How to Be Materials Scheduler - Job Description, Skills, and Interview Questions
The Materials Scheduler plays a critical role in ensuring a successful project. They have to ensure on-time delivery of materials and resources, in order to keep a project on schedule, within budget and of the highest quality. When materials are not delivered on time, it can cause delays in production, overtime expenses, and cost overruns.
It can also lead to unhappy customers, who might take their business elsewhere. By carefully managing the materials supply chain, the Scheduler can help prevent these problems and ensure that the project is completed on time, within budget and to the customer's satisfaction.
Steps How to Become
- Obtain a high school diploma or GED. Most employers require that applicants hold at least a high school diploma or a GED.
- Consider obtaining a college degree. Many employers prefer to hire candidates who have obtained a bachelor's degree in supply chain management, operations management, logistics, or a related field.
- Gain experience in the field. Try to get a job in supply chain management or logistics to acquire experience with scheduling and production planning.
- Become familiar with industry-specific software. Materials schedulers use software to track inventory levels and plan production schedules.
- Learn about the company you are applying to. Understanding the company's production process and needs will help you to be a better materials scheduler.
- Apply for materials scheduler positions. Look for job postings online or contact staffing agencies.
- Prepare for the job interview. Make sure to bring a resume and any relevant certifications or degrees that you may have obtained.
- Take and pass any required assessments. Many companies require applicants to pass assessments related to scheduling, inventory management, and other relevant topics.
- Participate in training. After you are hired, you will likely need to undergo a training period in order to learn the company's systems and processes.
- Perform your job duties. As a materials scheduler, your job will involve tracking inventory levels, planning production schedules, and monitoring orders.
Staying ahead and efficient as a Materials Scheduler requires careful planning and organization. The key to success is to ensure that all the materials necessary for a job are on hand when they are needed. This means staying on top of inventory levels, ordering materials in a timely manner, and making sure that any delays or issues in delivery are addressed as quickly as possible.
When inventory levels are managed properly, it reduces the risk of running out of materials or having them arrive late, which can lead to costly delays or even production stoppages. regularly reviewing scheduling processes and procedures can help identify areas where improvements can be made, leading to more efficient operations and better use of resources.
You may want to check Materials Manager, Materials Handler, and Materials Accounting Clerk for alternative.
Job Description
- Monitor inventory levels and place orders for materials as needed.
- Source and purchase materials from approved vendors.
- Negotiate with vendors to obtain the best pricing and terms.
- Maintain accurate records of inventory levels, order processing, and vendor information.
- Coordinate and manage the movement of materials to production areas in a timely fashion.
- Develop and implement strategies for efficient storage of materials.
- Track and report on material costs and usage trends.
- Ensure compliance with all safety and environmental regulations related to materials handling.
- Monitor supplier performance and resolve any issues in a timely manner.
- Analyze supplier data to identify cost savings opportunities.
Skills and Competencies to Have
- Strong organizational skills
- Ability to prioritize tasks
- Excellent communication skills
- Ability to work well under pressure
- Knowledge of material scheduling software
- Knowledge of inventory management
- Understanding of supply chain principles
- Ability to work with multiple stakeholders
- Knowledge of supplier contracts and negotiation
- Understanding of purchasing processes
- Attention to detail
- Ability to analyze data and make decisions
- Ability to forecast and plan for the future
- Ability to troubleshoot and problem-solve
Time management is an essential skill for a Materials Scheduler to possess in order to be successful. Without proper time management, the scheduler may find themselves falling behind, unable to catch up on tasks, and even missing deadlines. This can cause production delays, resulting in lost profits and customer dissatisfaction.
inadequate scheduling can lead to an increase in material costs due to inaccurate or untimely ordering of supplies. Good time management skills enable a Materials Scheduler to create realistic schedules, respond promptly to changes in demand, and plan ahead for potential supply chain disruptions. This helps to ensure that materials are ordered and received on time, while also minimizing unnecessary costs.
having strong time management skills enables a Materials Scheduler to effectively and efficiently manage the materials needed for production, resulting in a successful and profitable operation.
Materials Sales Representative, Materials Analyst, and Materials Inventory Clerk are related jobs you may like.
Frequent Interview Questions
- What is your experience in materials scheduling?
- How do you ensure that materials availability meets production needs?
- Describe your experience with identifying and resolving supply chain issues.
- How do you prioritize tasks to ensure on-time delivery of materials?
- What techniques do you use to maintain accurate records of inventory and shipments?
- How do you ensure that the right materials are delivered to the right locations on time?
- What strategies do you use to manage and forecast inventory levels?
- What experience do you have with ERP systems?
- What processes do you use to track shipments and expedite orders when needed?
- How do you stay up-to-date with industry trends and supply chain innovations?
Common Tools in Industry
- Scheduling Software. Scheduling software helps to manage resources, tasks and events in a systematic way. (eg: Microsoft Project)
- Supply Chain Management Software. This software helps to manage the flow of goods from the supplier to the customer. (eg: Oracle Supply Chain Management)
- Inventory Management Software. This software helps to track and manage inventory in warehouses or other locations. (eg: Fishbowl)
- Material Requirement Planning Software. This software helps to plan and manage the materials needed for production. (eg: SAP MRP)
- Data Analysis Tool. This tool helps to analyse and interpret data in order to make informed decisions. (eg: Tableau)
- Document Management Software. This software helps to store, manage and share documents and other files securely. (eg: Microsoft SharePoint)
Professional Organizations to Know
- Material Handling Equipment Distributors Association (MHEDA)
- American Supply Association (ASA)
- International Warehouse Logistics Association (IWLA)
- Institute of Supply Chain Management (ISM)
- Material Handling Industry of America (MHIA)
- Material Handling Education Foundation (MHEFI)
- National Association of Purchasing Management (NAPM)
- American Production and Inventory Control Society (APICS)
- National Council of Examiners for Engineering and Surveying (NCEES)
- American Society of Mechanical Engineers (ASME)
We also have Materials Coordinator, Raw Materials Specialist, and Materials Program Manager jobs reports.
