How to Be Generator and Alternator Repair Technician - Job Description, Skills, and Interview Questions
The repair of generators and alternators is vital for the efficient functioning of many industries. When these components of machines malfunction, it can lead to disrupted production, delayed projects, and an overall decrease in productivity. The expertise of a generator and alternator repair technician is thus essential to diagnose and fix any problems that arise in these machines.
With their knowledge of the components and their functionality, the technician can effectively identify and resolve any issues, ensuring that the machine is running smoothly and efficiently. By doing so, they can save companies time and money, while also ensuring a safe working environment.
Steps How to Become
- Obtain a high school diploma or equivalent. A high school diploma is the minimum educational requirement to become a generator and alternator repair technician.
- Consider enrolling in a postsecondary educational program in electricity and electronics. While not a requirement to becoming a generator and alternator repair technician, enrolling in a postsecondary program in electricity and electronics can provide the theoretical foundation for working with generators and alternators.
- Pursue an apprenticeship with a generator and alternator repair technician. Training for this profession is usually provided through on-the-job experience, so it is important to secure an apprenticeship with a technician who is willing to provide hands-on training and mentorship.
- Become certified. Many employers prefer to hire technicians who are certified in the field of generator and alternator repair. Certification can be obtained by taking and passing an examination administered by the National Institute for Automotive Service Excellence (ASE).
- Consider earning advanced certifications to further enhance your job prospects. The ASE offers certificates in specialty areas such as diesel engines, advanced engine performance, and emissions systems.
- Join professional organizations like the National Electrician Association (NEA) or the Diesel Technology Forum (DTF). These organizations offer members access to educational programs, industry resources, and networking opportunities.
To be a successful generator and alternator repair technician, one must have a keen eye for detail and possess a wide range of technical knowledge. Firstly, a solid foundation of basic electrical engineering principles is vital to understand the workings of the electrical systems. Knowledge of the various components and their operation is also essential.
Secondly, it is important to have a comprehensive understanding of the various types of generators and alternators, including their installation, maintenance and troubleshooting. the technician must be able to use specialized tools such as ohm meters, circuit testers and oscilloscopes. Lastly, the technician must possess the ability to read and understand schematic diagrams, as well as troubleshoot complex systems with precision and accuracy.
With all of these skills combined, a technician can become highly skilled and competent in the repair and maintenance of generators and alternators.
You may want to check Diesel Engine Repair Technician, Automotive Repair Technician, and Military Aircraft Repairer for alternative.
Job Description
- Diagnose and repair malfunctioning alternator systems.
- Inspect and replace worn and damaged alternator components.
- Test and adjust voltage regulators, brushes, brushes holders and rectifiers.
- Repair and maintain wiring and electrical systems in alternators.
- Troubleshoot and repair alternator malfunctions.
- Perform periodic maintenance on alternators and related systems.
- Adjust and align field current and voltage in alternators.
- Install, remove, and repair alternators.
- Monitor and inspect alternator performance.
- Create reports and document maintenance activities for each alternator.
Skills and Competencies to Have
- Knowledge of electrical theory and principles
- Expertise in troubleshooting both AC and DC generator and alternator systems
- Ability to read and interpret electrical schematics, diagrams, and drawings
- Proficiency in the use of hand and power tools, measuring devices, and test equipment
- Familiarity with the operation and maintenance of engine-driven generators and alternators
- Ability to diagnose and repair faults in generator and alternator systems
- Ability to use welding and soldering equipment
- Skilled in the replacement of worn or defective parts
- Ability to follow safety protocols and procedures
- Exceptional communication, problem solving, and customer service skills
Having a strong understanding of electricity and electronics is essential for a Generator and Alternator Repair Technician. A successful technician must possess a good knowledge of electrical systems and how they function, including the ability to diagnose, troubleshoot, and repair engine-driven generator and alternator systems. They must also understand the various components of such systems, including the wiring and circuitry, and be able to safely work with electrical power supplies and tools.
the technician must be knowledgeable in the proper use of necessary safety equipment, as well as the preventive maintenance of such systems. By mastering these skills, technicians are able to effectively and efficiently repair generator and alternator systems, thus avoiding costly repairs and helping to ensure that these systems remain running smoothly.
