How to Be Machine Operator (Machinist) - Job Description, Skills, and Interview Questions
Operator (Machinist) plays an integral role in the manufacturing industry. They are responsible for ensuring that machines are operating correctly and efficiently. The success of a machine operator depends on their ability to accurately and quickly set up and operate machines, as well as their ability to troubleshoot any issues that may arise.
Poor machine operation can lead to missed deadlines or inferior products, which can result in lost profits for the company. On the other hand, correctly setting up and operating machines can lead to increased production output and higher quality products, resulting in higher customer satisfaction, greater market share and improved profitability. Machine operators must be knowledgeable in the machines they are operating, understand how to make any necessary adjustments, and be able to make quick decisions when a problem arises.
Steps How to Become
- Obtain a High School Diploma or GED. Obtaining a high school diploma or GED is the first step in becoming a machinist. This will provide the basic foundation of knowledge and skills needed for the job.
- Complete a Vocational Training Program. There are a variety of vocational programs available to help prepare individuals for a career as a machinist. These programs typically include instruction in mathematics, blueprint reading, computer-aided design (CAD) software, and hands-on training in operating various machinery.
- Gain Work Experience. Many employers prefer to hire experienced machinists, so gaining some work experience can be helpful when applying for jobs. Apprenticeships, internships, and other entry-level positions are all good ways to gain experience in this field.
- Earn Professional Certification. Professional certification is not required to become a machinist, but it can be beneficial for career advancement. The National Institute for Metalworking Skills (NIMS) offers certifications in several different areas of machining, including CNC programming, manual machining, and quality assurance.
- Get Licensed. Some states require machinists to be licensed in order to work in the field. Requirements vary by state, but typically involve passing an exam that tests knowledge and skills related to operating machinery.
Staying ahead and capable as a machine operator (machinist) requires dedication to learning and staying up to date with the latest technological advancements in the field. The best way to stay ahead is to invest in ongoing education and training. This could include attending conferences and seminars, taking courses, and participating in workshops.
acquiring certifications in related areas like automation, computer-aided design, and machining processes will ensure that the machine operator is knowledgeable of the current technologies and can apply them to the job. Keeping up with industry trends and news is also important as it will help the machine operator stay ahead of the competition. Finally, investing in the best tools and equipment available is key to staying competitive and capable in this field.
Doing so will ensure that the machine operator is able to create high-quality products and be productive throughout the job process.
You may want to check Laser Machinist, Fabrication Machinist, and Mold Maker Machinist for alternative.
Job Description
- Set up, operate, and maintain various machines, such as lathes, milling machines, drill presses, grinders, and other metalworking equipment to produce precision metal parts and components.
- Read and interpret blueprints, sketches, or technical drawings to determine the specific machining operations to be performed.
- Measure materials or workpieces to determine dimensions and ensure conformance to specifications using precision measuring instruments.
- Calculate and set controls to regulate machining factors such as speed, feed, coolant flow, and depth and angle of cut.
- Lift and position workpieces on machines, using hoists, cranes and other lifting equipment.
- Monitor machine operations to detect any problems or defects.
- Perform minor maintenance or cleaning activities on machines.
- Replace worn or broken cutting tools or adjust cutting tools to specified settings.
- Maintain accurate records of tooling and materials used in the machining processes.
- Follow all safety protocols and procedures related to the operation of machines.
Skills and Competencies to Have
- Knowledge of safety protocols and procedures
- Ability to read and interpret blueprints and drawings
- Ability to make mathematical calculations
- Proficiency in the operation of machine tools
- Knowledge of tooling, cutting speeds, and feed rates
- Ability to use various measuring instruments (micrometers, calipers, etc. )
- Ability to interpret a variety of instructions furnished in written, oral, diagram or schedule form
- Proficiency in operating CNC machines
- Knowledge of manual lathes, milling machines, and drills
- Ability to troubleshoot and identify defects in parts
- Ability to recognize and correct machine malfunctions
- Ability to perform setup operations
- Knowledge of basic shop mathematics
- Knowledge of quality standards and procedures
- Ability to maintain accurate records and logs
Operating a machine in a machinist role requires a great deal of skill and knowledge. The most important skill for a machine operator to possess is attention to detail. This is because small errors can have a big impact on the quality of the product.
