How to Be Materials Accounting Clerk - Job Description, Skills, and Interview Questions
The Accounting Clerk ensures that the company is accurately accounting for all material purchases and sales. By performing this role, they are responsible for the successful management of the company's inventory and supply chain. This is achieved through accurate data entry and tracking of inventory, orders, and invoices, as well as verifying customer data and balances.
In addition, this role ensures that accurate financial records are kept and that items are being purchased for the correct prices. When this is done correctly, it can help to reduce costs, improve customer service, and increase overall efficiency. As a result, it helps to ensure the company's profitability and sustainability.
Steps How to Become
- Earn a High School Diploma or GED. Most employers will not consider candidates for a materials accounting clerk position without a high school diploma or GED.
- Consider Postsecondary Training. Although it is not required, some employers may prefer to hire materials accounting clerks with postsecondary training in accounting or bookkeeping.
- Pursue On-the-Job Training. Most employers will provide on-the-job training for materials accounting clerks. Employees will typically learn how to use the employer's accounting system, as well as how to properly record incoming and outgoing materials.
- Earn Certification. Those who want to gain an advantage over other job candidates may want to consider earning voluntary certification from organizations such as the Institute of Certified Professional Managers.
- Consider Additional Certifications. Materials accounting clerks who work in specific industries, such as healthcare, may need to earn additional certifications related to their job duties. For example, a materials accountant who works in a hospital setting may need to obtain certification in medical coding.
Having a reliable and capable Accounting Clerk is essential for any business. Proper accounting and tracking of materials is critical to ensure that the companys financial records are up-to-date and accurate. Without a reliable Accounting Clerk, businesses can risk inaccurate bookkeeping, leading to costly errors and potential fines.
having an experienced Accounting Clerk can help the business save money by reducing the amount of time it takes to complete tasks, while also ensuring that proper procedures are followed. Furthermore, an Accounting Clerk with the right qualifications and experience can help the business remain compliant with applicable laws and regulations. When businesses invest in a reliable and capable Accounting Clerk, they can benefit from more accurate financial records, improved efficiency, cost savings, and compliance with applicable laws and regulations.
You may want to check Materials Scheduler, Materials Program Manager, and Materials Quality Control Inspector for alternative.
Job Description
- Maintain accurate records of all materials received and issued, including invoices, purchase orders and stock inventories.
- Reconcile discrepancies in inventory and identify causes.
- Monitor material levels and report shortages to purchasing or production departments.
- Enter material data into accounting software and generate reports.
- Prepare documents for material returns, exchanges and credits.
- Assist in the preparation of cost analyses and other financial reports.
- Prepare material invoices for payment.
- Collect and analyze data to identify trends in materials usage.
- Perform periodic cycle counts of material inventory and reconcile results with system records.
- Assist with budget preparation and other projects as assigned.
Skills and Competencies to Have
- Knowledge of accounting principles, procedures and practices
- Ability to accurately enter financial data into accounting systems
- Familiarity with standard office equipment and computer software related to accounting
- Excellent organizational and multitasking skills
- Ability to work independently and manage time effectively
- Strong written and verbal communication skills
- Attention to detail and problem-solving skills
- Ability to maintain confidentiality of sensitive information
- Knowledge of pertinent laws, regulations, and standards
- Understanding of inventory management principles
One of the most important skills for an Accounting Clerk to have is excellent time management. By managing their time effectively, Accounting Clerks can ensure that all materials and resources are accounted for accurately and promptly. This can help prevent any errors or delays that may occur if tasks are not done in a timely manner.
In addition, having strong organizational skills is also necessary, as it allows Accounting Clerks to efficiently keep track of numerous documents and other materials. With strong organizational skills, they can ensure that all records are up to date and accurate, helping to prevent any discrepancies or inaccuracies that could arise due to lack of organization. Finally, having a solid understanding of accounting principles and procedures is essential for an Accounting Clerk to be successful.
By having a good understanding of the accounting process and how it works, they can better ensure that all financial transactions are recorded properly and accurately.
Raw Materials Specialist, Materials Planner, and Recycled Materials Coordinator are related jobs you may like.
Frequent Interview Questions
- What experience do you have working in materials accounting?
- How do you handle the reconciliation of inventory transactions?
- What methods would you use to track and analyze inventory levels?
- How would you handle a situation where inventory counts and records dont match?
- What processes do you follow to ensure accurate inventory and cost records?
- How do you maintain accurate records and accounts for inventory items?
- Are you familiar with common industry software/systems used for materials accounting?
- What strategies do you use to optimize inventory levels and reduce costs?
- How do you ensure accuracy in your data entry and other materials accounting tasks?
- How do you ensure that all materials accounting tasks are completed on time and accurately?
Common Tools in Industry
- Accounting Software. used to track and manage financial transactions (example: Quickbooks).
- Spreadsheet Software. used to create and manage numerical data (example: Microsoft Excel).
- Database Software. used to store and access large amounts of data (example: Microsoft Access).
- Barcode Scanner. used to scan barcodes to capture data (example: Motorola DS6878).
- Inventory Management System. used to track and manage inventory levels (example: Fishbowl Inventory).
- Point of Sale System. used to track sales transactions (example: Square Register).
- Accounting Ledger. used to record financial transactions (example: General Ledger).
