How to Be Assembly Machinist - Job Description, Skills, and Interview Questions
Assembly Machinists are highly skilled professionals who use a variety of tools and machines to assemble components. They are responsible for the accuracy and precision of each part they produce and must adhere to strict quality standards. The assembly process involves multiple steps and requires precision, accuracy and attention to detail.
Poorly assembled parts can lead to costly delays, breakdowns, and even dangerous malfunction in the products they assemble. Working as an assembly machinist requires knowledge of engineering principles, along with the ability to read blueprints and use specialized tools such as calipers, micrometers, and thread gauges. Quality control measures, safety protocols, and regular maintenance of equipment are also essential for successful assembly operations.
Steps How to Become
- Obtain a high school diploma or equivalent. Many employers prefer to hire machinists who have a high school diploma or equivalent, such as a GED.
- Enroll in a machining program at a technical school or community college. Machinists must have a thorough knowledge of mathematics, physics, and computer programming.
- Gain experience with machine tools and learn the basics of machining processes. This can be done through on-the-job training or by taking courses in machining at a technical school or community college.
- Obtain a license or certificate for assembly machining. Most states require machinists to be licensed or certified before they can work with certain types of machinery.
- Work as an apprentice or helper under the guidance of an experienced assembly machinist. During this time, the apprentice will gain valuable experience that will help him or her advance in the assembly machining field.
- Become knowledgeable in all aspects of assembly machining, including blueprints, shop drawings, and safety procedures. This can be done through on-the-job training, attending seminars, and reading textbooks.
- Obtain certification from a trade organization or professional association in assembly machining. This certification is not required to work as an assembly machinist, but it will demonstrate to potential employers that the applicant has the necessary knowledge and skills.
Being a skilled and competent machinist requires dedication and hard work. To become an expert machinist, one must have a deep understanding of the workings of different machines, be familiar with the tools used to work on them, and have experience in assembling and operating the machinery. it is essential to understand the various safety protocols and regulations associated with the profession, as well as possessing strong problem solving skills to be able to effectively troubleshoot any issues that may arise.
Furthermore, it is important to be knowledgeable in mathematics to be able to calculate angles and distances accurately, as well as have the physical strength and dexterity to operate machinery for long periods of time. With continued practice and training, an individual can become a skilled and competent machinist.
You may want to check Tool and Die Machinist, Machine Operator (Machinist), and Computer Numerical Control (CNC) Machinist for alternative.
Job Description
- Read and interpret blueprints, sketches, and specifications to determine job instructions and requirements.
- Set up and adjust machine tools, including cutting and grinding machines, to perform precision operations.
- Examine parts for surface defects and measure parts to determine accuracy of machine operation.
- Load parts in machine, cycle machine, detect malfunctions in machine operations, and adjust machine settings as necessary to ensure quality of production.
- Monitor and verify quality in accordance with statistical process or other control procedures.
- Dismantle machines and make repairs as needed, using hand tools and measuring devices.
- Maintain records of production output and operational data to ensure quality control.
- Install and program new machines, as well as maintain existing machines, ensuring that they are in proper condition.
- Perform routine maintenance on machines, including oiling and cleaning.
- Consult technical handbooks and other sources of information to assist with problem solving and troubleshooting.
Skills and Competencies to Have
- Knowledge of precision measuring tools and techniques
- Ability to read and understand blueprints
- Expertise in basic machining methods and operations
- Ability to set up and operate various types of machinery
- Proficiency in using manual and computer numeric control (CNC) machines
- Knowledge of computer-aided design (CAD) and computer-aided manufacturing (CAM) software
- Ability to use hand tools, such as drill presses and lathes
- Excellent problem-solving and troubleshooting skills
- Ability to work with a variety of metals and other materials
- Detail-oriented with an eye for accuracy and precision
- Ability to work independently and in a team environment
- Ability to work quickly and accurately in a fast-paced environment
Having the right skills as a Machinist is crucial to the success of any manufacturing operation. The primary skill required to be an effective Machinist is the ability to accurately read and interpret technical drawings and instructions. This allows the Machinist to create precise parts and assemblies according to the specified design.
