How to Be Plastic Tool Maker - Job Description, Skills, and Interview Questions
The use of plastic tool makers has grown significantly in recent years, as they offer a number of advantages over traditional metal tools. These benefits include a lightweight design, low production cost, and longer life span due to their resistance to corrosion. These features have allowed plastic tool makers to become a popular option for many businesses, as they can provide increased efficiency, reduce costs, and create higher quality products.
The increased use of plastic tool makers has had a positive effect on the manufacturing industry, as it has allowed for a more efficient production process and improved product quality. it has increased the demand for skilled workers in the manufacturing sector, as the production of plastic tools requires specialized knowledge and expertise.
Steps How to Become
- Obtain a high school diploma or equivalent. To become a plastic tool maker, you must have a high school diploma or equivalent. This includes a GED or other certificate of completion.
- Consider enrolling in a technical school or apprenticeship program. Many technical schools and apprenticeship programs offer training related to plastic tool making. These programs provide hands-on experience and allow you to gain valuable skills in the field.
- Learn about the tools used in plastic tool making. Plastic tool makers use a variety of tools to create and shape plastic components. Examples include drill presses, lathes, milling machines, and injection molding machines.
- Learn about the materials used in plastic tool making. It is important to understand the types of plastics used in the industry and how they can be manipulated to create various shapes and sizes.
- Pursue additional certifications and training if desired. Many employers require workers to have additional certifications or training in order to work as a plastic tool maker. Certifications may include safety training, mold making, and quality assurance.
- Find a job as a plastic tool maker. Once you have completed your training, you can begin looking for a job as a plastic tool maker. You can search online job boards or contact local plastics companies to inquire about open positions.
Becoming a skilled and qualified plastic tool maker requires dedication and hard work. First, you must gain the necessary theoretical knowledge by learning about the principles of plastic and the manufacturing processes used to create plastic tools. Next, you must have hands-on experience with the equipment and machinery used to craft these tools.
This can be achieved through apprenticeships, internships, or formal training programs. Once you have the necessary experience, you will need to hone your skills by practicing and perfecting your techniques. Finally, you must demonstrate your abilities and knowledge in order to become certified in your field.
Once certified, you will be able to work with confidence as a professional plastic tool maker.
You may want to check Plastic Recycling Technician, Plastic Machine Operator, and Plastic Extrusion Operator for alternative.
Job Description
- Design and build plastic injection molds for production of plastic parts.
- Create 3D CAD models for plastic parts and plastic molds.
- Use computer-aided design (CAD) software to modify existing designs or create new ones from scratch.
- Work with engineers to ensure accuracy of design specifications and tolerances.
- Develop tooling plans and process sheets for molding operations.
- Analyze design data and specifications to determine appropriate tooling and materials.
- Select and order materials, components, and tooling needed for production.
- Troubleshoot and address any molding issues that arise during production.
- Make modifications to existing molds as needed to improve production process.
- Perform routine maintenance on tools, equipment, and machinery.
Skills and Competencies to Have
- Knowledge of injection molding processes and techniques
- Proficiency in the use of computer-aided design (CAD) software
- Knowledge of machining, grinding, and assembly operations
- Ability to read and interpret engineering drawings and blueprints
- Ability to use a variety of hand and power tools
- Ability to troubleshoot complex problems
- Excellent communication skills
- Ability to work with a variety of materials, including metals, plastics, and composites
- Good organizational and problem-solving skills
- Attention to detail and accuracy in work product
Having a strong set of skills as a Plastic Tool Maker is essential for success in the field. Attention to detail, the ability to think critically and problem-solve, and the ability to follow instructions carefully are all important traits for this type of work. having knowledge of the tools and materials used to make plastic tools is also essential.
Understanding the basics of how to use a lathe, drill press, milling machine, and other tools is also important. Finally, knowing how to read engineering drawings, interpret specifications, and properly measure and inspect finished parts is necessary to ensure that the product meets the desired standards. All of these skills combined allow a Plastic Tool Maker to produce quality parts while working efficiently and keeping production costs low.
