How to Be Welding Machinist - Job Description, Skills, and Interview Questions
Welding is a process used to join two or more metal parts together by melting and fusing them together. It is an important skill in the manufacturing and engineering industries and requires specialized equipment and knowledge. A welding machinist is responsible for the operation of the welding machinery, ensuring the quality of the welds, and troubleshooting in case of any problems.
They must have a thorough understanding of the welding process, the different types of welds, and how to use the equipment safely. The success of the welds relies heavily on the welding machinist's skill, knowledge, and experience. If they are not competent or properly trained, it could lead to dangerous defects in the welds which could cause structural damage or even injuries.
On the other hand, a skilled welding machinist can create strong, reliable welds that will last for years.
Steps How to Become
- Obtain a High School Diploma or GED. To become a welding machinist, the first step is to obtain a high school diploma or GED. Most employers require that candidates have at least a high school diploma or equivalent to be considered for a welding machinist position.
- Complete a Vocational or Technical Program. To become a welding machinist, you must complete a vocational or technical program. Most welding machinist programs take about one to two years to complete and include courses in welding, mathematics, safety practices, and blueprint reading.
- Obtain Certification. After completing a vocational or technical program, you may want to obtain certification through the American Welding Society (AWS). AWS certification is not required but may give you an edge when looking for a job.
- Gain Experience. To become a welding machinist, you must gain experience in the field. Many employers require at least one to two years of experience before they will consider hiring you. Try to find an apprenticeship or entry-level position so you can gain the experience you need.
- Take Continuing Education Classes. To stay up to date on the latest developments in the welding industry, it is important to take continuing education classes. These classes can help you stay ahead of the competition and may even lead to higher pay and new job opportunities.
Welding machinists must have a strong technical background and possess good problem-solving skills. In order to become a reliable and qualified machinist, they must first receive the proper training, which includes technical courses in welding and metallurgy, as well as safety courses. they should have a good understanding of welding equipment and its operation.
Once they have obtained the necessary qualifications, machinists must also stay up-to-date with the latest welding techniques and technologies through continuous practice and learning. As a result of this dedication, welding machinists can become reliable and qualified professionals who can safely and accurately weld a variety of materials.
You may want to check Quality Control Machinist, Tool and Die Machinist, and Computer Numerical Control (CNC) Machinist for alternative.
Job Description
- Assemble, install, and maintain welding equipment and tools.
- Set up and operate welding equipment, such as TIG, MIG, and Stick welders.
- Read and interpret blueprints and diagrams to determine the specific welding requirements.
- Inspect completed work for conformance to specifications and make any necessary adjustments.
- Monitor the welding process to detect potential problems.
- Operate grinders, cutters, and other tools to prepare materials for welding.
- Select the appropriate filler materials, such as electrodes, wire or rods, and fluxes.
- Maintain accurate records of all welds performed.
- Follow safety procedures when working with flammable materials and hazardous chemicals.
- Repair or modify existing structures or fabricate new parts as needed.
Skills and Competencies to Have
- Ability to read blueprints and understand welding specifications.
- Knowledge of welding techniques and processes, such as MIG/MAG, TIG, and arc welding.
- Skilled in operating welding machinery and equipment.
- Ability to use a variety of welding tools and instruments, such as rulers and calipers.
- Proficient in using metal fabrication tools, such as grinders, shears, and saws.
- Ability to troubleshoot welding problems and make necessary adjustments.
- Knowledge of safety procedures and OSHA regulations related to welding operations.
- Ability to work with minimal supervision and complete tasks within designated time frames.
- Good communication and organizational skills.
- Ability to lift up to 50 pounds and stand for extended periods of time.
Welding is a highly skilled trade that requires a great deal of knowledge and experience. A welding machinist must possess a variety of skills in order to be successful, including a strong knowledge of the welding process and materials, excellent problem-solving abilities, and an eye for detail. The most important skill a welding machinist needs to have is an understanding of the various welding processes such as MIG, TIG, stick, flux cored arc welding, oxyacetylene and plasma arc welding.
they must be knowledgeable about the different metals and alloys they will be working with, as well as the various tools and equipment used in the welding process. Furthermore, they must be able to read and interpret blueprints, drawings, and schematics to ensure precision and accuracy. Finally, a welding machinist must be able to work safely and ensure that all safety procedures are followed.
Having these core skills is essential for a welding machinist to successfully complete their job.
Production Machinist, Manual Machinist, and Machine Operator (Machinist) are related jobs you may like.
Frequent Interview Questions
- How much experience do you have with welding machining?
- Describe your experience setting up, operating and maintaining welding machines.
- What safety protocols do you follow when operating welding machines?
- What methods do you use to troubleshoot welding issues?
- How do you keep up to date on new welding technologies?
- What type of welding processes are you familiar with?
- How do you ensure welds are of the highest quality?
- How do you handle multiple tasks and prioritize them efficiently?
- What challenges have you faced in a welding machinist role and how did you address them?
- What do you enjoy most about working with welding machines?
Common Tools in Industry
- TIG Welder. A tool used for welding thin metals together with a tungsten electrode. (eg: example: used to weld aluminum sheet metal together).
- MIG Welder. A tool used for welding thicker metals together with a wire feed. (eg: example: used to weld steel beams together).
- Arc Welder. A tool used for welding thick metals together with an arc of electricity. (eg: example: used to weld steel plate together).
- Spot Welder. A tool used for welding thin sheets of metal together with a spot of electric current. (eg: example: used to weld sheet metal parts together).
- Plasma Cutter. A tool used for cutting hard materials such as steel, aluminum, and stainless steel using a plasma arc. (eg: example: used to cut metal bars into pieces).
