How to Be Plastic Molder - Job Description, Skills, and Interview Questions
The use of plastic molds has become increasingly popular in the manufacturing industry due to their cost effectiveness and efficiency. The use of plastic molds has allowed companies to reduce their production costs while also increasing their production speed. This is because plastic molds are able to create products quickly and with a high degree of accuracy.
Furthermore, the use of plastic molds reduces the amount of waste created in the production process. As a result, companies have been able to achieve greater profitability while also reducing their environmental impact. In addition, plastic molds are highly durable and resistant to wear and tear, making them a cost-effective long-term option for manufacturing companies.
Steps How to Become
- Obtain a High School Diploma or GED. The first step to becoming a plastic molder is to obtain a high school diploma or GED. Having a basic education is essential for succeeding in the field.
- Obtain Plastic Molder Training. The next step is to obtain plastic molder training. This can be done through a community college, technical school, or other training programs. It is important to research the different programs available and find the one that best suits your needs.
- Get Certified. Once you have completed the appropriate training, it is recommended that you become certified in plastic molding. This certification can be obtained through the American Plastics Molders Association (APMA).
- Get Experience. After obtaining the necessary training and certification, the next step is to gain experience in the field. You can do this by working as an apprentice or intern with a plastic molding company. This will allow you to gain hands-on experience and learn from experienced professionals.
- Get Hired. Once you have gained the necessary experience and certification, you will be ready to start looking for full-time work as a plastic molder. Many companies prefer to hire certified professionals, so having your certification can be a great asset.
The impact of becoming a skilled and capable plastic molder is far-reaching. With the right training and experience, a plastic molder can take on a wide range of jobs. In addition to increasing their knowledge base, they can earn higher wages, have more job security, and become a part of a larger career network.
Furthermore, having a strong background in this field can open up opportunities to work with advanced materials, leading to more innovative products and services. On the other hand, if a plastic molder fails to stay up to date with the latest trends and technologies, they will likely miss out on potential job opportunities and may even be unable to compete in the marketplace. Therefore, it is essential that plastic molders continually strive to improve their skills and stay ahead of the competition.
You may want to check Plastic Mold Maker, Plastic Machine Operator, and Plastic Fabrication Technician for alternative.
Job Description
- Design and create custom plastic molding parts and products.
- Use CNC machines to shape, trim, and cut plastic parts to specifications.
- Monitor and adjust the plastic molding process to improve quality and efficiency.
- Perform maintenance and repairs on plastic molding machines.
- Operate auxiliary molding equipment as needed.
- Work with engineering and production staff to meet customer's requirements.
- Inspect parts and products for defects, accuracy, and conformance to customer specifications.
- Troubleshoot molding problems and make necessary corrections.
- Research new technologies and materials to improve existing products and processes.
- Follow safety protocols and wear protective gear when operating machinery.
Skills and Competencies to Have
- Knowledge of injection molding processes and materials
- Understanding of safety regulations and procedures
- Ability to set up, operate and troubleshoot injection molding machines
- Experience with measuring and testing equipment
- Proficient in adjusting and calibrating molds
- Skilled in the use of computers for programming, data analysis and reporting
- Must have good manual dexterity
- Ability to read and interpret blueprints, diagrams and schematics
- Ability to work independently with minimal supervision
- Good problem solving and communication skills
Plastic molding is a crucial part of the manufacturing process for many products and requires a range of skills to do it effectively. The most important skill required for successful plastic molding is the ability to work with a variety of materials and tools. This includes being able to understand the properties of different types of plastics and the effects of manipulating them in different ways.
the person must be able to operate the machinery and tools needed to make the molds, as well as have a basic knowledge of how to troubleshoot problems that may arise. Finally, the plastic molder must have a keen eye for detail, as precision and accuracy are key to ensuring that the finished product is of high quality. Without these skills, plastic molding would be impossible.
Plastic Injection Molding Technician, Plastic Tool Maker, and Plastic Extrusion Operator are related jobs you may like.
Frequent Interview Questions
- What experience do you have in plastic molding?
- What challenges have you faced while working with plastic molding?
- What safety measures do you take while handling plastic molding machinery?
- How do you ensure that the plastic parts meet the required specifications?
- How do you troubleshoot any issues during the plastic molding process?
- Are you familiar with the different types of plastics and their properties?
- How do you optimize existing plastic molding operations?
- What kind of maintenance do you perform to keep the plastic molding machine in good working order?
- What strategies do you use for reducing waste and increasing efficiency during the plastic molding process?
- What procedures do you follow to ensure that the plastic parts meet the highest quality standards?
Common Tools in Industry
- Injection Molding Machine. A machine used to form plastic into specific shapes by injecting heated plastic into a mold. (eg: creating plastic toy blocks)
- Vacuum Forming Machine. A machine used to shape plastic sheets by applying heat and vacuum pressure. (eg: forming plastic parts for automotive interiors)
- Extrusion Machine. A machine used to form plastic into long shapes by squeezing it through a die. (eg: creating plastic tubing)
- Blow Molding Machine. A machine used to form hollow plastic parts by blowing air into a heated mold. (eg: creating plastic bottles)
- Rotational Molding Machine. A machine used to form hollow parts by slowly rotating the mold in an oven. (eg: creating plastic kayaks)
- Compression Molding Machine. A machine used to form plastic parts by applying pressure to heated molds. (eg: creating plastic car parts)
Professional Organizations to Know
- American Mold Builders Association (AMBA)
- Society of Plastics Engineers (SPE)
- Plastics Industry Association (PIA)
- National Plastics Center and Museum (NPCM)
- International Association of Plastics Distributors (IAPD)
- Association of Rotational Molders (ARM)
- International Association for Polymer Processing (IAPP)
- American Plastics Council (APC)
- Society of Injection Molding Professionals (SIMP)
- International Institute of Injection Molding Technology (IIIMT)
We also have Plastic Fabricator, Plastics Quality Inspector, and Plastic Packaging Technician jobs reports.
