How to Be Repair Coordinator - Job Description, Skills, and Interview Questions
Using the services of a Repair Coordinator can cause significant improvements in the efficiency and cost-effectiveness of any repair process. This is because they are able to coordinate the resources involved in a repair job, such as parts, personnel, and tools, in order to expedite the process and reduce costs. By correctly identifying the necessary resources and scheduling the necessary labor, a Repair Coordinator can take a repair job from start to finish in a timely and organized manner.
they often have knowledge of where to find the best deals on parts and tools, which can further reduce costs. the use of a Repair Coordinator can result in more efficient repairs that are completed in a shorter amount of time, while also being more cost-effective.
Steps How to Become
- Obtain a high school diploma or equivalent. Most repair coordinator positions require at least a high school diploma or equivalent.
- Enroll in a college degree program. Many employers prefer to hire repair coordinators who have a college degree, such as an associate's degree in business or a related field.
- Gain experience in repair and maintenance. Repair coordinators are responsible for overseeing the repair and maintenance of equipment, so it is important to gain some experience in this area before applying for a job. Consider interning with a local repair and maintenance company or volunteering to help out with repair and maintenance tasks.
- Develop customer service skills. As a repair coordinator, you will be dealing with customers on a daily basis. Therefore, it is important to develop excellent customer service skills, including communication and problem-solving skills.
- Seek out job opportunities. Once you have the necessary qualifications and experience, start looking for job openings in your area. Consider both online job boards and local classifieds as resources for finding vacancies.
- Apply for the position. When you find a job opening that interests you, prepare your application materials and submit them according to the job posting instructions. Be sure to highlight your qualifications and experience in your application.
- Attend the interview. If you are selected for an interview, make sure you are prepared to answer questions about your qualifications and experience with repair and maintenance.
- Start working as a repair coordinator. Once you have been hired, you can begin your new job as a repair coordinator.
The success of a Repair Coordinator relies heavily on their ability to stay up to date with new technologies and processes. Maintaining an efficient workflow depends on having the right tools and resources, such as updated software and manuals, as well as being able to quickly and accurately diagnose and repair problems. Regularly attending training courses and workshops can help a Repair Coordinator stay ahead of the curve, while networking with peers in the industry can help them stay informed of best practices and the latest trends.
Having a well-organized system for tracking and managing repairs, as well as having sound communication practices for interacting with customers, are also key components for an efficient repair process. Collectively, these factors can help a Repair Coordinator keep their operations running smoothly and effectively.
You may want to check Aircraft Structural Repairer, Repair Installer, and Automated Teller Machine (ATM) Repair Technician for alternative.
Job Description
- Create and maintain repair schedules for all necessary repairs and maintenance.
- Monitor progress of repairs and ensure that all repairs are completed on time and to a high standard.
- Liaise with repair technicians, suppliers, and customers to ensure a smooth repair process.
- Troubleshoot problems to determine the best course of action for repairs.
- Collect and analyze data to identify areas of improvement in the repair process.
- Create and implement plans to improve repair processes and reduce costs.
- Maintain accurate records of all repairs and parts used.
- Develop and implement safety protocols to ensure a safe working environment.
- Train, mentor, and manage repair technicians and other staff members.
- Monitor repair costs and generate reports as required.
Skills and Competencies to Have
- Excellent customer service skills
- Strong communication and listening skills
- Ability to prioritize tasks and manage time effectively
- Ability to solve problems and think critically
- Knowledge of repair processes and procedures
- Ability to read and interpret technical drawings and schematics
- Knowledge of safety regulations
- Strong organizational skills
- Ability to work independently or in a team environment
- Computer proficiency in commonly used software applications
Being a Repair Coordinator requires an array of skills, but the most important one is excellent communication. Being able to effectively communicate with customers, technicians, and other repair coordinators is essential to ensure that repair needs are met accurately and efficiently. Good communication also helps to reduce conflict, build strong relationships, and make sure that tasks are completed on time.
