How to Be Materials Inventory Clerk - Job Description, Skills, and Interview Questions
The role of an Inventory Clerk is vital to the success of any company that relies on a steady supply of materials and products. This position plays a key role in ensuring that materials are ordered in a timely manner and received as expected. By ensuring that the right amount of materials are available when needed, the Inventory Clerk helps to prevent costly delays and increases efficiency.
this position helps to reduce overhead costs by preventing unnecessary over-ordering, as well as tracking inventory levels to ensure that materials and products are not lost or wasted. In essence, an effective and efficient Inventory Clerk is critical to the success of any organization that relies on the timely delivery and availability of materials and products.
Steps How to Become
- Obtain a High School Diploma or GED. To become a materials inventory clerk, you need to have a high school diploma or GED. This is the minimum requirement for most entry-level positions.
- Receive On-the-Job Training. Many employers provide on-the-job training to their new inventory clerks. During this training, you will learn how to use the company's inventory software and other operational procedures.
- Consider Earning a Certificate. Some employers may prefer that you have a certificate in materials inventory management. You can earn this certificate by taking classes at a community college or through an online program.
- Obtain Experience. The more experience you have working with inventory systems, the better your job prospects will be. Consider seeking out internships or volunteer positions at warehouses or retail stores to gain experience.
- Maintain Certification. After you have earned your certificate, make sure that you keep it up to date. Many employers require their inventory clerks to maintain their certifications in order to stay employed.
The key to becoming a skilled and efficient inventory clerk is to have a good understanding of the inventory process. This involves tracking all items that are delivered, ensuring they are accurately entered into the system, and staying organized. Doing this efficiently requires a good grasp of the inventory software, as well as keeping up-to-date records, such as stock levels, ordering and shipping details.
By staying organized and having a thorough understanding of the inventory process, it is possible to maintain efficient inventory levels and optimize the organizations resources. This will in turn lead to cost savings and improved customer service.
You may want to check Raw Materials Specialist, Materials Technician, and Materials Buyer for alternative.
Job Description
- Receive, store and issue materials, supplies, tools and equipment in accordance with established inventory control procedures.
- Maintain records of material quantities, types and values in manual or computerized inventory system.
- Inspect incoming materials for quality, quantity and conformance to specified requirements.
- Set up and maintain files on inventory items, including price lists, vendor information and related data.
- Ensure accuracy of inventory records by comparing physical counts of stock to computer-generated reports.
- Monitor stock levels and advise management on reordering levels of inventory items.
- Prepare reports on inventory activity, shortages, discrepancies and other related matters.
- Participate in physical inventories, including counting and verifying stock on hand.
- Coordinate the transfer of materials to and from other departments or facilities.
- Respond to inquiries from internal and external customers concerning availability of inventory items.
Skills and Competencies to Have
- Knowledge of inventory tracking systems and software.
- Demonstrated ability to accurately track and reconcile inventory records.
- Ability to visually inspect and verify physical inventory.
- Strong organizational and problem solving skills.
- Excellent communication and interpersonal skills.
- Attention to detail and accuracy in all work activities.
- Ability to work independently and as part of a team.
- Ability to lift and move items weighing up to 50 pounds.
- Proficiency in Microsoft Office Suite, including Excel and Access.
- Familiarity with barcode scanners, RF systems, and other automated inventory control systems.
Having good organizational skills is essential for an Inventory Clerk to be successful. Its important to be able to properly organize and track materials and supplies in order to prevent unnecessary delays or costly errors. An effective Inventory Clerk is also able to prioritize tasks and stay focused on their goals, ensuring that all inventory is updated in a timely manner.
They must also be able to accurately record and report any discrepancies in inventory, as well as identify and resolve any supply chain issues. By having the necessary organizational and communication skills, an Inventory Clerk can ensure that materials are properly managed, which leads to a smoother flow of operations, higher customer satisfaction, and improved profitability for the company.
Materials Handler, Advanced Materials Engineer, and Materials Coordinator are related jobs you may like.
Frequent Interview Questions
- What experience do you have in materials inventory management?
- How do you stay organized when tracking and managing inventory?
- Describe a time when you had to prioritize multiple tasks related to material inventory.
- What challenges have you faced while working with inventory in a warehouse or manufacturing environment?
- How do you stay up to date on industry trends and technologies related to materials inventory?
- What strategies do you use to ensure accuracy in inventory tracking and management?
- How do you handle unexpected changes in the inventory levels?
- Describe your experience with using software systems to track and monitor materials inventory.
- What metrics do you use to measure the success of material inventory management projects?
- What processes do you use to keep track of vendor orders and deliveries?
Common Tools in Industry
- Barcode Scanner. A device used to read barcodes (eg: Honeywell Voyager 1202g).
- Barcode Printer. A device used to print barcodes (eg: Zebra Technologies GK420d).
- Stock Management Software. Software used to track inventory levels and orders (eg: Fishbowl Inventory).
- Label Maker. A device used to create labels for items (eg: Dymo LabelWriter 450 Twin Turbo).
- Inventory Tracking System. A system used to track all inventory items and their status (eg: Brightpearl).
- Shipping Software. Software used to manage orders, shipments, and returns (eg: ShipStation).
- Weigh Scale. A device used to weigh packages (eg: My Weigh iBalance 7001).
- RFID Reader/Writer. A device used to read and write radio-frequency identification tags (eg: Impinj Speedway Revolution).
