How to Be Quality Systems Specialist - Job Description, Skills, and Interview Questions
The implementation of a quality systems specialist in a business is essential for the successful operation of the company. By establishing quality systems and standards, a quality systems specialist can ensure that products and services meet customer expectations. This leads to increased customer satisfaction, improved customer loyalty, and ultimately increased profits.
by maintaining quality systems and standards, a business can prevent costly mistakes, reduce waste, and increase efficiency. the presence of a quality systems specialist can have a positive impact on a business, resulting in greater success and profitability.
Steps How to Become
- Earn a Bachelors Degree. The first step to becoming a Quality Systems Specialist is to earn a bachelors degree in an engineering or related field. This will provide the fundamental knowledge and skills needed to understand and develop quality systems.
- Obtain Relevant Work Experience. In order to become a Quality Systems Specialist, it is important to have relevant work experience. This could include positions in manufacturing, engineering, or quality assurance.
- Pursue Certification. Pursuing certification as a Quality Systems Specialist is another important step in the process. There are several certifying organizations that provide certification for Quality Systems Specialists.
- Get Trained in Quality Management. It is also important to become trained in quality management systems, such as ISO 9001, ISO 14001, and OHSAS 18001. This will help develop the skills necessary to be successful in this field.
- Stay Current with Industry Trends. Finally, it is important to stay current with industry trends and best practices. Quality Systems Specialists must be knowledgeable about the latest developments and changes in the field.
The implementation of an effective Quality System is essential to ensuring the success of any company. A Quality System Specialist is responsible for creating and implementing an effective quality system that meets the needs of the organization. They must be experienced in identifying the root causes of problems and developing solutions that can help prevent their reoccurrence.
Quality Systems Specialists work with all levels of management to ensure the quality of products and services meet or exceed customer expectations. An effective Quality System provides a framework for consistent processes, documentation, and communication between all departments, as well as providing a platform for continuous improvement and cost savings. By utilizing the right tools and techniques, Quality Systems Specialists can help organizations create an efficient quality system that is compliant with standards and regulations.
In turn, this can result in improved customer satisfaction and increased profitability.
You may want to check Quality Manager, Quality Systems Coordinator, and Quality Improvement Coordinator for alternative.
Job Description
- Quality Systems Specialist: Responsible for developing, implementing, and managing quality assurance systems and processes to ensure compliance with applicable regulations and industry standards. Performs audits of quality systems and processes to ensure compliance with applicable regulations and industry standards.
- Quality Assurance Technician: Responsible for carrying out inspections, tests, and measurements to ensure product quality and reliability. Identifies and documents defects and non-conformities in products.
- Quality Systems Engineer: Responsible for designing, developing, and maintaining quality systems and processes to ensure that products meet customer requirements and applicable regulations.
- Quality Control Analyst: Responsible for monitoring the quality of products during production and storage. Develops and implements quality control plans and procedures to ensure product quality assurance.
- Quality Assurance Manager: Responsible for overseeing the quality assurance program. Sets quality assurance standards, monitors quality systems and processes, and implements corrective action when needed.
Skills and Competencies to Have
- Understanding of quality systems, including ISO, FDA, and other regulatory standards
- Knowledge of process improvement and audit techniques
- Ability to develop, maintain, and review quality system documentation
- Ability to identify and address areas of concern within a quality system
- Ability to develop and implement corrective actions
- Proficiency in data collection, analysis, and report writing
- Proficiency in Microsoft Office Suite (Word, Excel, PowerPoint, etc. )
- Excellent organizational skills
- Strong communication and interpersonal skills
- Ability to work independently and as part of a team
The ability to develop and maintain high quality systems is essential for any organization. Quality systems help to ensure that products, services, and processes meet the highest standards and meet customer expectations. Quality systems specialists are responsible for designing, implementing, and maintaining systems that identify and reduce errors and ensure that the organization is meeting its goals.
The ability to understand and apply quality principles and techniques is a key skill for quality systems specialists. They must also be able to analyze data and make decisions based on their findings. they must be able to communicate effectively with stakeholders, such as customers, suppliers, and employees.
Without the skills of a quality systems specialist, an organization would have difficulty meeting customer expectations, preventing errors, and staying on track with its goals.
Quality Assurance Coordinator, Quality Improvement Inspector, and Quality Control Lead are related jobs you may like.
Frequent Interview Questions
- What experience do you have in developing and implementing Quality Systems?
- What techniques do you use to ensure that Quality Systems are adequately maintained?
- How do you stay up to date with Quality System regulations, standards and best practices?
- What strategies have you used to ensure customer satisfaction with Quality Systems?
- Describe a successful Quality System implementation project you have been involved in.
- How do you ensure that Quality System-related decisions align with the organization's overall objectives?
- How do you handle non-conformance to Quality Systems?
- What challenges have you faced in managing Quality Systems?
- How do you use data to measure the effectiveness of Quality Systems?
- In what ways do you seek to continuously improve Quality Systems?
Common Tools in Industry
- Quality Control Software. A software tool used to track, monitor and analyze quality assurance data (eg: Minitab).
- Quality Management System (QMS). A comprehensive system that defines the processes, procedures and responsibilities to ensure quality products and services (eg: ISO 9001).
- Auditing Software. A software tool used to assess the compliance of processes, procedures and products with standards (eg: MetricStream).
- Statistical Process Control (SPC). A method used to identify and control process variability by monitoring and recording key performance indicators (eg: Excel).
- Root Cause Analysis (RCA). A problem-solving technique used to identify the underlying cause of an issue or defect (eg: Fishbone Diagrams).
- Document Control System. A system used to ensure documents related to quality assurance are up-to-date and compliant with standards (eg: MasterControl).
