How to Be Maintenance Machinist - Job Description, Skills, and Interview Questions
Steps How to Become
- Obtain a high school diploma or equivalent. Most employers prefer to hire maintenance machinists with a high school diploma or equivalent. If you do not have a high school diploma, you can obtain a GED or other equivalent certification.
- Enroll in a vocational or technical school program. Many vocational and technical schools offer programs in maintenance machining. These programs provide students with the basic knowledge and skills necessary to become a successful maintenance machinist.
- Gain experience. Most employers require at least one year of experience in the field before they will consider hiring a maintenance machinist. After completing your education, consider working as an apprentice or intern in a machine shop to gain the necessary experience.
- Obtain certification. Many employers also require their maintenance machinists to be certified by the National Institute for Metalworking Skills (NIMS). Certification exams are offered through NIMS-certified schools and organizations.
- Apply for jobs. Once you have the necessary qualifications, begin applying for jobs as a maintenance machinist. Consider applying to larger manufacturing companies as well as smaller machine shops and repair facilities.
The need for a qualified Maintenance Machinist is paramount in order to ensure that machines are operating at peak efficiency and productivity. Without a qualified Maintenance Machinist, machines can experience frequent breakdowns, resulting in costly downtime, decreased production output, and higher costs for repairs and maintenance. Furthermore, without a qualified Maintenance Machinist, machines may not be used safely, leading to potential worker injuries and liabilities.
To be ideal and qualified, a Maintenance Machinist must possess a combination of technical knowledge, problem-solving expertise, and experience in machine operations. They should also be well versed in the latest industry technologies and possess the necessary certifications. having a qualified Maintenance Machinist ensures the smooth running of machines and helps to avoid costly downtime and liabilities.
You may want to check Mold Maker Machinist, Manual Machinist, and Lathe Machinist for alternative.
Job Description
- Set up, adjust, and operate all of the basic machine tools and many specialized or advanced variation tools in order to perform precision machining operations.
- Read and interpret blueprints, sketches, drawings, manuals, specifications, or sample parts to determine dimensions and tolerances of finished workpiece, sequence of operations, and setup requirements.
- Measure, mark, and scribe dimensions and reference lines on material or workpiece as guides for subsequent machining.
- Calculate and set control settings for machine tools to index or feed stock into position for machining.
- Select tools, attachments, collets, fixtures, and/or template to be used in machining operations.
- Position, secure, and align cutting tools in tool holders on machine spindles.
- Start and observe machine operation to detect malfunctions or out-of-tolerance machining, and adjust machine controls or control media as required.
- Inspect machined workpieces visually and with measurement instruments such as micrometers and dial indicators to verify conformance to specifications.
- Perform minor machine maintenance tasks such as cleaning, lubricating, adjusting, or replacing consumable parts such as cutting tools, tool bits, belts, and other parts as necessary.
- Monitor the feed and speed of machines during the machining process.
Skills and Competencies to Have
- Knowledge of machine operations and maintenance principles
- Ability to troubleshoot and diagnose machinery problems
- Ability to read and understand engineering drawings and schematics
- Ability to use hand tools, measuring instruments, and precision measuring equipment
- Ability to use basic software programs, such as computer numerical control (CNC) programming
- Ability to fabricate and repair parts using welding, soldering, and other metalworking techniques
- Knowledge of safety protocols and procedures
- Ability to work independently and as part of a team
- Excellent communication and problem-solving skills
- Attention to detail and accuracy
Maintenance machinists require a variety of skills in order to be successful in their role. The most important skill is the ability to troubleshoot. Maintenance machinists must be able to quickly identify and resolve potential problems with machines, mechanical systems, and other equipment.
This requires knowledge of the technical aspects of the machines, as well as a deep understanding of the operating principles of the systems. maintenance machinists must have strong problem-solving skills in order to accurately diagnose issues and plan efficient solutions. They must also possess excellent communication skills in order to collaborate with other technicians, engineers and supervisors to ensure proper maintenance of the machines.
