How to Be Metallurgical Technician - Job Description, Skills, and Interview Questions
Steps How to Become
- Obtain a High School Diploma or GED. Most employers require metallurgical technicians to have a high school diploma or equivalent.
- Complete a Postsecondary Program. Some employers prefer applicants who have completed a postsecondary program in metallurgical technology or a related field. These programs provide a comprehensive overview of the principles and processes involved in metallurgical testing and analysis.
- Gain Work Experience. Although some employers may hire recent graduates, most prefer to hire metallurgical technicians who have work experience. Students may be able to gain valuable experience by participating in internships or apprenticeships.
- Obtain Professional Certification. Professional certification is not always required, but it may help applicants stand out from the competition. The American Society for Nondestructive Testing (ASNT) offers a Level I certification in basic visual inspection and Level II certification in advanced visual inspection, among other certifications.
- Participate in Continuing Education. Metallurgical technicians should stay abreast of developments in the field by taking part in continuing education opportunities. Seminars, workshops, and online courses can all help technicians stay current on industry trends and hone their skills.
Being a Metallurgical Technician requires staying ahead and being capable of the ever-changing technology. Keeping up to date with the latest trends, developments and advancements in the field is essential to staying ahead. This means reading trade publications and attending seminars and conferences to stay abreast of the latest innovations.
staying technically proficient is important to keeping up with the latest technological developments. This means taking courses, seminars, workshops and certifications to stay current with the latest technologies. Finally, networking with other professionals in the industry is a great way to stay informed and up to date with industry trends and developments, as well as to establish contacts and gain valuable insights from other professionals.
You may want to check Metallurgist, Metallurgical Project Engineer, and Metallurgical Quality Control Technician for alternative.
Job Description
- Perform metallurgical and materials engineering tests and experiments, including tensile, fatigue, corrosion, impact, and hardness tests.
- Monitor and document results from testing and experiments in accordance with established procedures and regulations.
- Interpret test results and create reports, making recommendations for improvement or changes as necessary.
- Develop new processes and techniques to improve the quality and efficiency of metallurgical and materials engineering processes.
- Troubleshoot issues with metallurgical or materials engineering processes or systems.
- Develop and implement safety protocols to ensure the safety of workers using metallurgical or materials engineering equipment.
- Monitor the quality of finished products to ensure they meet established standards.
- Provide technical support to customers and colleagues regarding metallurgical and materials engineering processes.
- Research industry standards, trends, and new technologies to stay current in the field of metallurgical and materials engineering.
- Maintain accurate records of testing, experiments, and results.
Skills and Competencies to Have
- Knowledge of metallurgical principles, processes, and procedures.
- Ability to interpret metallurgical results and propose actions based on findings.
- Familiarity with metallurgical lab equipment and tools.
- Proficiency in using metallurgical software packages, such as finite element analysis (FEA) and computational fluid dynamics (CFD).
- Knowledge of welding processes and inspection techniques.
- Ability to understand and interpret technical drawings and specifications.
- Excellent problem-solving and troubleshooting skills.
- Ability to effectively communicate with supervisors, peers, and customers.
- Strong analytical and organizational skills.
- Knowledge of safety protocols and compliance policies.
Metallurgical technicians play an important role in the metallurgical industry, as they are responsible for making sure that metals and alloys meet the required production standards. The most important skill a metallurgical technician must have is a deep knowledge of metallurgy and its processes. This includes understanding the chemical, mechanical, and physical properties of metals and alloys, as well as the methods of testing them.
the technician should have a good grasp on the principles of metallurgy, including heat treatment, welding, and various casting techniques. Furthermore, they should also be adept at problem-solving and possess strong communication skills in order to effectively communicate with other members of the team. With these skills, technicians are able to identify potential issues with metals and alloys, helping to ensure that production runs smoothly and efficiently.
these skills are vital to the success of any metallurgical operation.
Metallurgical Process Engineer, Metallurgical Welding Specialist, and Metallurgical Process Engineer/Metallurgist are related jobs you may like.
Frequent Interview Questions
- What experience do you have in the metallurgical field?
- What makes you the best candidate for this position?
- Describe a difficult situation you faced in a previous job and how you handled it.
- How do you ensure the accuracy of your work?
- What safety protocols do you follow when working with hazardous materials?
- How do you stay up to date on the latest industry developments?
- Describe a project you have worked on that required extensive problem solving.
- How would you go about troubleshooting a metallurgical issue?
- What software tools are you familiar with that are relevant to metallurgy?
- Are you familiar with quality control protocols in the metallurgical field?
Common Tools in Industry
- Furnace. Used to heat and melt metals such as iron and steel. (e. g. Electric Arc Furnace)
- Spectrometer. Used to analyze the composition of metals. (e. g. X-Ray Fluorescence Spectrometer)
- Tensile Testing Machine. Used to determine the strength of metals. (e. g. Universal Testing Machine)
- Metallurgical Microscope. Used to view the microstructure of metals. (e. g. Polarizing Light Microscope)
- Hardness Tester. Used to measure the hardness of metals. (e. g. Brinell Hardness Tester)
- Impact Tester. Used to test the impact resistance of metals. (e. g. Charpy Impact Tester)
- Scanning Electron Microscope (SEM). Used to view the surface structure of metals at very high magnifications. (e. g. Field Emission Scanning Electron Microscope)
- X-ray Diffraction. Used to determine the crystal structure of metals. (e. g. X-ray Powder Diffraction)
- Analytical Balance. Used to measure the weight of materials accurately. (e. g. Digital Analytical Balance)
- Heat Treating Ovens. Used to harden or soften metals by applying heat or cooling them rapidly. (e. g. Gas-Fired Heat Treating Oven)
Professional Organizations to Know
- American Foundry Society (AFS)
- National Association for Surface Finishing (NASF)
- American Welding Society (AWS)
- Association of Iron and Steel Technology (AIST)
- Institute of Materials, Minerals and Mining (IOM3)
- Society of Manufacturing Engineers (SME)
- American Society for Metals (ASM)
- The Minerals, Metals & Materials Society (TMS)
- International Titanium Association (ITA)
- International Magnesium Association (IMA)
We also have Metallurgical Plant Manager, Metallurgical Sales Engineer, and Metallurgical Lab Technician jobs reports.
