How to Be Grinder Machinist - Job Description, Skills, and Interview Questions
Steps How to Become
- Obtain a high school diploma or GED. The first step to becoming a grinder machinist is to obtain a high school diploma or GED. Most employers will require a minimum of a high school diploma or GED in order to be considered for the job.
- Take classes in machining and grinding. Grinder machinists must have a strong knowledge of machining and grinding. Taking classes in these subjects can give you a leg up when it comes to applying for jobs.
- Get on-the-job training. Many employers will provide on-the-job training for new hires, so look for an employer that offers this type of training. This will give you the opportunity to learn the skills you need to become a successful grinder machinist.
- Become certified. Some employers may require certification in order to work as a grinder machinist. Look into certification programs offered by trade organizations or community colleges to become certified.
- Find an apprenticeship. Apprenticeships are a great way to gain hands-on experience and learn from experienced professionals. Look for apprenticeship programs in your area that can help you gain the skills and knowledge you need to become a successful grinder machinist.
- Join professional organizations. Joining professional organizations can help you stay up-to-date on industry trends, find job opportunities, and network with other professionals in the field. Look for local and national organizations that specialize in grinding and machining.
In order to stay ahead and efficient as a Grinder Machinist, it is important to have a thorough understanding of the materials, tools, and techniques used in the trade. Staying up to date with the latest technology and advancements in grinding processes can help a Grinder Machinist stay ahead of the competition. training and experience are essential to mastering the precision and accuracy required for the job.
Investing in both the right equipment and the right people will ensure that jobs are completed in a timely and accurate manner. Lastly, having an organized and well-maintained work area will help the Grinder Machinist work faster, more efficiently, and with better quality results.
You may want to check Manual Machinist, Tool and Die Machinist, and Laser Machinist for alternative.
Job Description
- Set up and operate a variety of grinding machines to produce precision parts or products.
- Read blueprints, job orders, and other instructions to determine product specifications, set up requirements, and machine operations.
- Check parts for conformity to specifications using a variety of measuring tools and instruments.
- Select appropriate grinding wheels, based on factors such as finish, tolerances, and material specifications.
- Adjust machine settings, such as speed, feeds, and depth of cuts, to ensure optimal performance.
- Monitor machine operations to detect malfunctions or out-of-tolerance conditions.
- Dismantle and reassemble grinding machines for maintenance and repair.
- Clean and lubricate machine parts, using solvents and other materials.
- Repair worn or damaged parts; fabricate new parts using machine shop tools.
- Operate machinery to sharpen knives, drill bits, and other cutting tools.
Skills and Competencies to Have
- Knowledge of machine tools and their functions
- Ability to read and interpret blueprints and engineering drawings
- Ability to set up and operate grinding machines
- Knowledge of various grinding techniques and processes
- Knowledge of materials and their properties
- Knowledge of cutting tool materials
- Good hand-eye coordination and manual dexterity
- Sound problem solving and troubleshooting skills
- Good verbal and written communication skills
- Attention to detail
- Ability to work with tight tolerances
- Ability to work independently and as part of a team
- Understanding of safety procedures
- Proficiency in mathematics, including geometry and trigonometry
Being a Grinder Machinist requires a combination of technical and creative skill. The most important skill to have is the ability to use precision measuring tools, such as calipers and micrometers, to accurately measure and inspect parts. This requires a high level of attention to detail and a thorough understanding of the tolerances for each part.
In addition, machinists must be able to read and interpret blueprints and technical drawings to create parts that meet the required specifications. Furthermore, they must be able to program and operate grinding machines, as well as properly set-up and adjust the machines. Finally, having problem-solving skills to troubleshoot issues that arise is also essential.
All of these skills are essential for a successful Grinder Machinist.
Maintenance Machinist, Prototype Machinist, and Machine Operator (Machinist) are related jobs you may like.
Frequent Interview Questions
- What experience do you have operating a grinder machine?
- How would you respond to tight deadlines and quick turnarounds?
- Are you comfortable working with a variety of metals and materials?
- How do you handle the challenges of precision grinding?
- What safety protocols do you follow when using a grinder machine?
- Do you have any experience troubleshooting mechanical issues?
- What methods do you use to ensure accuracy in your work?
- Can you describe a project youve completed that required the use of a grinder machine?
- What strategies do you use to maximize efficiency when working with a grinder machine?
- How do you stay up-to-date with the latest industry changes and advances in grinder machine technology?
Common Tools in Industry
- Hand Grinder. A handheld grinding tool used to shape, cut, and smooth materials. (e. g. metals, plastics, and ceramics).
- Bench Grinder. A stationary grinding tool with two grinding wheels used to sharpen and shape objects. (e. g. drill bits, knives, and chisels).
- Lathe. A machine tool used to rotate a workpiece against a cutting tool to produce cylindrical shapes. (e. g. shafts, bushings, and spindles).
- Milling Machine. A machine tool used to cut and shape materials, such as metal or wood. (e. g. drilling, boring, and turning).
- Drill Press. A machine tool used to drill holes into materials with a rotating bit. (e. g. making holes in wood, metal, and plastic).
- Surface Grinder. A machine tool used to grind flat surfaces, typically for precision work. (e. g. sharpening blades and blades with intricate shapes).
- CNC Machine. A computer-controlled machine tool used to produce precision parts with high accuracy and repeatability. (e. g. complex 3D shapes and intricate patterns).
- Shaper. A machine tool used to shape and form materials, typically along a straight line or by a contour. (e. g. shaping a piece of metal into an axle or gear).
