How to Be Materials Planner - Job Description, Skills, and Interview Questions
When a business is unable to plan and manage their materials, it can cause significant disruption in their supply chain. A Materials Planner helps to prevent this by ensuring that the right materials are ordered in the right amounts at the right time. They analyze the production needs and forecast demand, monitor stock levels, and coordinate the procurement of materials.
This helps to ensure that the business has adequate inventory to meet production requirements, while also avoiding overstocking materials and incurring additional costs. The Materials Planner plays a critical role in maintaining the supply chain's efficiency and effectiveness and is essential for businesses to remain competitive.
Steps How to Become
- Obtain a high school diploma or GED. Many employers require materials planners to have a high school diploma or GED.
- Pursue a college degree. A bachelor's degree in supply chain management, logistics, business administration or a related field is beneficial for materials planning positions. Coursework should include inventory control and management, logistics, and project management.
- Consider pursuing an internship. Internships provide practical experience and can help you build relationships within the industry.
- Obtain certifications. Certification in supply chain management or logistics can demonstrate your knowledge and skills in the field.
- Gain experience in materials planning. Many materials planners come to the profession with experience in procurement, logistics, inventory control and distribution management.
- Take advantage of professional development opportunities. Professional development opportunities such as seminars and workshops can help build your knowledge of the latest materials planning techniques and technology.
- Develop strong communication skills. Materials planners must be able to communicate effectively with vendors, suppliers and other internal departments.
A successful Materials Planner must stay informed and efficient in order to maintain an accurate inventory. Keeping up with current trends and technology, researching new suppliers, and utilizing modern inventory management systems are all essential components to staying on top of the materials planning process. An effective Materials Planner should also be organized, detail-oriented and able to multitask in order to remain on top of their workload.
In addition, a Materials Planner needs to have excellent communication skills in order to communicate their needs to other departments and build relationships with suppliers. By staying on top of the latest trends and utilizing the right tools, a Materials Planner will be able to keep their inventory up-to-date and ensure the best possible outcome for their organization.
You may want to check Materials Inventory Clerk, Materials Program Manager, and Materials Manager for alternative.
Job Description
- Research and analyze inventory needs and availability, and create purchase requisitions.
- Maintain and update inventory records and reports.
- Monitor inventory levels and identify potential shortages or excesses.
- Track and expedite vendor orders.
- Work with vendors to negotiate prices and delivery times.
- Manage the cycle counting process to ensure accuracy of inventory records.
- Utilize MRP (Material Requirements Planning) system to generate material orders.
- Generate and analyze inventory reports, such as stock status reports, slow-moving inventory reports, and aged inventory reports.
- Collaborate with internal departments to optimize supply chain processes.
- Recommend solutions for improving inventory management procedures.
Skills and Competencies to Have
- Knowledge of production planning principles and practices
- Understanding of inventory management
- Ability to analyze and interpret data
- Excellent organizational and problem-solving skills
- Ability to work independently and in a team environment
- Knowledge of supply chain management
- Ability to effectively communicate with internal departments and external vendors
- Proficiency with computer software such as MS Word, Excel, Access, etc.
- Attention to detail and accuracy
- Ability to develop and maintain relationships with suppliers
Effectively planning materials is essential for any business that relies on the availability of supplies to complete operations. Without a materials planner, companies may face delays or shortages of essential items, which can lead to lost profits and other negative outcomes. An effective materials planner must possess a variety of skills, including strong organizational abilities, excellent communication skills, and the ability to think proactively.
The planner must be able to anticipate future needs and plan for them accordingly. They must also have the ability to identify potential issues, such as supply chain interruptions, and suggest solutions to prevent them from occurring. Furthermore, the materials planner must have a deep understanding of industry trends, as this can help them anticipate demand and adjust their plans accordingly.
An effective materials planner is the key to ensuring that a business has the necessary materials available when needed.
Materials Handler, Materials Supervisor, and Materials Technician are related jobs you may like.
Frequent Interview Questions
- What experience do you have in materials planning?
- How would you ensure that all materials needed for production are available on time?
- Describe your experience with creating, maintaining and updating inventory systems.
- How would you manage the complex relationships between suppliers, customers and production managers?
- How do you stay up to date with new technologies in materials planning?
- How would you handle a situation when supplier delivery times conflict with customer demand?
- What strategies do you use to reduce inventory costs?
- How do you decide which items need to be stocked based on their usage rate?
- How do you handle unexpected changes in production schedules or orders?
- How do you handle a situation in which demand exceeds supply?
Common Tools in Industry
- Supply Chain Management System. This is a system used to track and manage the flow of materials and goods from supplier to customer. Example: Oracle Supply Chain Management.
- Project Management Software. This is a software used to coordinate and plan tasks, resources and timelines for projects. Example: Trello.
- MRP Software. This is a software used to optimize the production process and plan inventory levels. Example: SAP ERP.
- Inventory Management Software. This is a software used to track and take control of inventory levels in warehouses and stores. Example: Zoho Inventory.
- Forecasting Software. This is a software used to predict demand for materials, products and services. Example: Anaplan.
- Business Intelligence Solutions. This is a suite of tools used to analyze data from multiple sources and make informed decisions. Example: Tableau.
