How to Be Metallurgical Operator - Job Description, Skills, and Interview Questions
Metallurgical operators are responsible for operating and maintaining metallurgical equipment used in the production of metal products. This job requires a great deal of knowledge and skill, as well as the ability to use complex machinery. As a result of their expertise, metallurgical operators can help to ensure that metal products are produced quickly, efficiently, and safely.
They may also be involved in tasks such as inspecting and testing metal products for quality control, setting up machines for production runs, and troubleshooting any problems that arise in the production process. Furthermore, their knowledge of metallurgy can help to identify and resolve any issues related to corrosion or other forms of metal degradation. the expertise of metallurgical operators helps to ensure that metal products are manufactured to the highest possible standards of quality.
Steps How to Become
- Obtain a high school diploma or equivalent. Many employers require applicants to have a high school diploma or GED to become a metallurgical operator.
- Enroll in a post-secondary metallurgical program. Many technical schools and community colleges offer metallurgical programs, which provide students with the knowledge and skills necessary to become a metallurgical operator.
- Gain work experience. Many employers prefer applicants with at least one year of experience in a related field, such as welding, machining or manufacturing.
- Obtain certification. Many employers require metallurgical operators to be certified by the American Welding Society.
- Find a job. After obtaining the necessary training and certification, prospective metallurgical operators can search for job openings with metal fabrication companies, steel mills and other related businesses.
In order to remain qualified and up-to-date as a Metallurgical Operator, it is important to stay informed about industry advancements and regulatory changes. This can be accomplished through industry-specific publications, attending conferences, and engaging in continuing education. Keeping active in the field will help operators remain knowledgeable about the latest safety regulations and technological developments, which can then be put into practice to ensure that operations run smoothly and efficiently.
operators should regularly participate in job-specific training courses to hone their skills and stay knowledgeable about the most current practices in the field. By staying informed and engaged in the metallurgical industry, operators can ensure that they remain qualified and up-to-date.
You may want to check Metallurgical Draftsperson, Metallurgical Quality Control Technician, and Metallurgical Technician/Dimensional Inspector for alternative.
Job Description
- Operate and monitor furnace and other metallurgical equipment to refine metals, alloy steels, and fabricate parts or products.
- Monitor gauges, meters, and control panels to ensure proper temperature, pressure, and vacuum levels.
- Adjust controls to regulate the flow of materials into furnace, ensure proper mixing of alloys, and control cooling rate.
- Start and stop operation of furnaces and ancillary equipment.
- Analyze metallurgical test samples to ensure adherence to quality standards.
- Inspect parts for defects and ensure that specifications are met.
- Maintain records of production data such as temperatures, material quantities, and processing times.
- Troubleshoot and repair equipment as necessary.
- Perform preventative maintenance on equipment such as filters, valves, and pumps.
- Load and unload materials into furnaces.
- Follow safety protocols when handling hazardous materials.
Skills and Competencies to Have
- Knowledge of metallurgical processes and techniques
- Ability to monitor and adjust metallurgical processes
- Ability to operate and maintain metallurgical equipment
- Ability to interpret metallurgical test results
- Knowledge of safety procedures and precautions
- Knowledge of quality standards and testing procedures
- Ability to troubleshoot and repair equipment
- Knowledge of numerical and analytical methods
- Ability to read and understand technical documents
- Strong organizational and time management skills
Metallurgical operators must have a wide range of skills to ensure that their work is successful and meets quality standards. The most important skill for a metallurgical operator is their knowledge of the metallurgical process. They need to understand the chemical and physical properties of various metals and how those properties can affect the end product.
They also need to be able to interpret and understand metallurgical drawings, as well as being able to identify and locate the necessary materials for the operation. Furthermore, they must be able to use specialized tools and equipment in order to carry out the job properly and efficiently. In addition, metallurgical operators must have strong communication skills to be able to effectively explain procedures and processes to other team members, as well as being able to work well with supervisors and other personnel.
Finally, they must have good problem-solving skills and be able to think on their feet in order to troubleshoot any issues that may arise during the process. All these skills combined help the operator successfully complete their task and produce a high-quality product.
Metallurgical Technician Supervisor, Metallurgical Engineer, and Metallurgical Welding Specialist are related jobs you may like.
Frequent Interview Questions
- What experience do you have in a metallurgical operating role?
- Are you familiar with the safety protocols and guidelines for working in a metallurgical environment?
- How do you ensure accuracy and precision in your work?
- What steps do you take to ensure quality control in a metallurgical process?
- What methods do you use to troubleshoot issues with a metallurgical process?
- Describe a challenging situation youve encountered in a metallurgical role, and how you overcame it.
- How comfortable are you working with computers and software specifically designed for metallurgical operations?
- Describe a time when you had to prioritize multiple tasks in a metallurgical environment.
- How do you ensure accurate data entry when managing a metallurgical process?
- How do you stay updated on the latest advances in metallurgical technology?
