How to Be Materials Program Manager - Job Description, Skills, and Interview Questions
The success of a Materials Program Manager depends heavily on their ability to accurately forecast material needs and develop timely and cost-efficient supply chains. Poor forecasting can lead to inadequate supply, resulting in project delays, increased costs, and dissatisfied customers. having an efficient supply chain management strategy is key to minimizing costs, improving customer service, and ensuring timely delivery of materials to the end user.
An effective Materials Program Manager should possess strong analytical and organizational skills to successfully manage resources, analyze market trends, identify new suppliers, and maintain long-term relationships with vendors. With these skills, they can ensure the successful operation of the supply chain and strengthen their organization's competitive advantage.
Steps How to Become
- Obtain a Bachelor's Degree. To become a materials program manager, you must have a bachelor's degree in engineering or a related field. Additionally, some employers may require a master's degree in business administration or engineering.
- Get Relevant Experience. Most employers require materials program managers to have several years of experience in the field. Consider getting an entry-level job in the materials engineering field to gain experience.
- Develop Leadership Skills. A successful materials program manager needs to have strong leadership and team management skills. Consider taking classes in management, project management, and communication to hone your skills.
- Become Certified. Materials program managers may consider becoming certified by organizations such as the American Society for Quality or the American Production and Inventory Control Society.
- Obtain a Position. Once you have the necessary qualifications, you can start job searching for materials program manager positions. Check out job boards and online job search engines to find available positions.
You may want to check Materials Supervisor, Materials Analyst, and Finished Materials Inspector for alternative.
Job Description
- Develop, implement and manage materials programs in support of business objectives
- Oversee and manage the procurement of materials and services, ensuring that quality and cost goals are met
- Analyze and monitor materials usage to identify opportunities for cost savings or process improvements
- Maintain accurate records of materials inventory, usage and cost
- Negotiate contracts with suppliers and service providers to ensure cost-effectiveness
- Monitor supplier performance and ensure compliance with agreements
- Research, select and purchase materials, components, supplies and services as required
- Work with engineering and production teams to identify and implement cost-saving and process improvement initiatives
- Monitor material costs, availability and lead times to minimize disruption of production schedules
- Develop and maintain relationships with suppliers to ensure quality and timely delivery
- Evaluate supplier performance, ensuring that the highest quality standards are maintained
- Manage the disposal of obsolete materials and components in a cost-effective manner
- Provide training and support to personnel on proper materials management procedures
- Develop and maintain reporting systems to track materials usage, cost and performance
Skills and Competencies to Have
- Knowledge of material management principles and practices
- Proficiency in inventory management and scheduling
- Expertise in cost control and budgeting
- Excellent communication, interpersonal and organizational skills
- Strong problem-solving, analytical and decision-making abilities
- Ability to manage multiple projects simultaneously
- Proficiency in computer programs related to materials and inventory management
- Knowledge of relevant safety regulations and standards
- Ability to form effective partnerships with vendors and suppliers
- Understanding of logistics and supply chain management concepts
Effective program management is essential for successful materials programs. Effective program managers must possess a wide array of skills including leadership, communication, problem solving, and organizational abilities. Without these skills, materials programs will not reach their goals.
Leadership is critical for setting direction and inspiring individuals to take action. Communication is necessary for keeping stakeholders informed, motivating teams, and making sure everyone is on the same page. Problem solving is important for identifying potential issues and finding solutions in a timely manner.
Finally, organizational skills are essential for ensuring that resources are allocated properly and that deadlines are met. When these four skills are combined, materials programs are more likely to succeed.
Materials Sales Representative, Materials Manager, and Materials Accounting Clerk are related jobs you may like.
Frequent Interview Questions
- What experience do you have in managing materials programs?
- How have you used data analytics to improve the performance of materials programs?
- What challenges have you faced in managing materials programs?
- How do you ensure that materials program deadlines are met?
- Describe your experience with negotiating contracts with vendors and suppliers.
- What strategies have you employed to ensure that materials programs remain cost-effective?
- How have you managed the relationship between vendors and internal stakeholders?
- What steps have you taken to develop and implement successful materials programs?
- Describe a time when you had to solve a complex problem related to materials programs.
- How do you stay current with industry trends and best practices related to materials programs?
Common Tools in Industry
- Microsoft Project. Project management software that helps teams track tasks, resources, and timelines. (eg: Tracking the progress of a software development project)
- Primavera P6. Project planning software for scheduling and resource management. (eg: Creating a project timeline and resource allocation plan)
- Microsoft Excel. Spreadsheet software for collecting, analyzing, and presenting data. (eg: Creating a project budget)
- JIRA. Issue tracking and project management software for teams. (eg: Tracking and managing customer support requests)
- SharePoint. Collaboration software for storing, organizing, and sharing documents. (eg: Sharing product specifications with team members)
- Lucidchart. Online diagramming and flowcharting tool for creating visual diagrams. (eg: Mapping out a process flow for a manufacturing line)
- Asana. Project management software for tracking tasks and assigning work to team members. (eg: Assigning tasks to a team working on a research project)
- Smartsheet. Collaborative work management platform for organizing projects in a spreadsheet layout. (eg: Creating a Gantt chart for tracking deadlines)
Professional Organizations to Know
- American Institute of Materials Management (AIMM)
- Association for Operations Management (APICS)
- International Association of Materials Management (IAMM)
- National Association of Purchasing Management (NAPM)
- Council of Supply Chain Management Professionals (CSCMP)
- Supply Chain Management Association (SCMA)
- Society for Maintenance and Reliability Professionals (SMRP)
- Institute for Supply Management (ISM)
- International Supply Chain Education Alliance (ISCEA)
- American Society for Quality (ASQ)
We also have Materials Coordinator, Advanced Materials Engineer, and Materials Quality Control Inspector jobs reports.