Professional Organizations to Know
- The Society of Manufacturing Engineers (SME)
- The American Society of Mechanical Engineers (ASME)
- The International Grinding Foundation (IGF)
- International Manufacturing Technology Show (IMTS)
- Association for Manufacturing Technology (AMT)
- The National Center for Manufacturing Sciences (NCMS)
- National Institute for Metalworking Skills (NIMS)
- National Tooling and Machining Association (NTMA)
- CNC Machine Tool Operators Association (CNCMTOA)
- American Machine Tool Distributors Association (AMTDA)
We also have Assembly Machinist, Production Machinist, and Computer Numerical Control (CNC) Machinist jobs reports.
Common Important Terms
- Lathe. A machine tool that rotates a workpiece about an axis of rotation to perform various operations such as cutting, sanding, drilling, or deformation.
- Drilling Machine. A machine tool used for drilling holes in various materials such as metal and wood.
- Milling Machine. A machine tool used for milling, which is a process of cutting and shaping material with a rotating cylindrical cutting tool.
- CNC Machine. A machine tool controlled by a computer program that automates the production of parts.
- Grinding Machine. A machine tool used to grind and finish material with an abrasive wheel.
- Jig Grinder. A machine tool used for grinding complex shapes and holes with an extremely high degree of accuracy.
- Tool and Cutter Grinder. A machine tool used for grinding and sharpening tools and cutters.
Frequently Asked Questions
What is a Grinder Machinist?
A Grinder Machinist is a skilled tradesperson who operates grinding and milling equipment to produce precision machined parts for various industries.
What are the duties of a Grinder Machinist?
The duties of a Grinder Machinist include setting up and operating grinding machines, selecting and measuring the correct tools and abrasives for the job, and examining and inspecting parts to meet quality standards.
What skills are necessary for a Grinder Machinist?
A Grinder Machinist should have experience with precision measurement tools, strong mechanical aptitude, and manual dexterity. Mathematics, blueprint reading, and problem-solving skills are also necessary.
What is the average salary of a Grinder Machinist?
According to the U.S Bureau of Labor Statistics, the median annual salary for a Grinder Machinist is $37,590.
What is the job outlook for Grinder Machinists?
The job outlook for Grinder Machinists is expected to have little or no change over the next decade.
What are jobs related with Grinder Machinist?
- Fabrication Machinist
- Lathe Machinist
- CNC Machinist
- Welding Machinist
- Mill Machinist
- Die Cast Machinist
- Quality Control Machinist
Web Resources
- Grind Machinist | Piedmont Technical College - ptc.edu www.ptc.edu
- Grinders - makerspace.tulane.edu makerspace.tulane.edu
- Bench Grinder Safety Awareness Guide | Environment, Health and Safety ehs.cornell.edu
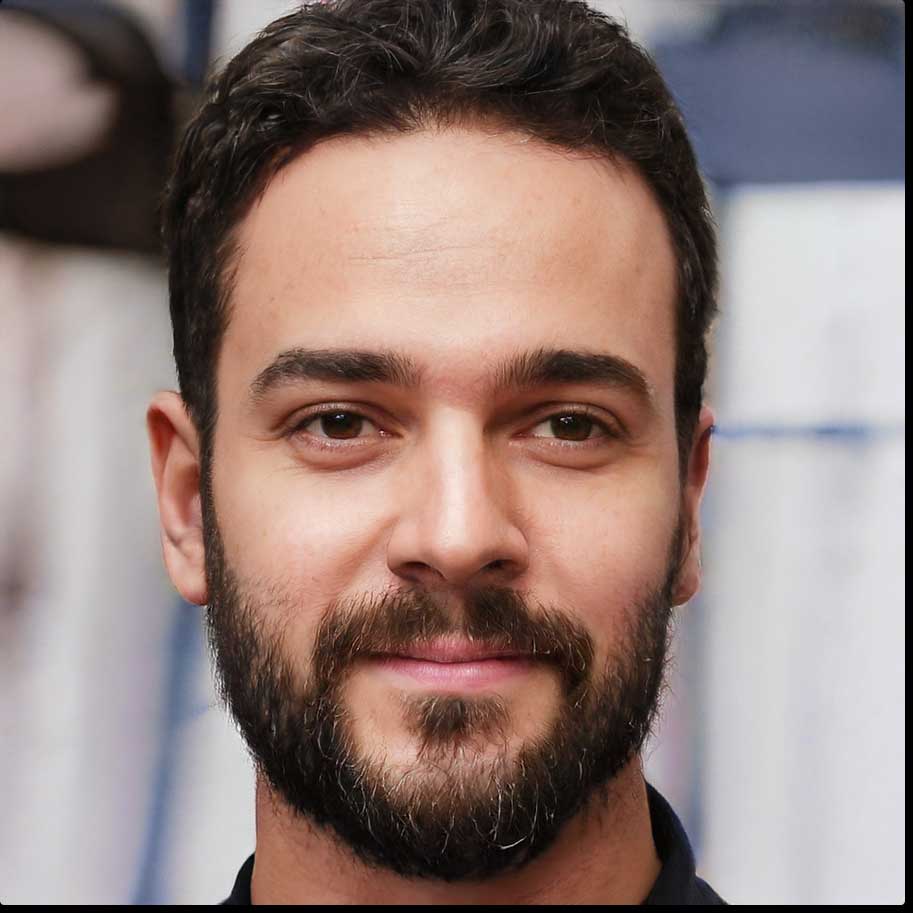