Finally, a high level of mechanical aptitude is essential for maintenance machinists to repair and maintain various mechanical systems and components. Overall, a combination of these skills is essential for any successful maintenance machinist.
Welding Machinist, Computer Numerical Control (CNC) Machinist, and Quality Control Machinist are related jobs you may like.
Frequent Interview Questions
- What experience do you have with machine maintenance?
- What is your knowledge of CNC machining?
- How do you troubleshoot machine problems?
- Describe a time when you identified and resolved a machine issue efficiently and effectively.
- What safety protocols do you follow when performing maintenance and repairs?
- What experience do you have with PLC programming?
- How do you stay up to date with the latest technology and industry trends?
- How do you prioritize tasks to ensure all work is completed efficiently?
- What processes do you use to ensure that all maintenance and repairs are documented correctly?
- Describe a project where you successfully planned, organized and completed a complex maintenance job.
Common Tools in Industry
- Lathe. A machine tool that rotates a workpiece about an axis of rotation to perform various operations such as cutting, sanding, knurling, drilling, or deformation. (Eg: CNC Lathe)
- Mill. A machine tool that uses a rotating cutting tool to remove material from a workpiece. (Eg: CNC Mill)
- Drill Press. A machine tool used to create holes in materials. (Eg: Radial Arm Drill Press)
- Grinder. A machine tool used to shape or finish a workpiece by abrasion with grinding wheels. (Eg: Bench Grinder)
- Saw. A machine tool used to cut material into desired shapes and sizes. (Eg: Table Saw)
- Welder. A machine tool used to join two pieces of metal together using heat or pressure. (Eg: Arc Welder)
- Press. A machine tool used to exert force on a workpiece to form or shape it. (Eg: Hydraulic Press)
- Bender. A machine tool used to bend or shape material. (Eg: Pipe Bender)
- Sander. A machine tool used to smooth surfaces by abrasion with sandpaper. (Eg: Belt Sander)
- Shaper. A machine tool used to cut or shape material with a reciprocating single-point cutting tool. (Eg: Shaping Machine)
Professional Organizations to Know
- American Society of Mechanical Engineers (ASME)
- International Association for Automation and Robotics in Construction (IAARC)
- Society of Manufacturing Engineers (SME)
- National Institute for Metalworking Skills (NIMS)
- International Manufacturing Technology Show (IMTS)
- International Machine Tool Show (IMTS)
- Association for Manufacturing Technology (AMT)
- International Organization for Standardization (ISO)
- National Institute of Standards and Technology (NIST)
- Fabricators & Manufacturers Association, International (FMA)
We also have Grinder Machinist, Production Machinist, and Prototype Machinist jobs reports.
Common Important Terms
- Tool Grinding. The process of grinding a tool to a desired shape or size.
- Lathe Operation. The operation of a lathe, which typically involves turning a cylindrical object against a cutting tool.
- CNC Milling. Computer numerical control (CNC) milling is a process that uses computer-controlled cutting tools to create intricate shapes and parts from a variety of materials.
- Sheet Metal Working. The process of forming sheet metal into various shapes and sizes using specialized tools and machinery.
- Welding. The process of joining two pieces of metal together using heat or an electric current.
- Metal Fabrication. The process of creating custom parts and components from various metal materials through various processes including cutting, bending, and shaping.
- Hydraulics. The use of pressurized liquids to generate power or motion.
- Pneumatics. The use of pressurized air to generate power or motion.
- Electrical Troubleshooting. The process of diagnosing and resolving electrical problems in equipment.
Frequently Asked Questions
What is the role of a Maintenance Machinist?
A Maintenance Machinist is responsible for repairing and maintaining machinery, tools, and equipment used in industrial and commercial settings. They also perform preventive maintenance and troubleshooting of machinery and equipment to ensure operational efficiency.
What skills are needed for a Maintenance Machinist?