Common Important Terms
- Metallurgy. The study of the physical and chemical behavior of metallic elements, their intermetallic compounds, and their mixtures, which are known as alloys.
- Metallographic Analysis. The study of the microstructure of a metal or alloy. It is used to examine the grain size, shape and distribution, as well as the presence of impurities and inclusions.
- Heat Treatment. The process of heating and cooling metals in order to change their physical and chemical properties.
- Hardening. A heat treatment process used to increase the hardness of a material.
- Tempering. A heat treatment process used to reduce the hardness of a material.
- Stress Relieving. A heat treatment process used to reduce internal stresses in a material.
- Annealing. A heat treatment process used to soften a material.
- Non-Destructive Testing. The process of examining a material or component without causing any permanent damage or alteration.
- Welding. The process of joining two pieces of metal together by melting and fusing them.
- Machining. The process of removing material from a workpiece in order to create a desired shape or finish.
Frequently Asked Questions
What is the job of a Metallurgical Technician?
A Metallurgical Technician is responsible for conducting tests on metal products and analyzing the results to determine their physical and chemical properties.
What qualifications are required to become a Metallurgical Technician?
To become a Metallurgical Technician, you must have a Bachelor's degree in metallurgy, materials science, or a related field, as well as experience in metalworking and quality control.
What types of tests do Metallurgical Technicians perform?
Metallurgical Technicians use a variety of testing methods, including hardness testing, tensile testing, and optical microscopy, to evaluate metal products and determine their performance characteristics.
What is the average salary of a Metallurgical Technician?
The average salary of a Metallurgical Technician is $62,000 per year.
What industries employ Metallurgical Technicians?
Metallurgical Technicians are employed by a variety of industries, including aerospace, automotive, electronics, and construction.
What are jobs related with Metallurgical Technician?
- Metallurgical Operator
- Metallurgical Engineering Technician
- Metallurgical Draftsperson
- Metallurgical and Materials Engineer
- Metallurgical Engineer
- Metallurgical Maintenance Technician
- Metallurgical Research Scientist
- Metallurgical Technician/Dimensional Inspector
- Metallurgical Technician Supervisor
Web Resources
- Metallurgical Laboratory Technician - etsu.edu www.etsu.edu
- Metallurgy Technician 2022-10233 - career.arizona.edu career.arizona.edu
- Metallurgical and Materials Engineering Degree | Montana Tech www.mtech.edu
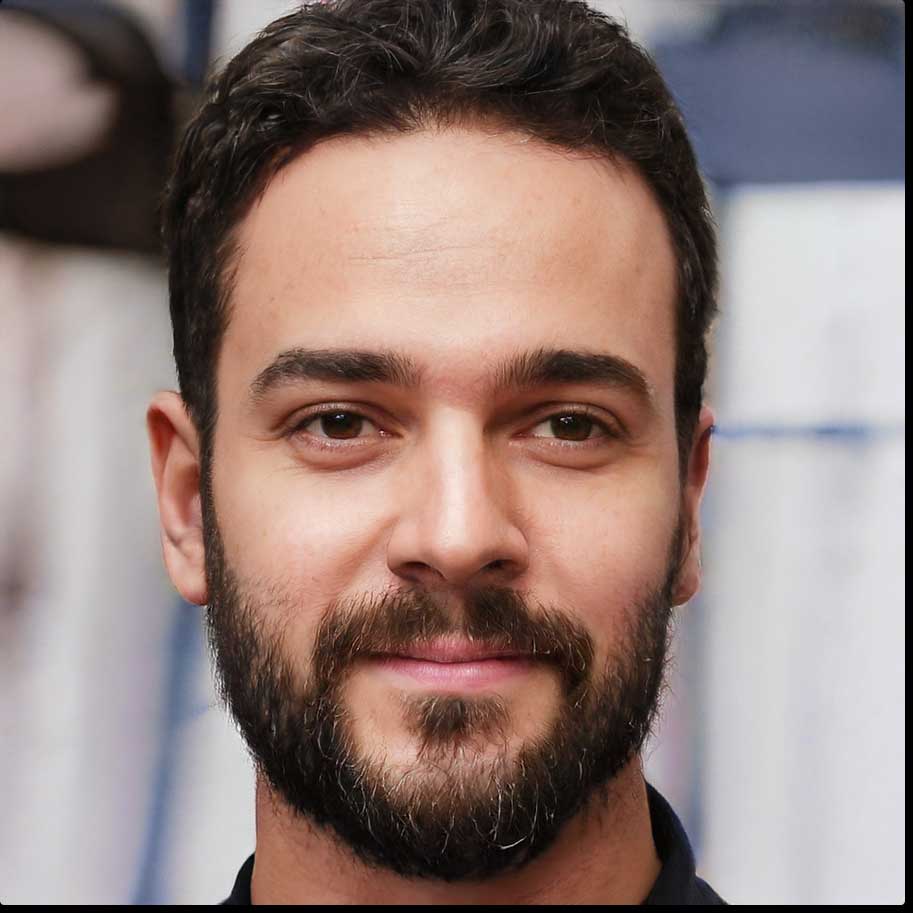