How to Be Facilities Maintenance Technician - Job Description, Skills, and Interview Questions
Steps How to Become
- Obtain a high school diploma or equivalent. Most employers require applicants for maintenance technician positions to have a high school diploma or equivalent.
- Take courses in a related field. Many employers prefer applicants who have taken coursework in the areas of electricity, plumbing, heating and air conditioning, carpentry, and building maintenance.
- Get on-the-job training from a professional. Many employers offer on-the-job training for maintenance technicians. During this time, technicians will learn about the equipment and tools used in their job and gain hands-on experience.
- Earn certifications or licenses. Depending on the state, some positions may require technicians to be certified or licensed to work in certain areas such as HVAC or electrical work.
- Consider continuing education courses. In order to stay up-to-date with the latest technologies and techniques, many employers require technicians to take continuing education courses to maintain their certification or license.
- Become a member of a professional organization. Joining a professional organization such as the Building Maintenance and Facilities Management Association can be beneficial for networking and keeping up with industry trends.
Being a Facilities Maintenance Technician requires staying ahead of the curve when it comes to new technologies and techniques. To do this, it is important to continue learning and developing new skills to ensure that you remain qualified and up-to-date. This can be done by attending industry-specific workshops and seminars, participating in online courses, and reading trade publications to stay informed about the latest trends and developments in the field.
staying connected with colleagues and other professionals in the industry can help to build a network and gain access to valuable resources and advice. By taking the time to stay ahead of the curve and stay qualified, Facilities Maintenance Technicians can remain competitive and provide their clients with the best possible service.
You may want to check Property Maintenance Worker, Tenant Relations Coordinator, and Housing Inspector for alternative.
Job Description
- Diagnose and repair facility equipment including HVAC, plumbing, electrical, and mechanical systems.
- Perform preventative maintenance on facility equipment to ensure optimal performance and efficiency.
- Troubleshoot and repair facility electrical issues, including wiring, controls, and circuits.
- Install new equipment and systems according to manufacturer's instructions.
- Monitor facility systems to ensure they are operating properly and efficiently.
- Perform regular facility inspections to identify potential safety hazards and maintenance needs.
- Respond to emergency repair requests in a timely manner.
- Maintain records of all repairs, maintenance activities, and parts used.
- Procure materials, parts, and tools needed for maintenance tasks.
- Adhere to all safety policies, procedures, and regulations.
Skills and Competencies to Have
- Knowledge of general maintenance practices
- Knowledge of plumbing, electrical and HVAC systems
- Ability to troubleshoot and diagnose problems
- Ability to read and interpret blueprints and schematics
- Skilled in the use of a variety of hand and power tools
- Knowledge of relevant safety regulations
- Ability to work independently and as part of a team
- Good communication skills
- Ability to lift heavy items
- Good problem-solving skills
Having a good set of facilities maintenance technician skills is essential for anyone wanting to enter the profession. A great facility maintenance technician needs to be able to troubleshoot and diagnose issues quickly and accurately, be able to repair faulty machinery, and have a strong understanding of the buildings electrical and plumbing systems. They must also be adept at using hand and power tools, as well as a variety of diagnostic equipment.
Furthermore, they must be able to work in a variety of conditions and follow safety procedures to ensure everything is running smoothly. By having these skills, facility maintenance technicians can ensure that the workplace is safe and efficient, leading to increased productivity, reduced costs, and improved customer satisfaction.
Apartment Building Superintendent, Residential Property Manager, and Real Estate Investment Trust Analyst are related jobs you may like.
Frequent Interview Questions
- What experience do you have in facilities maintenance?
- How would you rate your ability to troubleshoot and resolve mechanical issues?
- Describe a recent project that you completed successfully in a facilities maintenance role.
- How do you stay up-to-date on the latest advancements in facilities maintenance?
- Describe your experience with HVAC systems and how you go about performing routine maintenance.
- What safety protocols do you follow when working with electricity and other hazardous materials?
- How do you prioritize tasks and manage competing demands?
- How would you handle a situation where a tenant is unhappy with the maintenance youve provided?
- How do you work with vendors to ensure timely delivery of parts and services?
- What do you believe are the most important skills for a successful facilities maintenance technician?
Common Tools in Industry
- Multimeter. A device used for measuring electrical current, voltage, and resistance. (eg: testing the voltage of a circuit)
- Wrench Set. A collection of wrenches used for tightening or loosening nuts and bolts. (eg: tightening a loose bolt on a machine)
- Pliers. Hand-held tools used for gripping and manipulating objects. (eg: removing a wire from a box)
- Screwdriver Set. A collection of screwdrivers used for driving screws into materials. (eg: installing new screws on a cabinet door)
- Socket Set. A collection of sockets and ratchets used for fastening and loosening nuts and bolts. (eg: unscrewing a bolt on a machine)
- Hammer. A tool used for pounding and driving nails into materials. (eg: nailing a nail into a wall)
- Saw. A tool used for cutting materials. (eg: cutting a piece of wood to size)
- Drill. A tool used for drilling holes into materials. (eg: drilling holes in a wall for mounting shelves)
- Level. A tool used for testing the flatness of surfaces. (eg: checking the level of a countertop)
- Soldering Iron. A device used for joining two pieces of metal together with solder. (eg: soldering two wires together)
Professional Organizations to Know
- American Society of Heating, Refrigerating and Air-Conditioning Engineers (ASHRAE)
- American Society of Mechanical Engineers (ASME)
- Plumbing-Heating-Cooling Contractors Association (PHCC)
- National Fire Protection Association (NFPA)
- Association of Facility Engineers (AFE)
- American Institute of Plant Engineers (AIPE)
- Building Owners and Managers Association International (BOMA)
- International Facility Management Association (IFMA)
- National Electrical Contractors Association (NECA)
- National Institute of Building Sciences (NIBS)
We also have Property Management Assistant, Landlord Assistant, and Property Administrator jobs reports.