- Warehouse Management System. A system used to manage the activities of a warehouse (eg: SAP Extended Warehouse Management).
- Pick-to-Light System. A system used to help warehouse staff quickly locate and pick items (eg: Kardex Remstar Shuttle XP).
Professional Organizations to Know
- Association for Supply Chain Management (ASCM)
- International Federation of Purchasing and Supply Management (IFPSM)
- American Purchasing Society (APS)
- International Association of Inventory Management (IAIM)
- Institute for Supply Management (ISM)
- National Association of Purchasing Management (NAPM)
- National Inventory and Materials Management Society (NIMMS)
- Chartered Institute of Procurement and Supply (CIPS)
We also have Recycled Materials Coordinator, Materials Analyst, and Materials Manager jobs reports.
Common Important Terms
- Inventory Management. The process of controlling and tracking the flow of goods, from the supplier to the customer.
- Stock Taking. The process of counting and recording the number of items on hand in an inventory.
- Cycle Counting. The process of periodically counting a subset of items in stock to ensure that the inventory records are accurate.
- Bin Location. A physical location or place where an item is stored in an inventory system.
- Reordering Point. The inventory level at which an item needs to be reordered to prevent stock outs.
- Safety Stock. The extra inventory held to protect against unexpected events, such as an increase in demand or a delay in receiving the order from the supplier.
Frequently Asked Questions
What are the main duties of a Materials Inventory Clerk?
The main duties of a Materials Inventory Clerk include maintaining accurate records of material inventories, conducting regular stock checks, tracking orders and deliveries, and ordering new materials when necessary.
What skills do Materials Inventory Clerks need?
Materials Inventory Clerks need strong organizational and analytical skills, attention to detail, and the ability to use inventory software programs.
How often do Materials Inventory Clerks conduct stock checks?
Materials Inventory Clerks typically conduct regular stock checks to ensure accuracy of inventory records. The frequency of these stock checks may vary depending on the size of the organization.
What is the job outlook for Materials Inventory Clerks?
According to the Bureau of Labor Statistics, the job outlook for Materials Inventory Clerks is projected to grow 5% from 2019 to 2029.
What is the median salary for Materials Inventory Clerks?
The median annual salary for Materials Inventory Clerks is $39,890, according to the Bureau of Labor Statistics.
What are jobs related with Materials Inventory Clerk?
- Materials Quality Control Inspector
- Materials Supervisor
- Materials Program Manager
- Materials Planner
- Materials Scheduler
- Materials Sales Representative
- Finished Materials Inspector
Web Resources
- Inventory Control Clerk - Job Descriptions - Human Resources :: ¦ jobdescriptions.unm.edu
- Materials Science < Clark College catalog.clark.edu
- Clark College www.clark.edu
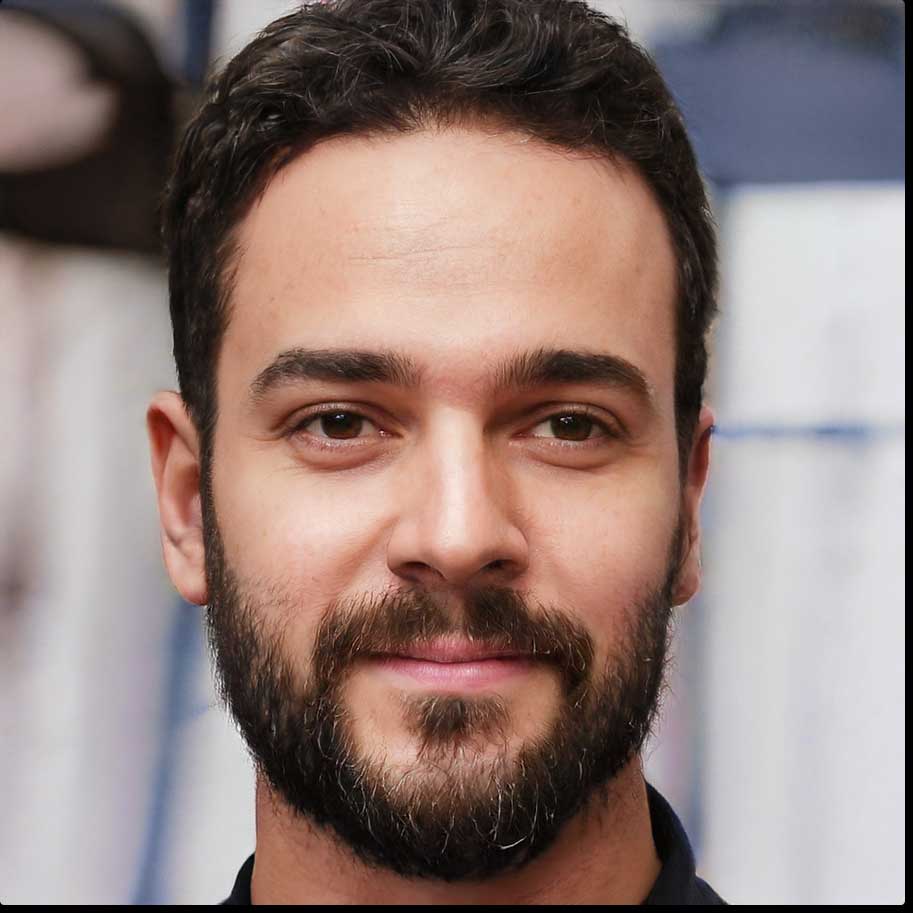