How to Be Maintenance Supervisor - Job Description, Skills, and Interview Questions
The lack of a maintenance supervisor can have a detrimental effect on a business. Without an experienced supervisor, technicians may not be trained properly and may lack the skills needed to properly maintain the company's equipment. This can lead to costly repairs and downtime, resulting in decreased productivity and revenue.
the absence of a maintenance supervisor can lead to a decrease in employee morale, as technicians may not feel supported or valued. In order to prevent these issues, it is essential for businesses to hire an experienced maintenance supervisor who can ensure that the company's equipment is well-maintained and that technicians are provided with the necessary training and resources.
Steps How to Become
- Earn a Bachelors Degree. Most employers prefer to hire maintenance supervisors who have a bachelors degree in a field related to engineering, construction management, or business.
- Obtain Relevant Experience. Most employers also require their maintenance supervisors to have at least five years of professional experience in a related field.
- Become Certified. Many employers prefer to hire maintenance supervisors who have earned certain certifications, such as the Certified Maintenance and Reliability Professional (CMRP) designation from the Society for Maintenance & Reliability Professionals (SMRP).
- Develop Technical Skills. Maintenance supervisors should have a strong understanding of mechanical and electrical systems, as well as knowledge of applicable codes and regulations. They should also be comfortable with computer systems and software used in facility management and maintenance.
- Get Familiar with Safety Protocols. Maintenance supervisors must be knowledgeable about safety protocols and procedures in order to ensure the safety of their staff and the facility. They should also be aware of any applicable regulations and laws related to safety.
- Develop Leadership Qualities. Maintenance supervisors must have strong leadership skills in order to effectively manage their staff, coordinate maintenance operations, and solve problems. They should also be able to communicate effectively and motivate their team members.
Maintenance supervisors must stay ahead of the curve and continue to qualify themselves to remain successful. To achieve this, they should regularly review industry trends and developments to gain insight into the latest advances in maintenance technology and practices. supervisors should take courses and attend seminars to stay up-to-date on relevant codes and standards, as well as safety and management best practices.
Finally, it is important for supervisors to build strong relationships with their peers in order to learn about new approaches and solutions in order to stay ahead of the competition. By taking these proactive steps, maintenance supervisors can ensure their success and remain qualified to do their job.
You may want to check Real Estate Investment Trust Analyst, Real Estate Investor, and Land Management Coordinator for alternative.
Job Description
- Develop and implement maintenance procedures and standards to ensure safety, quality, and efficiency.
- Monitor and inspect operations to ensure they conform to safety standards and government regulations.
- Schedule, coordinate, and supervise maintenance staff to ensure optimal use of resources.
- Monitor inventory of maintenance supplies and equipment and order new materials as needed.
- Diagnose mechanical and operational problems and perform necessary repairs and adjustments.
- Train and mentor maintenance staff on proper use of tools, equipment, and safety procedures.
- Develop preventative maintenance program to minimize downtime and improve overall efficiency.
- Diagnose electrical, hydraulic, pneumatic, and other systems, and recommend repairs or replacements as needed.
- Maintain records of activities, including work orders, preventive maintenance records, and parts used for repairs.
- Establish and maintain relationships with vendors for procurement of repair parts and services.
Skills and Competencies to Have
- Knowledge of repair and maintenance techniques
- Knowledge of safety regulations
- Ability to interpret technical manuals and diagrams
- Excellent mechanical skills
- Knowledge of building systems, such as HVAC, plumbing, and electrical
- Strong communication and interpersonal skills
- Ability to multitask and prioritize tasks
- Organizational and problem-solving skills
- Leadership and management skills
- Ability to work independently and as part of a team
- Computer proficiency with software applications, such as MS Office, AutoCAD, etc.
- Understanding of budgeting and cost control
Good maintenance supervisors need a broad range of skills to be successful. Chief among them is the ability to lead, motivate and direct the maintenance staff to ensure the smooth functioning of their department. Effective communication is also essential, as supervisors must be able to collaborate with other departments, issue directives, and explain complex technical information to their team.
