How to Be Metallurgical Maintenance Technician - Job Description, Skills, and Interview Questions
The Metallurgical Maintenance Technician is a critical role in the maintenance and operations of a metallurgical plant. This technician is responsible for performing routine maintenance and repairs on equipment and machines to ensure the safety and efficiency of the plant. Without proper maintenance, the plant could develop malfunctions and breakdowns that could lead to costly repairs, lost production time, and even injury.
The Metallurgical Maintenance Technician must be knowledgeable about the various processes and procedures related to steel production and have a strong understanding of the different machines and equipment used in the production process. they need to be prepared to respond to emergency situations quickly and safely. When metallurgical maintenance technicians are proficient in their job, they ensure the safety of the workers as well as the accuracy of the production process.
Steps How to Become
- Earn a High School Diploma or GED. The minimum educational requirement to become a Metallurgical Maintenance Technician is usually a high school diploma or equivalent.
- Complete an Apprenticeship Program. Many employers prefer Metallurgical Maintenance Technicians who have completed an apprenticeship program in metallurgy or a related field. Apprenticeship programs are sometimes available through local trade schools or community colleges.
- Obtain On-the-Job Training. Even if you have completed an apprenticeship program, you may still need to obtain on-the-job training from experienced Metallurgical Maintenance Technicians. This type of training can provide you with the hands-on experience you need to succeed in this career.
- Gain Industry Recognition. There are a number of industry certifications available for Metallurgical Maintenance Technicians, such as the Certified Metallurgy Technician (CMT) certification. Earning a certification can help you stand out from other applicants and demonstrate your knowledge and skills in the field.
- Advance Your Career. With experience, you may be able to advance to more complex positions, such as a Metallurgical Maintenance Supervisor. In this role, you may oversee the work of other technicians and provide guidance on how to best complete tasks.
Metallurgical maintenance technicians are essential for the efficient and effective operation of many industrial processes. They utilize their expertise in materials science and engineering to inspect, repair, and service the machinery and equipment used in metallurgical operations. As a result, they help to ensure that production is running smoothly and safely, while also minimizing downtime and costs associated with breakdowns.
By regularly checking and servicing machinery and equipment, they can also extend their lifespan, helping companies to save money by avoiding premature replacements. this helps to create an ideal and efficient metallurgical environment.
You may want to check Metallurgical Plant Manager, Metallurgist, and Metallurgical Inspector for alternative.
Job Description
- Perform preventative maintenance on all metallurgical equipment
- Inspect and repair malfunctioning equipment
- Troubleshoot and diagnose mechanical, electrical, hydraulic, and pneumatic issues
- Adjust and calibrate metallurgical equipment to meet operational requirements
- Inspect, evaluate, and recommend replacement or repair of metallurgical equipment parts
- Perform welding and brazing operations as necessary
- Monitor and control inventory of spare parts
- Develop and implement safe work practices
- Maintain accurate records of metallurgical maintenance activities
- Liaise with vendors to coordinate repairs and obtain parts
Skills and Competencies to Have
- Knowledge of metallurgical principles and practices.
- Ability to read, analyze, and interpret technical documents, drawings and schematics.
- Strong knowledge of safety protocols and procedures.
- Ability to troubleshoot and diagnose mechanical equipment failures.
- Experience in performing preventive and corrective maintenance on metallurgical equipment.
- Proficient in welding and metal fabrication techniques.
- Ability to operate various metallurgical testing equipment.
- Ability to perform metallurgical calculations and interpret test results.
- Knowledge of computerized maintenance management systems (CMMS).
- Skilled in using hand tools, power tools, and other related equipment.
- Excellent written and verbal communication skills.
Metallurgical Maintenance Technicians need to have a wide range of skills to effectively carry out their job. One of the most important skills for a Metallurgical Maintenance Technician to possess is problem-solving. This includes troubleshooting, diagnosing and repairing complex mechanical systems, as well as being able to identify potential problems before they become critical.
