How to Be Mold Maker Machinist - Job Description, Skills, and Interview Questions
Mold makers and machinists play an important role in the manufacturing of products. Mold makers create the molds that define the shape of products, while machinists use lathes, milling machines and other tools to cut, shape and form the materials used to make products. The cause-and-effect relationship between mold makers and machinists is clear: without the molds created by mold makers, it would be impossible for machinists to transform raw materials into the products needed.
without the skills of machinists, the molds created by mold makers would be useless. Both these roles are essential to the manufacturing process, and both are required to produce quality products.
Steps How to Become
- Obtain a high school diploma or equivalent. A high school diploma or equivalent is typically required to become a mold maker machinist.
- Enroll in an apprenticeship program. Apprenticeships are the most common way to become a mold maker machinist. They last for about four years, and involve both on-the-job training and classroom instruction.
- Learn about mold making. In order to become a successful mold maker machinist, you must have a thorough understanding of mold-making principles and processes.
- Learn how to operate machinery. As a mold maker machinist, you will be required to operate various types of machinery and tools, including lathes, mills, grinders, and computer numerical control (CNC) machines.
- Become certified. Certification is optional for mold maker machinists, but it can be beneficial in terms of both job prospects and wages. A number of certification programs are offered by trade associations and other organizations.
- Obtain additional training. Many employers require mold maker machinists to have additional training in areas such as quality control, safety, and advanced manufacturing technologies. Employers may also require specialized training in certain types of materials, such as plastics and metals.
Mold Maker Machinists are responsible for the production of custom molds, parts and tools from raw material. In order to remain efficient and up-to-date, Mold Maker Machinists must stay current on the latest technologies, techniques, and materials available. This can be accomplished by attending classes, workshops and/or webinars, reading professional journals, and engaging with other professionals in their field.
Mold Maker Machinists should invest in modern tools and equipment, as well as practice proper maintenance to ensure the machines are running properly. By taking the necessary steps to stay informed and ahead of the curve, Mold Maker Machinists can increase their productivity and quality of work, while reducing costs and waste.
You may want to check Laser Machinist, Fabrication Machinist, and Manual Machinist for alternative.
Job Description
- Design and fabricate metal molds used for producing plastic and metal parts.
- Set up, operate, and maintain CNC machines and other related equipment.
- Measure and verify dimensions of machined parts against drawings and specifications.
- Make necessary adjustments to machines to maintain quality production.
- Troubleshoot machining problems and take corrective action.
- Read and interpret blueprints, sketches, and other technical documents to determine machining requirements.
- File, grind, and polish molds to ensure proper fit and finish.
- Perform regular maintenance and cleaning of machining equipment.
- Working knowledge of safety protocols related to operating machinery.
- Keep accurate records of time, materials, and other data related to production.
Skills and Competencies to Have
- Knowledge of CNC machines and their operation.
- Ability to read and interpret blueprints to create molds.
- Proficiency in using a variety of hand tools, power tools, and measuring instruments.
- Ability to perform complex mathematical calculations.
- Knowledge of metallurgy and mold materials.
- Ability to troubleshoot and repair molds and machines.
- Understanding of safety protocols and procedures.
- Ability to collaborate and work with others in a team environment.
- Strong problem solving and communication skills.
- Detail-oriented with the ability to work independently.
Being a Mold Maker Machinist requires a specialist set of skills, including the ability to accurately read and interpret technical drawings, use a range of sophisticated tools and machines, and understand the principles of metalworking. A Mold Maker Machinist must also be able to work within tight tolerances and have excellent problem-solving skills. Furthermore, the ability to work within a team environment is essential, as is the ability to communicate effectively with colleagues and other stakeholders.
The combination of these skills leads to a successful Mold Maker Machinist who is able to create quality components that meet customer needs. When these elements are combined, it leads to satisfied customers, increased production efficiency, and a profitable business.
Lathe Machinist, Mill Machinist, and CNC Machinist are related jobs you may like.
