How to Be Plastic Fabricator - Job Description, Skills, and Interview Questions
The increasing use of plastics in industries and households has had a major effect on the demand for plastic fabricators. Plastic fabricators are professionals who work with plastic materials to create a wide range of products, such as pipes, containers, and other items. With increased plastic usage, the demand for plastic fabricators has risen, resulting in more job openings for these professionals.
Consequently, the need for more training and education in the field has also grown, leading to higher wages and more benefits for those with the necessary skills. As the need for plastic fabricators continues to rise, the outlook for this profession is very promising.
Steps How to Become
- Obtain a high school diploma or GED. Most employers prefer to hire plastic fabricators who have a high school education or equivalent.
- Take a course in plastics technology. Many community colleges and technical schools offer courses in plastics technology. These courses will provide knowledge of the basics of working with plastics and the types of plastics available.
- Participate in an apprenticeship program. Many companies offer apprenticeships programs where you can learn the skills needed to become a plastic fabricator while on the job.
- Obtain a certification in plastic fabrication. Many organizations offer certification programs that will give you recognition as a qualified plastic fabricator. The Society of Plastics Engineers, for example, offers a Certified Plastics Technician program.
- Gain experience in the field. Experience is an important part of becoming a qualified plastic fabricator. Working in the industry for several years will give you the knowledge and expertise necessary to excel in the field.
- Stay up to date on new technologies and materials. The world of plastic fabrication is constantly changing and advancing. Staying informed of new technologies and materials will help you stay ahead of the competition and remain an expert in the industry.
As a plastic fabricator, it is important to stay up-to-date on the latest technology and processes to remain competitive in the industry. To do this, one must stay abreast of changes in materials, equipment, and techniques. Investing in continuing education and research will help ensure that you stay ahead of the curve and remain knowledgeable about the latest advancements in the industry.
investing in quality tools and machinery is key to being able to produce top-tier products. Keeping up with the ever-evolving landscape of the plastic fabricating industry is essential for success and staying competitive.
You may want to check Plastics Engineer, Plastic Molder, and Plastic Recycling Technician for alternative.
Job Description
- Assemble plastic parts according to customer specifications.
- Operate welding and molding equipment to create plastic components.
- Utilize computer-aided design (CAD) software to create plastic parts.
- Measure and cut plastic materials to size and shape.
- Glue, weld, and fasten plastic components together.
- Test plastic components for functionality and quality assurance.
- Troubleshoot and repair plastic components and equipment.
- Maintain a clean and safe work area.
- Monitor the production process and make adjustments as needed.
- Prepare reports detailing the production process and results.
Skills and Competencies to Have
- Knowledge of plastic fabrication techniques and materials.
- Ability to read blueprints and schematics.
- Proficiency with hand tools, power tools, and machinery used in plastic fabrication.
- Knowledge of safety practices and procedures in a manufacturing environment.
- Ability to work accurately and efficiently with attention to detail.
- Ability to work independently or as part of a team.
- Ability to communicate effectively with supervisors and co-workers.
- Ability to lift and move heavy objects when necessary.
- Ability to troubleshoot and identify problems with plastic fabrication processes.
- Good organizational skills and the ability to prioritize tasks.
Having experience as a plastic fabricator requires a wide range of skills, but the most important of these is the ability to think critically and solve problems. A plastic fabricator must be able to identify potential issues in the fabrication process and have the knowledge to create solutions that are both efficient and effective. In addition, the fabricator must have a good working knowledge of the various types of plastics and their properties, as well as the tools and techniques used to shape plastic.
Finally, an experienced plastic fabricator must be able to work safely and abide by all safety regulations. Having these skills is essential for successful plastic fabrication, as it allows the fabricator to create quality products with fewer mistakes and less waste.
Plastic Film Processor, Plastics Production Worker, and Plastic Packaging Technician are related jobs you may like.
Frequent Interview Questions
- What prior experience do you have in plastic fabrication?
- Describe a challenging project you have worked on in the past.
- How do you stay organized when working with multiple projects?
- What safety protocols do you follow when working with plastic?
- How do you approach troubleshooting when working with plastics?
- What do you know about the different types of plastic and their properties?
- How do you determine the best plastic for a given project?
- What strategies do you use to ensure accuracy and precision when working with plastic?
- How do you go about ensuring quality control in your work?
- Describe your experience with plastic welding and/or cutting tools.
Common Tools in Industry
- Soldering Iron. Used for joining metal components together, such as connecting electrical wires. (eg: soldering a circuit board)
- Heat Gun. Used to create heat for welding, shrinking plastic, and more. (eg: heating and shrinking a PVC pipe)
- Power Drill. Used for drilling holes into materials, such as wood, metal and plastic. (eg: drilling holes in a sheet of acrylic plastic)
- Router. Used to cut and shape materials, such as wood and plastic. (eg: cutting a groove in a piece of wood)
- Grinder. Used to grind down and shape hard materials, such as metal and stone. (eg: grinding down a metal part to fit a specific shape)
- Hot Glue Gun. Used to join two materials together with hot glue. (eg: gluing plastic pieces together)
- Heat Sealer. Used to seal plastic products and packages with heat. (eg: sealing a plastic bag shut)
- Plastic Welder. Used to weld thermoplastics together with heat. (eg: welding two pieces of plastic together)
- Jigsaw. Used to cut curves and complex shapes into materials, such as wood and plastic. (eg: cutting a curved shape out of a sheet of acrylic)
- Band Saw. Used to make straight cuts in materials, such as wood and metal. (eg: cutting a straight line in a piece of aluminum)
Professional Organizations to Know
- American Plastics Council
- Society of Plastics Engineers
- Plastics Industry Association
- Society of Manufacturing Engineers
- American Society of Mechanical Engineers
- International Association of Plastics Distribution
- National Association of Plastics Distributors
- National Tooling and Machining Association
- Fabricators and Manufacturers Association International
- Association of Plastics Recyclers
We also have Plastics Product Designer, Plastics Technician, and Plastic Tool Maker jobs reports.
