How to Be Materials Manager - Job Description, Skills, and Interview Questions
The lack of an effective materials manager can have a detrimental effect on a company's operations. Without a materials manager, the company may experience a shortage of necessary supplies or materials, have difficulty controlling costs, and have trouble meeting customer demands. Furthermore, an inadequate materials manager can lead to inefficient inventory management, resulting in lost sales and higher overhead costs.
Consequently, companies must invest in hiring and training an experienced materials manager to ensure that the necessary materials are available when needed, costs remain under control, and customer needs are met. This, in turn, can help the company to maximize profits and maintain a competitive edge.
Steps How to Become
- Earn a Bachelor's Degree. The first step to becoming a materials manager is to obtain a bachelor's degree in business, logistics, supply chain management, or a related field. Programs that offer courses in inventory control, procurement and contract management, and transportation management are especially beneficial.
- Gain Experience. It is important for aspiring materials managers to gain experience in the field. This can be done through internships, apprenticeships, or through working in a related field such as inventory control or supply chain management.
- Obtain Certification. Many materials managers choose to obtain certification in order to demonstrate their expertise and to increase their job prospects. The American Production and Inventory Control Society (APICS) offers several certification options, such as the Certified in Production and Inventory Management (CPIM) and Certified Supply Chain Professional (CSCP) certifications.
- Develop Management Skills. Materials managers must have strong management skills in order to effectively lead teams and oversee projects. Developing these skills can be done through professional workshops, seminars, and courses.
- Stay Up-to-Date on Industry Trends. The materials management field is constantly evolving, so it is important for materials managers to stay up-to-date on industry trends. This can be done through reading trade publications, attending conferences, and networking with professionals in the field.
As a materials manager, staying ahead and capable requires a combination of proactive planning and ongoing assessment. Proactive planning involves conducting research to stay informed of industry trends, analyzing current material needs, and forecasting future demands. This can help identify potential risks and opportunities prior to material acquisitions, as well as ensure the right materials are available to meet production needs.
In addition to proactive planning, materials managers must use ongoing assessments to monitor inventory levels, evaluate current suppliers and vendors, and assess alternative supply sources. Regular assessments of these factors can help reduce costs, improve customer service, and ensure the availability of materials to keep production running smoothly. By utilizing proactive planning and ongoing assessments, materials managers can remain ahead and capable in the ever-changing materials management environment.
You may want to check Materials Scheduler, Materials Sales Representative, and Materials Program Manager for alternative.
Job Description
- Develop and implement inventory control systems.
- Analyze data to determine the need for restocking or replenishing inventory.
- Monitor stock levels and anticipate future needs.
- Identify and resolve discrepancies between physical stock counts and computerized inventory records.
- Evaluate suppliers to ensure quality and cost-effective purchasing.
- Develop relationships with vendors and negotiate contracts for the purchase of materials.
- Monitor and inspect incoming shipments to ensure accuracy and quality.
- Store materials in accordance with established procedures and maintain accurate records of movement.
- Oversee the disposal of excess, obsolete, or damaged materials.
- Coordinate with other departments to ensure timely ordering, delivery, and availability of materials.
- Establish and maintain effective safety procedures for material handling processes.
- Prepare reports on inventory levels and inventory costs.
Skills and Competencies to Have
- Knowledge of procurement and inventory management processes
- Excellent organizational, problem solving and analytical skills
- Ability to develop and maintain strong relationships with vendors
- Ability to multitask and manage multiple projects simultaneously
- Knowledge of industry-specific supply chain requirements
- Knowledge of material resource planning, production scheduling and inventory control systems
- Excellent communication and negotiation skills
- Experience with budgeting and financial management
- Ability to work independently and as part of a team
- Proficiency in Microsoft Office Suite and other relevant software applications
A successful Materials Manager needs to have excellent organizational skills in order to effectively keep track of the materials and components that are necessary for the smooth operation of a business. This includes being able to accurately assess the amounts and types of materials needed, as well as effectively scheduling deliveries. It is also important to be able to build strong relationships with suppliers, so that they can be relied on to provide quality materials in a timely manner.
