How to Be Plastic Finisher - Job Description, Skills, and Interview Questions
Plastic finishers play a crucial role in the plastic industry. They apply a range of finishes, like texturing, polishing, and coating, to plastic products in order to make them aesthetically pleasing and reduce the risk of damage or wear. As a result, it increases the longevity of the plastic products and ensures that they look attractive.
Furthermore, the application of finishes also helps to protect the plastic parts from corrosion and other environmental elements. this improves the quality and performance of the plastic products, making them more competitive in the market.
Steps How to Become
- Obtain a high school diploma or equivalent. Plastic finishers typically need a high school education or equivalent to get started in the field.
- Enroll in a vocational school or apprenticeship program. Many plastic finishers attend a vocational school or apprenticeship program to learn the skills necessary to become a plastic finisher. These programs typically include an introduction to the different types of plastics and the different processes used to finish them.
- Gain experience in the field. Once you have completed your training, it is important to gain experience in the field by working as an apprentice or assistant to an experienced plastic finisher. This will help you gain the skills and knowledge necessary to become a successful plastic finisher.
- Get certified. Many employers require plastic finishers to be certified by either the American Plastics Finishing Association (APFA) or the Plastic Finishing Institute (PFI). To become certified, you must pass an examination administered by either organization.
- Obtain a job. Once you have completed your training and gained experience in the field, you can begin looking for a job as a plastic finisher. You can find job openings through job search engines or by networking with other professionals in the field.
The process of finding a reliable and qualified Plastic Finisher can be a difficult task. To ensure that the chosen individual or firm is capable of delivering quality results, it is important to consider a few key factors. First, check the experience and expertise of the individual or company.
Consider their prior work history and their ability to complete projects in a timely manner. look for evidence of strong customer service and satisfaction ratings. Lastly, ask for references from past clients to determine if the Plastic Finisher is reliable and trustworthy.
Taking the time to research these factors will help ensure that the Plastic Finisher chosen is reliable and qualified for the job.
You may want to check Plastic Machine Operator, Plastics Production Worker, and Plastics Product Designer for alternative.
Job Description
- Prepare surfaces for painting, finishing, and sealing.
- Apply primers, sealers, and finish coats to products.
- Sand, file, and buff parts to prepare them for finishing.
- Inspect and test finished products for quality and accuracy.
- Operate buffing machines, air guns, and other equipment.
- Troubleshoot and repair faulty plastic parts.
- Cut and shape plastic materials using saws, drills, and other tools.
- Follow safety protocols when handling hazardous chemicals and materials.
- Maintain production records and log data in computer systems.
- Monitor stock levels of finishing materials.
Skills and Competencies to Have
- Attention to Detail: The ability to focus on the accuracy and precision of tasks while being mindful of the overall goal.
- Quality Control: Ability to inspect work and identify errors, as well as suggest ways to improve production.
- Mechanical Aptitude: Knowledge of mechanical tools and processes to complete tasks with efficiency and accuracy.
- Interpersonal Skills: Ability to communicate with fellow workers in a professional manner, as well as establish and maintain positive working relationships.
- Problem-Solving: Ability to identify problems, analyze possible solutions, and implement solutions in a timely manner.
- Time Management: Ability to prioritize tasks and manage time effectively to meet deadlines.
- Safety Awareness: Knowledge of safety procedures and regulations to ensure the safety of yourself and others.
- Flexibility: Adaptability to changing tasks and environments.
- Finishing Techniques: Knowledge of buffing, sanding, and polishing techniques for plastic components.
- Working with Chemicals: Proficiency in handling and mixing chemicals for a variety of finishing tasks.
The ability to accurately and efficiently finish plastic products is essential for any plastic finisher. A high level of precision and attention to detail are the most important skills for a plastic finisher to possess, as they must be able to produce consistent results with little to no margin of error. the plastic finisher must have a wide range of knowledge regarding different types of plastic and the tools used to finish them.
This knowledge is necessary in order to successfully operate the machines used for finishing plastics, and also to determine the most efficient and effective method for finishing each product. Without these skills, the finisher would not be able to complete their job properly and would cause delays in production, resulting in a decrease in profits for the company. Therefore, having the right skills is essential for any plastic finisher in order to ensure successful and timely production.
Plastic Molder, Plastic Artist, and Plastics Technician are related jobs you may like.
Frequent Interview Questions
- What experience do you have in plastic finishing?
- How would you ensure the highest quality of finish for a plastic product?
- Describe a difficult project you have worked on in the past involving plastic finishing.
- How do you troubleshoot issues with plastic finishing equipment?
- What safety protocols do you follow while working with hazardous materials?
- What methods do you use to check the quality of your finish?
- What strategies do you use to stay up to date on new developments in plastic finishing technology?
- Describe a time when you overcame a challenging situation while working on a plastic finishing job.
- What techniques do you use to ensure a consistent finish on multiple pieces of plastic?
- How do you prevent contamination of the plastic surface while working?
Common Tools in Industry
- Sander. A tool that is used to smooth the surface of materials such as wood, plastic, or metal. (e. g. orbital sander)
- File. A tool used to shape, smooth, or remove material from a surface. (e. g. flat file)
- Grinder. A tool used to grind down and polish surfaces. (e. g. die grinder)
- Drill. A tool used to make holes in materials such as wood, plastic, or metal. (e. g. cordless drill)
- Rasp. A tool used to shape and smooth surfaces with a coarse surface. (e. g. rat-tail rasp)
- Heat Gun. A tool used to apply heat to an area in order to soften it and make it more malleable. (e. g. butane heat gun)
- Buffer. A tool used to create a glossy finish on material surfaces by rubbing them with an abrasive material. (e. g. electric buffer)
- Polisher. A tool used to create a high-gloss finish on surfaces by polishing them with an abrasive material. (e. g. orbital polisher)
Professional Organizations to Know
- Society of Plastics Engineers
- International Association of Plastics Distribution
- Plastics Industry Association
- American Composites Manufacturers Association
- The Vinyl Institute
- International Plastics Exposition & Conference
- International Plastics Design Forum
- International Polymer Processing Society
- Resin Suppliers Association
- British Plastics Federation
We also have Plastic Packaging Technician, Plastic Recycling Technician, and Plastic Mold Maker jobs reports.