Having strong organizational skills is also essential, as repair coordinators need to be able to manage multiple tasks at once and prioritize them according to importance and urgency. An understanding of the repair process, including parts ordering and tracking, is also important. Finally, having excellent problem-solving skills is key to being a successful repair coordinator, as it allows the coordinator to quickly identify and resolve any issues that arise during the repair process.
Machine Tool Repairer, Aircraft Electronics and Avionics Equipment Installer and Repairer, and Repair Welder are related jobs you may like.
Frequent Interview Questions
- What experience do you have managing repair projects?
- How do you prioritize and organize repairs?
- What strategies do you use to ensure repairs are completed on time?
- How do you handle customer complaints related to repairs?
- How do you stay up to date with new repair technologies?
- What challenges have you faced in coordinating repairs?
- How do you ensure accuracy when ordering parts for repairs?
- How do you ensure safety when completing repairs?
- What experience do you have working with technicians to complete repairs?
- What would you do if a repair project was behind schedule?
Common Tools in Industry
- Multi-meter. A device used to measure electrical current, voltage and resistance. (e. g. Fluke 87V Digital Multimeter)
- Pliers. A hand tool used for gripping and cutting wires. (e. g. Irwin Vise-Grip Long Nose Pliers)
- Screwdriver. A tool used for turning and removing screws. (e. g. Stanley FatMax Screwdriver Set)
- Wrench. A tool used to turn nuts and bolts. (e. g. Craftsman Ratchet Wrench Set)
- Soldering Iron. A tool used to melt and join two pieces of metal together. (e. g. Weller WLC100 40-Watt Solder Station)
- Drill. A tool used to make holes in various materials. (e. g. Black & Decker Corded Drill)
- Utility Knife. A tool used to cut a variety of materials including paper, plastic, and wood. (e. g. Stanley Retractable Utility Knife)
- Tape Measure. A measuring device used to measure distances accurately. (e. g. Stanley Tape Measure)
Professional Organizations to Know
- American Industrial Hygiene Association (AIHA)
- National Air Filtration Association (NAFA)
- National Fire Protection Association (NFPA)
- American Society of Heating, Refrigerating and Air-Conditioning Engineers (ASHRAE)
- Air-Conditioning, Heating, and Refrigeration Institute (AHRI)
- Sheet Metal and Air Conditioning Contractors National Association (SMACNA)
- American Society of Mechanical Engineers (ASME)
- American Society of Plumbing Engineers (ASPE)
- International Facility Management Association (IFMA)
- International Organization for Standardization (ISO)
We also have Phone and Computer Repair Technician, Repair Process Technician, and Auto Body and Paint Repair Technician jobs reports.
Common Important Terms
- Warranty. A guarantee given by a manufacturer or supplier of a product, typically for a period of time, that protects against defects in materials or workmanship.
- Parts Ordering. The process of ordering spare parts from a supplier for the purpose of repair, maintenance, or replacement of a faulty device or component.
- Quality Assurance. A set of processes and procedures that guarantee products and services meet quality standards and customer expectations.
- Troubleshooting. The process of identifying, diagnosing, and resolving problems and issues with a product or system.
- Damage Assessment. The process of determining the condition of a device or system to determine what repairs are needed.
- Estimating. The process of predicting the cost, time, or effort that will be required to complete a repair job.
- Logistics. The process of planning, organizing, and coordinating the movement of goods and materials between different locations.
- Service Contract. An agreement between a customer and a service provider that outlines the terms and conditions of the service being provided.
Frequently Asked Questions
What is a Repair Coordinator?
A Repair Coordinator is a professional who oversees the repair process for a variety of items, such as industrial equipment, vehicles, machines, and other mechanical components. They are responsible for coordinating repair services and managing the associated costs, scheduling, and quality assurance of repairs.
What skills are required to be a Repair Coordinator?
To be a successful Repair Coordinator, you should have excellent problem-solving skills, strong organizational and communication skills, and experience in working with a range of maintenance and repair services. Additionally, knowledge of safety regulations and experience in dealing with vendors and suppliers is helpful.