Frequent Interview Questions
- What experience do you have working with mold making machinery?
- What processes do you use to ensure precision when making molds?
- How have you optimized production efficiency for mold making?
- What safety protocols do you follow when operating mold making machinery?
- What challenges have you faced in your previous mold making projects?
- How do you troubleshoot and diagnose any issues with the machinery?
- What materials do you prefer to work with when making molds?
- How do you ensure the quality of the molds you produce?
- How have you contributed to the development of new processes or technologies in the field of mold making?
- What measures do you take to stay up-to-date on industry trends and advancements in mold making?
Common Tools in Industry
- Lathe. A machine used to shape a material by rotating it against a cutting tool. (eg: turning a metal cylinder into a sphere)
- Milling Machine. A machine used to shape materials by cutting with a rotary cutting tool. (eg: cutting grooves in a metal block)
- Drill Press. A machine used to make holes in materials by drilling into them with a drill bit. (eg: drilling a hole in a metal plate)
- Grinder. A machine used to grind materials by abrading them with an abrasive wheel. (eg: sharpening the edges of a metal object)
- Saw. A machine used to cut materials by using a blade or a rotating disc. (eg: cutting a piece of wood into two pieces)
- Sander. A machine used to smooth materials by abrading them with an abrasive belt or paper. (eg: sanding down wood to create a smooth finish)
- Heat Treating Furnace. A machine used to heat treat materials in order to change their properties. (eg: hardening steel parts to increase their strength)
- EDM Machine. A machine used to cut materials using electrical discharges. (eg: cutting intricate shapes out of metal pieces)
- CNC Machine. A computer-controlled machine used to shape materials with high precision. (eg: carving intricate designs into plastic parts)
Professional Organizations to Know
- The Society of Manufacturing Engineers (SME)
- National Tooling and Machining Association (NTMA)
- American Mold Makers Association (AMMA)
- International Mold Makers Association (IMMA)
- Tool and Manufacturing Engineers Association (TMEA)
- Association for Manufacturing Technology (AMT)
- American Machine Tool Distributors Association (AMTDA)
- American Precision Machinists Association (APMA)
- International Association of Machinists and Aerospace Workers (IAMAW)
- National Association of Manufacturers (NAM)
We also have Grinder Machinist, Prototype Machinist, and Production Machinist jobs reports.
Common Important Terms
- CNC Machining. Computer Numerical Control (CNC) Machining is a manufacturing process that uses computers to control machine tools such as lathes, mills, and grinders to create custom parts.
- Toolmaking. Toolmaking is the process of designing, creating, and maintaining tools used in the production of goods.
- Metal fabrication. Metal fabrication is the process of forming, cutting, and assembling various components from raw materials to create metal products.
- CAD/CAM Software. CAD/CAM software is used for design and manufacturing of parts and components. It is used to create 3D models, drawings, and CNC programs.
- Mold Making. Mold making is the process of creating molds from which parts can be cast in various materials.
- Injection Molding. Injection molding is a manufacturing process that uses molds to form parts out of thermoplastic or thermoset plastics.
- Heat Treatment. Heat treatment is a process used to alter the physical and sometimes chemical properties of metals or other materials.
- Surface Finishing. Surface finishing is a process used to improve the aesthetics, smoothness, and/or durability of a materials surface.
- Quality Control. Quality control is a process used to ensure that products meet predetermined standards of quality.
- Metrology. Metrology is the study of measurement, including the development of measurement systems, instruments, and standards.
Frequently Asked Questions
What is a Mold Maker Machinist?
A Mold Maker Machinist is a professional who designs and fabricates molds used in industrial manufacturing. They use advanced machining techniques to create a variety of precision molds for injection molding, rotational molding, die casting, and other manufacturing processes.
What skills are needed to be a Mold Maker Machinist?
A Mold Maker Machinist requires strong technical skills in CNC machining, CAD/CAM software, and manual machining operations. They should also have a strong knowledge of metallurgy and material selection. Problem-solving skills and attention to detail are also essential for success in this field.