Plastics Quality Inspector, Plastic Molder, and Plastic Injection Molding Machine Operator are related jobs you may like.
Frequent Interview Questions
- What experience do you have in the production of plastic tools?
- How do you ensure the accuracy and quality of the plastic tools that you create?
- Describe a project where you were able to use your skills as a plastic tool maker.
- What processes do you use to manufacture plastic tools?
- How do you troubleshoot when problems arise in your plastic tool making process?
- What challenges have you encountered in your role as a plastic tool maker?
- Are there any particular methods or techniques that you prefer when creating plastic tools?
- How do you stay up to date on advances in the field of plastic tool making?
- Do you have any suggestions for improvement in regards to the production of plastic tools?
- What safety protocols do you follow when working with plastic tools?
Common Tools in Industry
- Hammer. Used to drive nails or strike other objects; example: a hammer with a curved claw.
- Screwdriver. Tool used to drive screws into or out of an object; example: a Phillips head screwdriver.
- Wrench. Tool used to tighten or loosen nuts and bolts; example: a box-end wrench.
- Pliers. Tool used to grip, bend and cut objects; example: a pair of needle-nose pliers.
- Drill. Powered tool used to make holes in materials; example: an electric drill.
- Saw. Used to cut through materials; example: a handsaw.
- Sander. Tool used to smooth surfaces; example: an orbital sanding machine.
- Router. Tool used to cut out shapes in materials; example: a router with a laminate trimmer bit.
- Grinder. Tool used to grind down materials; example: an angle grinder.
- Heat Gun. Tool used to apply heat to materials; example: a heat gun with variable temperature settings.
Professional Organizations to Know
- American Mold Builders Association (AMBA)
- Society of Plastics Engineers (SPE)
- Plastics Industry Association (PIA)
- International Association of Plastics Distribution (IAPD)
- International Plastics Designers and Manufacturers Association (IPDMA)
- Society of Manufacturing Engineers (SME)
- Tooling and Manufacturing Association (TMA)
- National Tooling and Machining Association (NTMA)
- Precision Machined Products Association (PMPA)
- Society of Plastics Industry (SPI)
We also have Plastics Production Worker, Plastic Packaging Technician, and Plastic Finisher jobs reports.
Common Important Terms
- Injection Molding. Process of forming plastic parts by injecting molten plastic material into a mold cavity.
- Thermoforming. Process of heating plastic sheets and then shaping them into desired shapes using vacuum or mechanical pressure.
- Blow Molding. Process of forming hollow plastic parts using air pressure.
- Vacuum Forming. Process of forming and shaping plastics using vacuum pressure.
- Rotational Molding. Process of forming plastic parts using a heated mold and rotating it to evenly distribute the molten plastic.
- Compression Molding. Process of forming and shaping plastic parts by applying pressure and heat to a pre-heated mold.
- Extrusion Molding. Process of forming and shaping plastic parts by forcing molten material through a die or opening.
- Casting. Process of forming and shaping plastic parts by pouring molten material into a mold and allowing it to cool and solidify.
- Fusion Welding. Process of joining two or more pieces of plastic together by melting them together.
- Ultrasonic Welding. Process of joining two or more pieces of plastic together by vibrating them at high frequency.
