How to Be Plastic Film Processor - Job Description, Skills, and Interview Questions
The increasing use of plastic film has had a significant effect on processors. As demand for plastic packaging increases, processors must invest in the latest state-of-the-art equipment and technology to keep up with the growing demand. This includes investing in multi-layer lines for co-extrusion and lamination, as well as sophisticated printing and converting equipment.
In addition, processors must have highly trained and knowledgeable personnel to operate their equipment. As a result of these investments, plastic film processors are able to produce high-quality products that meet the most stringent requirements of their customers.
Steps How to Become
- Learn about the plastic film processing industry. Become familiar with the types of plastic films available and the types of equipment used in the processing industry.
- Develop a strong knowledge base of safety and operation procedures. Learn the necessary safety protocols and procedures for operating the different types of equipment used in the plastic film processing industry.
- Complete a training program. Many employers require that prospective plastic film processors complete an accredited training program before they are hired. These programs typically involve both classroom instruction and hands-on experience.
- Obtain certifications. Many employers also require that prospective plastic film processors obtain certifications in order to work in the field. Obtain certifications from the National Plastics Film Processor Certification Program or similar organizations.
- Find a job as a plastic film processor. Use job search sites and job fairs to network with employers who are hiring in the plastic film processing industry.
- Continue to develop your skills and knowledge. The plastic film processing industry is constantly changing and evolving, so it is important to stay on top of developments in the field in order to remain competitive.
The ability to process plastic film to a high standard is dependent upon having the right equipment and skilled personnel. The first step is to ensure the processor is using the latest technology and has the necessary tools to process the film at the highest levels of quality. Quality assurance technicians should also be employed to ensure that the process meets the required standards and that the product meets customer expectations.
Furthermore, a processor should have experienced staff who are knowledgeable about the properties of the film, its characteristics, and how to manipulate it. Finally, the processor should have a good understanding of the end-use product that is being produced, as this will help them understand how to develop a process that will deliver the desired outcome. By having the right tools, personnel, knowledge, and understanding, a processor can produce high-quality plastic film products and be an ideal and capable partner for its customers.
You may want to check Plastic Injection Molding Machine Operator, Plastic Tool Maker, and Plastic Artist for alternative.
Job Description
- Set-Up Technician: Responsible for preparing and setting up machines for plastic film processing.
- Quality Assurance Technician: Responsible for evaluating and testing plastic films to ensure quality standards are met.
- Maintenance Technician: Responsible for troubleshooting and repairing plastic film processing machines.
- Machine Operator: Responsible for operating plastic film processing machines according to established safety and quality standards.
- Supervisor: Responsible for overseeing the operations of the plastic film processing team, ensuring that safety and quality standards are met.
- Materials Handler: Responsible for receiving, storing, and delivering raw materials used in plastic film processing.
- Lab Technician: Responsible for conducting research, development, and testing of new plastic films.
- Production Planner: Responsible for planning and scheduling production runs of plastic films.
- Data Analyst: Responsible for analyzing data from plastic film processing operations to identify areas of improvement.
- Shipping/Receiving Clerk: Responsible for packing and shipping plastic films to customers, as well as receiving shipments of raw materials from suppliers.
Skills and Competencies to Have
- Knowledge of plastic film manufacturing processes, including extrusion, calendaring, winding, printing, and laminating
- Understanding of plastics materials, including resins, additives, and modifiers
- Knowledge of plastic film characteristics and performance specifications
- Ability to troubleshoot and diagnose issues with machinery and equipment
- Ability to set-up and operate plastic film processing equipment
- Ability to adjust and maintain process parameters for optimal performance
- Experience in working with die systems
- Ability to read and interpret technical drawings, blueprints, and schematics
- Understanding of safety protocols and operating procedures
- Ability to work independently as well as part of a team
- Good problem-solving skills
- Strong communication skills
Having a good knowledge of plastic film processing is essential for any processor. It involves understanding the mechanical and chemical processes involved in transforming a raw material into a usable product. This includes knowing how to heat and cool, stretch and shrink, and chemically treat the plastic film.
processors must have an understanding of the physical properties of the plastic film and be able to identify any flaws or defects in the product. Understanding the different types of plastic film, such as polyethylene, vinyl, and polypropylene, is necessary to determine the best process for each material. Processors must also have good problem-solving skills to troubleshoot any issues that may arise during the production process.
