How to Be Metallurgical Engineer - Job Description, Skills, and Interview Questions
Metallurgical engineering is a key engineering discipline that combines materials science and manufacturing processes in the production of metal components. It is critical to the success of the manufacturing industry and its impact on the economy. The cause and effect of metallurgical engineering are seen in the ability to create superior metal components with increased performance, improved safety, and greater reliability.
The engineer must create the processes and materials to achieve these results. This includes a detailed understanding of the properties of metals and alloys, heat treatments, and joining processes. With this knowledge, the engineer can select the optimal material and process combination for a specific application.
This results in improved product quality, reduced costs, and more efficient production cycles. The positive effects of metallurgical engineering can be seen in increased customer satisfaction, improved brand recognition, and increased sales.
Steps How to Become
- Get a Bachelor's Degree. The first step towards becoming a Metallurgical Engineer is to pursue a bachelor's degree in metallurgical engineering. This four-year degree provides you with the foundational skills and knowledge in the field, such as materials science, mathematics, chemistry, physics, and engineering principles.
- Gain Relevant Experience. Many employers prefer to hire engineers with experience, so gaining relevant experience is key. You can gain such experience through internships or co-op programs in the field. Other ways to gain experience include volunteer positions in engineering firms, research assistantships, and working as a laboratory technician.
- Acquire Certification. Certification is typically not required for metallurgical engineers, but it can help you stand out from the competition and increase your job prospects. The American Foundry Society offers a Certified Metallurgist (CM) designation for those with at least five years of experience in the field.
- Consider Additional Education. Depending on your career goals, you may want to consider additional education and training. For example, if you're interested in research and development, pursuing a master's degree in metallurgical engineering or materials science may be a good idea.
- Join Professional Organizations. Joining professional organizations can help you stay updated on the latest industry developments and build your professional network. The American Institute of Mining, Metallurgical, and Petroleum Engineers (AIMMPE) is a popular organization for metallurgical engineers.
Metallurgical engineers must stay updated and efficient in order to effectively design and develop new materials and processes. Keeping up with the latest technologies and advancements in the field is essential to staying ahead of the competition. One important way to stay informed is to attend industry conferences, workshops, and events.
Doing so allows metallurgical engineers to learn about the latest trends, best practices, and processes in their field. staying organized and prioritizing tasks is another key element in being an efficient metallurgical engineer. By taking the time to plan out and map out tasks and projects, metallurgical engineers can ensure that they are focusing their efforts on the most important tasks and staying productive throughout the day.
Finally, continuing to educate oneself through seminars, courses, and other learning opportunities is another great way for metallurgical engineers to stay up to date with the latest advancements in their fields. By investing in their own education, metallurgical engineers can ensure that they are always ahead of the curve.
You may want to check Metallurgical Quality Control Technician, Metallurgical Process Engineer, and Metallurgical Lab Technician for alternative.
Job Description
- Develop processes to separate metals from ore, refine metals, and fabricate metals into products.
- Design and implement quality control procedures to ensure the purity of metals.
- Monitor and evaluate process performance, production costs, and waste management.
- Troubleshoot and optimize metallurgical processes to improve efficiency and reduce costs.
- Develop new techniques for processing materials to meet specific customer requirements.
- Design test protocols to analyze the physical and chemical characteristics of metals.
- Investigate the causes of metallurgical defects in manufactured parts and recommend corrective action.
- Develop models to predict the behavior of metals under various conditions.
- Supervise technicians and other personnel in the operation of metallurgical equipment.
- Prepare technical reports and documents for customers, management, and regulatory agencies.
Skills and Competencies to Have
- Knowledge of metallurgy principles and processes, including thermodynamics, physical metallurgy, corrosion, and failure analysis
- Understanding of materials science, including mechanical properties and physical characteristics
- Ability to analyze and interpret data from laboratory tests, experiments and production processes
- Familiarity with computer-aided design (CAD) and computer-aided manufacturing (CAM) software
- Familiarity with industry standards and specifications for metals and alloys
- Knowledge of welding and fabrication processes
- Ability to develop new processes and methods to improve production efficiency
- Problem solving skills and analytical ability
- Ability to work independently and as part of a team
- Excellent communication skills, both written and verbal
Metallurgical engineering is an important field in the manufacturing industry, as it is essential for producing high quality products. The most important skill for a Metallurgical Engineer to have is an understanding of materials science and the ability to apply this knowledge to the design and production of metals and alloys. This involves understanding the properties of metals, their metallurgy and their behavior under different conditions, such as heat, pressure and chemical reactions.