Common Important Terms
- Bill of Materials (BOM). An itemized list of components that are required to manufacture a product.
- Procurement. The process of obtaining goods or services from an external source, usually at the best price and quality available.
- Demand Planning. The process of forecasting future customer demand and aligning inventory with that demand.
- Inventory Management. The process of tracking and managing inventory levels to ensure there is enough product to meet customer demand.
- Supply Chain. The network of suppliers and customers that provide the necessary materials and products to create a product or service.
- Project Management. The process of planning and executing projects within an organization in order to achieve a specific goal.
- Capacity Planning. The process of planning for the right amount of resources and capacity to meet future demand.
Frequently Asked Questions
What is Materials Scheduler?
Materials Scheduler is a software tool used for planning, scheduling and managing materials resources. It helps organizations to optimize their supply chain and improve operational efficiency.
What features does Materials Scheduler offer?
Materials Scheduler offers a range of features, including inventory tracking, demand forecasting, material requirements planning (MRP), vendor management, production scheduling, and more.
What are the benefits of using Materials Scheduler?
Benefits of using Materials Scheduler include improved inventory management, better production planning, reduced costs, improved customer service, and increased visibility into material supply chains.
Does Materials Scheduler integrate with other systems?
Yes, Materials Scheduler can be integrated with other systems such as enterprise resource planning (ERP) software, warehouse management systems (WMS), customer relationship management (CRM) systems, and more.
What type of organizations can use Materials Scheduler?
Materials Scheduler is used by companies in various industries, including manufacturing, distribution, retail, and logistics. It is suitable for organizations of all sizes, from small businesses to large enterprises.
What are jobs related with Materials Scheduler?
- Materials Planner
- Materials Technician
- Materials Buyer
- Materials Quality Control Inspector
- Finished Materials Inspector
- Materials Supervisor
- Advanced Materials Engineer
Web Resources
- MATERIAL SCHEDULE FORMAT (edited) www.academia.edu
- Scheduler Training Materials - Office of Class Management classroom.fiu.edu
- What is Materials Science and Engineering? mse.washington.edu
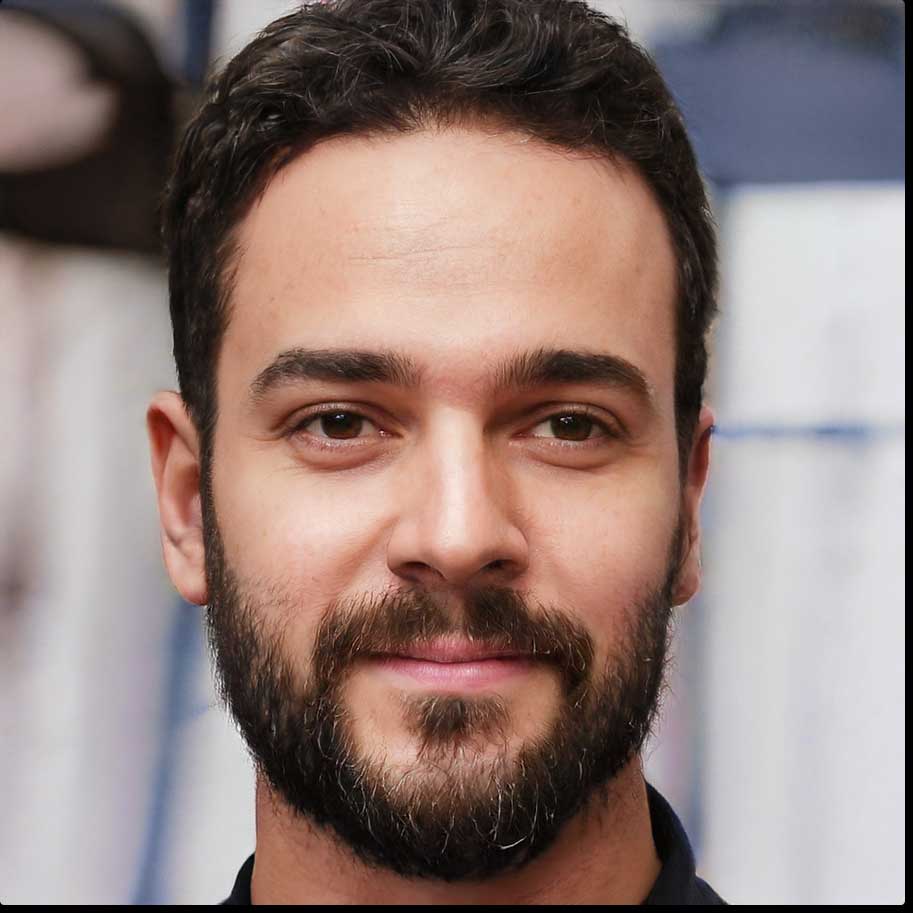