How to Be Mill Machinist - Job Description, Skills, and Interview Questions
The use of mill machines in the manufacturing industry is essential to precision and accuracy. This is because the machines are able to precisely cut, shape, and drill materials with a high degree of accuracy, which is often required for complex projects. the machines can reduce waste by cutting and shaping materials to exact specifications.
As a result, the expertise of a mill machinist is paramount for the success of a project, as they are responsible for programming and operating the machines. The machinists must possess a combination of mechanical aptitude and technical skills to successfully create products. Furthermore, communication between the machinist and the customer is essential to ensure accuracy and quality.
Therefore, the role of a mill machinist is essential for successful production in the manufacturing industry.
Steps How to Become
- Obtain a High School Diploma or GED. Mill machinists typically need a high school diploma or its equivalent, the General Education Development (GED), to qualify for an apprenticeship or even entry-level work.
- Take Math, Computer and Science Classes. During the high school years, potential mill machinists should take courses in math, computer science, physics and other related sciences. These courses will help prepare students to understand the complexities of milling machines and industrial materials.
- Apply for an Apprenticeship. Apprenticeships provide workers with hands-on experience and training in a milling environment. Apprentices often receive both classroom instruction and on-the-job training from experienced machinists. Apprentices may work for two to four years before they become certified mill machinists.
- Obtain Certification. Some states and employers require mill machinists to become certified. To become certified, mill machinists must demonstrate their skills in areas such as safety, operating procedures and machine setup. Certification is typically obtained through trade schools or industry organizations.
- Gain Experience. The best way for mill machinists to gain the experience necessary for advanced positions is to stay with the same employer for several years and to take advantage of any training or educational opportunities offered by the employer.
The key to staying updated and efficient as a mill machinist is to stay up-to-date on industry trends, maintain a solid understanding of the latest technologies and best practices, and develop a strong foundation of knowledge on machining operations and procedures. Keeping up with industry trends helps a machinist stay current on the latest technological advancements, understand new products, and learn about new ways to improve their work. Developing a strong knowledge base of machining operations and procedures enables a machinist to make more informed decisions and increase productivity.
investing in quality machinery and tools is an important factor in being efficient and staying competitive. Investing in high-quality tools and machinery reduces the risk of breakage and costly repairs, increases the quality of work, and improves safety. Finally, staying organized and having a system for tracking and keeping records of work is essential for success in the field.
Keeping organized records of work and progress helps to cut down on time spent searching for data, increases accuracy and efficiency, and allows machinists to track their progress over time.
You may want to check Assembly Machinist, Laser Machinist, and Grinder Machinist for alternative.
Job Description
- Set up and operate a variety of machine tools to produce precision parts and instruments.
- Calculate dimensions, tolerances, and feed rates.
- Read blueprints, sketches, drawings, manuals, specifications, or sample part to determine dimensions and tolerances of finished work piece, sequence of operations, and setup requirements.
- Measure, examine, and test completed work pieces to ensure conformance to specifications, using precision instruments such as micrometers and gauge blocks.
- Sharpen dull cutting tools or adjust tools to compensate for wear.
- Set up and operate conventional or computer-controlled machines to perform routine and complex machining operations, such as drilling, reaming, tapping, milling, boring, and grinding of parts to close tolerances.
- Fit and assemble parts into complete assembly using hand tools and power tools.
- Monitor the feed and speed of machines during the machining process.
- Detect and troubleshoot irregularities and malfunctions of machines during operation to determine necessary repairs or adjustments.
- Inspect work pieces for conformance to specifications.
- Maintain records of approved and defective parts or materials.
- Perform routine maintenance on machines such as lubricating parts.
Skills and Competencies to Have
- Knowledge of basic machining principles, including metal and plastic properties, cutting tools and tool geometry
- Ability to read and interpret engineering drawings, sketches, blueprints and specifications
- Ability to set-up and operate conventional and CNC mills, lathes, drill presses and other related machine tools
- Ability to perform basic mathematical calculations
- Proficiency in making precision measurements with calipers, micrometers and other measuring instruments
- Knowledge of shop safety protocols and procedures
- Ability to work with a minimum of supervision
- Knowledge of shop mathematics and trigonometry
- Ability to troubleshoot machinery and make necessary repairs and adjustments
- Ability to maintain accurate records and prepare reports
- Knowledge of material selection and heat treatment procedures
- Ability to use CAD/CAM software
The ability to use precision measuring tools and read complex blueprints accurately is an essential skill for any machinist. Without this basic knowledge, machinists will not be able to create parts with the required accuracy, causing problems downstream in the production process. If machinists lack the ability to read blueprints, they will not be able to properly understand the specifications of the part they are creating, leading to the production of an incorrect part.