Professional Organizations to Know
- Association for Supply Chain Management (ASCM)
- International Society of Logistics (SOLE)
- National Association of Purchasing Management (NAPM)
- American Production and Inventory Control Society (APICS)
- Material Handling Industry of America (MHIA)
- Institute of Supply Management (ISM)
- Institute for Supply Chain Management (ISM-UK)
- Chartered Institute of Procurement & Supply (CIPS)
- International Association of Materials Management (IAMM)
- Logistics & Supply Chain Management Professionals (LSCMP)
We also have Materials Sales Representative, Materials Buyer, and Recycled Materials Coordinator jobs reports.
Common Important Terms
- Materials Requirement Planning (MRP). A process that uses software to plan and schedule the purchase, delivery and production of materials in an efficient and cost-effective manner.
- Bills of Material (BOM). A list of all the components, assemblies, and parts that make up a larger product.
- Capacity Planning. Process of determining the amount of resources (people, machines, equipment, etc. ) needed to meet production goals.
- Just-in-Time (JIT). A management philosophy that strives to reduce inventory levels by scheduling materials and products to arrive just when they are needed in the production process.
- Inventory Management. The process of tracking and ordering materials to ensure that the right amount is available at the right time.
- Vendor Managed Inventory (VMI). Process in which a company's suppliers are responsible for managing the inventory of items used by the company.
- Kanban. A system for tracking and managing inventory levels using visual cards or containers.
Frequently Asked Questions
What is Materials Planner?
Materials Planner is a supply chain management software used to optimize the procurement and inventory management process. It helps organizations manage their inventory levels, supplier relationships, and purchase orders.
What are the key features of Materials Planner?
Materials Planner offers a variety of features, including demand forecasting, order optimization, integrated supplier management, vendor rating systems, inventory tracking, and cost analysis.
How does Materials Planner help organizations improve their procurement process?
Materials Planner helps organizations reduce costs, streamline the ordering process, and improve visibility into supplier performance. It also provides insights into inventory levels and demand forecasting to help organizations make informed decisions about their procurement plans.
What is the pricing model for Materials Planner?
Materials Planner offers a subscription-based pricing model with a per-user fee and an annual license fee. Additional services such as implementation and training may also be available for an additional cost.
What types of organizations can benefit from using Materials Planner?
Materials Planner is designed to help businesses of all sizes improve their procurement process. It can be used by manufacturers, distributors, retailers, and other organizations that require efficient and cost-effective purchasing and inventory management.
What are jobs related with Materials Planner?
- Raw Materials Specialist
- Materials Quality Control Inspector
- Finished Materials Inspector
- Materials Analyst
- Materials Accounting Clerk
- Materials Scheduler
- Advanced Materials Engineer
Web Resources
- Materials Planner Career Advising & Professional Development capd.mit.edu
- (PDF) Material Requirements Planning - Academia.edu www.academia.edu
- Material Planner at Honda Aircraft Company - UC Berkeley IEOR ... ieor.berkeley.edu
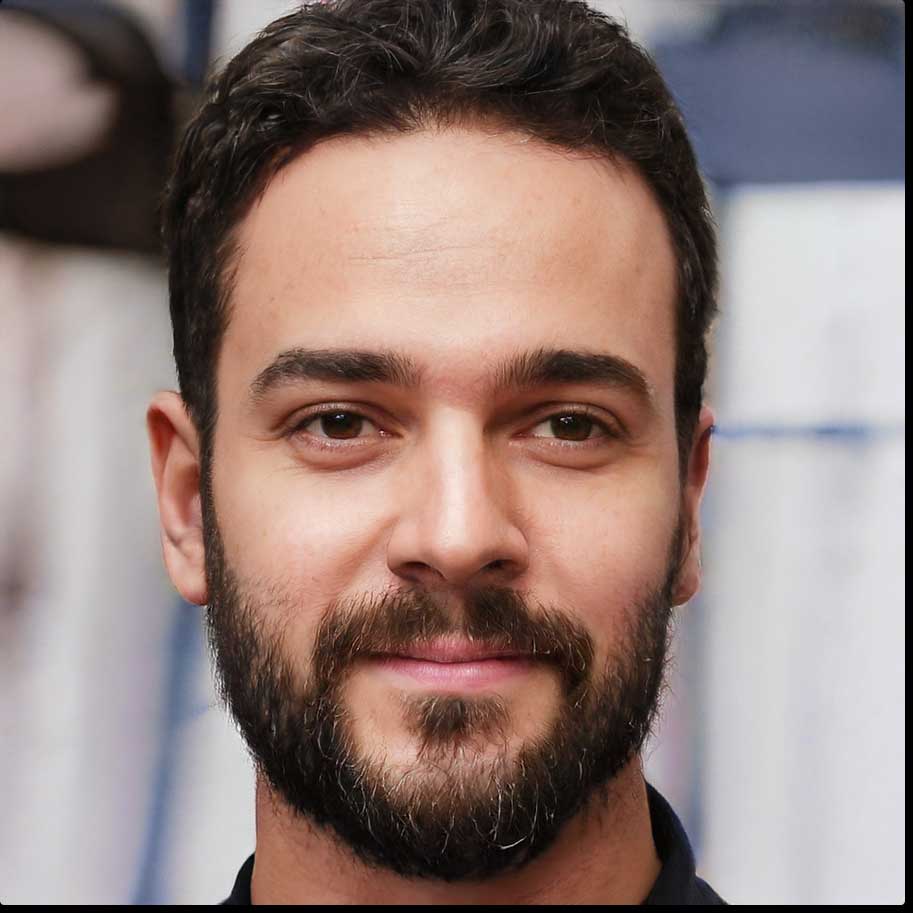