How to Be Quality Improvement Engineer - Job Description, Skills, and Interview Questions
Steps How to Become
- Obtain a Bachelors Degree in Quality Improvement Engineering. Quality Improvement Engineering degrees are usually offered at technical schools and universities. Coursework typically includes topics such as quality control, reliability engineering, quality management, and manufacturing processes.
- Obtain a Masters Degree in Quality Improvement Engineering. A Masters in Quality Improvement Engineering can provide additional knowledge and skills in the field, such as data analysis, continuous improvement, and problem solving.
- Get industry experience. Completing an internship or working as a quality engineer can provide valuable experience in the field.
- Become certified as a Quality Improvement Engineer. Professional certifications such as the Certified Quality Improvement Engineer (CQIE) from the American Society for Quality (ASQ) can demonstrate expertise and credibility.
- Consider additional certifications. Additional certifications may be necessary depending on the industry, company, or job duties. For example, the Certified Six Sigma Black Belt (CSSBB) from ASQ is often required for quality improvement engineer positions in the medical device industry.
- Network with other professionals in the field. Building relationships with other quality improvement engineers can help to stay up to date with industry trends, as well as identify potential job opportunities.
Continuous improvement is essential for Quality Improvement Engineers to stay ahead and qualified. By staying abreast of new technology and industry trends, Quality Improvement Engineers can ensure they are equipped with the latest skills and knowledge, allowing them to remain competitive in their field. By keeping up with advances in quality management systems, Quality Improvement Engineers can ensure that their processes are as efficient and effective as possible.
obtaining certifications in relevant fields and attending conferences or workshops can further enhance their qualifications and help them stay ahead of the curve. By investing in their professional growth and development, Quality Improvement Engineers can remain qualified and successful in their field.
You may want to check Quality Assurance Inspector, Quality Assurance Coordinator, and Quality Improvement Specialist for alternative.
Job Description
- Develop and implement quality improvement process initiatives to identify, analyze and improve current business processes.
- Establish and maintain standards for process improvement projects, including project plans and timelines.
- Monitor, measure and report on quality performance, effectiveness and accuracy of processes.
- Analyze customer feedback and other data sources to identify areas for improvement in products and services.
- Develop and document quality assurance procedures and audit plans to ensure compliance with regulations and standards.
- Design control systems to ensure quality and accuracy of product output.
- Develop training programs to enhance the knowledge and skills of quality personnel in the organization.
- Facilitate team meetings and workshops to identify process improvement opportunities.
- Monitor the implementation of process improvement initiatives.
- Provide technical guidance and support to other departments in the development and implementation of quality improvement strategies.
Skills and Competencies to Have
- Technical knowledge of quality systems and processes.
- Ability to develop quality improvement plans.
- Strong analytical skills and data-driven mindset.
- Excellent communication and interpersonal skills.
- Proficiency in statistical analysis and process mapping.
- Knowledge of root cause analysis techniques.
- Ability to work with cross-functional teams.
- Ability to design and implement experiments to test process changes.
- Knowledge of tqm (Total Quality Management) principles.
- Knowledge of ISO 9000 and other quality standards.
Quality Improvement Engineers play a vital role in ensuring the success of any business. They are responsible for identifying and resolving any issues that may be causing problems with the production process. The most important skill they need to have is problem-solving.
Being able to identify the root cause of issues and coming up with innovative solutions is absolutely crucial. With their sharp analytical skills, Quality Improvement Engineers can quickly identify any areas of improvement that need to be addressed. They also need to have excellent communication skills, as they must be able to explain their solutions clearly to stakeholders.
Furthermore, strong organizational skills are also essential for Quality Improvement Engineers, as they must be able to prioritize tasks and manage time effectively. By possessing these skills, Quality Improvement Engineers can ensure that the production process is running smoothly and efficiently.
Quality Supervisor, Quality Support Specialist, and Quality Improvement Technician are related jobs you may like.
Frequent Interview Questions
- What experience do you have working in quality improvement or process improvement?
- Describe a successful project you've completed related to quality improvement.
- How do you ensure that all stakeholders are involved in the quality improvement process?
- How do you use data and analysis to identify problems and solutions for improvement?
- How do you plan and prioritize workflow to meet deadlines for quality improvement projects?
- What methods do you use to measure the effectiveness of quality improvement initiatives?
- How do you collaborate with other departments and teams to ensure quality improvement?
- Describe a project in which you used root cause analysis to solve a quality issue.
- What strategies do you use to motivate team members working on quality improvement projects?
- What metrics or KPIs do you use to track progress and performance of quality improvement initiatives?
Common Tools in Industry
- Lean Six Sigma. Lean Six Sigma is an approach that focuses on improving quality by eliminating waste and reducing variability. Example: Measuring customer satisfaction to identify areas for improvement.
- Statistical Process Control (SPC). SPC is a method of using statistical techniques to analyze process data in order to identify trends, patterns, or special causes of variation and take corrective action. Example: Monitoring production line output and making adjustments as needed to maintain quality.
- Kaizen. Kaizen is a Japanese term for continuous improvement that emphasizes small, incremental changes in processes, rather than large-scale overhauls. Example: Holding daily meetings to discuss ways to improve the production process.
- Root Cause Analysis (RCA). RCA is a structured problem-solving method that identifies the underlying causes of problems so that corrective action can be taken. Example: Investigating customer complaints to identify the root cause of the issue.
- Design of Experiments (DOE). DOE is a scientific approach to testing different variables in order to understand their effect on a particular process or outcome. Example: Testing different types of packaging to determine which one offers the best protection for the product.