Furthermore, if a machinist lacks the ability to use precision measuring tools, they will not be able to ensure the part they are making is within the specified tolerances, which can lead to costly delays in the production process and may even result in the part having to be redone, causing a significant financial loss. Therefore, having a good understanding of precision measuring tools and the ability to read blueprints accurately is essential for machinists in order to create high-quality parts efficiently and cost-effectively.
Quality Control Machinist, CNC Machinist, and Manual Machinist are related jobs you may like.
Frequent Interview Questions
- What experience do you have working with mill machines?
- What safety protocols do you follow when working with mill machines?
- How do you troubleshoot mill machines when they malfunction?
- Describe a time when you had to modify a mill machine for a specific job.
- How do you ensure that the milling operations are accurate and precise?
- What have you done to stay up-to-date on the latest milling technology?
- Do you have experience using CAD software to design and create parts for mill machines?
- How do you approach the job of measuring and cutting materials for milling operations?
- What techniques do you use to optimize production output on mill machines?
- How do you inspect the parts produced by mill machines to ensure quality?
Common Tools in Industry
- Lathe. A machine tool used to shape metal or wood by rotating the material against a cutting tool. (e. g. a lathe can be used to create cylindrical parts from a solid block of material).
- Milling Machine. A machine tool used for the precision machining of metal parts. (e. g. a milling machine can be used to create complex shapes and holes in a piece of metal).
- Drill Press. A machine tool used to make holes in a workpiece by rotating a cutting tool against it. (e. g. a drill press can be used to create holes for bolts or screws).
- Grinder. A machine tool used to sharpen cutting tools or remove material from a workpiece. (e. g. a grinder can be used to sharpen drill bits or grind down a surface).
- Saw. A machine tool used to make straight or curved cuts in a workpiece by using a cutting blade. (e. g. a saw can be used to cut through metal, wood, or other materials).
- Band Saw. A machine tool used to make straight or curved cuts in a workpiece by using a continuous loop of cutting blades. (e. g. a band saw can be used to make curved cuts in a workpiece).
- CNC Machine. A computer-controlled machine tool used for the automation of manufacturing processes. (e. g. a CNC machine can be used to precisely cut and shape metal components with highly accurate dimensions).
Professional Organizations to Know
- American Machine Tool Distributors Association (AMTDA)
- National Institute for Metalworking Skills (NIMS)
- Society of Manufacturing Engineers (SME)
- CNC Machinists Association
- International Association of Machinists & Aerospace Workers (IAMAW)
- The Manufacturing Institute
- National Tooling & Machining Association (NTMA)
- Association for Manufacturing Technology (AMT)
- The Manufacturing Institute
- The Fabricators & Manufacturers Association, International (FMA)
We also have Machine Operator (Machinist), Die Cast Machinist, and Computer Numerical Control (CNC) Machinist jobs reports.
Common Important Terms
- CNC Machining. The process of using computer numerical control (CNC) machines to cut, shape and form components from raw materials.
- Lathe Operator. A machinist who operates a lathe machine to shape metal or other materials into desired shapes.
- Milling Machine Operator. A machinist who operates a milling machine to cut and shape metal or other materials.
- Drilling Machine Operator. A machinist who operates a drilling machine to create holes in metal or other materials.
- Grinder Operator. A machinist who operates a grinding machine to sharpen, polish or grind metal or other materials.
- Tool and Die Maker. A machinist who designs, creates and maintains molds, dies, and fixtures used in industrial production processes.
- EDM Operator. A machinist who operates an electrical discharge machining (EDM) machine to cut, shape and form components from raw materials.
- CAD/CAM Operator. A machinist who operates computer-aided design (CAD) and computer-aided manufacturing (CAM) software to design and create components from raw materials.
