How to Be Plastic Mold Maker - Job Description, Skills, and Interview Questions
Plastic mold makers are responsible for creating molds that are used to produce plastic products. The mold maker begins the process by using a computer program to design a mold based on the specific needs of the client. Once the design is finalized, the mold maker then creates the mold with a variety of materials including aluminum, steel or plastic.
The mold is then tested and tweaked until it is ready for production. The finished product must meet the customer's requirements in order for it to be accepted for use. The quality of the molds produced by a plastic mold maker directly affects the quality of the final product, as any imperfections in the mold can cause flaws in the finished product.
Furthermore, the ability of a plastic mold maker to produce high-quality molds quickly and efficiently can have a significant impact on the success of a business.
Steps How to Become
- Obtain a High School Diploma or GED. Most employers require mold makers to have a high school diploma or equivalent. Taking courses in math, shop, and drafting will help prepare students for the job.
- Consider a Vocational Program. Many high schools offer vocational programs in machining, tool-and-die making, and other related trade skills. Completing one of these programs can provide students with a foundation in the skills required for mold making.
- Obtain an Apprenticeship. Apprenticeships with mold makers are a great way to gain hands-on experience in the field. Apprenticeships generally last two to four years and involve studying under an experienced mold maker.
- Complete an Associate Degree. Some employers prefer job applicants to have a college degree in the field. Two-year associate degrees in machining, tool-and-die making, and other related fields are available from many community colleges and technical schools.
- Pursue Certification. The American Mold Builders Association offers certification in mold making. Becoming certified can give job applicants an edge when applying for positions.
- Consider Specialization. Specializing in a particular type of mold making can be beneficial for job seekers. Specialties include injection molding, blow molding, and thermoforming.
In order to stay ahead and efficient as a plastic mold maker, it is important to keep up with the latest trends in the industry, including the most advanced technologies and materials available. Investing in high-quality tools and equipment can help to reduce production time, increase precision and accuracy, and ensure that products are made with the highest level of quality. having a thorough understanding of the customer's needs and requirements is key to creating a successful product.
Finally, investing in ongoing professional development and training can help to ensure that plastic mold makers have the knowledge and skills necessary to remain competitive. By following these steps, plastic mold makers can stay ahead of the competition and remain efficient in their craft.
You may want to check Plastics Production Worker, Plastic Tool Maker, and Plastics Engineer for alternative.
Job Description
- Design and fabricate molds used to manufacture plastic parts.
- Analyze blueprints, sketches, and 3D models of products to determine the best mold-making techniques.
- Fabricate molds from metals such as aluminum and steel using CNC machine tools.
- Use precision measuring tools to ensure the accuracy of molds.
- Install and adjust mold components to ensure proper fit and alignment.
- Identify and troubleshoot problems with molds.
- Inspect and test finished molds to ensure quality and accuracy.
- Prepare molds for shipment to customers.
- Maintain records of projects and materials used.
- Monitor stock levels of raw materials and order new supplies as needed.
Skills and Competencies to Have
- Ability to read and interpret technical drawings, schematics, and engineering specifications.
- Knowledge of injection molding principles, materials, and processes.
- Proficiency in CAD/CAM software for mold design and programming.
- Ability to use and maintain a variety of precision measuring instruments.
- Excellent problem-solving skills to diagnose and troubleshoot production issues.
- Ability to develop and use cost-effective molding techniques.
- Excellent organizational skills to manage multiple projects and tasks.
- Ability to work with minimal supervision while adhering to tight deadlines.
- Knowledge of safe operating procedures and quality control standards.
- Excellent communication and interpersonal skills to work with other personnel.
The most important skill for a plastic mold maker is the ability to think critically and create innovative designs. This requires a combination of technical knowledge, creativity, and problem-solving skills. Critical thinking involves analyzing complex scenarios and identifying potential problems, while creativity allows a mold maker to develop unique solutions to those problems.
technical knowledge is necessary in order to create a design that can be successfully produced with the machinery and materials available. Finally, problem-solving abilities are essential for quickly and accurately troubleshooting any issues that arise during production. the combination of these skills is what enables a plastic mold maker to create efficient and effective molds.
Plastic Extrusion Operator, Plastic Finisher, and Plastic Packaging Technician are related jobs you may like.
Frequent Interview Questions
- What experience do you have working with plastic injection molding machines?
- How do you ensure your molds are accurately dimensioned?
- What type of CAD software do you use to design molds?
- Describe a difficult challenge you have faced in the mold-making process.
- How do you troubleshoot complex molding issues?
- What safety protocols do you follow when working with plastic molding machines?
- What techniques do you use to reduce cycle time and improve production?
- Describe your experience setting up and running production for plastic parts.
- How do you stay current with changes in the plastic molding industry?
- How do you ensure the quality of your work?
Common Tools in Industry
- Drill Press. A machine tool used to shape and drill materials, such as metal or plastic. (eg: Used to create holes in molds for inserting screws or pins)
- Grinder. A machine tool used for grinding, typically to make precise cuts or finishes on a workpiece. (eg: Used to smooth out rough edges on the mold after it has been machined)
- Lathe. A machine tool used to shape an object by rotating it while applying pressure to it. (eg: Used to turn metal rods into the desired shape for the mold)
- Milling Machine. A machine tool used to machine solid materials, such as metal or plastic. (eg: Used to create cavities and grooves in the mold)
- Sander. A machine tool used to sand down rough surfaces on a workpiece, such as plastic or metal. (eg: Used to smooth out the molds surface after it has been machined)
- Band Saw. A machine tool used to cut materials, such as metal or plastic, into the desired shape. (eg: Used to cut the mold into its final shape)
Professional Organizations to Know
- American Mold Builders Association (AMBA)
- Society of Plastics Engineers (SPE)
- Society of Manufacturing Engineers (SME)
- Institute of Electrical and Electronics Engineers (IEEE)
- International Association of Plastics Distributors (IAPD)
- National Tooling and Machining Association (NTMA)
- National Association of Manufacturers (NAM)
- Tooling and Manufacturing Association (TMA)
- Moldmaking Technology Magazine
- The Plastics Exchange
We also have Plastics Quality Inspector, Plastic Injection Molding Technician, and Plastic Machine Operator jobs reports.