Problem-solving is another critical skill, as they must be able to identify and address issues quickly and efficiently. Finally, a good maintenance supervisor also needs excellent organizational skills, as they must be able to plan and coordinate the activities of their staff and manage resources to ensure cost-effectiveness. With these skills in place, maintenance supervisors can help ensure the smooth running of their department, the efficiency of their staff, and the successful completion of projects.
Property Management Assistant, Property Administrator, and Rental Property Manager are related jobs you may like.
Frequent Interview Questions
- What experience do you have in the Maintenance Supervisor role?
- Describe your experience in managing maintenance staff and budgeting.
- How do you prioritize work orders and ensure timely completion?
- What strategies do you employ to ensure customer satisfaction?
- How do you handle difficult maintenance issues?
- What methods have you used to develop preventive maintenance programs?
- What is your experience with safety protocols?
- How do you ensure compliance with local, state, and federal regulations?
- How do you keep up with new technologies and industry trends?
- What has been your greatest accomplishment as a Maintenance Supervisor?
Common Tools in Industry
- Computerized Maintenance Management System (CMMS). A software used to manage maintenance tasks and resources, such as scheduling and tracking of maintenance activities, inventory and asset management. (e. g. SAP Plant Maintenance, IBM Maximo)
- Automated Data Collection System (ADCS). A system that can collect, store, and transmit data from various operational sources. (e. g. RFID systems, barcode scanners)
- Handheld Device. A mobile device such as a smartphone, tablet, or laptop used for data collection and analysis. (e. g. iPhone, iPad, Samsung Galaxy)
- Automated Testing Equipment. A device used to test the performance and condition of a product or system. (e. g. pressure gauges, temperature sensors)
- Building Management System (BMS). A system used to control and monitor environmental conditions in a building, such as air conditioning and lighting. (e. g. Honeywell Tridium, Siemens Desigo CC)
- Predictive Maintenance Software. Software that can detect potential problems in a machine before they occur. (e. g. Prediktiv, Reliability Solutions)
- Virtual Reality (VR) Technology. A computer-generated environment used for training and troubleshooting purposes. (e. g. Oculus Rift, HTC Vive)
Professional Organizations to Know
- American Society of Mechanical Engineers (ASME)
- Institute of Electrical and Electronics Engineers (IEEE)
- National Society of Professional Engineers (NSPE)
- American Society for Quality (ASQ)
- National Council for Examiners for Engineering and Surveying (NCEES)
- Association for Facilities Engineering (AFE)
- International Facility Management Association (IFMA)
- Professional Engineers in California Government (PECG)
- American Society of Civil Engineers (ASCE)
- American Welding Society (AWS)
We also have Tenant Relations Coordinator, Tenant Relations Manager, and Property Maintenance Worker jobs reports.
Common Important Terms
- Preventative Maintenance. A scheduled procedure or process designed to reduce the probability of failure or malfunction of equipment.
- Corrective Maintenance. A type of maintenance performed to restore a failed or malfunctioning piece of equipment to its original working condition.
- Predictive Maintenance. A strategy used to monitor the performance of a machine or system and detect any changes that may indicate a pending problem.
- Scheduled Maintenance. Planned maintenance activities that are performed on a regular basis in order to reduce the likelihood of equipment or system failure.
- Asset Management. The process of managing and optimizing the use of assets in an organization.
- Availability Management. The process of ensuring that assets are available when needed in order to meet business objectives.
- Reliability Engineering. A branch of engineering focused on developing and improving the reliability of machines, systems, and processes.
- Quality Management. The process of ensuring that products and services meet predetermined standards of quality.
- Risk Analysis. The analysis of potential risks associated with a given process or system in order to identify and mitigate them.
- Safety Management. The process of ensuring that safety procedures are followed and that potential hazards are identified and addressed in a timely manner.
Frequently Asked Questions
What qualifications are necessary to become a Maintenance Supervisor?
To become a Maintenance Supervisor, you typically need a minimum of a high school diploma or equivalent, as well as experience in the maintenance field. Some employers may also require a degree in engineering, industrial technology, or a related field.
What duties does a Maintenance Supervisor typically perform?