Frequently Asked Questions
What skill sets are needed to be a Mill Machinist?
Mill Machinists need to be proficient in the use of various tools, such as lathes, milling machines, drill presses, grinders and other precision measuring instruments. They should also have a working knowledge of mathematics, geometry and technical drawing.
What kind of jobs does a Mill Machinist typically perform?
Mill Machinists typically perform a variety of tasks such as machining parts from metal, plastic or other materials, creating custom parts from drawings and specifications, and setting up and operating machines.
How much do Mill Machinists typically earn?
The median annual wage for Mill Machinists is $45,050, according to the U.S. Bureau of Labor Statistics.
What qualifications are needed to become a Mill Machinist?
To become a Mill Machinist, individuals typically need to complete a certificate or associate degree program in machining or a related field.
What safety protocols are used by Mill Machinists?
Mill Machinists must adhere to safety protocols such as wearing protective clothing and equipment, following machine safety procedures and using proper lifting techniques.
What are jobs related with Mill Machinist?
- Lathe Machinist
- Welding Machinist
- Maintenance Machinist
- Prototype Machinist
- Tool and Die Machinist
- Fabrication Machinist
- Production Machinist
Web Resources
- What Is a CNC Mill Machinist? | UTI www.uti.edu
- CNC mill machinist | Institute for Transportation intrans.iastate.edu
- Machinist - BatesTech - BatesTech www.batestech.edu
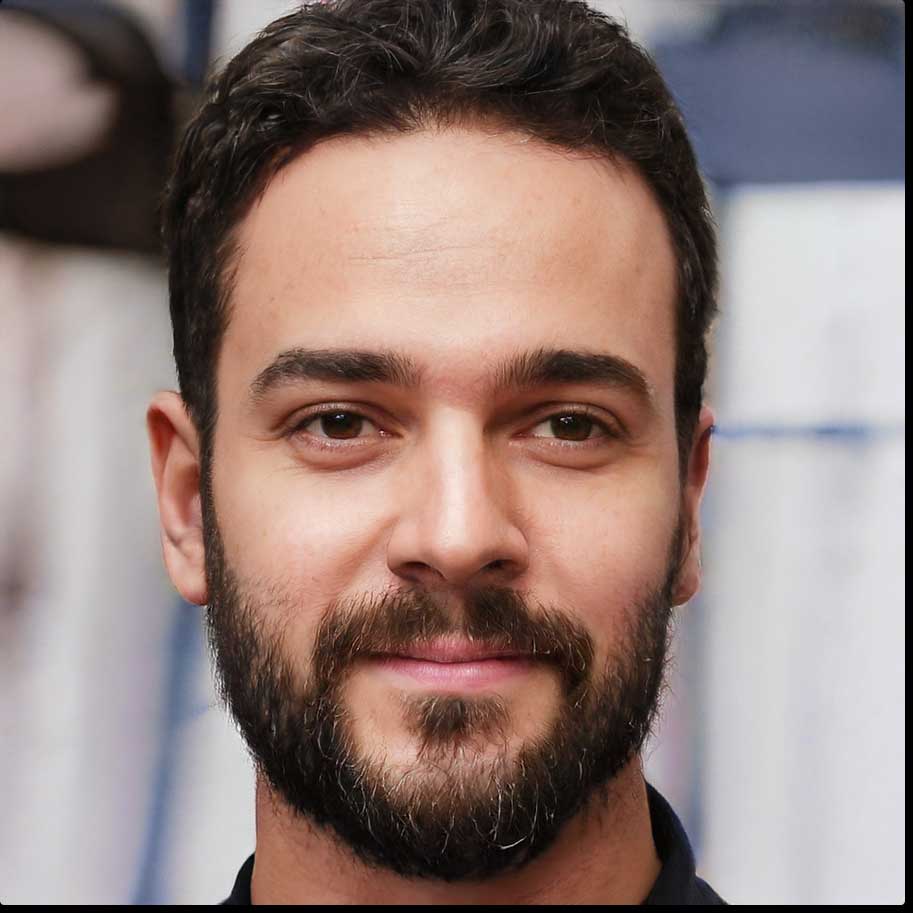