Finally, good communication skills are essential for processors to effectively communicate with other team members, vendors, and customers.
Plastics Product Designer, Plastic Mold Maker, and Plastic Fabricator are related jobs you may like.
Frequent Interview Questions
- What experience do you have working with plastic films?
- How have you maintained quality control in prior positions?
- What safety practices do you follow when processing plastic film?
- Describe a time when you had to troubleshoot a machine malfunction related to plastic film processing.
- How do you stay organized when managing multiple tasks related to processing plastic film?
- What methods do you use to ensure accurate measurements when cutting plastic film?
- Describe a process you have implemented to improve the efficiency of plastic film processing.
- How do you ensure that the finished product meets customer expectations?
- Do you have any experience working with automated systems for plastic film processing?
- What challenges have you encountered when working with plastic films, and how did you resolve them?
Common Tools in Industry
- Extruder. A machine used to melt and form plastic film into shapes and sizes, (eg: example: extruding plastic film into a sheet of a certain thickness).
- Shrinker. A machine used to shrink plastic film to a specific size, (eg: example: shrinking a large roll of plastic film to fit a printers specifications).
- Slitter. A machine used to cut plastic film into various widths, (eg: example: cutting a roll of plastic film into strips of different widths).
- Winder. A machine used to wind plastic film onto spools or reels, (eg: example: winding a long roll of plastic film onto a reel for easy storage).
- Heat Sealer. A machine used to fuse two pieces of plastic film together, (eg: example: sealing the edges of a bag made from two pieces of plastic film).
- Trimmer. A machine used to trim plastic film into a specific shape, (eg: example: trimming the edges of a plastic sheet to make it fit into a specific container).
Professional Organizations to Know
- American Chemistry Council (ACC)
- Plastic Industry Association (PIA)
- Society of the Plastics Industry (SPI)
- American Plastics Council (APC)
- International Society of Plastic Engineers (ISPE)
- Association of Postconsumer Plastic Recyclers (APR)
- Institute of Scrap Recycling Industries (ISRI)
- Film & Bag Federation (FBF)
- International Plastics Association (IPA)
- European Plastics Converters (EuPC)
We also have Plastic Injection Molding Technician, Plastic Extrusion Operator, and Plastics Quality Inspector jobs reports.
Common Important Terms
- Extrusion. The process of forcing melted plastic through a die oropening to form a continuous profile, such as a film or sheet.
- Calendering. The process of passing a sheet or film between two or more smooth, heated rolls to produce a uniform thickness and smooth surface.
- Laminating. The process of bonding two or more layers of material together, such as a plastic film and paper.
- Coating. The process of applying a thin layer of plastic onto another material, such as a fabric or paper.
- Slitting. The process of cutting a roll of material into narrower widths.
- Printing. The process of applying a design or pattern onto plastic film using inks, dyes, or other methods.
- Rewinding. The process of winding a roll of material onto smaller cores.
- Die Cutting. The process of cutting a material into shapes using a die.
Frequently Asked Questions
What is a Plastic Film Processor?
A Plastic Film Processor is a machine used to cut and shape plastic films. It typically consists of a cutting knife and a heating element, which are used to cut and form the film into desired shapes or sizes.
What types of plastic films can be processed?
Plastic Film Processors can be used to process a variety of different types of plastic films, such as polyethylene, polypropylene, PVC, PET, and nylon.
What are the benefits of using a Plastic Film Processor?