Common Important Terms
- Injection Molding. A manufacturing process in which plastic is melted and injected into a mold to form the desired shape.
- Vacuum Forming. A process in which a plastic sheet is heated and placed into a mold, forming the desired shape when the air between the two is removed.
- Rotational Molding. A process in which a mold is slowly rotated while heated plastic is added, allowing the plastic to coat the inside of the mold and form the desired shape.
- Extrusion. A manufacturing process in which plastic is melted and forced through a die to create a long, continuous shape.
- Blow Molding. A process in which a heated plastic shape is inserted into a mold and air pressure is used to form the desired shape.
- Thermoforming. A process in which a heated plastic sheet is inserted into a mold and vacuum pressure is used to form the desired shape.
- Fabrication. The process of assembling plastic components into a finished product using various processes such as drilling, cutting, welding, and riveting.
Frequently Asked Questions
What is a Plastic Fabricator?
A Plastic Fabricator is a machine that is used to shape and form plastic parts using a variety of tools and techniques. It typically consists of a heating element, a cooling element, a cutting blade, and a forming tool.
What materials can be worked with a Plastic Fabricator?
Plastic Fabricators can work with a variety of different materials, including thermoplastics and thermosets. Common materials that can be worked with a Plastic Fabricator include ABS, PVC, polyethylene, polypropylene, and nylon.
What types of products can be made with a Plastic Fabricator?
Products that can be made with a Plastic Fabricator include custom parts and components for medical equipment, industrial machinery, and consumer electronics. Additionally, plastic fabricators can be used to create prototypes, molds, and enclosures.
How accurate is the fabrication process with a Plastic Fabricator?
The accuracy of the fabrication process with a Plastic Fabricator depends on the type of machine being used. Generally speaking, modern Plastic Fabricators are capable of producing parts and components with tolerances of less than 0.001 inches.
What safety measures should be taken when operating a Plastic Fabricator?
When operating a Plastic Fabricator, it is important to wear eye protection and other protective gear to prevent injury from flying debris. Additionally, all tools and components should be checked for proper operation before use, and all safety instructions should be followed at all times.
What are jobs related with Plastic Fabricator?
- Plastics Quality Inspector
- Plastic Finisher
- Plastic Injection Molding Technician
- Plastic Mold Maker
- Plastic Injection Molding Machine Operator
- Plastic Artist
- Plastic Fabrication Technician
- Plastic Extrusion Operator
Web Resources
- Plastic Fabrication | Center of BioModular Multi-Scale ¦ cbmm.ku.edu
- Plastics Fabricator Apprentice - PARTEC(Qld) Pty Ltd partec.qld.edu.au
- Plastics: Materials and Fabrication - NHTI www.nhti.edu
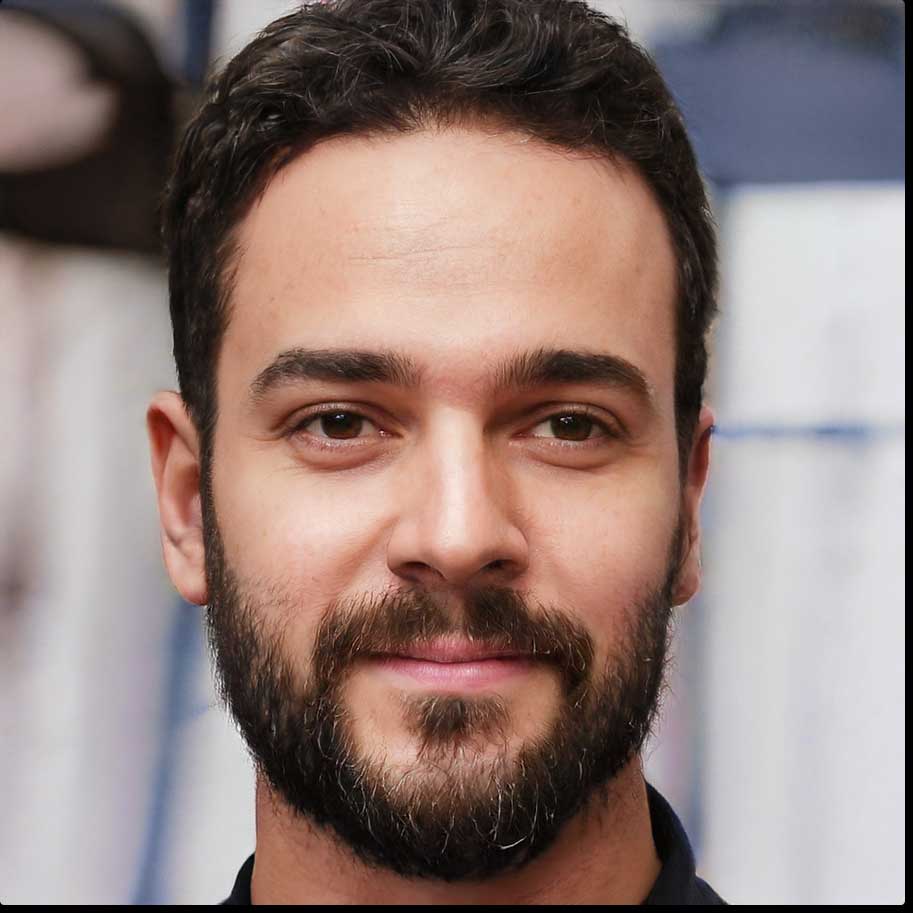