Common Important Terms
- Injection Molding. A manufacturing process in which molten material is injected into a mold cavity to shape and solidify it into desired shape.
- Tool and Die Making. The manufacturing of tools and dies used to create molds, dies, and other components.
- CAD/CAM Software. Computer-aided design and computer-aided manufacturing software used to design and manufacture molds, dies, and other components.
- CNC Machining. Computer numerical control machining is a manufacturing process that uses computers to control machine tools such as lathes and mills for cutting and shaping metal and other materials.
- Reverse Engineering. The process of analyzing an existing product or object in order to create a new design or a similar product or object.
- Milling. A machining process that uses rotary cutting tools to remove material from a workpiece.
- Grinding. A machining process that uses abrasive particles to remove material from a workpiece.
- Heat Treating. A process of subjecting metals and alloys to controlled heating and cooling cycles to alter their physical and mechanical properties.
- Finishing. A process of applying finishes such as plating, painting, polishing, sandblasting, and anodizing to a molded part or product after the initial molding process.
Frequently Asked Questions
What is a Plastic Mold Maker?
A Plastic Mold Maker is a professional who creates molds used to create plastic parts and components.
What materials can a Plastic Mold Maker work with?
A Plastic Mold Maker can work with a variety of materials, such as thermoplastics, thermosets, metals, and composites.
What is the typical size of a Plastic Mold Maker's molds?
A Plastic Mold Maker's molds typically range in size from a few millimeters to several meters depending on the desired part or component.
What type of machinery does a Plastic Mold Maker use?
A Plastic Mold Maker typically uses specialized machinery such as CNC lathes, milling machines, injection molding machines, and die casting machines.
How long does it take to produce a Plastic Mold?
The production time for a Plastic Mold typically ranges from one day up to several weeks depending on the complexity of the mold design.
What are jobs related with Plastic Mold Maker?
- Plastics Technician
- Plastic Injection Molding Machine Operator
- Plastic Film Processor
- Plastic Molder
- Plastic Fabrication Technician
- Plastics Product Designer
- Plastic Recycling Technician
- Plastic Artist
Web Resources
- Plastic Molding Manufacturing | Plastic Mold | Plastic Molds mold.world.edu
- Plastic molding Technology | Plastic Mold | Plastic Injection Mold ... mold.world.edu
- Plastic Molding | Processes Lab | NC State ISE www.ise.ncsu.edu
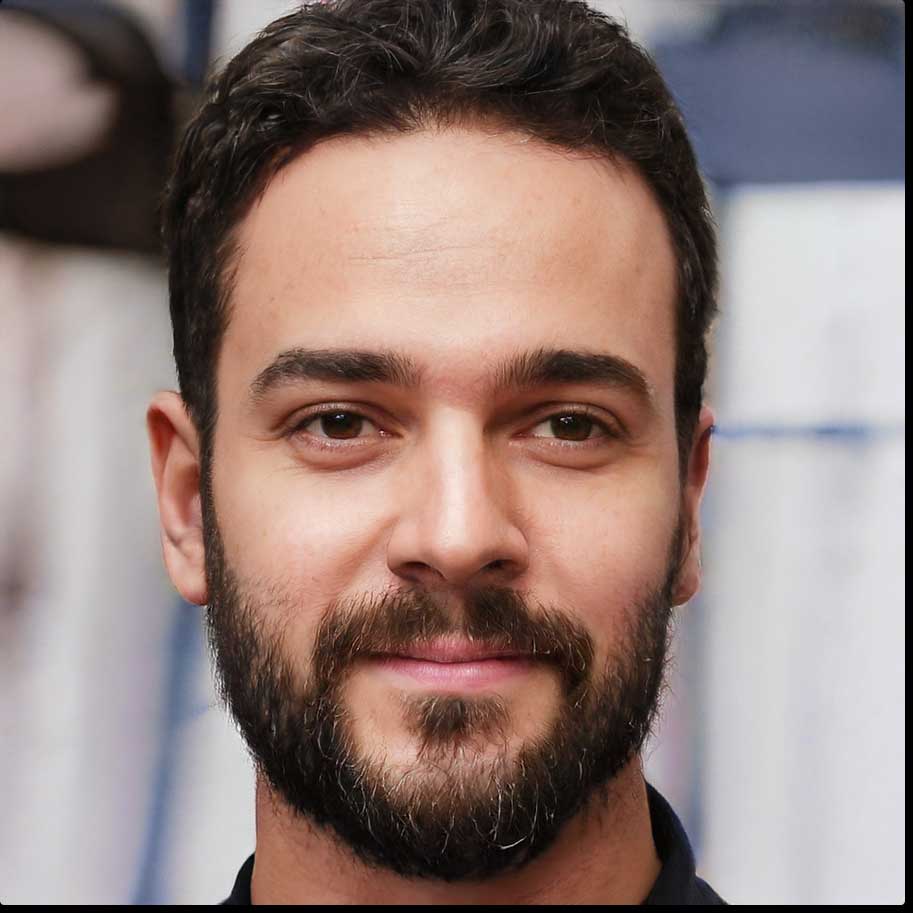