In addition, Metallurgical Engineers must also be able to develop efficient production processes and techniques, as well as understand the economics of industrial production. By having a thorough understanding of materials science, Metallurgical Engineers are able to develop new and improved materials for use in industry, which can lead to improved quality, efficiency and cost-effectiveness. This in turn can result in better products and services, higher customer satisfaction and increased profitability for companies.
Metallurgical Technician/Dimensional Inspector, Metallurgical Welding Specialist, and Metallurgical Technician Supervisor are related jobs you may like.
Frequent Interview Questions
- What experience do you have in metallurgical engineering?
- What processes do you have experience with?
- How have you contributed to process improvements in the past?
- How have you used computer simulations to improve processes?
- Describe a project you have been involved with that had a successful outcome.
- What challenges have you faced in the past and how did you address them?
- What methods do you use to analyze data and draw conclusions?
- How do you stay up to date on developments in the field?
- What safety protocols do you follow in your work?
- How do you manage competing priorities in a fast-paced environment?
Common Tools in Industry
- Metallographic Analysis Tools. Used to examine the microstructure of metals and their alloys. (eg: Scanning Electron Microscope)
- Metallurgical Testing Tools. Used to evaluate the mechanical properties of metals and alloys. (eg: Tensile Testing Machine)
- Heat Treatment Tools. Used to change the physical and mechanical properties of metals and alloys through heating and cooling. (eg: Heat Treatment Furnace)
- Nondestructive Testing Tools. Used to detect defects in metal components without damaging them. (eg: X-ray Fluorescence Spectrometer)
- Failure Analysis Tools. Used to analyze the cause of metal component breakage and failure. (eg: Scanning Acoustic Microscope)
- Automated Process Control Tools. Used to monitor and control manufacturing processes in metal processing plants. (eg: Flow Meters)
Professional Organizations to Know
- The American Institute of Mining, Metallurgical, and Petroleum Engineers (AIME)
- The Minerals, Metals & Materials Society (TMS)
- Society for Mining, Metallurgy & Exploration (SME)
- International Association for Process Metallurgy (IAPM)
- The Institute of Materials, Minerals and Mining (IOM3)
- The International Metallographic Society (IMS)
- The Iron and Steel Society (ISS)
- The Australasian Institute of Mining and Metallurgy (AusIMM)
- The Canadian Institute of Mining, Metallurgy and Petroleum (CIM)
- The European Federation of Corrosion (EFC)
We also have Metallurgical and Materials Engineer, Metallurgical Inspector, and Metallurgical Draftsperson jobs reports.
Common Important Terms
- Metallurgy. The science and technology of processing metals to obtain desired properties and characteristics.
- Alloy. A mixture or combination of two or more elements, at least one of which is a metal.
- Heat Treatment. A process used to change the physical and/or chemical properties of a material by heating and cooling it in a controlled manner.
- Casting. The process of forming a solid object from a liquid or other material by pouring it into a mold.
- Welding. A process used to join two pieces of metal together by melting and fusing them together.
- Corrosion. The process of deterioration of a material due to chemical or electrochemical reaction with its environment.
- Metallography. The study of the microstructure of metals and alloys to determine their properties and characteristics.
- Physical Metallurgy. The study of the physical properties of metals and alloys, including their mechanical and electrical properties.
- Powder Metallurgy. The process of forming objects from powdered metals and alloys using heat and pressure.
- Non-Destructive Testing. A variety of techniques used to evaluate the properties of a material without causing any damage to the material.
Frequently Asked Questions
What is a Metallurgical Engineer?
A Metallurgical Engineer is a professional who specializes in designing and managing the manufacturing processes used to create materials and products from metals and other materials.
What qualifications are needed to become a Metallurgical Engineer?