Common Important Terms
- Preventive Maintenance. Regularly scheduled inspections, tests, and repairs of critical systems and equipment to ensure they are operating properly and to prevent potential future breakdowns.
- Troubleshooting. Systematically identifying, isolating, and diagnosing problems or malfunctions in equipment, systems, or processes.
- HVAC Systems. Heating, Ventilation, and Air Conditioning systems that provide thermal comfort, improved indoor air quality, and air circulation.
- Electrical Systems. Electrical systems that are responsible for providing power to buildings, homes and other structures.
- Plumbing Systems. Pipes and fixtures used to convey water and other liquids, as well as sewage disposal systems.
- Building Automation Systems. Computerized control systems used to monitor and manage the mechanical, electrical, and lighting systems in a building.
- Life Safety Systems. Equipment such as fire alarms, smoke detectors, emergency lighting, and sprinkler systems used to protect people from injury or death in case of emergency.
Frequently Asked Questions
What qualifications do I need to become a Facilities Maintenance Technician?
Generally, a high school diploma or equivalent is required, along with experience in basic maintenance, repair and construction techniques. Knowledge of building systems such as HVAC, plumbing, electrical, and carpentry is also necessary, as well as experience with hand and power tools.
What are the responsibilities of a Facilities Maintenance Technician?
Facilities Maintenance Technicians are responsible for performing a wide range of duties related to the upkeep and maintenance of buildings and grounds. This includes inspecting and testing equipment, performing minor repairs, diagnosing and resolving problems, maintaining records and reports, and ordering supplies as needed.
How much does a Facilities Maintenance Technician make?
The average salary for a Facilities Maintenance Technician is around $43,000 annually. This can vary depending on experience, geographic location, and employer.
What safety measures should a Facilities Maintenance Technician be aware of?
Facilities Maintenance Technicians should be aware of and follow all safety regulations, wear appropriate safety equipment, and use caution when working with hazardous materials or tools. It is also important to be aware of potential hazards in the work environment and take steps to minimize risks.
What type of work environment do Facilities Maintenance Technicians typically work in?
Facilities Maintenance Technicians typically work in an indoor or outdoor environment. They may be required to work in hazardous conditions such as high places or confined spaces, and must be able to lift and carry heavy objects. They may also work in both residential and commercial settings.
What are jobs related with Facilities Maintenance Technician?
- Property Rental Agent
- Building Supervisor
- Residential Leasing Manager
- Tenant Liaison Officer
- Lease Administrator
- Property Caretaker
- Real Estate Investor
- Property Acquisition Analyst
- Rental Property Manager
- Apartment Leasing Consultant
Web Resources
- Facility Maintenance Technician - Center for Employment Training cetweb.edu
- Facility Maintenance Technician | Maintenance ¦ www.ccnn.edu
- What Does a Facilities Maintenance Technician Do? www.rsi.edu
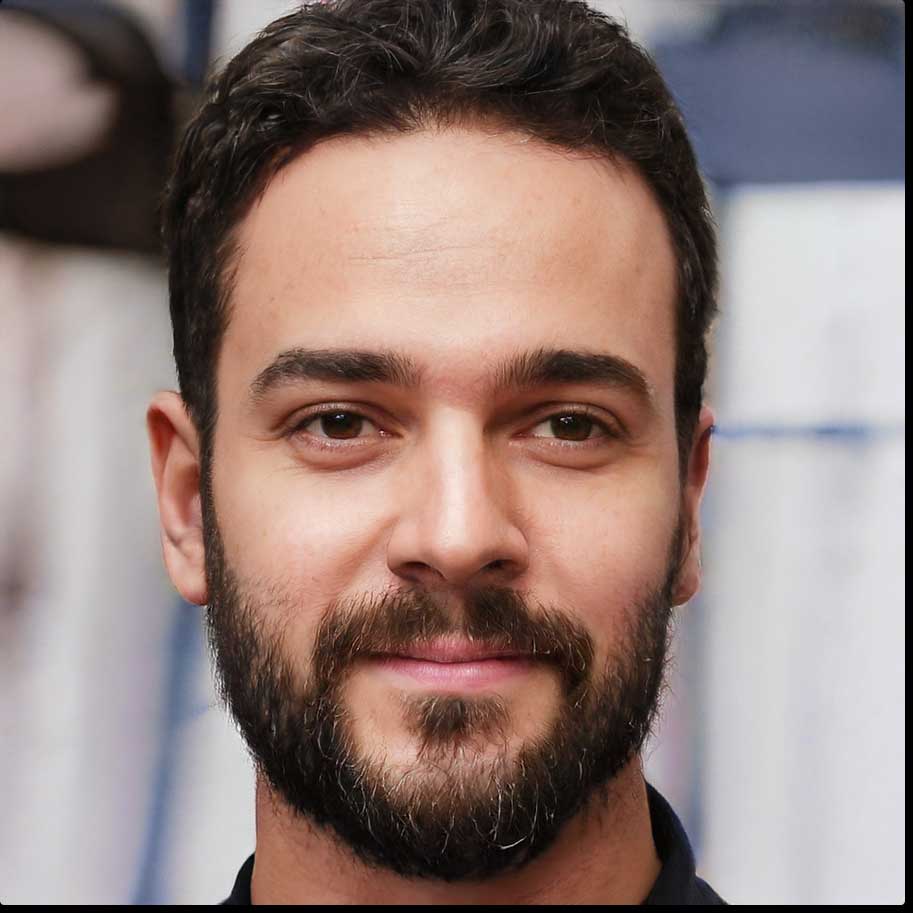