The primary benefit of using a Plastic Film Processor is that it can significantly reduce the amount of time and effort required to cut and shape plastic films. Additionally, the use of a machine ensures accuracy and consistency in the finished product.
What safety measures should be taken when using a Plastic Film Processor?
When using a Plastic Film Processor, it is important to take safety precautions such as wearing protective clothing, safety glasses, and gloves. Additionally, it is important to ensure that the machine is operated in accordance with the manufacturer's instructions and safety guidelines.
How often should a Plastic Film Processor be serviced?
In order to maintain optimal performance, it is recommended that a Plastic Film Processor be serviced at least once per year. Regular servicing helps to ensure that the machine is operating properly and that any worn parts are replaced.
What are jobs related with Plastic Film Processor?
- Plastics Production Worker
- Plastic Fabrication Technician
- Plastics Engineer
- Plastic Packaging Technician
- Plastic Molder
- Plastic Machine Operator
- Plastic Finisher
- Plastics Technician
Web Resources
- Plastic Processing Polymer Engineering Center UWMadison pec.engr.wisc.edu
- Plastic film | UW Facilities - University of Washington facilities.uw.edu
- Plastic Film | Sustainability sustainability.lehigh.edu
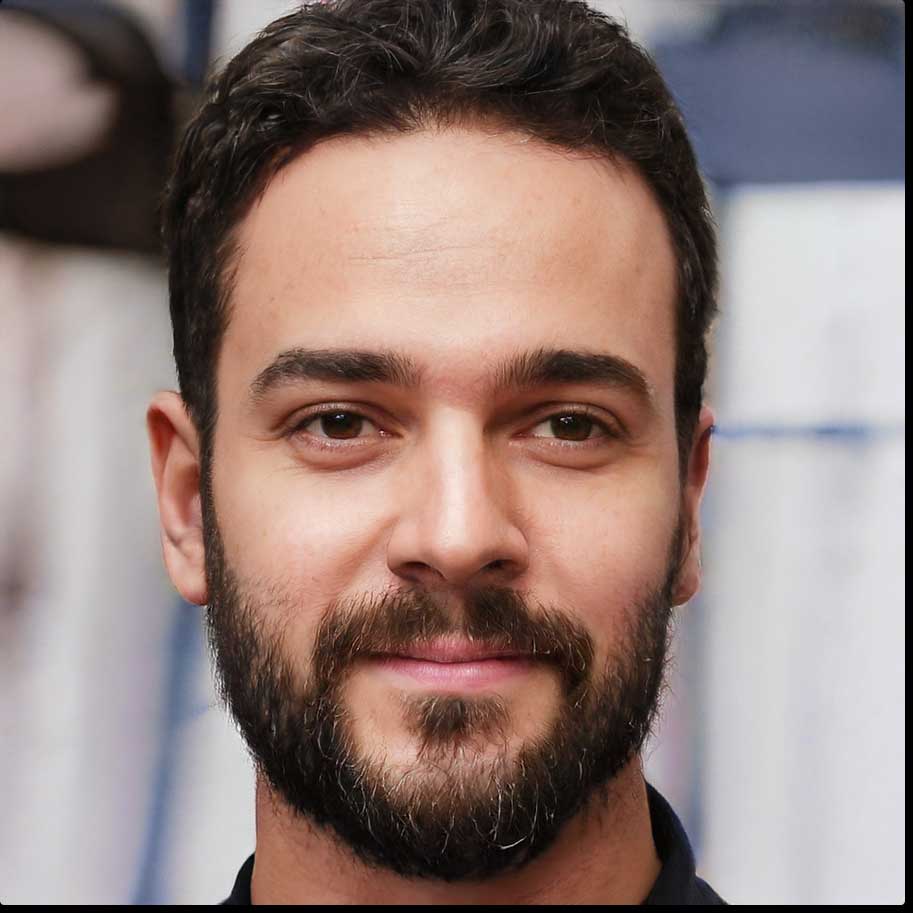