In addition, a good Machinist must possess exceptional attention to detail and an in-depth knowledge of mechanical principles and mathematics. The Machinist must also have a high level of technical understanding, be able to troubleshoot and solve complex problems, and have the ability to operate a variety of precision equipment. An effective Machinist must also have strong problem-solving skills, be able to work independently, and be able to communicate effectively with other members of the team.
These skills are essential for a Machinist to be successful in their role and ensure that all parts and assemblies produced meet the specified requirements.
Welding Machinist, Prototype Machinist, and Die Cast Machinist are related jobs you may like.
Frequent Interview Questions
- What experience do you have in assembly machining?
- How would you troubleshoot a machine that isnt functioning properly?
- Describe a time you had to make a modification to a machine to improve its efficiency.
- What safety protocols do you follow when working with assembly machines?
- What challenges have you faced while working with assembly machines?
- How do you ensure accuracy when assembling parts?
- What processes do you use to inspect parts before and after assembly?
- What tools and techniques do you use to measure components during assembly?
- How do you ensure that all parts are correctly positioned during assembly?
- What challenges have you experienced in communicating with colleagues about assembly issues?
Common Tools in Industry
- Lathe Machine. A machine tool that rotates a workpiece on its axis to perform various operations such as cutting, sanding, knurling, drilling, or deformation. (eg: CNC Lathe)
- Milling Machine. A machine tool used to machine solid materials such as metal and wood. It utilizes a rotating cutter to remove material from a workpiece. (eg: CNC Milling Machine)
- Drill Press. A machine tool used to create holes in materials such as metal and wood. It uses a rotating cutting tool to create holes of varying sizes and depths. (eg: Radial Arm Drill Press)
- Grinder. A machine tool used to sharpen, buff, or grind materials such as metal and wood. It utilizes an abrasive wheel to refine the material's surface. (eg: Bench Grinder)
- Tap and Die Set. A set of tools used to cut internal and external threads on objects such as bolts and pipes. It allows users to create threads of various sizes and depths. (eg: Adjustable Tap and Die Set)
- Bandsaw. A machine tool used to cut curves and circles in materials such as metal and wood. It utilizes a long, continuous band of metal with a toothed edge to cut the material. (eg: Vertical Bandsaw)
- Sheet Metal Shear. A machine tool used to cut sheet metal into desired shapes and sizes. It utilizes two blades that move in opposite directions to cut the material. (eg: Hydraulic Sheet Metal Shear)
- Threading Machine. A machine tool used to create threads on objects such as bolts and pipes. It utilizes a rotating cutting tool to create helical grooves in the material's surface. (eg: CNC Threading Machine)
Professional Organizations to Know
- National Association of Manufacturers (NAM)
- The Precision Machined Products Association (PMPA)
- International Association of Machinists and Aerospace Workers (IAMAW)
- Association for Manufacturing Technology (AMT)
- Society of Manufacturing Engineers (SME)
- Fabricators & Manufacturers Association, International (FMA)
- American Machine Tool Distributors Association (AMTDA)
- National Institute for Metalworking Skills (NIMS)
- American National Standards Institute (ANSI)
- National Tooling & Machining Association (NTMA)
We also have Laser Machinist, CNC Machinist, and Mold Maker Machinist jobs reports.
Common Important Terms
- CNC Machining. A machining process that uses computer numerical control (CNC) technology to automate and control the movements of a machine tool.
- Drilling. A machining process in which holes are created in a workpiece by rotating a drill bit.
- Turning. A machining process in which a cutting tool is used to remove material from the surface of a workpiece in the form of a rotating motion.
- Milling. A machining process in which a cutting tool is used to remove material from the surface of a workpiece in the form of a linear motion.
- Grinding. A machining process in which an abrasive wheel is used to remove material from the surface of a workpiece.
- Tapping. A machining process in which threading is created in a workpiece by using a tap.
- EDM or Electrical Discharge Machining. A machining process that utilizes electrical sparks to remove material from the surface of a workpiece.
- Heat Treating. A process in which metal is heated and cooled in order to alter its properties and/or structure.