What qualifications are required for a Mold Maker Machinist?
Typically, employers require a high school diploma or GED and formal training in CNC machining and CAD/CAM software. Additionally, many employers also prefer to hire individuals who have experience in the manufacturing industry.
What is the average salary of a Mold Maker Machinist?
According to the Bureau of Labor Statistics, the median annual salary for a Mold Maker Machinist in the United States is $40,430. Salaries can vary depending on experience, location, and type of employer.
How long does it take to become a Mold Maker Machinist?
It typically takes one to two years of training and experience to become a qualified Mold Maker Machinist. However, the exact amount of time may vary depending on the individual's experience level and training program.
What are jobs related with Mold Maker Machinist?
- Tool and Die Machinist
- Welding Machinist
- Quality Control Machinist
- Machine Operator (Machinist)
- Maintenance Machinist
- Assembly Machinist
- Die Cast Machinist
Web Resources
- Mold Maker Apprentice | WTCS www.wtcsystem.edu
- Mold Making, Certificate < College of DuPage catalog.cod.edu
- Tool and Die Maker Apprenticeship - Northcentral Technical College www.ntc.edu
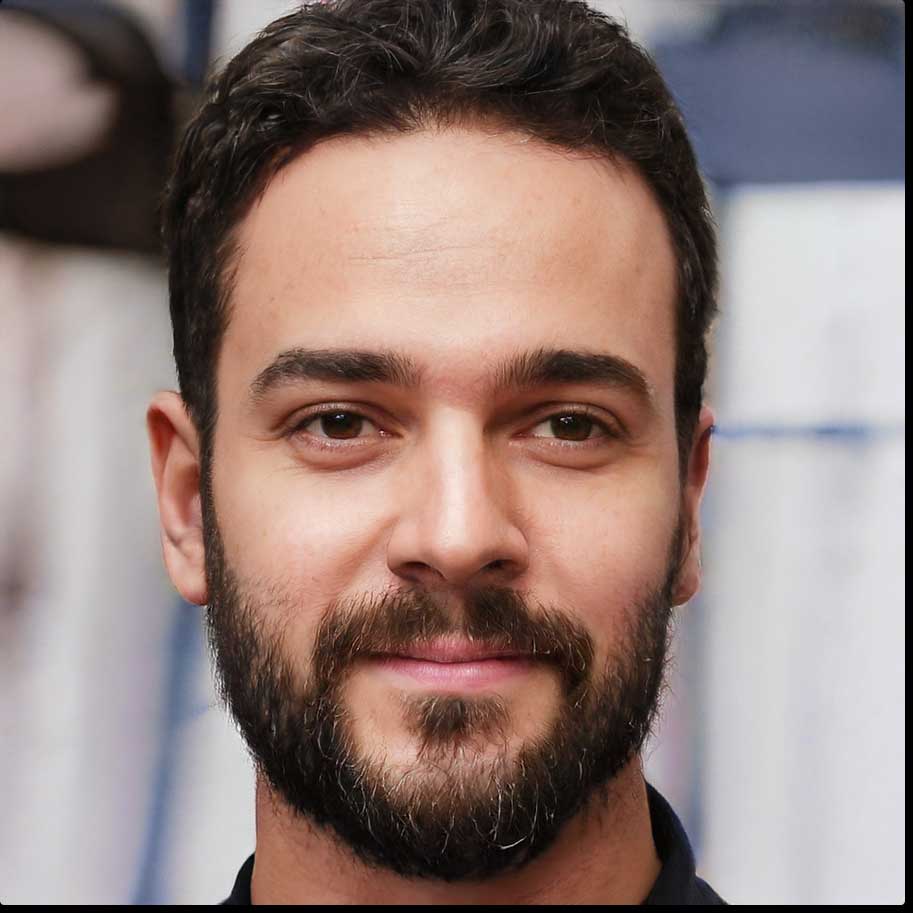