To become a Metallurgical Engineer, you will typically need a bachelor's degree in metallurgical engineering or a related field such as materials science, chemical engineering, or mechanical engineering.
What does a Metallurgical Engineer do?
A Metallurgical Engineer is responsible for designing and managing the manufacturing processes used to produce metals and other materials into products. This includes overseeing the process from extraction of raw materials to refining and processing the material into a usable form.
What are some common job responsibilities of a Metallurgical Engineer?
Common job responsibilities of a Metallurgical Engineer include researching, designing, and testing new production processes; overseeing production operations to ensure quality and safety standards are met; and analyzing product performance. They also develop maintenance and safety protocols for machinery and equipment.
What is the average salary of a Metallurgical Engineer?
The average salary of a Metallurgical Engineer is $76,820 per year, according to PayScale.com.
What are jobs related with Metallurgical Engineer?
- Metallurgical Technician
- Metallurgist
- Metallurgical Engineering Technician
- Metallurgical Sales Engineer
- Metallurgical Project Engineer
- Metallurgical Operator
- Metallurgical Plant Manager
- Metallurgical Maintenance Technician
- Metallurgical Research Scientist
Web Resources
- Metallurgical Engineer | NC State Online and Distance Education online-distance.ncsu.edu
- Metallurgical Engineering - South Dakota School of ¦ www.sdsmt.edu
- Home - Metallurgical and Materials Engineering metallurgy.mines.edu
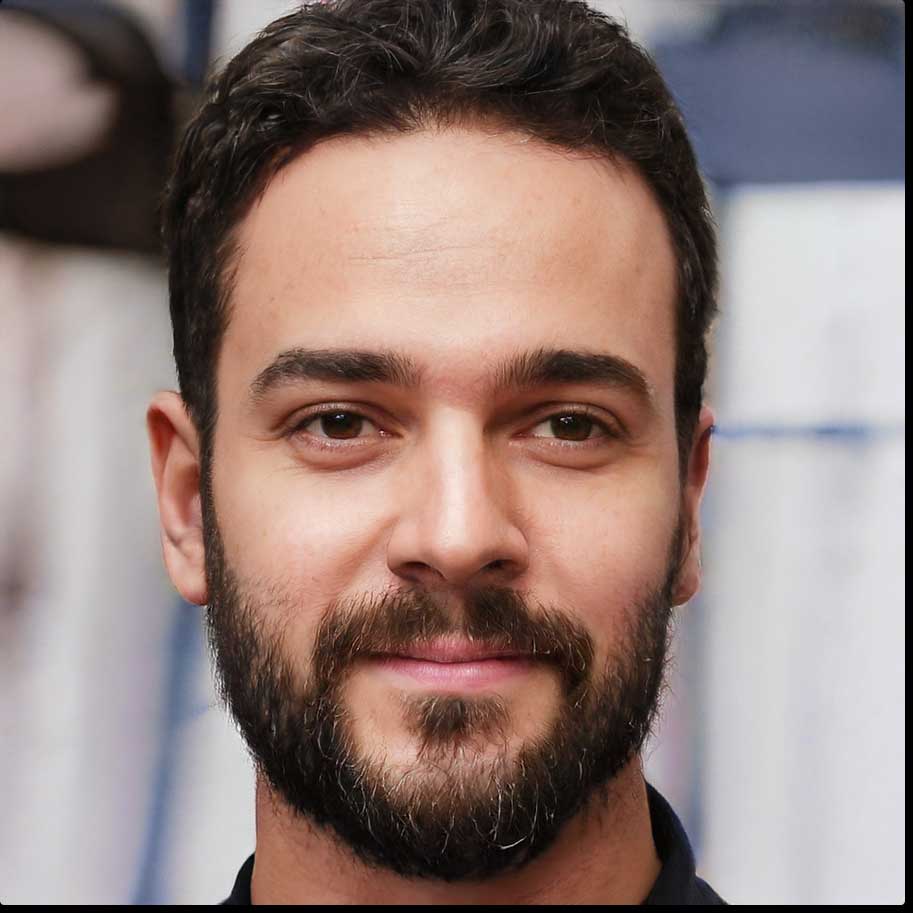