Common Important Terms
- Materials Requirement Planning (MRP). A system used to manage the procurement and inventory of materials used in the production process. It tracks and plans for the exact amount of materials needed to meet customer orders.
- Inventory Management. The process of tracking and managing the amount of inventory on hand, including order fulfillment and storage.
- Purchasing. The process of selecting and acquiring goods and services to meet organizational needs.
- Quality Control. The process of monitoring and evaluating the quality of products and services to ensure they meet customer requirements.
- Supply Chain Management. The process of managing the supply chain to ensure efficient flow of materials, products, and services from suppliers to customers.
- Logistics Management. The process of managing the transportation and storage of materials, products, and services from suppliers to customers.
- Warehousing. The process of storing materials, products, and services in an organized manner for easy retrieval and distribution.
Frequently Asked Questions
What is a Materials Program Manager?
A Materials Program Manager is responsible for leading and managing the planning, acquisition, and control of materials and services necessary for production. This includes managing the purchasing, inventory, and supply chain processes.
What are the main duties of a Materials Program Manager?
The main duties of a Materials Program Manager include developing materials strategies, negotiating contracts, managing supplier relationships, monitoring inventory levels, and overseeing logistics operations.
What qualifications are needed to become a Materials Program Manager?
To become a Materials Program Manager, you should have a bachelor's degree in business, supply chain management, or a related field. Experience in materials management is also beneficial.
What skills do Materials Program Managers need?
Materials Program Managers need strong interpersonal and communication skills, problem solving abilities, leadership and organizational skills, as well as knowledge of industry-specific software and processes.
What is the average salary of a Materials Program Manager?
According to PayScale, the average salary of a Materials Program Manager is around $75,000 per year.
What are jobs related with Materials Program Manager?
- Materials Handler
- Raw Materials Specialist
- Materials Buyer
- Materials Planner
- Recycled Materials Coordinator
- Materials Inventory Clerk
- Materials Scheduler
Web Resources
- Hazardous Materials Program Manager TEAMS Titles teams-titles.hr.ufl.edu
- Materials Management | Georgia College & State University www.gcsu.edu
- What is Materials Management in logistics? - SCM EDU scmedu.org
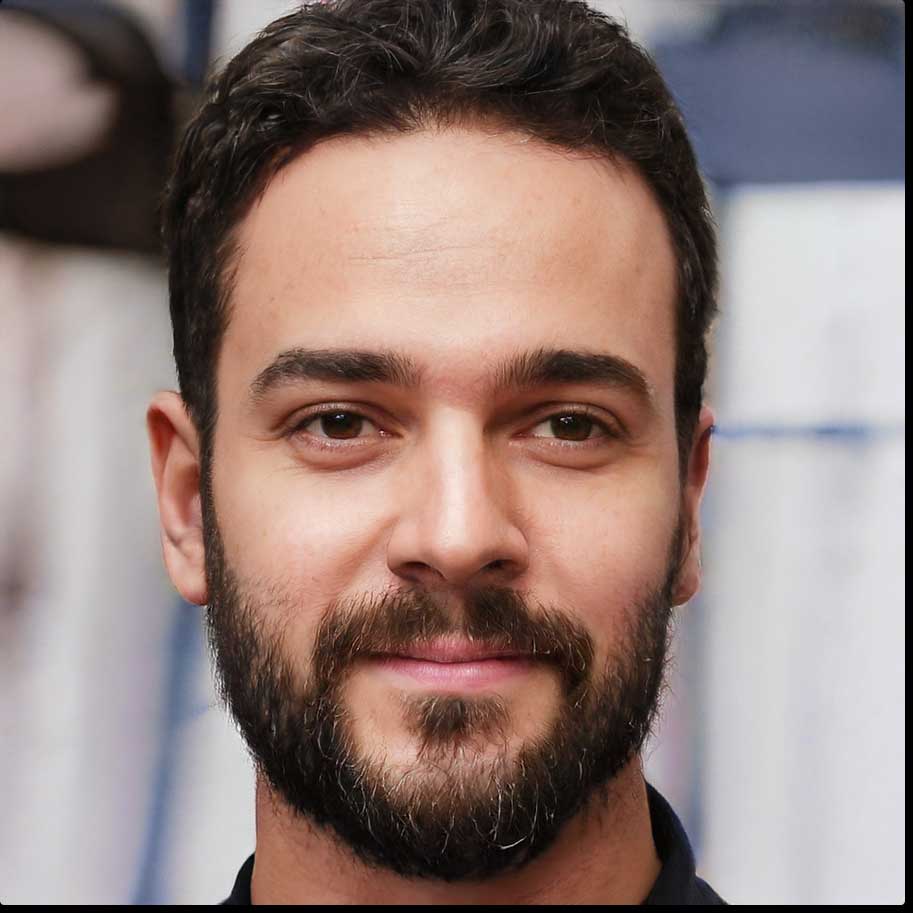