How to Be Metallurgist - Job Description, Skills, and Interview Questions
Metallurgists can have a major influence on the development of new materials and technologies. By studying metal structures, properties, and characteristics, they can identify ways to make metals stronger, lighter, and more resistant to corrosion. This knowledge can lead to the development of new materials with improved characteristics, which can then be used to create advanced products such as aerospace components and medical implants.
In turn, these new products can lead to improved efficiency, safety, and cost savings in various industries. metallurgists can also find ways to reduce environmental impacts by developing more eco-friendly metal production processes. the work of metallurgists contributes significantly to technological progress and economic growth.
Steps How to Become
- Obtain a High School Diploma or GED. Before you can become a metallurgist, you must complete a high school diploma or GED. Most employers prefer applicants to have a minimum of a high school diploma or GED equivalent.
- Pursue a Degree in Metallurgy. After completing your high school diploma or GED, the next step is to pursue a degree in metallurgy. You can pursue either an undergraduate degree or a masters degree in metallurgy depending on your career goals. Make sure to attend an accredited college or university that offers a program in metallurgy.
- Gain Work Experience. After obtaining your degree in metallurgy, you should gain some work experience in the field. You can do this by interning at a metalworking plant or working as a research assistant at a university. This will give you valuable hands-on experience that will help you stand out when applying for jobs as a metallurgist.
- Obtain a Professional Certification. In order to become a metallurgist, you will need to obtain professional certification. You can do this by taking and passing the American Society for Metals Certification Exam. This exam is designed to test your knowledge of metallurgical principles and practices.
- Apply for Jobs in Metallurgy. Once you have obtained your professional certification, you will be eligible to apply for jobs in metallurgy. You can search for job openings through job sites, newspapers, and industry publications. It is also a good idea to network with professionals in the field to get an idea of what employers are looking for in a potential employee.
Continuing to stay current and competent in the field of Metallurgy requires a great deal of dedication and hard work. Keeping up with the latest advances in the field is essential for success in the industry. To do this, Metallurgists should regularly attend seminars and conferences, read industry publications, and take continuing education classes to stay up-to-date on the latest developments.
networking with other professionals in the field and joining professional organizations can help provide access to new information and resources. By taking advantage of these opportunities, Metallurgists can remain knowledgeable of the newest technologies and trends in the field, enabling them to stay competitive in an ever-changing industry.
You may want to check Metallurgical Welding Specialist, Metallurgical Lab Technician, and Metallurgical Sales Engineer for alternative.
Job Description
- Process Engineer
- Plant Manager
- Quality Control Technician
- Maintenance Technician
- Safety Inspector
- Metallurgist
- Casting Technician
- Data Analyst
- Design Engineer
- Production Supervisor
Skills and Competencies to Have
- Knowledge of metallurgical principles, practices and processes.
- Knowledge of materials science and engineering.
- Knowledge of specialized testing and analysis techniques.
- Ability to interpret technical specifications and drawings related to metal products and processes.
- Familiarity with welding, soldering, and other metal joining techniques.
- Ability to operate and troubleshoot tools, machinery, and equipment used in metal production.
- Understanding of safety procedures and industry standards.
- Excellent problem-solving and analytical skills.
- Excellent written and verbal communication skills.
- Ability to work independently and as part of a team.
Metallurgists are highly-skilled professionals who use their knowledge of metal and its properties to work with raw materials and create products for a variety of industries. These professionals must possess a range of abilities, including an understanding of metallurgy principles, engineering principles, and the ability to think critically and solve complex problems. They must also have excellent communication and interpersonal skills to be able to effectively collaborate with colleagues, customers, and suppliers.
The success of a Metallurgist depends on their ability to accurately assess the properties of metals, evaluate the strength of alloys, and recommend the best heat-treatment processes to achieve desired results. Their expertise is also essential in ensuring the safety and integrity of metal products and components. As a result, Metallurgists play an integral role in the production of high-quality industrial products.
Metallurgical Plant Manager, Metallurgical Project Engineer, and Metallurgical Process Engineer/Metallurgist are related jobs you may like.
Frequent Interview Questions
- What experience do you have working with metals?
- How would you describe your experience with metal fabrication and welding?
- What processes have you used to analyze metals for their properties and composition?
- Do you have experience with heat treating metal products?
- What safety protocols have you followed when working with metal materials?
- What is your experience with developing new metallurgical processes?
- How do you stay up to date on the latest metallurgical research?
- How do you troubleshoot problems that arise during metalworking processes?
- What methods do you use to assess the quality of metal products?
- What processes do you use to minimize scrap and waste during metalworking operations?
Common Tools in Industry
- Band Saw. A power saw used to cut metal into desired shapes and sizes (eg: cutting a round pipe).
- Drill Press. A machine tool used to drill holes in metal (eg: making holes in a sheet of metal).
- Grinder. A machine used to grind metal surfaces (eg: sharpening a drill bit).
- Lathe. A machine tool used to shape metal using a rotating cutting tool (eg: threading a bolt).
- Milling Machine. A machine tool used to shape metal using a rotating cutting tool (eg: cutting a groove in a metal block).
- Oxy-Acetylene Torch. Equipment used to cut metal with heat (eg: cutting a pipe).
- Shear. A machine tool used to cut sheet metal (eg: cutting a sheet of metal into smaller pieces).
- Welding Machine. Equipment used to join two pieces of metal with heat (eg: joining two pieces of steel together).