Problem-solving also requires the ability to think critically, analyze data and make sound decisions. Metallurgical Maintenance Technicians must have good communication and interpersonal skills in order to interact with customers, vendors and colleagues. They must be able to explain complex technical information in an understandable way.
Finally, they must be able to stay organized and adhere to safety protocols. Having these skills is essential for Metallurgical Maintenance Technicians, who are responsible for maintaining the safety and efficiency of various types of industrial equipment.
Metallurgical Technician Supervisor, Metallurgical Research Scientist, and Metallurgical Process Engineer/Metallurgist are related jobs you may like.
Frequent Interview Questions
- What experience do you have with metallurgical maintenance?
- What have been some of the most challenging metallurgical maintenance tasks you have been responsible for?
- How do you ensure that all safety protocols are followed while performing maintenance tasks?
- What steps do you take to troubleshoot and repair metallurgical equipment?
- How do you stay up-to-date on the latest metallurgical maintenance best practices?
- Describe a time when you had to perform metallurgical maintenance under tight deadlines.
- How do you prioritize tasks and manage your workload when faced with multiple maintenance requests?
- What have been some of the biggest challenges you have faced when performing metallurgical maintenance?
- What methods do you use to ensure that all parts and components are in good working order?
- Describe a successful project or initiative you have taken to improve metallurgical maintenance efficiency or effectiveness.
Common Tools in Industry
- Pneumatic Wrenches. Tools used to loosen and tighten nuts and bolts quickly. (eg: Chicago Pneumatic CP749)
- Soldering Irons. Used to join two or more metal surfaces together by melting a metal alloy. (eg: Weller WLC100)
- Cutting Torches. A welding tool used to cut metal objects by burning or melting away material. (eg: Victor Journeyman)
- Hydraulic Presses. Used to exert force on an object or surface by using a pressurized fluid. (eg: Dake Hydraulic Press)
- Grinders. Used to reduce the size of a piece of metal or plastic by grinding it with an abrasive wheel. (eg: Milwaukee 4 1/2-Inch Grinder)
- Welding Machines. A device used to join two pieces of metal together by melting and fusing them. (eg: Miller MIG Welder)
- Metal Lathes. Machines used to shape metal by spinning it and cutting into it with a sharp tool. (eg: Clausing Lathe)
- Drills. Tools used to bore holes into metal and other materials. (eg: Milwaukee Cordless Drill)
Professional Organizations to Know
- American Welding Society
- American Society of Mechanical Engineers
- Association for Iron & Steel Technology
- American Foundry Society
- Society for the Advancement of Material and Process Engineering
- International Association for Bridge and Structural Engineering
- Nondestructive Testing Association
- Industrial Heating Equipment Association
- International Institute of Welding
- International Magnesium Association
We also have Metallurgical Draftsperson, Metallurgical Engineering Technician, and Metallurgical Quality Control Technician jobs reports.
Common Important Terms
- Metallurgy. The study and science of metals and their properties, such as heat treatment and alloying.
- Abrasion. The process of wearing away metal by rubbing.
- Hardening. A process of strengthening metal through heat treatment.
- Annealing. A process of softening metal through heat treatment.
- Corrosion. The deterioration of metal caused by chemical reactions or oxidation.
- Machining. The process of cutting, drilling, or grinding away unwanted material from a metal object.
- Welding. Joining two pieces of metal together using heat and pressure.
- Heat Treatment. A process of changing the physical and/or mechanical properties of a metal object by heating and cooling it to specific temperatures.
- Alloying. The process of mixing two or more metals together to form a new material with different characteristics.
- Non-Destructive Testing (NDT). Testing procedures that use a variety of methods to evaluate the condition or integrity of an object without causing damage or destruction to the object.
Frequently Asked Questions
What is a Metallurgical Maintenance Technician?
A Metallurgical Maintenance Technician is a skilled professional who inspects, repairs, and maintains equipment used to process metals and minerals, such as furnaces, tanks, and boilers.
What qualifications are required for the role of Metallurgical Maintenance Technician?
Metallurgical Maintenance Technicians typically need a high school diploma or equivalent, along with experience in welding, machine shop operations, and metallurgical processes. They must also have a working knowledge of safety practices and regulations related to the industry.
