How to Be Manual Machinist - Job Description, Skills, and Interview Questions
Manual machinists are highly sought after in the manufacturing industry due to their ability to produce precision parts with milling machines, lathes, and other manual tools. This skill requires a combination of technical knowledge, physical ability, and a keen eye for detail. As a result, manual machinists can create parts with tight tolerances and precise dimensions, which is essential for many different industries.
the manual machinistâs job often involves troubleshooting, problem solving, and working with other professionals and machines to meet project deadlines. By having these abilities, manual machinists play an important role in the manufacturing process, helping to create high-quality parts that are essential for the production of products that are reliable and safe for consumers.
Steps How to Become
- Research the trade. Researching manual machinist roles and the job requirements can help you decide if this career path is right for you. Learn about the duties, education requirements, and salary expectations to see if it matches your goals.
- Take a machinist class. Taking a machinist class is a great way to get a head start in the field. Many community colleges offer courses that teach the basics of manual machining and provide hands-on experience with the essential tools and machines.
- Seek an apprenticeship. Apprenticeships are a great way to gain hands-on experience in the field and learn from experienced professionals. Apprenticeships usually require applicants to have at least a high school diploma and some basic knowledge of the trade.
- Get certified. Once you have completed an apprenticeship, it may be beneficial to get certified as a manual machinist from a professional organization such as the National Institute for Metalworking Skills (NIMS). This certification can help you stand out to potential employers.
- Consider additional training. Manual machinists must constantly stay up to date on new technologies and techniques, so its important to consider additional training opportunities. Seminars, workshops, and online courses can help you stay ahead of the competition.
Manual machinists must continually stay up to date with the latest developments in their field in order to remain qualified. This requires researching and understanding new technologies, materials, and methods, as well as training in the use of newer equipment. Keeping up with the current trends in the industry can help manual machinists stay competitive in the job market and ensure that they are providing the highest quality service to their customers.
In addition, staying current on safety requirements and regulations can help to protect both the machinist and those working around them from potential harm. Finally, by keeping up with the latest advancements in machining technology, manual machinists can increase their efficiency and accuracy while reducing the time it takes to complete projects. The combination of all these factors can result in a more successful career for manual machinists.
You may want to check Grinder Machinist, Die Cast Machinist, and CNC Machinist for alternative.
Job Description
- Set up and operate a variety of manual and computer numerically controlled machine tools to produce precision parts and instruments.
- Read and interpret blueprints, sketches, drawings, manuals, specifications, or sample parts to determine dimensions and tolerances of finished work pieces, sequence of operations, and setup requirements.
- Measure, mark, and scribe dimensions and reference points on material or work pieces as guides for subsequent machining.
- Calculate and set controls to regulate machining factors such as speed, feed, coolant flow, depth and angle of cut, or enter commands to retrieve, input, or edit computerized machine control media.
- Select, align, and secure holding fixtures, cutting tools, attachments, accessories, and materials on machines such as mills, lathes, jig borers, grinders, and shapers.
- Start and observe machine operation to detect malfunctions or out-of-tolerance machining, and adjust machine controls or control media as required.
- Monitor the feed and speed of machines during the machining process.
- Fit and assemble parts into complete assembly using hand tools and power tools.
- Verify dimensions of products for accuracy using measuring instruments such as calipers, micrometers and dial indicators.
- Maintain records such as time studies and production records.
Skills and Competencies to Have
- Knowledge and understanding of machine tools and how to use them.
- Ability to read and interpret blueprints, drawings, and schematics.
- Ability to perform basic math calculations and use measuring instruments.
- Familiarity with manual and computer-controlled machining processes.
- Skill in using power tools such as lathes, milling machines, drill presses, and grinders.
- Ability to troubleshoot and diagnose problems with machines and parts.
- Strong mechanical aptitude and problem-solving skills.
- Ability to work independently and as part of a team.
- Attention to detail and a commitment to accuracy in all work performed.
- Good communication skills and the ability to follow directions.