Good problem solving skills are essential, as the Materials Manager is likely to be faced with unexpected issues that could have a major impact on operations. Finally, the ability to anticipate future needs and plan ahead is vital, so that materials are always available when needed and costs are kept to a minimum. By having these skills, a Materials Manager can ensure that operations run smoothly and efficiently, leading to increased revenue and customer satisfaction.
Materials Handler, Materials Accounting Clerk, and Advanced Materials Engineer are related jobs you may like.
Frequent Interview Questions
- What experience do you have in managing materials inventory?
- How do you ensure that the materials needed for production are available on time?
- What strategies do you employ to minimize excess materials and reduce waste?
- How do you ensure that materials are procured at the best possible price?
- How do you ensure that materials meet required quality standards?
- What methods do you use to track and monitor materials usage and costs?
- What systems have you implemented to improve material planning and forecasting?
- How do you develop and maintain relationships with suppliers to ensure reliable supply of materials?
- How do you ensure that materials are stored, handled, and moved safely and securely?
- How do you motivate and manage a team of materials personnel?
Common Tools in Industry
- Kanban Board. A visual tool used to track and manage material inventory. (eg: A whiteboard with columns for In Stock, On Order, and In Transit items. )
- Material Requirements Planning (MRP). A system for calculating and scheduling material needs based on production orders. (eg: An automated system that forecasts materials needed for production, taking into account inventory levels and lead times. )
- Barcoding System. A system for tracking and managing materials using barcodes. (eg: A hardware and software system that scans barcodes to manage inventory and track material movements. )
- Inventory Management Software. A software system used to manage and track materials, inventory, and orders. (eg: A software system that allows a materials manager to manage stock levels, order history, and other related tasks. )
- Supplier Relationship Management Software. A software system used to track and manage relationships with suppliers. (eg: A software system that stores supplier contact information, lead times, pricing, and other related data. )
- Warehouse Management System. A software system used to manage warehouse operations and inventory control. (eg: A software system that tracks receipt of materials, location of materials in the warehouse, and shipments of materials. )
Professional Organizations to Know
- Institute of Supply Management (ISM)
- Association for Supply Chain Management (ASCM)
- National Association of Purchasing Management (NAPM)
- Chartered Institute of Procurement and Supply (CIPS)
- International Federation of Purchasing and Supply Management (IFPSM)
- American Purchasing Society (APS)
- Global Supply Chain Council (GSCC)
- International Association for Inventory Management (IAIM)
- International Purchasing and Supply Education and Research Association (IPSERA)
- Material Handling Industry of America (MHIA)
We also have Recycled Materials Coordinator, Raw Materials Specialist, and Materials Technician jobs reports.
Common Important Terms
- Inventory Control. The process of managing and tracking the stock of goods and materials in order to prevent overstocking or running out of items.
- Procurement. The process of buying goods and services from external suppliers.
- Warehousing. The process of maintaining and storing goods until they are needed.
- Logistics. The process of planning and executing the efficient movement of goods and materials from one location to another.
- Supply Chain Management. The process of coordinating the activities involved in the production, procurement, and distribution of goods and services to ensure customer satisfaction.
- Quality Control. The process of ensuring that products or services meet established standards of quality.
- Lean Manufacturing. A manufacturing method that seeks to eliminate waste and maximize efficiency by focusing on eliminating non-value-added activities.
- Just-in-Time (JIT) Inventory. An inventory management strategy which seeks to reduce inventory by ordering only what is needed when it is needed.
Frequently Asked Questions
What is a Materials Manager?
A Materials Manager is responsible for tracking and ordering materials for a business or organization. They are also responsible for overseeing inventory control, warehouse management, distribution, and procurement operations.