Professional Organizations to Know
- American Society for Quality (ASQ)
- International Quality Federation (IQF)
- Quality Management Institute (QMI)
- Institute of Quality Assurance (IQA)
- International Society for Quality Research (ISQR)
- International Organization for Standardization (ISO)
- Association for the Advancement of Medical Instrumentation (AAMI)
- National Institute for Standards and Technology (NIST)
- American National Standards Institute (ANSI)
- International Conference on Quality and Improvement (ICQI)
We also have Quality Assurance Supervisor, Quality Control Manager, and Quality Performance Analyst jobs reports.
Common Important Terms
- Quality Assurance (QA). A process used to ensure that products and services meet a certain level of quality and consistency.
- Quality Control (QC). The process of inspecting and testing products to ensure they meet established quality standards and comply with customer requirements.
- Quality Management System (QMS). A system developed to help organizations manage their quality processes and ensure consistent and high-quality products and services.
- Quality Standards. A set of criteria used to measure the quality of a product or service, such as ISO 9000 or Six Sigma.
- Quality Metrics. Measures used to evaluate the performance and effectiveness of processes and products.
- Auditing. A systematic review of an organizations processes, procedures, and systems to ensure compliance with quality standards.
- Root Cause Analysis (RCA). A process used to identify and analyze the causes of a problem or issue in order to find an effective solution.
Frequently Asked Questions
What is a Quality Systems Specialist?
A Quality Systems Specialist is a professional responsible for developing, maintaining, and monitoring quality assurance systems and processes in an organization.
What are the responsibilities of a Quality Systems Specialist?
Responsibilities of a Quality Systems Specialist include designing and implementing quality control standards and procedures, monitoring product quality standards, verifying process control standards, and assessing customer satisfaction.
What qualifications are necessary to become a Quality Systems Specialist?
To become a Quality Systems Specialist, one must have a bachelor's degree in a related field such as engineering, quality management, or industrial engineering. Additionally, relevant experience in quality assurance or management is also beneficial.
What type of job growth is expected for Quality Systems Specialists?
According to the Bureau of Labor Statistics, the job outlook for Quality Systems Specialists is expected to grow by 7% from 2018 to 2028.
How much does a Quality Systems Specialist typically earn?
According to Payscale.com, the average salary for a Quality Systems Specialist is $63,000 per year.
What are jobs related with Quality Systems Specialist?
- Quality Improvement Specialist
- Quality Performance Coordinator
- Quality Assurance Technician
- Quality Management Manager
- Quality Support Analyst
- Quality Management Coordinator
- Quality Performance Manager
- Quality Control Inspector
- Quality Management Specialist
- Quality Improvement Manager
Web Resources
- Biologist (Quality Systems Specialist) Career Center careers.usc.edu
- Biologist (Quality Systems Specialist) - career.arizona.edu career.arizona.edu
- Biologist (Quality Systems Specialist) Office of Career Services ... careerservices.fas.harvard.edu
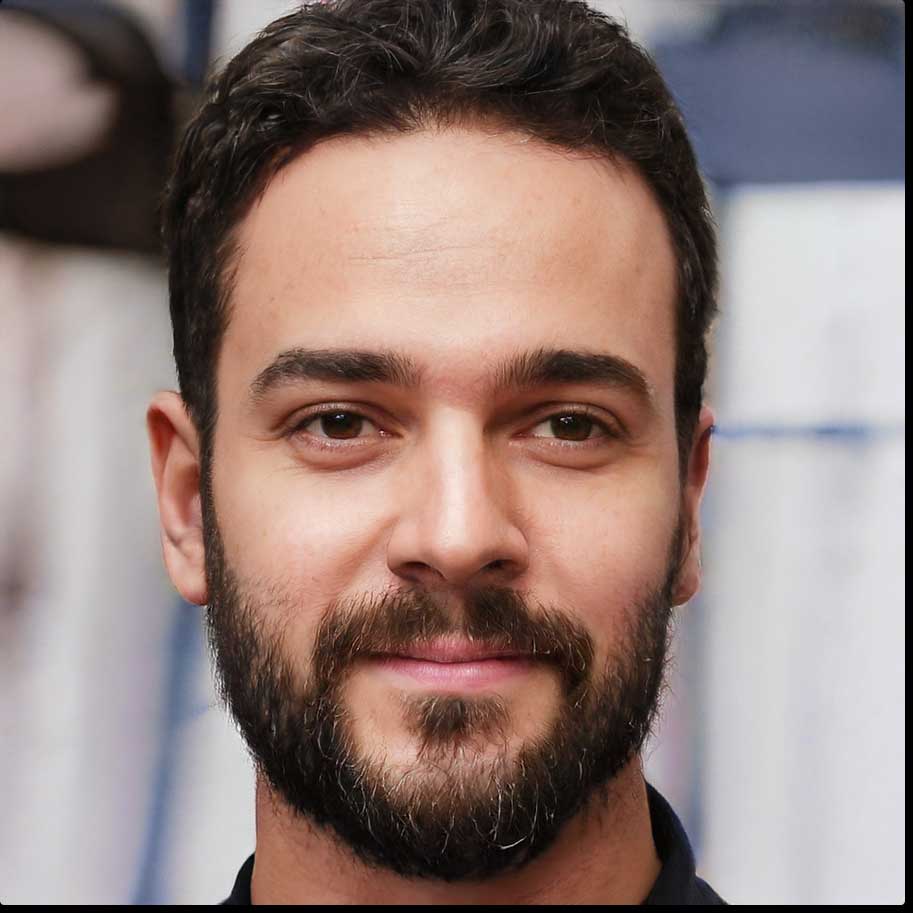