Attention to detail ensures that the machine is set up correctly and operated safely for maximum efficiency. a machine operator must have a basic understanding of mechanical and electrical engineering principles in order to troubleshoot any issues that may arise. Furthermore, it is important for the machine operator to have good hand-eye coordination and manual dexterity in order to make precise and accurate movements when operating the machine.
Finally, a good working knowledge of mathematics is essential to help calculate and measure the dimensions of the parts being produced. All of these skills are necessary in order for a machine operator to be successful in the role.
Production Machinist, Welding Machinist, and Computer Numerical Control (CNC) Machinist are related jobs you may like.
Frequent Interview Questions
- What experience do you have operating machines?
- Describe a time when you had to troubleshoot a machine issue.
- How would you handle a situation where you weren't comfortable operating a particular machine?
- How would you handle a situation where a machine was producing inaccurate results?
- Tell me about your experience with safety protocols related to machine operation.
- Are you familiar with the industry's standards and regulations for operating machines?
- Have you ever had to make adjustments to a machine's settings to ensure quality results?
- What steps do you take to ensure a machine is functioning correctly before beginning a job?
- Are you able to read and interpret engineering drawings and schematics?
- What strategies do you use to stay organized and productive while operating machines?
Common Tools in Industry
- Lathe. A machine tool that rotates a workpiece on its axis to perform various operations such as cutting, sanding, knurling, drilling, or deformation with tools that are applied to the workpiece to create an object with symmetry about an axis of rotation. (eg: CNC lathe)
- Milling Machine. A machine tool used to machine solid materials. It is capable of cutting and shaping a variety of materials including metal, wood, plastic, and composite materials. (eg: CNC milling machine)
- Drill Press. A machine tool used to drill holes in various materials. It consists of a base, column, spindle, chuck, and drill head. (eg: benchtop drill press)
- Band Saw. A type of saw in which a continuous band of toothed metal passes around two or more wheels to cut material. (eg: vertical band saw)
- Grinder. A machine tool used for grinding, which is a type of machining using an abrasive wheel as the cutting tool. (eg: bench grinder)
- Shaper. A machine tool used for shaping metal or other material by means of a single-point cutting tool. (eg: horizontal shaper)
Professional Organizations to Know
- Society of Manufacturing Engineers (SME)
- National Institute for Metalworking Skills (NIMS)
- Fabricators & Manufacturers Association (FMA)
- The American Machine Tool Distributors Association (AMTDA)
- The Association for Manufacturing Technology (AMT)
- National Tooling and Machining Association (NTMA)
- American Precision Machinists Union (APMU)
- International Association of Machinists and Aerospace Workers (IAMAW)
- The American Foundry Society (AFS)
- National Association of Manufacturers (NAM)
We also have Assembly Machinist, Lathe Machinist, and Die Cast Machinist jobs reports.
Common Important Terms
- Lathe Operator. An individual who uses a lathe machine to shape and form metal or other materials.
- CNC Operator. An individual who operates a computer numerical control (CNC) machine, which is a computer-controlled machine tool used to cut and shape metal or other materials.
- Drill Press Operator. An individual who uses a drill press machine to drill holes in metal or other materials.
- Milling Machine Operator. An individual who operates a milling machine, which is a machine tool used to shape and form metal or other materials.
- Grinder Operator. An individual who uses a grinding machine to shape and finish metal or other materials.
- Metal Fabricator. An individual who fabricates metal objects from raw materials using various tools and machines, such as welding, cutting, and bending.
- Quality Control Technician. An individual who checks products for quality and accuracy according to established standards.
- Tool and Die Maker. An individual who designs and manufactures molds, jigs, fixtures, dies, and other parts used in the machining process.
Frequently Asked Questions
What is a Machinist?