Common Important Terms
- Injection Molding. A manufacturing process for producing parts from both thermoplastic and thermosetting plastic materials by injecting molten material into a mold.
- Blow Molding. A manufacturing process that forms hollow plastic parts by forcing a heated plastic tube or parison against a mold cavity.
- Rotational Molding. A process that uses heat and rotation to create hollow, seamless objects.
- Compression Molding. A process that uses pressure to form a part from a pre-heated thermoplastic material.
- Extrusion Molding. A process that uses heat and pressure to shape a thermoplastic material into a specific shape.
- Thermoforming. A process that uses heat and pressure to form a thin plastic sheet into a specific shape.
- Vacuum Forming. A process that uses vacuum pressure to form a thin plastic sheet into a specific shape.
Frequently Asked Questions
Q1: What is plastic molding? A1: Plastic molding is a manufacturing process for producing parts from thermoplastic and thermosetting plastic materials. It typically involves heating the material, shaping it in a mold, and then cooling it to its final form. Q2: What types of materials can be used in plastic molding? A2: Thermoplastics and thermosetting plastics are the most common materials used in plastic molding. Thermoplastics include polyethylene, polypropylene, PVC, and ABS; while thermosetting plastics include epoxy, polyester, and phenolic resins. Q3: What is the typical production cycle time for a plastic molding project? A3: The typical production cycle time for a plastic molding project depends on the complexity of the part and the type of molding process being used. Generally, cycle times can range from a few seconds to several minutes. Q4: How much does a plastic molder cost? A4: The cost of a plastic molder will depend on the size and complexity of the part being molded, as well as the materials and processes used. Generally speaking, plastic molders can cost anywhere from a few hundred dollars to several thousand dollars. Q5: What safety precautions should be taken when working with a plastic molder? A5: When working with a plastic molder, it is important to take safety precautions such as wearing protective clothing, using proper ventilation, and following all manufacturer instructions. Additionally, it is important to make sure that the machine is in good working order and that all tools and materials are properly stored and secured.What are jobs related with Plastic Molder?
- Plastics Technician
- Plastics Product Designer
- Plastic Artist
- Plastics Engineer
- Plastic Film Processor
- Plastic Recycling Technician
- Plastics Production Worker
- Plastic Injection Molding Machine Operator
Web Resources
- Plastic Molding | Processes Lab | NC State ISE - Plastic www.ise.ncsu.edu
- Plastic molding Technology | Plastic Mold | Plastic Injection Mold ... mold.world.edu
- The Plastic in our Oceans - Science in the News sitn.hms.harvard.edu
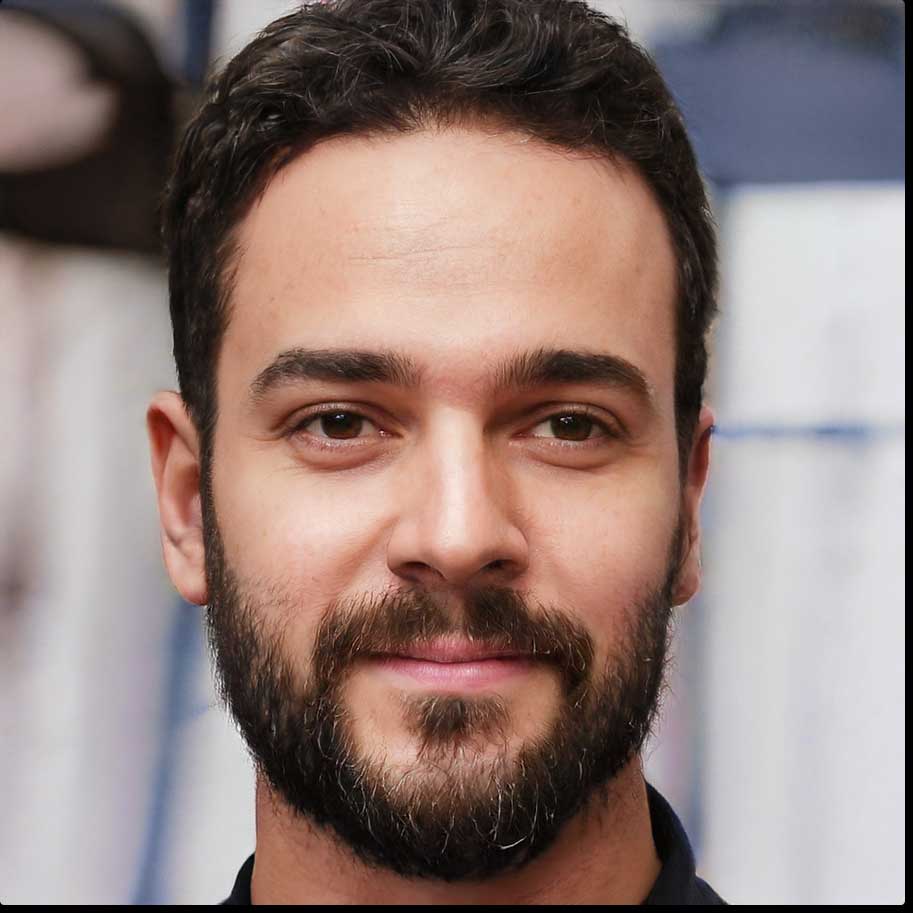