Common Important Terms
- Polishing. The process of smoothing a surface with abrasives.
- Buffing. The process of burnishing a surface to a high gloss finish.
- Sanding. The process of abrading a surface with sandpaper or other abrasive materials.
- Grinding. The process of removing material from a workpiece using an abrasive wheel.
- Finishing. The process of refining a surface to achieve the desired level of smoothness and shine.
- Tumbling. The use of vibratory media in a rotating barrel to deburr, polish, and clean parts.
- Sandblasting. The use of high-pressure air or steam to remove surface contaminants and coatings from a workpiece.
- Painting. The application of a protective or decorative coating to a surface using a brush, roller, or sprayer.
- Coating. The application of a protective or decorative layer to a surface to protect it from environmental elements and improve its appearance.
- Welding. The process of joining two pieces of metal by melting them together with a heat source, such as an electric arc or flame.
Frequently Asked Questions
Q1: What is a Plastic Finisher? A1: A Plastic Finisher is a person or machine that smoothes and shapes plastic products, such as toys, containers, or automotive parts. Q2: What skills are required of a Plastic Finisher? A2: A Plastic Finisher must have knowledge of the plastic material and the tools used to shape it. They must also have good hand-eye coordination and be able to follow directions and technical specifications. Q3: What tools are used by a Plastic Finisher? A3: Tools used by a Plastic Finisher include sanders, grinders, drill presses, saws, and polishers. Q4: What safety precautions should be taken when using a Plastic Finisher? A4: Safety precautions for using a Plastic Finisher include wearing protective gear such as goggles and gloves, using a dust mask, and taking care to operate tools according to the manufacturer's instructions. Q5: Are there any certifications required for someone to become a Plastic Finisher? A5: Certification may not be required in order to become a Plastic Finisher, but some employers may prefer candidates who have been trained in the safe use of the tools and materials used in the trade.What are jobs related with Plastic Finisher?
- Plastics Engineer
- Plastics Quality Inspector
- Plastic Injection Molding Technician
- Plastic Film Processor
- Plastic Extrusion Operator
- Plastic Injection Molding Machine Operator
- Plastic Tool Maker
- Plastic Fabrication Technician
Web Resources
- Plastic Waste Factsheet | Center for Sustainable Systems css.umich.edu
- About - Plastic EDU plastic.education
- The Plastic in our Oceans - Science in the News sitn.hms.harvard.edu
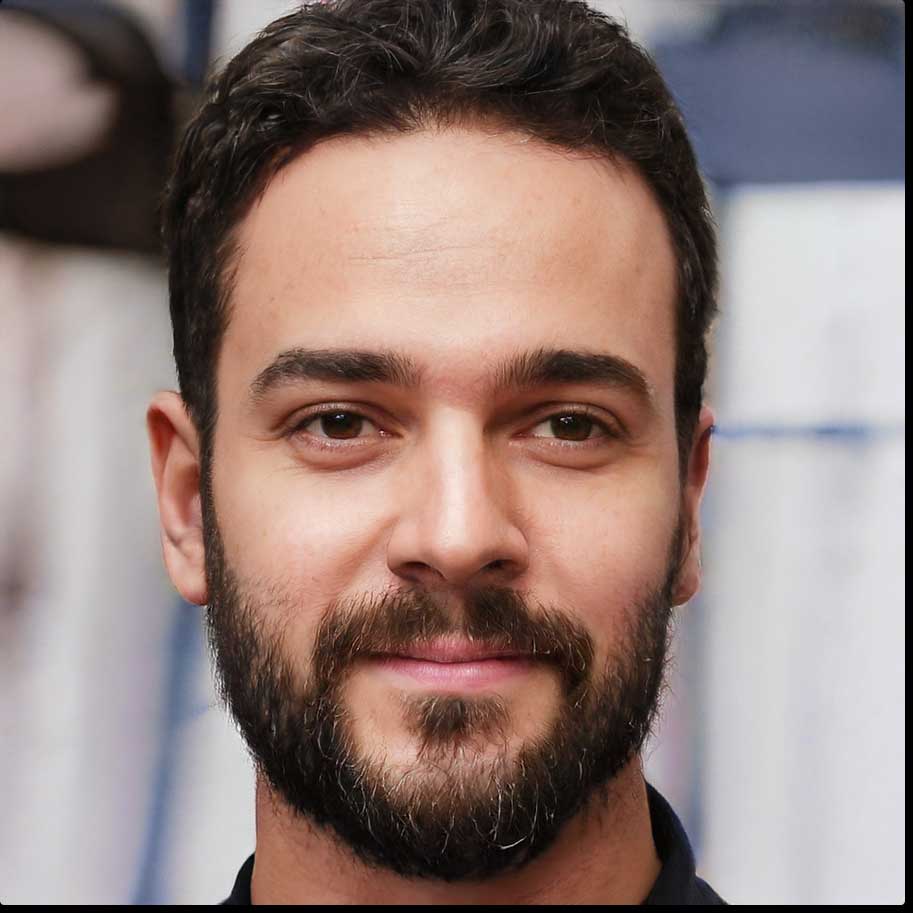