A Machinist is a skilled tradesperson who operates machine tools to manufacture parts, components and/or tools from metal, plastic, or other materials.
What skills are needed to be a Machinist?
To be a successful Machinist, one must have excellent manual dexterity and physical strength, as well as strong knowledge of mathematics, physics, and engineering principles. They must also have the ability to read blueprints and understand the use of precision measuring instruments.
What types of machines do Machinists operate?
Machinists typically operate lathes, milling machines, drill presses, grinders, saws and other metalworking machines.
How long does it take to become a Machinist?
It typically takes 2-4 years to become a qualified Machinist, depending on the individual's experience and commitment.
What is the median salary for a Machinist?
According to the Bureau of Labor Statistics, the median salary for a Machinist in May 2019 was $43,640 per year.
What are jobs related with Machine Operator (Machinist)?
- Quality Control Machinist
- Tool and Die Machinist
- Manual Machinist
- Maintenance Machinist
- Grinder Machinist
- CNC Machinist
- Prototype Machinist
Web Resources
- Machine Operator Certificate | Right Skills Now for Manufacturing www.saintpaul.edu
- Certified Machine Operator | Tulsa Technology Center tulsatech.edu
- Machine Tool Operator - Technical Diploma | CVTC www.cvtc.edu
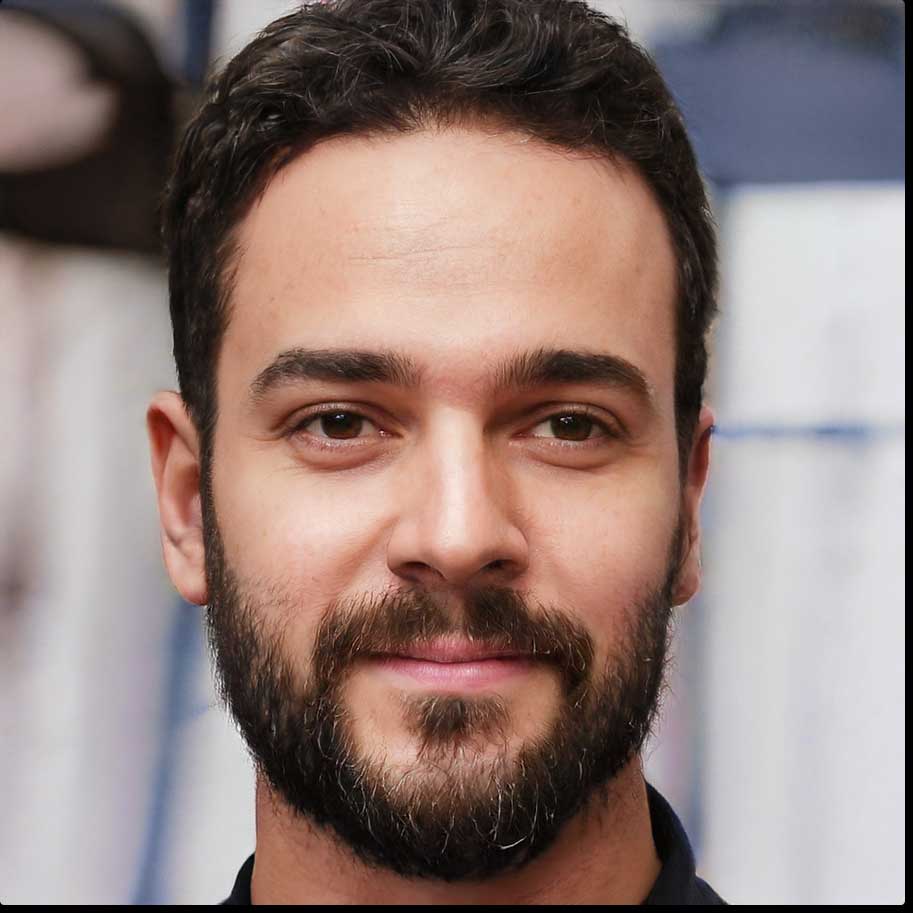