Common Tools in Industry
- Crucible. A heat-resistant container used to melt and heat metals. (eg: Steel Crucible)
- Forge. A furnace used to heat metal for shaping or welding. (eg: Gas Forge)
- Filler Rods. Metal rods used for welding and brazing. (eg: Copper Filler Rods)
- Tongs. A tool used to grip hot objects without burning oneself. (eg: Welding Tongs)
- Pliers. A tool with two jaws used for gripping and turning objects. (eg: Needle-Nose Pliers)
- Flux. A material used to prevent oxidation during melting or welding. (eg: Borax Flux)
- Anvil. A metal block used for hammering and shaping metals. (eg: Steel Anvil)
- Drill Bit. A cutting tool used to make holes in metal. (eg: Cobalt Drill Bit)
- Hammer. A tool used to strike metal by hand or with a mallet. (eg: Ball Peen Hammer)
- Grinder. An abrasive tool used to shape and polish metal surfaces. (eg: Bench Grinder)
Professional Organizations to Know
- American Foundry Society
- International Magnesium Association
- Society of Diecast Engineers
- Institute of Materials, Minerals and Mining
- American Welding Society
- Steel Founders' Society of America
- International Association for Sheet Metal, Air, Rail and Transportation Workers
- American Society for Metals
- Association for Iron & Steel Technology
- International Tin Research Institute
We also have Metallurgical Process Engineer, Metallurgical Lab Technician, and Metallurgical Process Engineer/Metallurgist jobs reports.
Common Important Terms
- Smelting. The process of melting ore in order to separate out its metal content.
- Alloying. The process of mixing two or more metals in order to create a new material.
- Annealing. Heating and then cooling a metal in order to improve its properties and workability.
- Casting. Creating a desired shape by pouring molten metal into a pre-made mold.
- Forging. Forming metal by hammering it into shape.
- Welding. Joining two pieces of metal together using heat and/or pressure.
- Heat Treatment. Using heat to alter the physical or chemical properties of a material.
- Galvanizing. Applying a protective coating to metal in order to prevent corrosion.
- Electroplating. Coating a surface with a thin layer of metal using electric current.
- Machining. Removing material from a workpiece in order to create a desired shape or finish.
Frequently Asked Questions
What does a Metallurgical Operator do?
A Metallurgical Operator is responsible for operating and maintaining metallurgical equipment to produce metal products with specific qualities. This includes monitoring and controlling the furnace, casting, and rolling processes, as well as conducting inspections and tests to ensure product quality.
What are jobs related with Metallurgical Operator?
- Metallurgical Sales Engineer
- Metallurgical Research Scientist
- Metallurgist
- Metallurgical and Materials Engineer
- Metallurgical Engineering Technician
- Metallurgical Inspector
- Metallurgical Project Engineer
- Metallurgical Plant Manager
- Metallurgical Technician
Web Resources
- Home - Metallurgical and Materials Engineering metallurgy.mines.edu
- Metallurgical Engineering | Mining & Metallurgical Engineering ... www.unr.edu
- Metallurgical and Materials Engineering College of eng.ua.edu
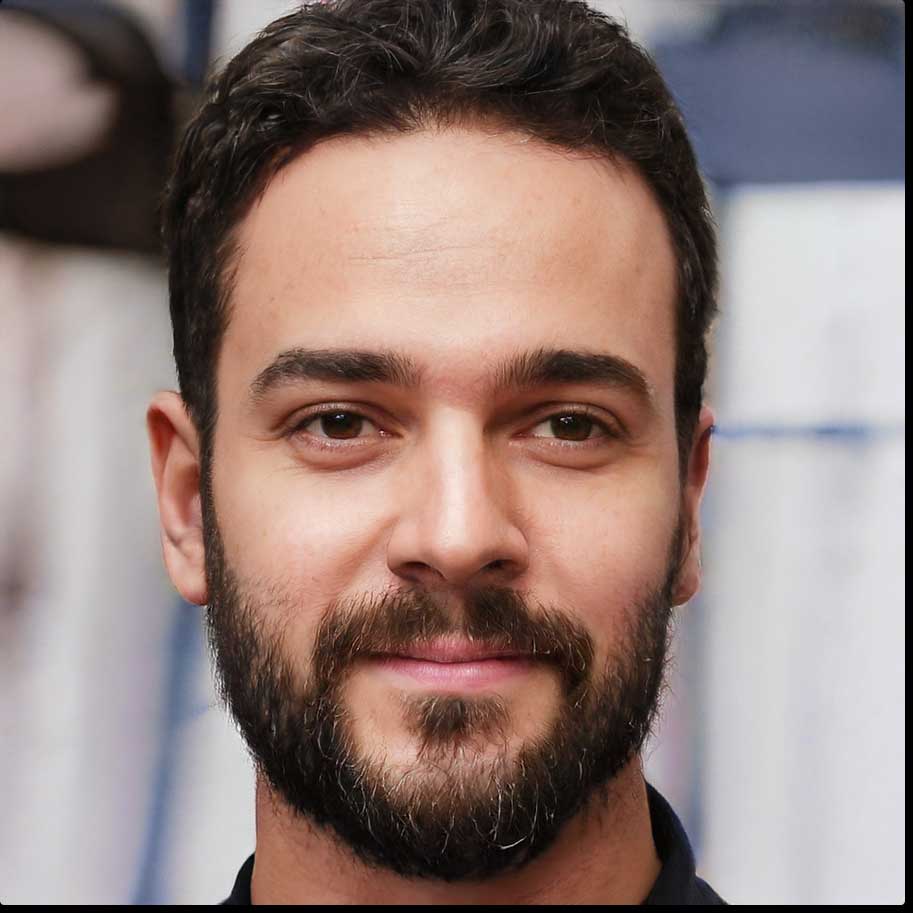