Manual machinists are highly skilled tradespeople responsible for operating and maintaining manual machines. This requires a great deal of knowledge and skill, but the most important skill for a manual machinist is the ability to think critically and solve problems. Manual machinists must be able to read and interpret blueprints, understand machine functions, and troubleshoot any issues that arise.
manual machinists must have a solid understanding of mathematics and be able to perform calculations quickly and accurately. With these skills, manual machinists are able to create high-quality parts, often with tight tolerances. As a result, they are essential for the manufacturing industry, helping to ensure that products are produced to exact specifications.
Without manual machinists, manufacturers would find it difficult to maintain production levels, which would have a ripple effect on other industries.
Mold Maker Machinist, Mill Machinist, and Welding Machinist are related jobs you may like.
Frequent Interview Questions
- What experience do you have operating manual machining equipment?
- How do you ensure the accuracy of the work you produce?
- What safety measures do you take when operating manual machining equipment?
- What challenges have you faced while operating manual machining equipment?
- How do you troubleshoot any issues that arise while operating manual machining equipment?
- Describe a time where you had to adjust the design of a part due to the limitations of the manual machining equipment.
- How do you maintain your manual machining tools?
- What strategies do you use to reduce cycle times when running manual machining jobs?
- What methods do you use to ensure that the parts you produce meet quality standards?
- How do you keep up with changes in technology related to manual machining processes?
Common Tools in Industry
- Drill Press. A machine tool that uses a drill bit to cut holes into material. (eg: A drill press is used to make precise holes in metal).
- Lathe. A machine tool that rotates a workpiece against a cutting tool to shape it. (eg: A lathe is used to turn round pieces of metal into cylindrical shapes).
- Milling Machine. A machine tool that uses a rotating cutter to shape or form material. (eg: A milling machine is used to create complex shapes and parts out of metal).
- Grinder. A machine tool that uses an abrasive wheel to grind and shape material. (eg: A grinder is used to smooth rough surfaces on metal pieces).
- Band Saw. A saw with a long, continuous blade that is used for cutting curved or irregular shapes. (eg: A band saw is used to cut intricate shapes out of metal).
- Shaper. A machine tool that uses a reciprocating ram and cutting tool to produce flat or contoured surfaces. (eg: A shaper is used to create intricate parts from metal).
Professional Organizations to Know
- American Association of Machinists and Aerospace Workers (AAMAW)
- Society of Manufacturing Engineers (SME)
- National Institute for Metalworking Skills (NIMS)
- Precision Machinists Association (PMA)
- National Tooling and Machining Association (NTMA)
- National Association of Metalworking Machinists and Machinery Manufacturers (NAMM)
- International Association of Machinists and Aerospace Workers (IAMAW)
- American Society of Mechanical Engineers (ASME)
- American Machine Tool Distributors' Association (AMTDA)
- Tooling and Manufacturing Association (TMA)
We also have Lathe Machinist, Prototype Machinist, and Machine Operator (Machinist) jobs reports.
Common Important Terms
- Lathe. A machine tool used for shaping metal or wood parts by rotating the workpiece on its axis against a cutting tool.
- Milling Machine. A machine tool used for machining solid materials, usually metals, with a rotating cutter.
- Drilling Machine. A machine tool used for drilling holes in materials, usually metals.
- Grinding Machine. A machine tool used for grinding materials, usually metals, using an abrasive wheel as the cutting tool.
- Turning. The process of cutting or shaping metal or wood parts by rotating the workpiece on its axis against a cutting tool.
- Boring. The process of enlarging or increasing the diameter of a hole in a workpiece, usually done with a boring bar.
- Tapping. The process of cutting threads into a hole by using a tap and die set.
- Facing. The process of creating flat surfaces on a workpiece by removing material from it, usually done with a facing tool.
- Reaming. The process of enlarging or finishing an existing hole in a workpiece, usually done with a reamer.
- Chiseling. The process of creating or shaping grooves, recesses, or channels in a workpiece by using a chisel.