Professional Organizations to Know
- Institute of Management Accountants (IMA)
- Association for Financial Professionals (AFP)
- National Association of Credit Management (NACM)
- American Production and Inventory Control Society (APICS)
- Institute of Chartered Accountants in England and Wales (ICAEW)
- American Accounting Association (AAA)
- Financial Executives International (FEI)
- Chartered Institute of Management Accountants (CIMA)
- Institute of Internal Auditors (IIA)
- Association of Certified Fraud Examiners (ACFE)
We also have Materials Manager, Materials Technician, and Materials Supervisor jobs reports.
Common Important Terms
- Inventory Management. The process of tracking and controlling the movement of materials within a company's inventory.
- Cost Accounting. An accounting methodology that tracks the costs associated with production, operations, and other activities.
- Stock Control. The practice of monitoring and managing the levels of stock in a companys inventory.
- Purchase Order. A document issued by a buyer to a seller, specifying the type, quantity, and agreed price for products or services the seller will provide to the buyer.
- Receiving. The process of verifying that the ordered goods have been delivered in good condition and are in line with the purchase order.
- Materials Handling. The process of safely and efficiently moving materials from one location to another.
- Supplier Relations. The process of managing relationships between a company and its suppliers to ensure that materials are delivered on time and at the best price possible.
- Quality Control. The practice of ensuring that materials meet prescribed standards of quality before they are accepted into inventory.
Frequently Asked Questions
What is the primary responsibility of a Materials Accounting Clerk?
The primary responsibility of a Materials Accounting Clerk is to track and maintain inventory records, ensuring that all materials are properly accounted for and documented.
What types of materials are tracked and maintained by a Materials Accounting Clerk?
A Materials Accounting Clerk typically tracks and maintains records for raw materials, finished goods, and supplies used in production.
What type of information is typically included in materials accounting records?
Materials accounting records typically include information such as quantity, cost, vendor, date of purchase, and other relevant information related to the materials being tracked.
How often does a Materials Accounting Clerk need to update the inventory records?
The frequency of updates to inventory records will vary depending on the specific business needs, but generally should be done on a daily or weekly basis.
How does a Materials Accounting Clerk ensure accuracy of inventory records?
A Materials Accounting Clerk can ensure accuracy of inventory records by performing regular audits and reviews of the records, as well as by comparing them to physical inventory counts.
What are jobs related with Materials Accounting Clerk?
- Materials Handler
- Materials Coordinator
- Materials Analyst
- Advanced Materials Engineer
- Materials Sales Representative
- Finished Materials Inspector
- Materials Buyer
Web Resources
- Accounting - Clark College www.clark.edu
- Accounting Clerk - Illinois Central College - Academics icc.edu
- Accounting Clerk (CP)(Plan Code: ATBACC45) < Clark College catalog.clark.edu
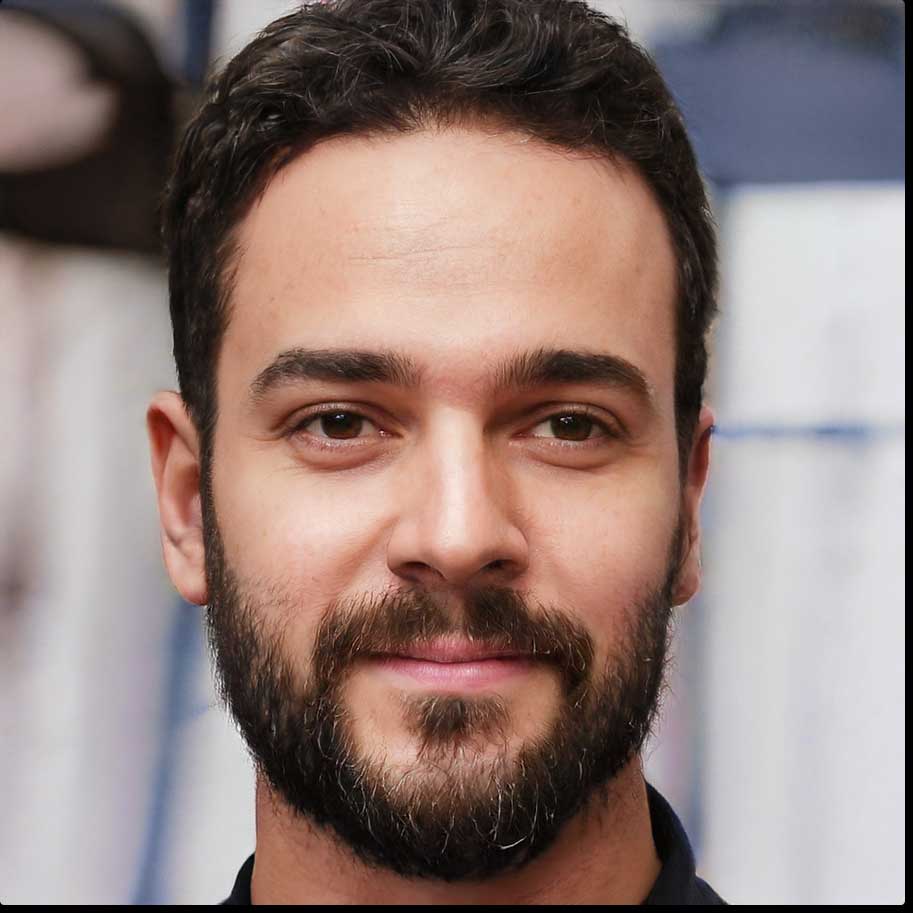