Professional Organizations to Know
- American Institute of Mining, Metallurgical, and Petroleum Engineers (AIME)
- The Minerals, Metals & Materials Society (TMS)
- International Association for Metallurgy and Materials (IAMM)
- Society of Mining, Metallurgy and Exploration (SME)
- American Foundry Society (AFS)
- International Iron and Steel Institute (IISI)
- International Association for Steel Structures (IASSC)
- International Copper Association (ICA)
- International Nickel Study Group (INSG)
- International Magnesium Association (IMA)
We also have Metallurgical Quality Control Technician, Metallurgical Technician/Dimensional Inspector, and Metallurgical and Materials Engineer jobs reports.
Common Important Terms
- Metallography. The study of metal structure, composition and properties.
- Alloy. A mixture of two or more elements in which the major component is a metal.
- Fracture Mechanics. The study of how materials fail under stress.
- Heat Treatment. The process of changing the physical and/or chemical properties of a metal by heating and cooling it.
- Casting. The process of forming a metal object by pouring molten metal into a mold.
- Forging. The process of shaping a metal object by hammering it into shape.
- Welding. Joining two pieces of metal together by melting them together with an electric arc or other heat source.
- Machining. The process of cutting, shaping, or forming a material using a machine tool.
- Corrosion. The deterioration of a material due to its reaction with its environment.
- Metallurgy. The science of extracting metals from their ores and refining them for use in various products.
Frequently Asked Questions
Q1: What is Metallurgist? A1: Metallurgist is a professional who studies the physical and chemical behavior of metallic elements and their mixtures, known as alloys. Q2: What kind of work does a Metallurgist do? A2: A Metallurgist may work with metals such as steel, aluminum, titanium, and magnesium, and they may analyze the properties of metals, develop new materials, and study the effects of corrosion. Q3: What qualifications are required to become a Metallurgist? A3: To become a Metallurgist, one typically needs a bachelors degree in metallurgical engineering or a related field. Additionally, experience such as internships or apprenticeships may be beneficial. Q4: What industries employ Metallurgists? A4: Metallurgists are employed in a variety of industries including automotive, aerospace, manufacturing, electronics, and energy. Q5: What tools do Metallurgists use? A5: Metallurgists use tools such as microscopes, spectroscopes, X-ray diffraction instruments, and computer-aided design software to analyze and develop metals and alloys.What are jobs related with Metallurgist?
- Metallurgical Inspector
- Metallurgical Engineer
- Metallurgical Maintenance Technician
- Metallurgical Technician
- Metallurgical Draftsperson
- Metallurgical Process Engineer
- Metallurgical Operator
- Metallurgical Technician Supervisor
- Metallurgical Research Scientist
Web Resources
- What does a metallurgist do? - The University of Queensland study.uq.edu.au
- Metallurgist : The University of Western Australia - UWA www.uwa.edu.au
- Home - Metallurgical and Materials Engineering metallurgy.mines.edu
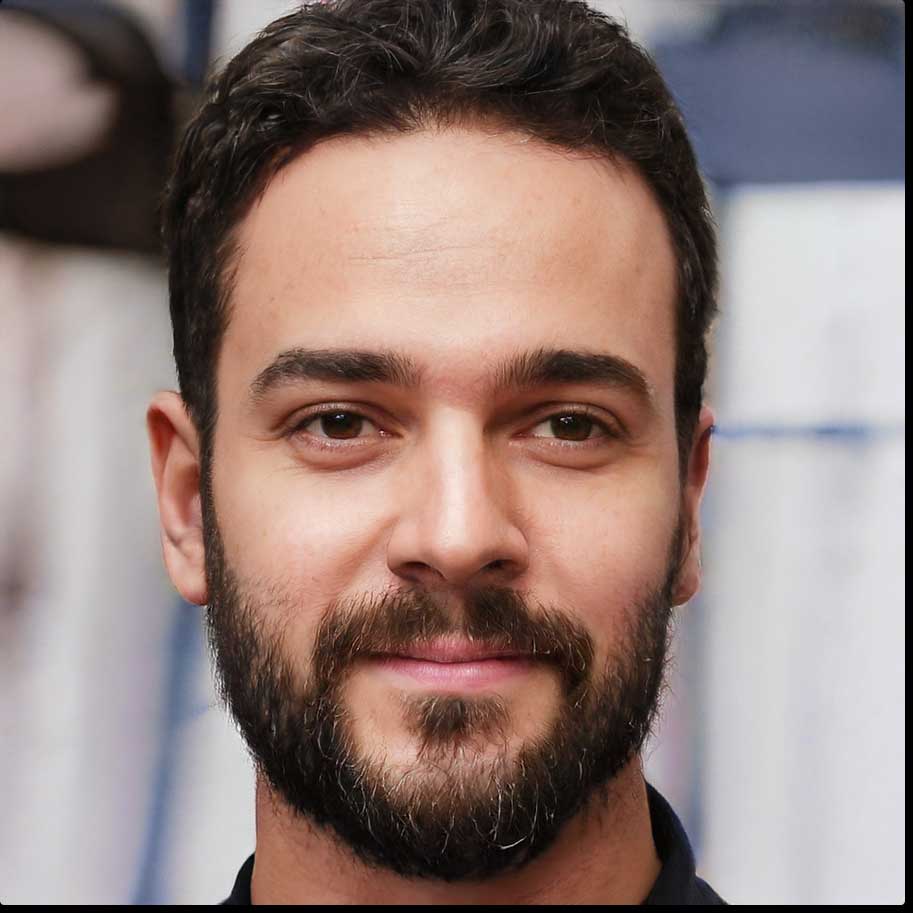