Professional Organizations to Know
- American Society for Quality (ASQ)
- International Quality Federation (IQF)
- Institute of Industrial and Systems Engineers (IISE)
- Society of Manufacturing Engineers (SME)
- International Organization for Standardization (ISO)
- Association for Advancement of Medical Instrumentation (AAMI)
- American Society of Mechanical Engineers (ASME)
- International Council on Systems Engineering (INCOSE)
- Institute of Electrical and Electronics Engineers (IEEE)
- Institute of Certified Professional Managers (ICPM)
We also have Quality Improvement Analyst, Quality Engineer, and Quality Control Lead jobs reports.
Common Important Terms
- Process Improvement. Process improvement is the practice of improving existing processes within an organization. It typically involves analyzing processes, identifying areas for improvement, and implementing changes to increase efficiency and reduce costs.
- Quality Assurance. Quality Assurance is a set of activities that are designed to ensure that products or services meet established standards of quality. Quality assurance helps organizations to meet customer expectations and achieve desired outcomes.
- Six Sigma. Six Sigma is a set of techniques and tools used to improve processes and reduce variation. It is based on the principles of continuous improvement and problem solving, and it focuses on reducing defects and increasing efficiency.
- Lean Manufacturing. Lean Manufacturing is a system of production that emphasizes reducing waste and increasing efficiency. The goal of Lean Manufacturing is to produce the highest quality product at the lowest possible cost.
- Total Quality Management. Total Quality Management (TQM) is a system of management that focuses on continuous improvement and customer satisfaction. TQM involves implementing processes and procedures that ensure quality at every stage of the production process.
Frequently Asked Questions
What is a Quality Improvement Engineer?
A Quality Improvement Engineer is a professional who works to identify and implement process improvements to ensure quality and efficiency in a company's operations.
What are some of the responsibilities of a Quality Improvement Engineer?
Quality Improvement Engineers are responsible for developing and implementing quality assurance processes and procedures, monitoring process performance, and designing and implementing process improvements.
What qualifications are needed to become a Quality Improvement Engineer?
To become a Quality Improvement Engineer, individuals must possess a Bachelor's degree in engineering, quality assurance, or a related field, as well as experience in quality management systems and process improvement techniques.
How is the role of Quality Improvement Engineer different from that of a Quality Manager?
Quality Improvement Engineers focus on developing and implementing process improvements, while Quality Managers are responsible for overseeing the overall quality assurance system within an organization.
What are some of the key metrics used by Quality Improvement Engineers?
Quality Improvement Engineers typically use metrics such as defect rate, cycle time, customer satisfaction, and cost savings to measure the effectiveness of process improvements.
What are jobs related with Quality Improvement Engineer?
- Quality Systems Specialist
- Quality Control Manager
- Quality Assurance Auditor
- Quality Improvement Inspector
- Quality Management Coordinator
- Quality Control Inspector
- Quality Systems Coordinator
- Quality Technician
- Quality Assurance Supervisor
- Quality Systems Manager
Web Resources
- Quality Improvement - University of Utah accelerate.uofuhealth.utah.edu
- Process Quality Engineer | NC State Online and Distance Education online-distance.ncsu.edu
- What is Quality Improvement in Healthcare? | SNHU www.snhu.edu
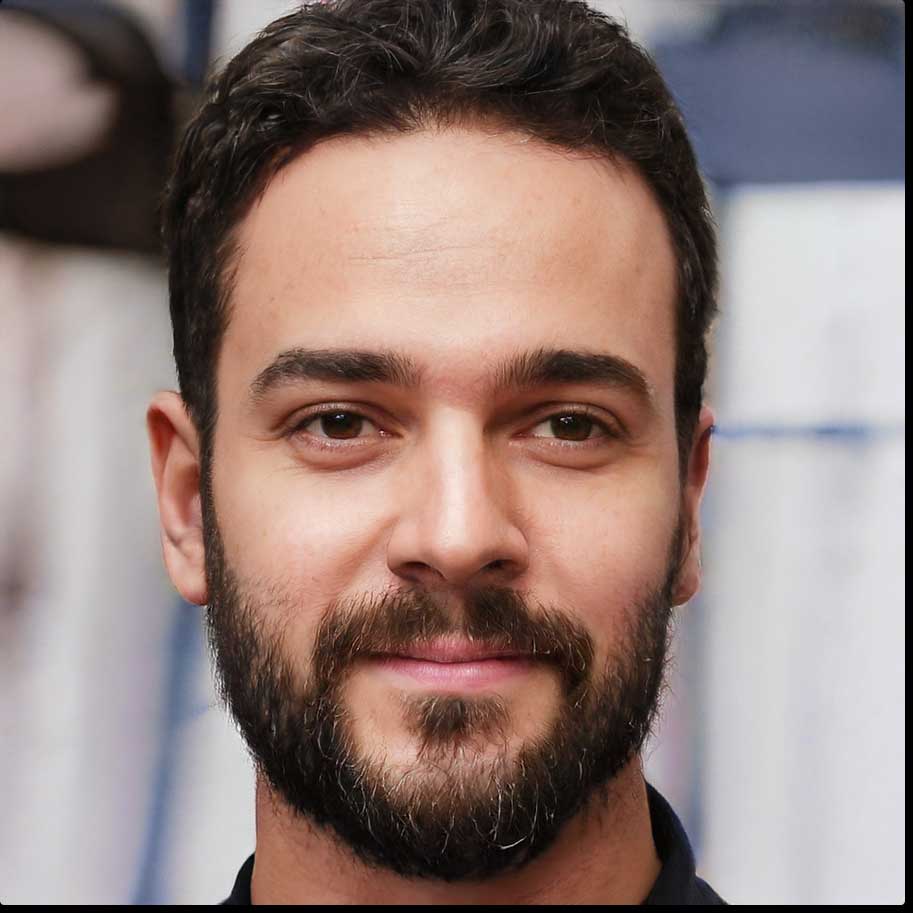