Frequently Asked Questions
Q1: What is a Plastic Tool Maker? A1: A Plastic Tool Maker is a type of manufacturing process used to create tools and parts from plastic materials. It involves the use of injection molding, extrusion, and other techniques to shape the plastic into the desired shape and size. Q2: What are the benefits of using a Plastic Tool Maker? A2: The benefits of using a Plastic Tool Maker include cost savings, shorter lead times, and improved product quality. Additionally, the process allows for increased flexibility in the design of parts and tools, as well as being able to produce parts with complex shapes and features. Q3: What materials can be used in Plastic Tool Maker? A3: Many different types of plastics can be used in Plastic Tool Maker processes, such as polypropylene, polyethylene, polycarbonate, polystyrene, ABS, and PVC. Q4: What is the typical lead time for Plastic Tool Maker? A4: The typical lead time for Plastic Tool Maker projects depends on the complexity of the product being created and the size of the order. Generally, lead times range from 4-6 weeks for smaller orders and 6-10 weeks for larger orders. Q5: What is the cost of using a Plastic Tool Maker? A5: The cost of using a Plastic Tool Maker depends on the size and complexity of the part or tool being produced. Generally, costs range from $500-$10,000 depending on the materials and production process used.What are jobs related with Plastic Tool Maker?
- Plastic Film Processor
- Plastic Fabrication Technician
- Plastics Technician
- Plastic Injection Molding Technician
- Plastic Artist
- Plastics Engineer
- Plastics Product Designer
- Plastic Mold Maker
Web Resources
- Plastic Injection mold tooling - Plastic Mold | Plastic Molding ... mold.world.edu
- Maker Tools and Materials - Makerspace Resources for K-12 ¦ k12maker.mit.edu
- Tool Maker Certificate of Achievement | HFC Catalog catalog.hfcc.edu
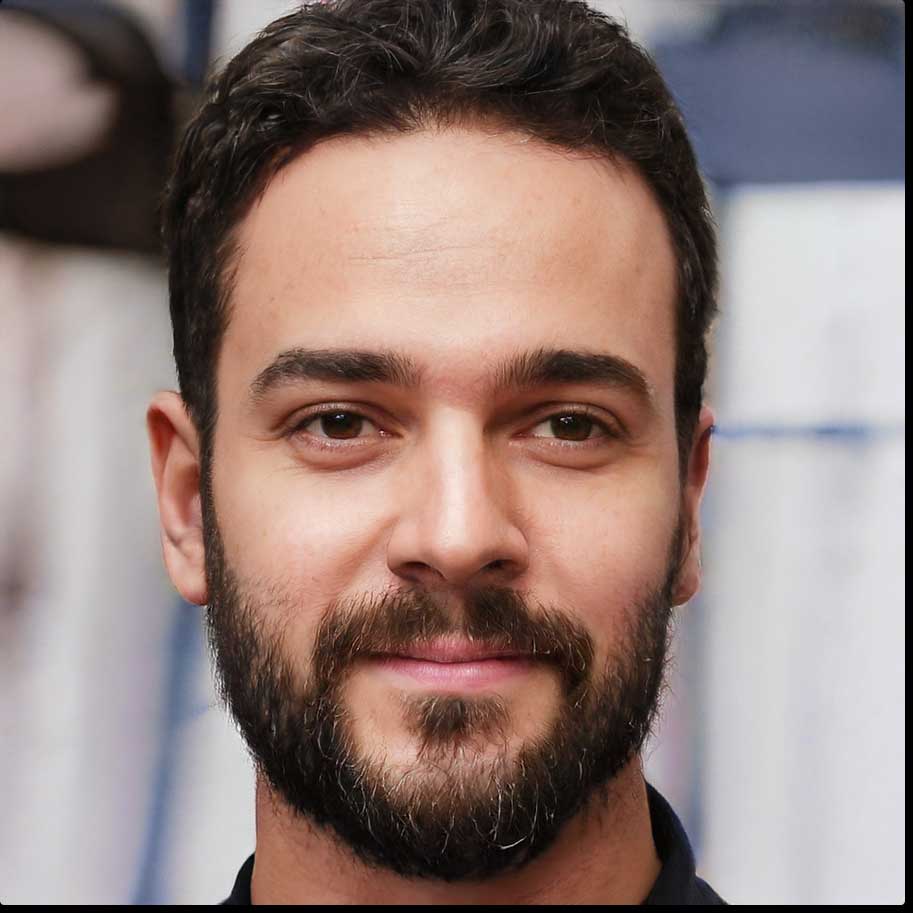