What are some of the duties of a Metallurgical Maintenance Technician?
A Metallurgical Maintenance Technician's duties may include inspecting and testing equipment, performing preventative maintenance, troubleshooting and repairing malfunctions, ordering and replacing parts, and documenting maintenance activities.
What tools are used by Metallurgical Maintenance Technicians?
Metallurgical Maintenance Technicians use tools such as wrenches, pliers, grinders, and welding equipment to complete their tasks. They may also use power tools such as drills and saws.
What is the average salary for a Metallurgical Maintenance Technician?
The average salary for a Metallurgical Maintenance Technician is $52,000 per year.
What are jobs related with Metallurgical Maintenance Technician?
- Metallurgical Technician
- Metallurgical Engineer
- Metallurgical Lab Technician
- Metallurgical Sales Engineer
- Metallurgical Process Engineer
- Metallurgical Operator
- Metallurgical and Materials Engineer
- Metallurgical Technician/Dimensional Inspector
- Metallurgical Welding Specialist
Web Resources
- Metallurgical Laboratory Technician - etsu.edu www.etsu.edu
- Overview - Metallurgical and Materials Engineering www.mtech.edu
- Maintenance Technician Training in California www.sjvc.edu
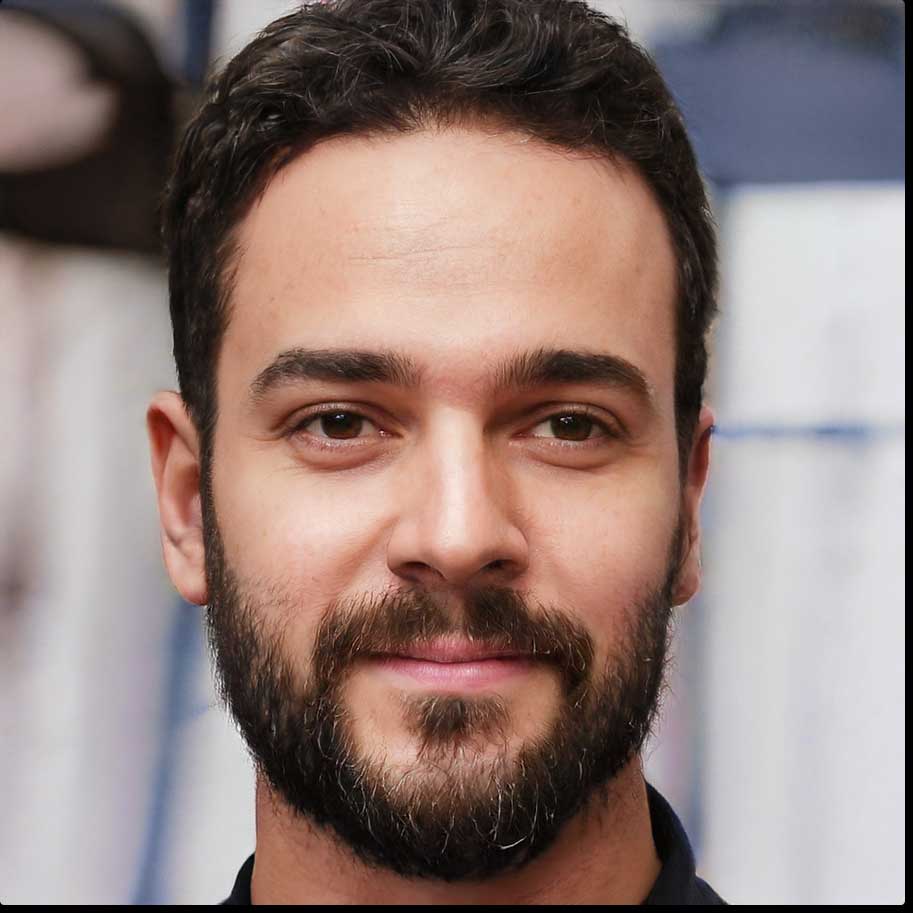