Aircraft Structural Repairer, Repair Engineer, and Electronics Repair Technician are related jobs you may like.
Frequent Interview Questions
- What experience do you have in repairing generators and alternators?
- How familiar are you with the different types of generators and alternators?
- Describe a successful repair job you have completed on a generator or alternator.
- Are you comfortable using power tools and other equipment to perform repairs?
- Do you have any experience troubleshooting electrical systems?
- What steps do you take to ensure safety while working with hazardous materials or high voltage equipment?
- How do you stay informed about advances in technology related to generator and alternator repair?
- What methods do you use to diagnose and repair generator and alternator problems?
- What challenges have you faced while repairing generators and alternators, and how did you overcome them?
- How do you handle customer complaints related to work performed on their generator or alternator?
Common Tools in Industry
- Multimeters. A device used to measure electrical current, voltage, and resistance. (eg: Fluke 117 Multimeter)
- Oscilloscopes. A device used to measure and display waveforms of electrical signals. (eg: Tektronix TDS1001B Digital Oscilloscope)
- AC/DC Clamp Meters. A device used to measure alternating current and direct current in an electrical circuit. (eg: Fluke 324 Clamp Meter)
- Insulation Testers. A device used to measure the insulation resistance of an electrical component or system. (eg: Megger MFT1730 Insulation Tester)
- Test Leads. Wires with connectors on the ends used to connect devices to each other or to a power source. (eg: Fluke TL224 Test Lead Set)
- Volt-Ohm Meters (VOM). A device used to measure voltage, resistance, and current in an electrical circuit. (eg: Extech EX330 Autoranging Multimeter)
- Circuit Breakers. A safety device that automatically disconnects power from a circuit if it is overloaded. (eg: Square D QO 20 Amp Circuit Breaker)
- Electric Motors. A machine that converts electrical energy into mechanical energy. (eg: Dayton 1/4 HP Electric Motor)
- Generators. A machine that converts mechanical energy into electrical energy. (eg: Champion 7500 Watt Dual Fuel Generator)
- Welding Equipment. A device used to join two metals or thermoplastics together by heating them until they melt and fuse together. (eg: Miller Electric MIG Welder)
Professional Organizations to Know
- International Electrical Testing Association (NETA)
- National Electrical Contractors Association (NECA)
- National Institute for Certification in Engineering Technologies (NICET)
- American Society for Testing and Materials (ASTM)
- Institute of Electrical and Electronics Engineers (IEEE)
- International Society of Automation (ISA)
- Electrical Apparatus Service Association (EASA)
- Generator and Alternator Service Association (GASA)
- InterNational Electrical Testing Association (INETA)
- International Council on Large Electric Systems (CIGRE)
We also have Repair Supervisor, Ship Engineer and Industrial Machinery Mechanic and Repairer, and Repair Coordinator jobs reports.
Common Important Terms
- Automotive Electrical System. A system of components used to power a vehicle, including the battery, starter, alternator, wiring, and other related parts.
- Alternator. A device that generates an alternating current (AC) by converting mechanical energy into electrical energy.
- Generator. A device that generates an electrical current by converting mechanical energy into electrical energy.
- Voltage Regulator. A device that regulates the output voltage of an alternator or generator.
- Battery. A device that stores and releases electrical energy to power a vehicle.
- Starter Motor. A device that is used to start an engine by supplying it with electricity.
- Ignition System. A system of components that provide the spark necessary to ignite the fuel in the engine.
- Wiring Harness. A collection of wires and connectors used to connect various components in a vehicle's electrical system.
Frequently Asked Questions
What type of certifications do Generator and Alternator repair technicians need?
Generator and Alternator repair technicians typically need to be certified in electrical engineering, power systems and/or industrial maintenance.
How much experience is typically required to become a Generator and Alternator Repair Technician?
Generally, Generator and Alternator Repair Technicians should have at least 5 years of relevant experience in the field.
