process control (SPC) charts, cause and effect diagrams, and root cause analysis.
What is the average salary of a Quality Systems Manager?
According to PayScale, the average salary for a Quality Systems Manager is $72,719 per year.
What are jobs related with Quality Systems Manager?
- Quality Improvement Lead
- Quality Improvement Coordinator
- Quality Assurance Technician
- Quality Assurance Coordinator
- Quality Support Specialist
- Quality Support Coordinator
- Quality Control Lead
- Quality Management Analyst
- Quality Management Specialist
- Quality Assurance Consultant
Web Resources
- Quality Systems Management Degree | Northwestern SPS: sps.northwestern.edu
- Quality Management System (QMS) Training - Purdue quality.mep.purdue.edu
- Quality Management Program - Online Bachelor's Degree global.cambridgecollege.edu
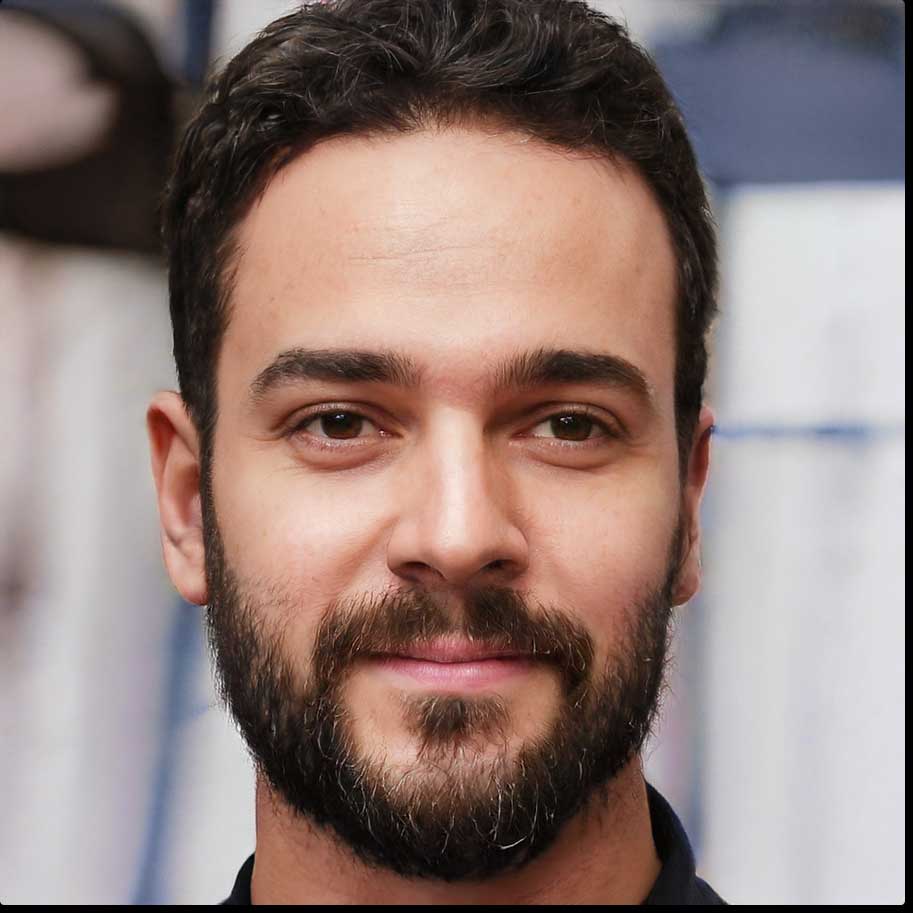