What duties does a Repair Coordinator typically perform?
The primary duties of a Repair Coordinator include scheduling and overseeing repairs, creating cost estimates, managing paperwork related to repairs, ordering parts and supplies, coordinating with vendors and suppliers, and ensuring that repairs are completed on time and within budget.
How much does a Repair Coordinator typically earn?
The median annual salary for a Repair Coordinator is approximately $53,000, depending on experience, location, and industry.
What type of environment does a Repair Coordinator typically work in?
A Repair Coordinator typically works in a professional office or industrial setting. They may also be required to travel to customer sites to oversee repairs.
What are jobs related with Repair Coordinator?
- Repair Technician Lead
- Repair Technician III
- Building Maintenance and Repair Technician
- Repair Inspector
- Repair Technician
- Plumbing Repair Technician
- Repair Helper
- HVAC Repair Technician
- Appliance Repair Technician
- Aircraft Repair Technician
Web Resources
- Maintenance & Repair UCF Facilities Operations fo.ucf.edu
- MAINTENANCE COORDINATOR TCSG - Technical College www.tcsg.edu
- Repair coordinator Jobs in Philadelphia, PA | Glassdoor www.glassdoor.com
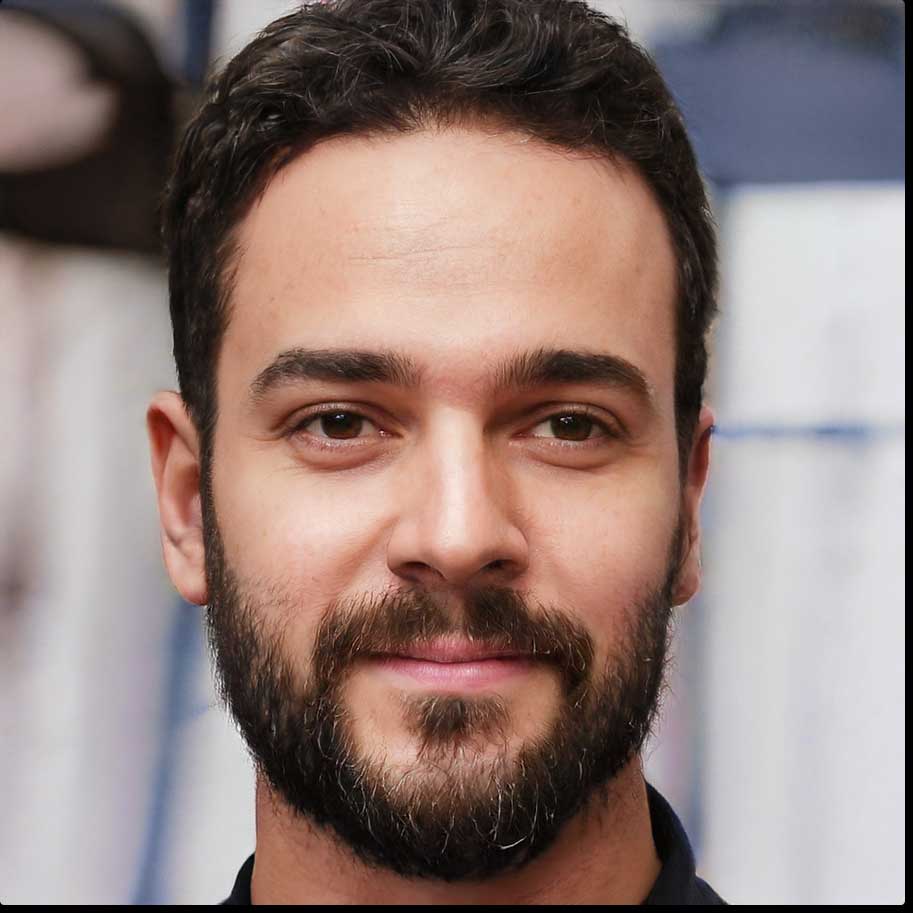