To be successful in the role of a Maintenance Machinist, one must have strong mechanical aptitude, knowledge of machine tools, welding, and machining processes. They must also be able to read blueprints and schematics, possess good problem-solving and troubleshooting skills, and have the ability to work with hand tools and power tools.
What are the hours of a Maintenance Machinist?
A Maintenance Machinist typically works full-time hours, often including evenings and weekends.
What is the salary range for a Maintenance Machinist?
The median salary for a Maintenance Machinist is $45,000 per year. Salaries range from $35,000 to $60,000 per year depending on experience and location.
What certifications are required for a Maintenance Machinist?
Most employers require a certification from the National Institute for Metalworking Skills (NIMS). Additionally, many employers may require specific certifications such as OSHA 10 or 30.
What are jobs related with Maintenance Machinist?
- Tool and Die Machinist
- Assembly Machinist
- Die Cast Machinist
- Fabrication Machinist
- CNC Machinist
- Mill Machinist
- Machine Operator (Machinist)
Web Resources
- Maintenance Mechanic I Certificate - Harper College www.harpercollege.edu
- Maintenance Mechanic- Machinist Greene Center | University ¦ careereducation.rochester.edu
- Maintenance Machinist City and County of San Francisco ¦ capd.mit.edu
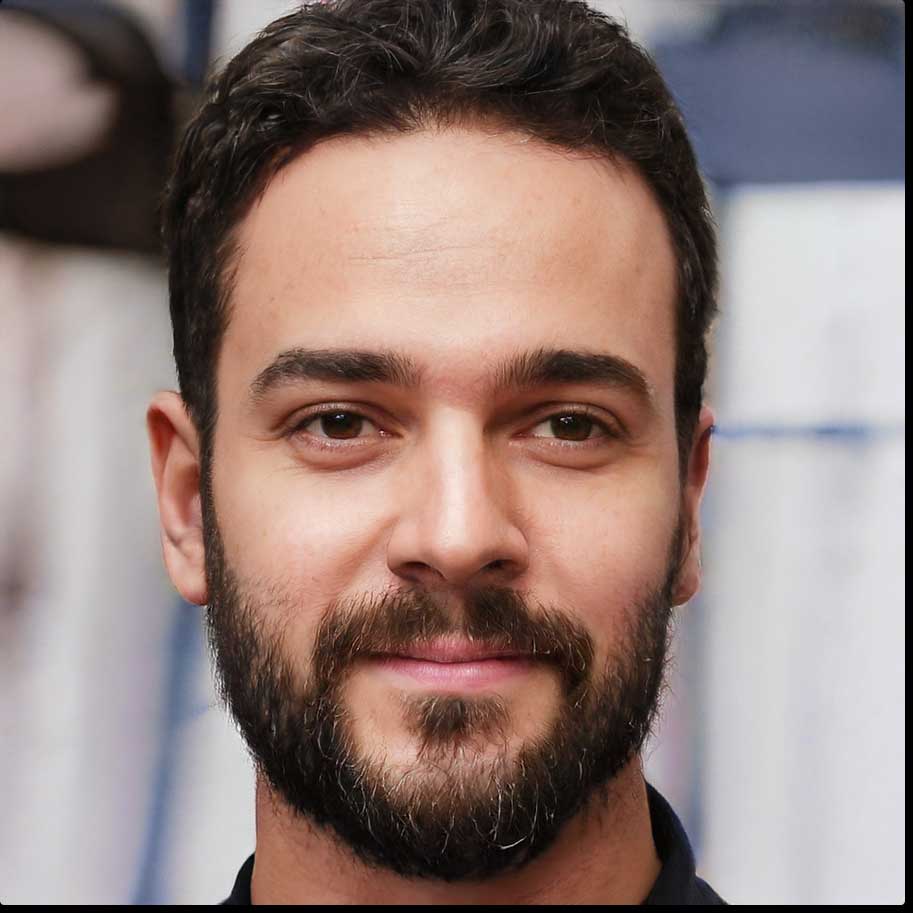