What skills are needed to be a successful Materials Manager?
A successful Materials Manager should possess strong organizational skills, knowledge of inventory management systems and software, good communication and negotiation skills, and the ability to work independently.
What qualifications are required to be a Materials Manager?
To be a Materials Manager, typically a bachelor's degree in business or a related field is required. Additionally, experience in inventory management, logistics, or supply chain management is often preferred.
What is the average salary for a Materials Manager?
The average salary for a Materials Manager is $64,185 per year. Salaries can vary depending on experience and location.
What are the duties of a Materials Manager?
The duties of a Materials Manager include overseeing inventory control and procurement operations, managing warehouse staff, tracking and ordering materials, evaluating suppliers, and negotiating contracts.
What are jobs related with Materials Manager?
- Materials Planner
- Materials Coordinator
- Finished Materials Inspector
- Materials Supervisor
- Materials Inventory Clerk
- Materials Analyst
- Materials Buyer
Web Resources
- Materials Management | Georgia College & State University www.gcsu.edu
- Materials Management | Portland State University - pdx.edu www.pdx.edu
- Materials Management and Logistics Department : Texas State ¦ www.materialsmgt.txst.edu
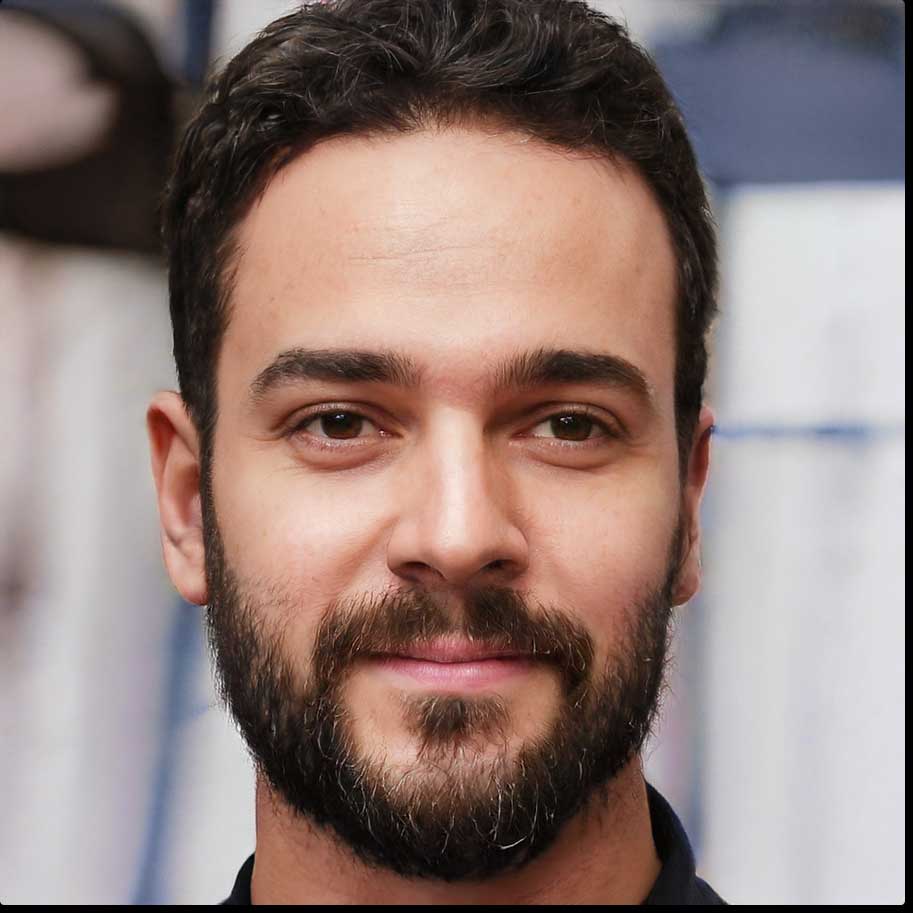