Frequently Asked Questions
What is a Manual Machinist?
A Manual Machinist is a skilled tradesperson responsible for operating manual machine tools to produce precision parts.
What types of machines does a Manual Machinist typically use?
A Manual Machinist typically uses manual lathes, milling machines, and drill presses to produce parts.
What skills are needed to be a successful Manual Machinist?
To be a successful Manual Machinist, one must have technical knowledge, manual dexterity, and problem solving skills.
What materials do Manual Machinists typically work with?
Manual Machinists typically work with a variety of materials including metals, plastics, and composites.
What are common measurements used by Manual Machinists?
Common measurements used by Manual Machinists include inches, millimeters, angles, and tolerances.
What are jobs related with Manual Machinist?
- Tool and Die Machinist
- Computer Numerical Control (CNC) Machinist
- Maintenance Machinist
- Production Machinist
- Assembly Machinist
- Quality Control Machinist
- Fabrication Machinist
Web Resources
- Online Manual Machinist from Arkansas State University ed2go.degree.astate.edu
- Manual Machinist - Tallahassee Community College - fl.edu fl.edu
- Manual Machinist - Tallahassee Community College www.tcc.fl.edu
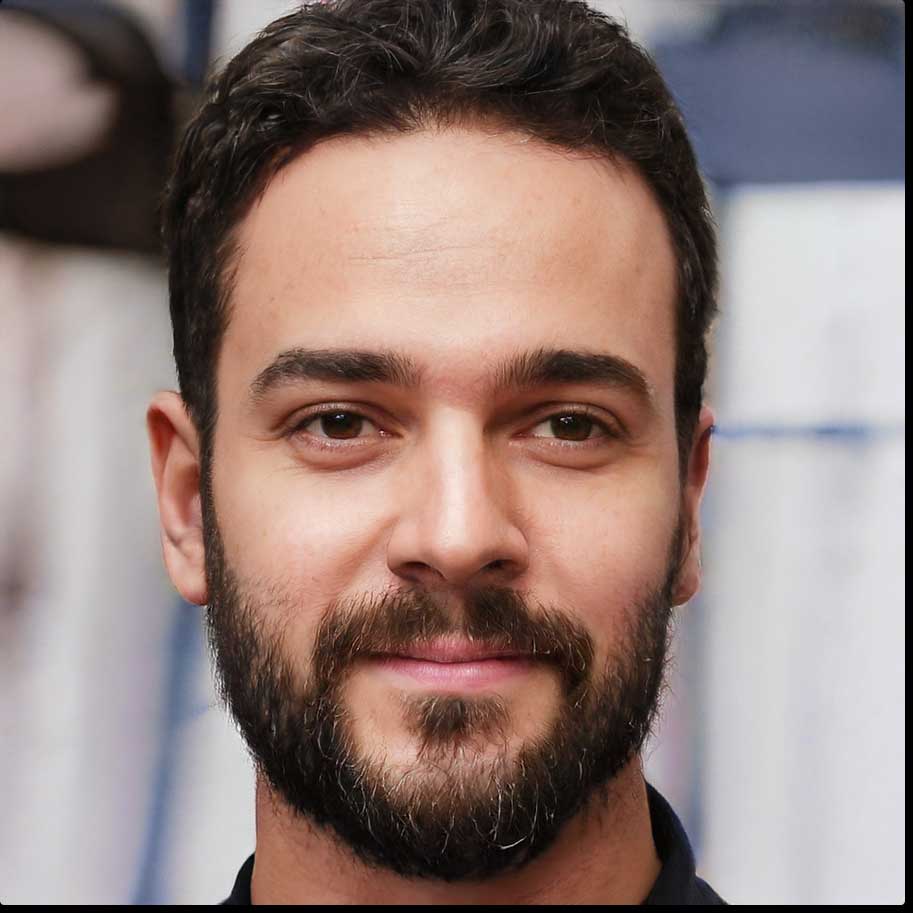