Professional Organizations to Know
- American Welding Society (AWS)
- American Society of Mechanical Engineers (ASME)
- National Association of Professional Welders (NAPW)
- Fabricators & Manufacturers Association International (FMA)
- American Boiler Manufacturers Association (ABMA)
- International Institute of Welding (IIW)
- International Brotherhood of Boilermakers (IBB)
- American Society for Materials International (ASM)
- American Welding Institute (AWI)
- National Center for Welding Education and Training (NCWET)
We also have Fabrication Machinist, Laser Machinist, and Mold Maker Machinist jobs reports.
Common Important Terms
- Arc Welding. A welding process in which an electric arc is used to generate heat and melt the metals being joined together.
- Gas Welding. A welding process in which two pieces of metal are joined by a flame produced from a combustible gas.
- MIG Welding. A welding process in which a wire electrode is fed through a welding gun and used to create an arc that melts and joins the two pieces of metal together.
- TIG Welding. A welding process in which an arc is created between a non-consumable tungsten electrode and the workpiece.
- Soldering. A process of joining two pieces of metal together by heating them with a soldering iron and applying a filler material such as solder.
- Brazing. A process of joining two pieces of metal together by heating them and applying a filler material such as a brazing rod or flux.
- Heat Treating. A process of altering the physical and/or chemical properties of metals by heating them to a specific temperature for a specific amount of time.
- Plasma Cutting. A process of cutting metal by using an electric arc to heat and vaporize the metal, leaving a clean cut.
Frequently Asked Questions
What type of welding does a Welding Machinist typically perform?
A Welding Machinist typically performs arc welding, oxy-fuel welding, and tungsten inert gas (TIG) welding.
What type of materials do Welding Machinists typically work with?
Welding Machinists typically work with metals such as steel, aluminum, and brass. They also work with plastics and composites.
What safety protocols must be followed when operating welding equipment?
Welding Machinists must wear appropriate safety gear such as a welding helmet and protective clothing. They must also be aware of the hazards associated with the welding process, such as sparks and intense heat, and take the necessary precautions to protect themselves and those around them.
What skills are required to be a successful Welding Machinist?
A successful Welding Machinist must have a good understanding of the metals being worked with, have excellent problem-solving skills, and be able to follow safety protocols. Additionally, they must have a good eye for detail and be able to work accurately, even under pressure.
How much does a Welding Machinist typically earn?
The average salary for a Welding Machinist is around $42,000 per year. However, this can vary depending on experience and region.
What are jobs related with Welding Machinist?
- Die Cast Machinist
- CNC Machinist
- Grinder Machinist
- Mill Machinist
- Assembly Machinist
- Lathe Machinist
- Prototype Machinist
Web Resources
- Machining & Welding Training | Community College of Denver www.ccd.edu
- Career Comparison: Welder vs. Machinist | Tulsa Welding School www.tws.edu
- Welding Machine Overview - Tulsa Welding School www.tws.edu
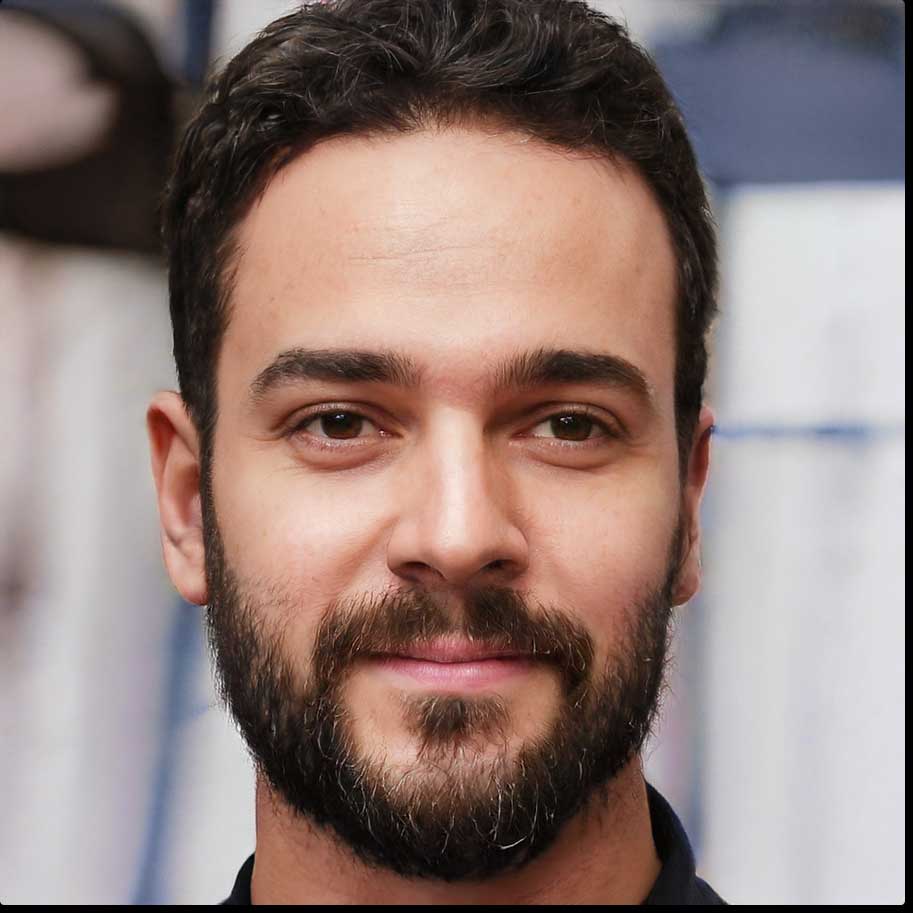