Frequently Asked Questions
What qualifications are needed to become an Assembly Machinist?
To become an Assembly Machinist, one must have a high school diploma or GED, as well as experience with machine tools and necessary technical knowledge.
What tasks does an Assembly Machinist typically perform?
An Assembly Machinist typically performs tasks such as setting up and operating machines to fabricate parts, assembling components, testing and inspecting parts, and troubleshooting and repairing any defects.
What tools and equipment does an Assembly Machinist typically use?
An Assembly Machinist typically uses tools and equipment such as drill presses, lathes, milling machines, grinders, and other machine tools to fabricate parts.
What safety measures must an Assembly Machinist take?
An Assembly Machinist must follow workplace safety protocols such as wearing protective clothing and equipment, properly securing tools and materials, and adhering to any applicable safety regulations.
What is the average salary of an Assembly Machinist?
According to the U.S. Bureau of Labor Statistics, the median salary for an Assembly Machinist is $38,890 per year.
What are jobs related with Assembly Machinist?
- Quality Control Machinist
- Mill Machinist
- Lathe Machinist
- Production Machinist
- Manual Machinist
- Grinder Machinist
- Fabrication Machinist
Web Resources
- Automotive Machinist Technology Program - Hinds Community ¦ www.hindscc.edu
- Machinist The Apprentice School The Apprentice School www.as.edu
- Machinist | Monroe County Community College www.monroeccc.edu
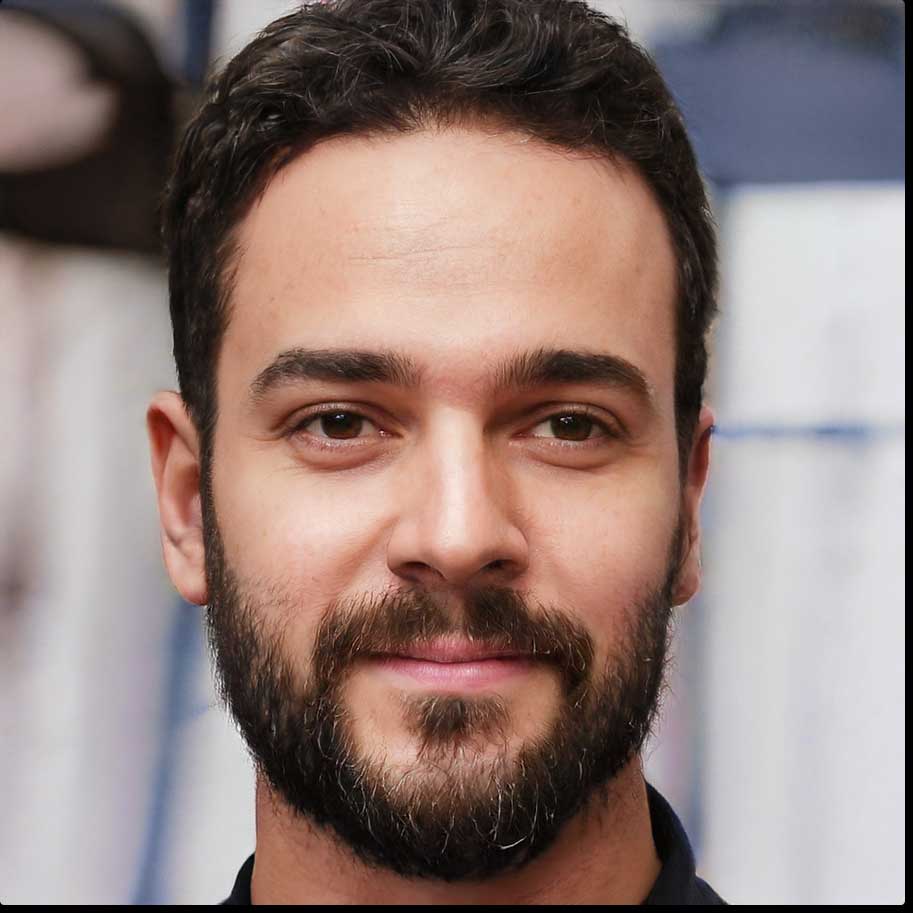