What are the primary duties of a Generator and Alternator Repair Technician?
The primary duties of a Generator and Alternator Repair Technician include inspecting, diagnosing, repairing, and maintaining generators and alternators.
What tools and equipment do Generator and Alternator Repair Technicians use?
Generator and Alternator Repair Technicians typically use tools such as multimeters, wrenches, screwdrivers, pliers, and soldering irons.
What safety protocols should be followed when working with Generators and Alternators?
Generator and Alternator Repair Technicians should always follow all relevant safety protocols, such as wearing protective gear, adhering to safety regulations, and following all manufacturer's instructions.
What are jobs related with Generator and Alternator Repair Technician?
- Repair Supervisor II
- Repair Technician Apprentice
- Auto Body and Paint Repair Technician
- Aircraft Repair Technician
- Repair Technician II
- Machine Tool Repairer
- Motorcycle and Power Equipment Repair Technician
- Aircraft Electronics and Avionics Equipment Installer and Repairer
- Repair Technician
- Repair Mechanic
Web Resources
- Generator Support Technician | Massachusetts Maritime Academy www.maritime.edu
- Turbine Generator Maintenance, Inspection and Repair fortmyerstech.edu
- Generator Mechanical Maintenance Technician - Stanford careersearch.stanford.edu
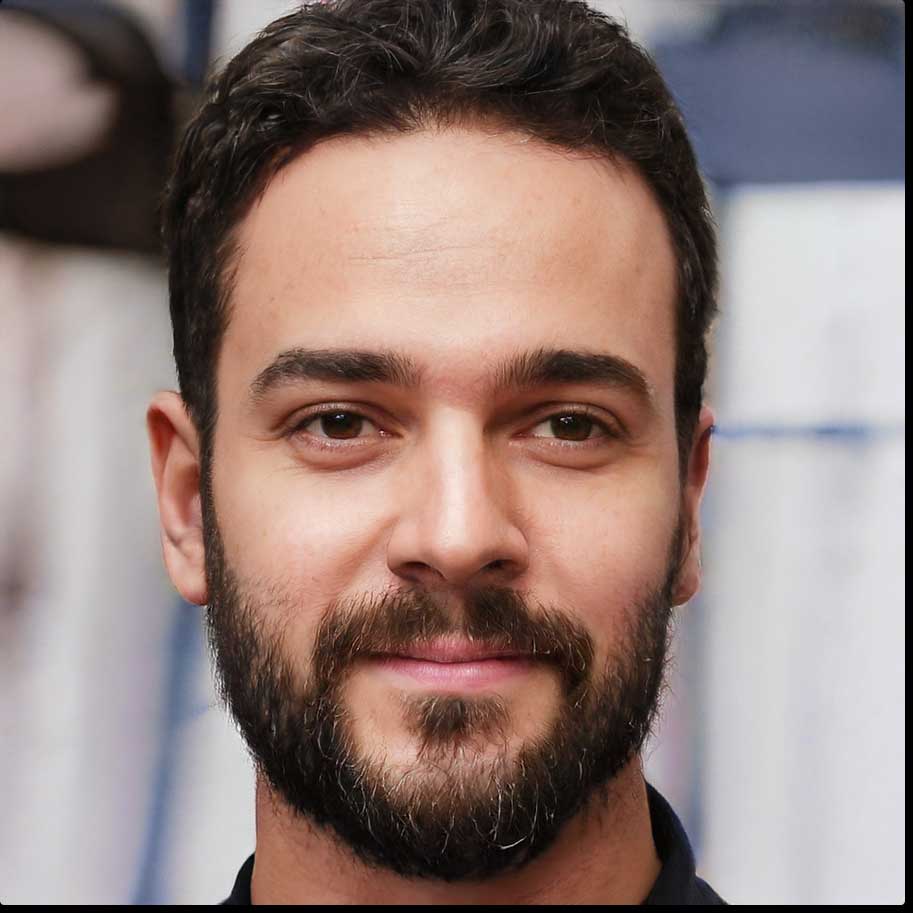