The primary duty of a Maintenance Supervisor is to manage and oversee the maintenance of buildings, equipment, and machinery. This includes coordinating repairs, preventive maintenance programs, and ensuring that safety standards are met.
What skills are necessary to excel as a Maintenance Supervisor?
To excel as a Maintenance Supervisor, you need excellent organizational and communication skills, as well as knowledge of safety procedures and regulations. You must also be able to work independently and be able to troubleshoot and repair complex mechanical systems.
What is the average salary of a Maintenance Supervisor?
The average salary of a Maintenance Supervisor is between $50,000-$70,000 per year, depending on the industry and location.
What types of work environments do Maintenance Supervisors typically work in?
Maintenance Supervisors typically work in industrial settings such as factories and warehouses. They may also work in hospitals, schools, and other commercial buildings.
What are jobs related with Maintenance Supervisor?
- Facilities Maintenance Technician
- Landlord/Property Manager
- Building Supervisor
- Lease Administrator
- Residential Leasing Manager
- Landlord
- Landlord Assistant
- Real Estate Agent/Property Manager
- Residential Property Manager
- Property Leasing Specialist
Web Resources
- What is a Maintenance Supervisor? | Goodwin University www.goodwin.edu
- Maintenance Supervisor NC State Continuing and Lifelong ¦ mckimmoncenter.ncsu.edu
- Maintenance Management Certificate Program - Conference training.ua.edu
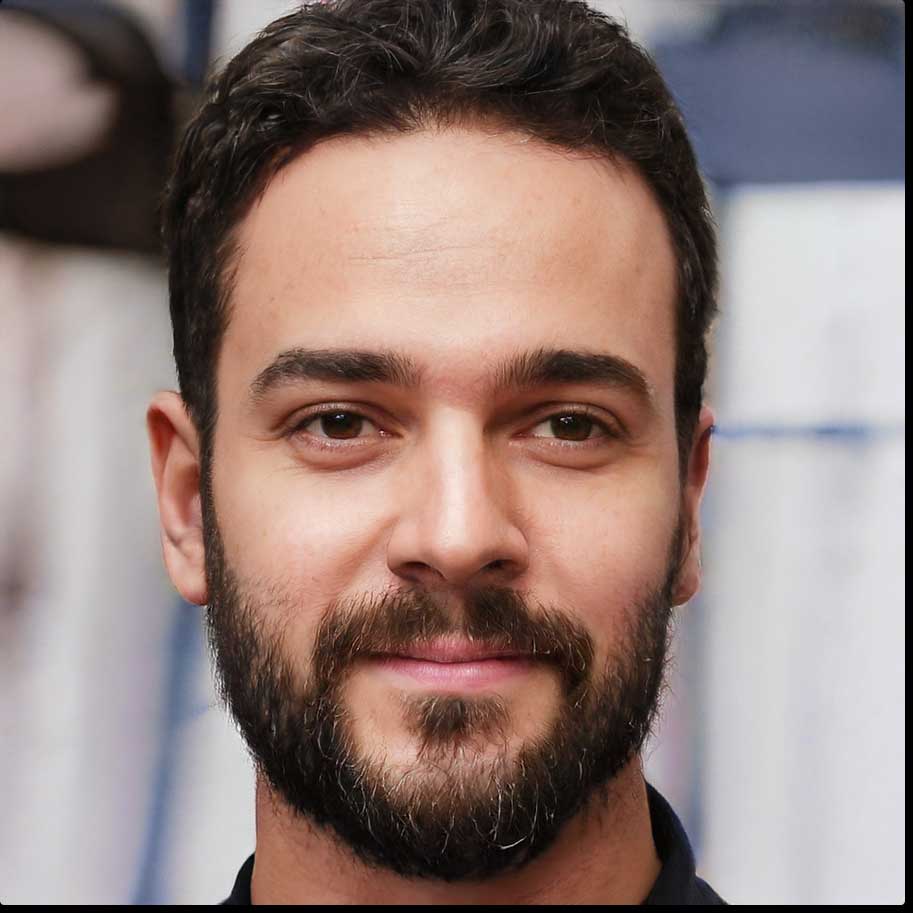